Papers by Dr. Rijo Jacob Thomas

Journal of Mechanical and Engineering Sciences, 2018
The main concerns in energy from petroleum-based fuels are the scarcity, cost, and pollution the ... more The main concerns in energy from petroleum-based fuels are the scarcity, cost, and pollution the fuels. Now, natural gas is considered as a better alternative. The process of converting natural gas into liquefied natural gas (LNG) is highly energy intensive and consumes about 10-15% of the total energy spent on natural gas production. Novel methods for regasification of LNG (converting back to NG) exist and are being used in various applications; mainly in power generation and refrigeration. One such method in power generation, the cold associated with LNG (cold exergy) can be utilized efficiently for improving the performance of power plants based on the Brayton cycle by precooling the working fluid. The study investigated such a possibility of precooling the inlet working fluid and to bring out the various factors influencing the overall efficiency of the power plant and regasification of LNG. Exergy analysis is the tool used for this study. The combined power plant is modeled using Aspen Hysys process simulation tool, and the results show that there is 35-135% improvement in the exergy efficiency of the power plant. This study also intends to find a suitable working fluid based on the objective functions such as exergy efficiency of the power plant and a regasification parameter (mass flow ratio). The gas turbine cycle gives maximum exergy efficiency when air is used as working fluid and Helium is the best working fluid candidate where regasification is the prime objective. Helium can gasify LNG about ten times more than other three working fluids
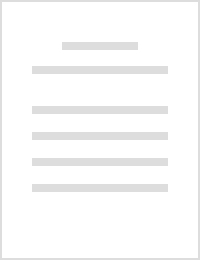
Journal of Thermal Science and Engineering Applications, 2012
Cold end in helium liquefiers, where finally the gas is converted to liquid, may have different a... more Cold end in helium liquefiers, where finally the gas is converted to liquid, may have different alternatives in configuration to achieve maximum exergy efficiency. Apart from high exergy efficiency, which also means low specific power consumption, reliability of operation and complexity of equipment design are also some of the concerns for designers. In this work, various cold end configurations are compared at different operating conditions to help arrive at appropriate choices during design and operation. When single Joule–Thomson valve is replaced by more efficient cold ends with expanders, it allows reduction of the number of Brayton stages in precooling section as well as the total heat exchanger size. Cold end with expander and Joule–Thomson valve combination has been found to be a good compromise between reliability, liquid production, specific power consumption, and exergy efficiency. However, for such a configuration, it is important to fix the intermediate pressure at appr...

International Journal of Refrigeration, 2012
In helium liquefiers, refrigeration stages have expanders connected in parallel (reverse Brayton ... more In helium liquefiers, refrigeration stages have expanders connected in parallel (reverse Brayton stage) and also in series with heat exchangers between them (modified Brayton stages). Options of splitting and combining Brayton stages into modified Brayton stages are evaluated and compared by exergy analysis. Results show that as two Brayton stages are combined to make two modified Brayton stages, the performance deteriorates. When one Brayton stage is split into two modified Brayton stages, the performance shows improvement with the total heat exchanger surface area remaining unchanged. When the stage operates at lower temperatures, such splitting has led to more improvement. Each stage, whether it is Brayton or modified Brayton, has been found to behave as an independent refrigeration stage allowing more additions of heat exchanger area. In a one-to-one comparison, a Brayton stage has been found to be superior to a modified Brayton stage at any temperature of operation. The impact of replacing Brayton stage with modified Brayton stage has been found to be more pronounced when heat exchangers in the configuration are less balanced in mass flow.
