Papers by Niklas Jarvstrat
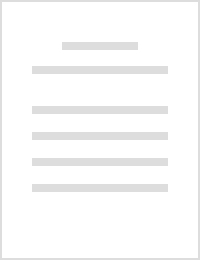
The microstructure and consequently the mechanical properties of titanium alloys are highly depen... more The microstructure and consequently the mechanical properties of titanium alloys are highly dependent on the temperature history endured by the material. The manufacturing process of metal deposition induces repetitive cooling and heating in the material determining a specific microstructure. The presented study is devoted to developing and implementing a microstructure model for Ti-6Al-4V intended to be coupled to a thermo- mechanical model of the metal deposition process. Microstructural analysis of the metal deposited samples was first performed to understand the formed microstructure. A set of representative parameters for microstructure modelling were then selected as representative for the known impact of Ti-6Al-4V microstructure on mechanical properties. Evolution equations for these parameters were implemented for thermal finite element analysis of the process. Six representative state variables are modelled: the phase volume fraction of total alpha, beta, Widmanstatten alpha, grain boundary alpha, martensite alpha, and the alpha lath thickness. Heating, cooling and repeated re-heating involved in the process of metal deposition are taken into account in the model. The phase transformations were modelled based on a diffusionnal theory described by a Johnson-Mehl-Avrami formulation, as well as diffusionless transformations for the martensite alpha formation and the beta reformation during reheating. The Arrhenius equation is applied as a simplification to model temperature dependent alpha lath size calculation. Grain growth is not included in the present formulation, but would have to be added for capturing alpha lath coarsening during long term heat treatment. The temperature history during robotised tungsten inert gas deposition welding is simulated together with the microstructure. The implementation of the model handles well the complex cyclic thermal loading from the metal deposition process. A particular banded structure observed in the metal deposited microstructure is partially explained using the proposed microstructure model. It is concluded that although qualitatively interesting results have been achieved, further calibration testing over a wider range of temperature histories must be performed to improve the transformation kinetic parameters for reliable quantitative predictions of the microstructure.
Journal of Engineering Materials and Technology-transactions of The Asme, 1996
A material model is suggested, suitable for modelling the mechanical behaviour of aluminium secti... more A material model is suggested, suitable for modelling the mechanical behaviour of aluminium sections, from directly after the extrusion and throughout the on-line quenching to room temperature. An experimental procedure is detailed, whereby all material parameters in the model can be determined by a single test. In the test, the specimen is subjected to a carefully prescribed load history in tension and compression during continuous cooling. Material parameters are determined for the AIMgSi alloy AA6060. Finally, the model is compared with conventional plasticity and viscoplasticity, and found to give much better accuracy.
Modelling Ti-6Al-4V microstructure by evolution laws implemented as finite element subroutines: :... more Modelling Ti-6Al-4V microstructure by evolution laws implemented as finite element subroutines: : Application to TIG metal deposition
Journal of Materials Processing Technology, Jun 1, 2009
The aim of this article is to investigate the effect of different fracture criteria on the chip f... more The aim of this article is to investigate the effect of different fracture criteria on the chip formation process, focusing on the formation of segmented chips and what happens around the cutting edge. Furthermore, it is investigated how well the finite element model is able to capture the transition from continuous to segmented chip formation in alloy 718. Machining alloy 718 at lower cutting speeds (below 50m/min) the chip produced is long and continuous. At higher cutting speeds (above 100m/min) the chip produced is segmented. The conclusion from this study is that the transition from continuous chip to segmented chip is caused by both thermal softening and material damage. Furthermore it is concluded that a fracture criterion with a hydrostatic dependency shall be used for accurate modelling of chip segmentation.

International Journal of Machine Tools & Manufacture, Aug 1, 2008
Tool wear is a problem in turning of nickel-based superalloys, and it is thus of great importance... more Tool wear is a problem in turning of nickel-based superalloys, and it is thus of great importance to understand and quantitatively predict tool wear and tool life. In this paper, an empirical tool wear model has been implemented in a commercial finite element (FE) code to predict tool wear. The tool geometry is incrementally updated in the FE chip formation simulation in order to capture the continuous evolution of wear profile as pressure, temperature and relative velocities adapt to the change in geometry. Different friction and wear models have been analysed, as well as their impact on the predicted wear profile assessed. Analyses have shown that a more advanced friction model than Coulomb friction is necessary in order to get accurate wear predictions, by drastically improving the accuracy in predicting velocity, thus having a dramatic impact on the simulated wear profile. Excellent experimental agreement was achieved in wear simulation of cemented carbide tool machining alloy 718.
