Papers by Mahesh A Makwana
International Journal of Current Microbiology and Applied Sciences, 2019

International Journal of Mathematical, Engineering and Management Sciences, 2021
For the parallel configuration of the robot manipulator, the solution of Forward Kinematics (FK) ... more For the parallel configuration of the robot manipulator, the solution of Forward Kinematics (FK) is tough as compared to Inverse Kinematics (IK). This work presents a novel hybrid method of optimizing an Artificial Neural Network (ANN) specifically Multilayer Perceptron (MLP) with Genetic Algorithm (GA) and Step-wise Linear Regression (SWLR) to solve the complex FK of Delta Parallel Manipulator (DPM). The joint space angular positional data has been iterated using IK to generate point cloud of Cartesian space positional data. This data set is highly random and broad which leads to higher-order nonlinearity. Hence, normalization of the dataset has been done to avoid outliers from the dataset and to achieve better performance. The developed ANN based MLP gave a mean square error of 0.0000762 and an overall R 2 value of 0.99918. Finally, the proposed network has been simulated to solve FK of the parallel manipulator and to check its efficacy. For given joint angles, the proposed network predicted positional values which are in good approximation with known trajectory solved by standard analytical method.

International Journal of Current Microbiology and Applied Sciences, 2019
Evaporative cooling system is one of the cooling techniques, but the limitation is that
cooling c... more Evaporative cooling system is one of the cooling techniques, but the limitation is that
cooling can be done up to wet bulb temperature only, so a study has been taken up to
design, develop a two-stage evaporative cooling system. Cooling performance of twostage indirect/direct evaporative cooling system was experimentally investigated. For this
purpose, a two-stage evaporative cooling experimental setup consisting of an indirect
cooling stage (IDC) followed by a direct evaporative cooling stage (DEC) was designed,
constructed and tested. The performance evaluation was done with respect to three
different air supply velocities, three pad thicknesses and three water flow rates. The results
showed that air velocity of 16.70 m/s, pad thickness of 200 mm, and water flow rate of 5
lpm were found to be the best operating parameters to obtain maximum reduction in air
temperature between 22.10 to 25.80 °C. Also, average relative humidity of air leaving was
found to be in the range of 40.50% to 72.83%. The obtained results were investigated for
best operating parameters with a CFD code. The mathematical model, governing equations
and the boundary conditions were implemented in the code and the calculated results were
analyzed and compared with experimental data. The results were almost similar in both the
cases and briefly described here under