International Journal of Refrigeration, 2013
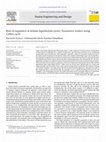
Fusion Engineering and Design, 2011
Large scale helium liquefaction/refrigeration plant is a key subsystem of fusion devices. Perform... more Large scale helium liquefaction/refrigeration plant is a key subsystem of fusion devices. Performance of these plants is dependent on a number of geometric and operating parameters of its constituting components such as compressors, heat exchangers, expanders, valves, etc. Expander has been chosen as the subject matter of analyses in the present study. As the sensible cold of helium vapor is lost in liquefiers, the expanders in liquefaction cycles have to provide more refrigeration than those in refrigeration cycles. The expander parameters such as rate of mass flow, operating pressure, inlet temperature, etc. are interdependent, and hence, it is difficult to predict the system behavior with variation of a particular parameter. This necessitates the use of process simulators. Parametric studies have been performed on Collins helium liquefaction cycle using Aspen HYSYS ®. Collins cycle has all the basic characteristics of a large-scale helium liquefier and the results of this study may be extrapolated to understand the behavior of large scale helium liquefiers. The study shows that the maximum liquid production is obtained when 80% of the compressor flow is diverted through the expanders and it is equally distributed between the two expanders. The relationships between the liquid production and the isentropic efficiency of expanders are almost linear and both the higher and lower temperature expanders exhibit similar trends.
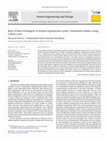
Fusion Engineering and Design, 2012
Energy efficiency of large-scale helium liquefiers generally employed in fusion reactors and acce... more Energy efficiency of large-scale helium liquefiers generally employed in fusion reactors and accelerators is determined by the performance of their constituting components. Simulation with Aspen HYSYS ® V7.0, a commercial process simulator, helps to understand the effects of heat exchanger parameters on the performance of a helium liquefier. Effective UA (product of overall heat transfer coefficient U, heat transfer surface area A and deterioration factor F) has been taken as an independent parameter, which takes into account all thermal irreversibilities and configuration effects. Nondimensionalization of parameters makes the results applicable to plants of any capacity. Rate of liquefaction is found to increase linearly with the effectiveness of heat exchangers. Performance of those heat exchangers that determine the inlet temperatures to expanders have more influence on the liquid production. Variation of sizes of heat exchangers does not affect the optimum rate of flow through expanders. Increasing UA improves the rate of liquid production; however, the improvement saturates at limiting UA. Maximum benefit in liquefaction is obtained when the available heat transfer surface area is distributed in such a way that the effectiveness remains equal for all heat exchangers. Conclusions from this study may be utilized in analyzing and designing large helium plants.

Energy, 2012
Exergy has proved to be a useful tool to analyze and optimize the design and operation of many sy... more Exergy has proved to be a useful tool to analyze and optimize the design and operation of many systems. Some studies on helium refrigerators and liquefiers based on exergy are available in literature. In this paper, systematic evaluation of important operating and geometric parameters has been done to determine the exergy destructions in components as well as in the entire cycle of Collins helium liquefiers. Grassmann diagram of exergy flow has been shown to be of immense help in understanding relative importance of different components used in the system. Compressor pressure, expander flow rates, heat exchanger surface area are some of the parameters optimized considering both presence and absence of pressure drop in the heat exchangers. Non-dimensionalization of parameters makes the results applicable to plants of any capacity. Exergy-analysis based on Second Law proves to be far superior to the First Law based energy analysis in designing of the helium plant as the former is holistic in approach and capable of deriving some additional conclusions. Results derived on Collins cycle may be applicable in large-scale helium liquefiers by providing basic understanding of the influence of components on the plant performance and reasonable initial guess values in their design and simulation.
Cryogenics, 2011
Large-scale helium liquefaction systems, being energy-intensive, demand judicious selection of pr... more Large-scale helium liquefaction systems, being energy-intensive, demand judicious selection of process parameters. An effective tool for design and analysis of thermodynamic cycles for these systems is exergy analysis, which is used to study the behavior of a helium liquefaction system based on modified Claude cycle. Parametric evaluation using process simulator Aspen HYSYS® helps to identify the effects of cycle pressure
Cryogenics, 2012
Proper design of helium systems with large number of components and involved configurations such ... more Proper design of helium systems with large number of components and involved configurations such as helium liquefiers/refrigerators requires the use of tools like process simulators. The accuracy of the simulation results, to a great extent, depends on the accuracy of property data. For computation of thermodynamic properties of helium, the 32-parameter MBWR equation of state proposed by McCarty and Arp [1] is widely used. However, it is computationally involved, makes the simulation process more time- ...