Mechanics of Materials, Dec 1, 2002
In this paper, a multiaxial generalization of the viscoplastic ''mechanical equation of state'' (... more In this paper, a multiaxial generalization of the viscoplastic ''mechanical equation of state'' (MEOS) by Gittus is proposed that preserves the physical soundness of the theory. The concept of forward and backward mobility of dislocations is generalized to a concept of directional mobility by splitting the mobile dislocation density in an isotropic and a tensorial part, similar to the approach used in the Bodner unified viscoplastic model. It is shown that the formulation is equivalent to the original MEOS in the case of uniaxial loadings. The approach is easily applied to any uniaxial viscoplastic material model.

Steel Research International, Dec 1, 2006
Prediction and control of flaws in welds play important roles in design of complex structures aga... more Prediction and control of flaws in welds play important roles in design of complex structures against fatigue and fracture failure. Cold lapsouter lack of fusion-are small geometrical imperfections at weld toes, which act as fatigue crack initiation sites and reduce the life of welded structures drastically. The aim of this work is to characterize and categorize different types of such imperfections in the tandem gas metal arc welding process and find the mechanisms of their formation. Tandem welding process with different welding parameters was used to produce bead-on-plate coupons. These coupons were then sliced to smaller specimens for further investigations. For studying the weld toes, all the specimens were hit in an impact test machine and then the fracture surfaces of welds and base materials were analysed by scanning electron microscopy (SEM). Two types of cold laps were observed at weld toes, namely overlap and spatter. Observation and measurement showed that these imperfections are in the form of micro cracks with depth between 0.1 to 1.5mm and length between 0.1 to 4 mm.
Surface geometry measurements and the experimental and numerical investigation of stress concentr... more Surface geometry measurements and the experimental and numerical investigation of stress concentration in fillet welds

In machining of nickel based superalloys, such as Inconel 718, tool wear is a major problem due t... more In machining of nickel based superalloys, such as Inconel 718, tool wear is a major problem due to the high stresses and the high temperatures at the tool chip interface. Enhanced knowledge of the tool wear mechanism and capability to predict tool wear are therefore of great importance in machining of nickel based superalloys. The objective with this paper is to investigate if the finite element method (FEM) can be used to predict the flank and crater wear of uncoated cemented carbide tool in turning of Inconel 718. An empirical model has been implemented in a commercial FE-code and the tool geometry is continuously updated to capture the evolution of wear. Experiments have been conducted to obtain parameters for the empirical wear model and for validation of the simulations. The worn geometry at the flank and rake face as well as the cutting edge radius was measured with white light interferometry. Wear model parameters were calibrated by fitting a simulation against measured worn geometries at the flank and rake face. Then separate simulations at other cutting speeds were compared with corresponding experiments to validate the model performance.
Computational Materials Science, Jul 1, 1993
The ellipsoidal geometry is shown by simple arguments to be a consistent and unique choice of mic... more The ellipsoidal geometry is shown by simple arguments to be a consistent and unique choice of microcell for calculating micro-stresses in any composite with randomly distributed, aligned short fibres. Appropriate boundary conditions for this geometry are derived. Comparison with available X-ray measurements of the so-called pseudomacro stress show that the performance of this microcell is superior to some other currently used geometries.