Journal of Physics: Conference Series, 2021
VFor a parallel configuration of a robot manipulator, the solution of Forward
Kinematics (FK) is ... more VFor a parallel configuration of a robot manipulator, the solution of Forward
Kinematics (FK) is tough compared to Inverse Kinematics (IK). This paper presents the modelbased
motion planning of a delta parallel robot in Simulink’s SimScape environment. A model
was developed and simulated for motion study. The developed model has been simulated to
solve the FK of the parallel manipulator and to check its efficacy. First, a helix curve has been
planned within the reachable workspace. Then IK was solved to extract angular positions of the
biceps. Obtained angular positions then fed to SimScape model to run a simulation. The path
taken by the end effector of the system calculated by simulation is in good approximation to
the planned helix path. Further, visual simulation and motion analysis of delta parallel robot
can be performed by Model-based simulation and solves mechanical design as well control
system design problems. Experimental study also shows that the circular path designed for
experiment is well followed in real time simulation.
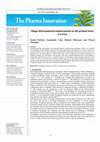
The Pharma Innovation Journal, 2023
Four-dimensional (4D) printing is an emerging additive manufacturing technique which is an extens... more Four-dimensional (4D) printing is an emerging additive manufacturing technique which is an extension of 3D printing. In 4D printing, structures can change their shape and function over time in response to external stimuli such as water, temperature, pH and light. 4D printing is still in its nascent stage, and its application in the food industry is limited. The main factors composing 4D printing technology are software, printing ink, 3D printers, and stimulus. The most common stimulant used in 4D printing is temperature and microwaves have a significant impact on 4D objects' shape-changing behavior. In this review, we give an overview of the software, printer, printing ink and stimuli used for 4D printing and summarise the rheological effect on the printing ink and the current application of 4D food printing based on physical changes over time due to hydration and dehydration.
Food Technica, 2023
Introduction Food safety is an essential aspect of the food industry. It is crucial to detect har... more Introduction Food safety is an essential aspect of the food industry. It is crucial to detect harmful contaminants in food before it reaches the consumers to avoid foodborne illness. Biosensors are one of the technologies that have been developed to ensure the safety of the food industry. Biosensors can detect various contaminants such as pathogens, toxins, and chemical residues. The use of biosensors in the food industry is growing, and it has the potential to revolutionize food safety.
Uploads
Papers by Mahesh A Makwana
cooling can be done up to wet bulb temperature only, so a study has been taken up to
design, develop a two-stage evaporative cooling system. Cooling performance of twostage indirect/direct evaporative cooling system was experimentally investigated. For this
purpose, a two-stage evaporative cooling experimental setup consisting of an indirect
cooling stage (IDC) followed by a direct evaporative cooling stage (DEC) was designed,
constructed and tested. The performance evaluation was done with respect to three
different air supply velocities, three pad thicknesses and three water flow rates. The results
showed that air velocity of 16.70 m/s, pad thickness of 200 mm, and water flow rate of 5
lpm were found to be the best operating parameters to obtain maximum reduction in air
temperature between 22.10 to 25.80 °C. Also, average relative humidity of air leaving was
found to be in the range of 40.50% to 72.83%. The obtained results were investigated for
best operating parameters with a CFD code. The mathematical model, governing equations
and the boundary conditions were implemented in the code and the calculated results were
analyzed and compared with experimental data. The results were almost similar in both the
cases and briefly described here under
Kinematics (FK) is tough compared to Inverse Kinematics (IK). This paper presents the modelbased
motion planning of a delta parallel robot in Simulink’s SimScape environment. A model
was developed and simulated for motion study. The developed model has been simulated to
solve the FK of the parallel manipulator and to check its efficacy. First, a helix curve has been
planned within the reachable workspace. Then IK was solved to extract angular positions of the
biceps. Obtained angular positions then fed to SimScape model to run a simulation. The path
taken by the end effector of the system calculated by simulation is in good approximation to
the planned helix path. Further, visual simulation and motion analysis of delta parallel robot
can be performed by Model-based simulation and solves mechanical design as well control
system design problems. Experimental study also shows that the circular path designed for
experiment is well followed in real time simulation.
cooling can be done up to wet bulb temperature only, so a study has been taken up to
design, develop a two-stage evaporative cooling system. Cooling performance of twostage indirect/direct evaporative cooling system was experimentally investigated. For this
purpose, a two-stage evaporative cooling experimental setup consisting of an indirect
cooling stage (IDC) followed by a direct evaporative cooling stage (DEC) was designed,
constructed and tested. The performance evaluation was done with respect to three
different air supply velocities, three pad thicknesses and three water flow rates. The results
showed that air velocity of 16.70 m/s, pad thickness of 200 mm, and water flow rate of 5
lpm were found to be the best operating parameters to obtain maximum reduction in air
temperature between 22.10 to 25.80 °C. Also, average relative humidity of air leaving was
found to be in the range of 40.50% to 72.83%. The obtained results were investigated for
best operating parameters with a CFD code. The mathematical model, governing equations
and the boundary conditions were implemented in the code and the calculated results were
analyzed and compared with experimental data. The results were almost similar in both the
cases and briefly described here under
Kinematics (FK) is tough compared to Inverse Kinematics (IK). This paper presents the modelbased
motion planning of a delta parallel robot in Simulink’s SimScape environment. A model
was developed and simulated for motion study. The developed model has been simulated to
solve the FK of the parallel manipulator and to check its efficacy. First, a helix curve has been
planned within the reachable workspace. Then IK was solved to extract angular positions of the
biceps. Obtained angular positions then fed to SimScape model to run a simulation. The path
taken by the end effector of the system calculated by simulation is in good approximation to
the planned helix path. Further, visual simulation and motion analysis of delta parallel robot
can be performed by Model-based simulation and solves mechanical design as well control
system design problems. Experimental study also shows that the circular path designed for
experiment is well followed in real time simulation.