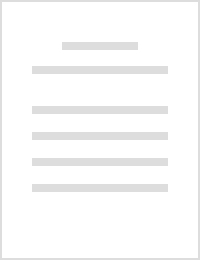
This paper deals with the application of dynamic simulation of helium refrigerators and liquefier... more This paper deals with the application of dynamic simulation of helium refrigerators and liquefiers by a general purpose process-simulator Aspen Hysys®. A standard helium liquefier for capacities of 100 L/hr and 50 L/hr with and without liquid nitrogen pre-cooling respectively, have been chosen for validation of the code of Aspen Hysys®. To obtain an accurate simulation result we need appropriate equation of state, accurate transport properties of helium and thermal properties of metal, actual equipment specifications and cool-down sequence with appropriate control. In the present work, the limitations of Aspen Hysys® in simulating helium systems have been identified and techniques to overcome these problems have been discussed. The dynamic simulation has been performed following the above techniques in order to obtain cool-down profiles. The cool-down process has been simulated from 300 K to 8 K showing similar trends in the temperature variations at different state points. However, it has not been possible to get below the level of 8 K and the solution diverges at this temperature. The reasons for this divergence are under investigation and future efforts would be made to achieve a complete cool-down process simulation. To conclude, it may be said that, despite the limitations of Aspen Hysys® and non-availability of many vital specifications of equipment of plant, we are optimistic about the applicability of Aspen Hysys® as dynamic simulator for simulation of helium systems down to its liquefaction point.
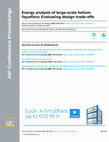
AIP Conference Proceedings, 2014
It is known that higher heat exchanger area, more number of expanders with higher efficiency and ... more It is known that higher heat exchanger area, more number of expanders with higher efficiency and more involved configuration with multi-pressure compression system increase the plant efficiency of a helium liquefier. However, they involve higher capital investment and larger size. Using simulation software Aspen Hysys v 7.0 and exergy analysis as the tool of analysis, authors have attempted to identify various trade-offs while selecting the number of stages, the pressure levels in compressor, the cold-end configuration, the heat exchanger surface area, the maximum allowable pressure drop in heat exchangers, the efficiency of expanders, the parallel/series connection of expanders etc. Use of more efficient cold ends reduces the number of refrigeration stages and the size of the plant. For achieving reliability along with performance, a configuration with a combination of expander and Joule-Thomson valve is found to be a better choice for cold end. Use of multi-pressure system is relevant only when the number of refrigeration stages is more than 5. Arrangement of expanders in series reduces the number of expanders as well as the heat exchanger size with slight expense of plant efficiency. Superior heat exchanger (having less pressure drop per unit heat transfer area) results in only 5% increase of plant performance even when it has 100% higher heat exchanger surface area.
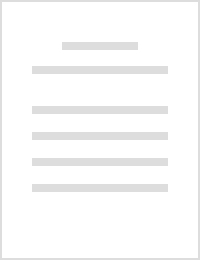
Large-scale helium liquefaction/refrigeration plants have thermodynamically more involved configu... more Large-scale helium liquefaction/refrigeration plants have thermodynamically more involved configurations than Collins cycle that is the fundamental cycle for liquefaction and are used for cooling superconducting magnets etc. Transient analysis helps in design of such plants through improved understanding of the processes leading to optimal designs and appropriate strategies for mitigating the effects of fluctuating heat loads. Process simulator with appropriate Equation of State for thermodynamic properties of the fluid, appropriate models for transport and thermo-physical properties of helium and the structural materials helps in modeling and simulation of such plants. In this paper, attempt has been made to bring out the features of helium liquefiers, to discuss the peculiarities of the properties of helium fluid and the materials of construction at temperatures near the normal boiling point of helium that need to be addressed in performing steady state and dynamic simulation. Many of these aspects are not taken care of by the commercial process simulators like Aspen Plus®, Aspen Dynamics®, Aspen Hysys®, ChemCAif etc. They have been compared on the basis of their suitability for addressing those issues. The areas, methodology and the extent of success that have been achieved in customizing the software, Aspen Hysys®, for simulation of helium systems have also been discussed.
Uploads
Papers by Dr. Rijo Jacob Thomas