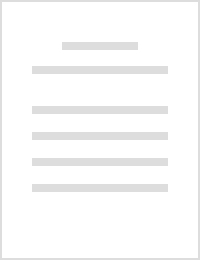
The microstructure and consequently the mechanical properties of titanium alloys are highly depen... more The microstructure and consequently the mechanical properties of titanium alloys are highly dependent on the temperature history endured by the material. The manufacturing process of metal deposition induces repetitive cooling and heating in the material determining a specific microstructure. The presented study is devoted to developing and implementing a microstructure model for Ti-6Al-4V intended to be coupled to a thermo- mechanical model of the metal deposition process. Microstructural analysis of the metal deposited samples was first performed to understand the formed microstructure. A set of representative parameters for microstructure modelling were then selected as representative for the known impact of Ti-6Al-4V microstructure on mechanical properties. Evolution equations for these parameters were implemented for thermal finite element analysis of the process. Six representative state variables are modelled: the phase volume fraction of total alpha, beta, Widmanstatten alpha, grain boundary alpha, martensite alpha, and the alpha lath thickness. Heating, cooling and repeated re-heating involved in the process of metal deposition are taken into account in the model. The phase transformations were modelled based on a diffusionnal theory described by a Johnson-Mehl-Avrami formulation, as well as diffusionless transformations for the martensite alpha formation and the beta reformation during reheating. The Arrhenius equation is applied as a simplification to model temperature dependent alpha lath size calculation. Grain growth is not included in the present formulation, but would have to be added for capturing alpha lath coarsening during long term heat treatment. The temperature history during robotised tungsten inert gas deposition welding is simulated together with the microstructure. The implementation of the model handles well the complex cyclic thermal loading from the metal deposition process. A particular banded structure observed in the metal deposited microstructure is partially explained using the proposed microstructure model. It is concluded that although qualitatively interesting results have been achieved, further calibration testing over a wider range of temperature histories must be performed to improve the transformation kinetic parameters for reliable quantitative predictions of the microstructure.
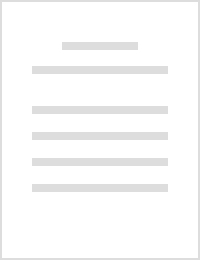
The microstructure and consequently the mechanical properties of titanium alloys are highly depen... more The microstructure and consequently the mechanical properties of titanium alloys are highly dependent on the temperature history endured by the material. The manufacturing process of metal deposition induces repetitive cooling and heating in the material determining a specific microstructure. The presented study is devoted to developing and implementing a microstructure model for Ti-6Al-4V intended to be coupled to a thermo- mechanical model of the metal deposition process. Microstructural analysis of the metal deposited samples was first performed to understand the formed microstructure. A set of representative parameters for microstructure modelling were then selected as representative for the known impact of Ti-6Al-4V microstructure on mechanical properties. Evolution equations for these parameters were implemented for thermal finite element analysis of the process. Six representative state variables are modelled: the phase volume fraction of total alpha, beta, Widmanstatten alpha, grain boundary alpha, martensite alpha, and the alpha lath thickness. Heating, cooling and repeated re-heating involved in the process of metal deposition are taken into account in the model. The phase transformations were modelled based on a diffusionnal theory described by a Johnson-Mehl-Avrami formulation, as well as diffusionless transformations for the martensite alpha formation and the beta reformation during reheating. The Arrhenius equation is applied as a simplification to model temperature dependent alpha lath size calculation. Grain growth is not included in the present formulation, but would have to be added for capturing alpha lath coarsening during long term heat treatment. The temperature history during robotised tungsten inert gas deposition welding is simulated together with the microstructure. The implementation of the model handles well the complex cyclic thermal loading from the metal deposition process. A particular banded structure observed in the metal deposited microstructure is partially explained using the proposed microstructure model. It is concluded that although qualitatively interesting results have been achieved, further calibration testing over a wider range of temperature histories must be performed to improve the transformation kinetic parameters for reliable quantitative predictions of the microstructure.

In machining of nickel based superalloys, such as Inconel 718, tool wear is a major problem due t... more In machining of nickel based superalloys, such as Inconel 718, tool wear is a major problem due to the high stresses and the high temperatures at the tool chip interface. Enhanced knowledge of the tool wear mechanism and capability to predict tool wear are therefore of great importance in machining of nickel based superalloys. The objective with this paper is to investigate if the finite element method (FEM) can be used to predict the flank and crater wear of uncoated cemented carbide tool in turning of Inconel 718. An empirical model has been implemented in a commercial FE-code and the tool geometry is continuously updated to capture the evolution of wear. Experiments have been conducted to obtain parameters for the empirical wear model and for validation of the simulations. The worn geometry at the flank and rake face as well as the cutting edge radius was measured with white light interferometry. Wear model parameters were calibrated by fitting a simulation against measured worn geometries at the flank and rake face. Then separate simulations at other cutting speeds were compared with corresponding experiments to validate the model performance.
Modelling Ti-6Al-4V microstructure by evolution laws implemented as finite element subroutines: :... more Modelling Ti-6Al-4V microstructure by evolution laws implemented as finite element subroutines: : Application to TIG metal deposition
Steel Research International
Prediction and control of flaws in welds play important roles in design of complex structures aga... more Prediction and control of flaws in welds play important roles in design of complex structures against fatigue and fracture failure. Cold laps - outer lack of fusion - are small geometrical imperfec ...
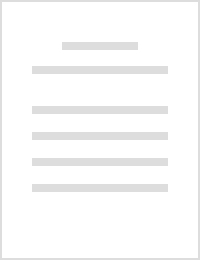
Purpose: The complex mechanisms of tool wear in metal cutting have not been possible to investiga... more Purpose: The complex mechanisms of tool wear in metal cutting have not been possible to investigate in detail by the experimental methods traditionally employed. However, as a result of both the continuous development of numerical methods, such as the Finite Element Method (FEM) and the development of ever more powerful computers, the evaluation of the chip formation process and the evolution of tool wear is now possible.Design/methodology/approach: : In the work presented in this paper, numerical methods are employed to study the effect of a single embedded hard carbide particle on tool wear and tool tip deformation. An important advantage of this approach is that particle size and position can easily be changed, thus making it possible to investigate the influence of these parameters on tool wear.Findings: The results reveal that the position, and in particular the size of carbide particles, have a dramatic impact on tool wear. In particular, particles larger than a certain size (...

Surface defects on sheet metal panels such as local out-of-plane geometric deviations, cause unwa... more Surface defects on sheet metal panels such as local out-of-plane geometric deviations, cause unwanted deviations from the intended visual appearance. In the automobile industry, these defects are commonly graded for visual acceptability through reflection analysis on the hardware. This widely used method is unfortunately subjective and thus has low repeatability. The same method can be applied on simulated sheet metal panels by the use of ray-tracing. In this paper we present an objective, appearance-based, measure by formalising the approach of subjective reflection analysis. Hence, a natural connection between an objective measure and the appearance is obtained making it easy to establish acceptable levels. The performance of this measure and three other objective measures is discussed and demonstrated for a real panel and a panel geometry obtained through sheet forming simulations. These examples illustrate that different measures yield different information about the geometry, and the proposed measure gives a useful quantification of the visual appearance deviation.
Construction on the moon poses radically new design challenges. We will give a brief overview ove... more Construction on the moon poses radically new design challenges. We will give a brief overview over the resources available, the structural loads and other design requirements, and some suggestions for construction approaches. The main structural load will not be gravita- tional loads, but rather internal pressure and airtightness, while additional specific considera- tions such as radiation protection and meteorite impact safety must be considered. It is argued that any long-term habitat on the moon will be buried deep - either by piling regolith on the structures or beneath rock in caves or mineshafts. BACKGROUND

Metallurgical and Materials Transactions B, 1996
A complete process model for the cooling of aluminium extrusions is presented. It is capable of p... more A complete process model for the cooling of aluminium extrusions is presented. It is capable of predicting both thermally induced distortions and possible strength reductions. The model consists of three parts: a thermal part, a metallurgical part, and a mechanical part. The thermal part includes heat-transfer and heat-conduction models and generates the temperature history needed as input to the other two parts. The metallurgical part consists of a kinematic model for the precipitation of nonhardening particles during cooling, and it predicts the resulting strength after subsequent aging. Finally, the mechanical part comprises the usual compatibility and consistency equations, as well as a unified material model that is very accurate both for rate-dependent material behavior at high temperatures and for the virtually rate-independent behavior at low temperatures. Water-cooling experiments have been performed, and finite element simulations were executed using the process model. The heat-transfer coefficient for water quenching is shown to be extremely sensitive to geometry and other cooling conditions. In addition, the cooling characteristics and the material model are factors of equal importance in the prediction of distortions.
Uploads
Papers by Niklas Jarvstrat