Papers by Abdulhakeem H Nurudeen

Mechanical Technology and Engineering Insights, 2024
Nigeria has huge deposits of kaolin spread across the country. Yet, Kaolin and its derivatives co... more Nigeria has huge deposits of kaolin spread across the country. Yet, Kaolin and its derivatives cost Nigeria around 14 million USD annually, and they have diverse industrial applications such as the manufacturing of paper, ceramics, cosmetics, medicine, paints, and porcelain. This loss of revenue is due to the under-tapping of the mineral due to the absence of beneficiation plants. Currently, the mining is primarily done crudely by artisan miners. Implementing modern manufacturing infrastructure requires adequate attention to cater to facility layout and future improvements, reduce costs, improve customer satisfaction, space utilization, etc. Simulation exercises proffer solutions to these problems in a virtual environment. This work reports a proposed facility layout design for kaolin beneficiation. The proposed plant was designed using Systematic Layout Planning (SLP) methodology and tested using FLEXSIM Simulation software to optimize the plant's production capacity. The results from the design showed that the optimized production plant had an annual production capacity of 95,328 tons, which was higher than the initial layout, with 69,120 tons per annum. The workstations utilization for the optimized layout showed better results than the initial layout design, with the optimized results showing improvements in the efficiency of the workstations as follows (after the simulation): fluid mixer1 had 73.77%, sedimentation tank had 18.44%, rotary drum dryer had 18.44%, packaging line had 63.87%, Screener_washer had 74.46%, and magnetic separator has 63.94% utilization.
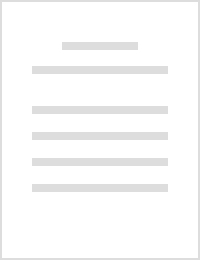
Background: Students’ academic achievement is regarded as the scholastic standing of students at ... more Background: Students’ academic achievement is regarded as the scholastic standing of students at the end of a given study period that is expressed in terms of grades. The key to bridging the attainment gap at the end of their study period is through their cumulative grade points over the duration of the study. Predictive validity study on students first-year GPA as a predictor of their final-year CGPA was carried out to predict the students’ academic performance in Chemical, Civil, Electrical, and Mechanical Engineering. Purpose/Hypothesis: This study examined the relationship between first-year GPA and final-year CGPA, as well as the relationship between Age, Gender and Geopolitical zones on first-year GPA and CGPA of Engineering students in the Faculty of Engineering students University of Abuja, Nigeria. The data obtained from the four Departments; Chemical, Civil, Electrical and Mechanical were analyzed. Two hypotheses were formulated to guide the study. Design/Method: An ex-pos...

Journal of Future sustainability , 2023
Manufacturing facilities are systems that require adequate designing, maintenance and reservation... more Manufacturing facilities are systems that require adequate designing, maintenance and reservations for improvement in the future. Layouts need to be effectively designed to reduce operating to the minimum. Computer simulation is a process of investigating and analyzing the behavior of production processes for effective decision-making using computers to generate solutions that will positively impact short, and long-term planning of the Plants and save costs of real-life implementation. This study investigated a 500Kg capacity shea nut processing plant using FlexSim©. The findings from the initial model were not effective and experienced bottlenecks in workstations (Roaster and Milling) sections, poor cycle and lead times coupled with manual labor, Plant efficiency was 35.7%. However, the Improvement Layout Model was able to address these bottlenecks, the results showed the Plant efficiency increased to 83.3%, shorter lead and cycle times, improved machine utilization, and throughput capacity of the Plant. The results were an indication of conformance to the layout design developed to aid in enhancing the traditional shea nut processing that is largely dominated by traditional processing practices.

Arid Zone Journal of Engineering, Technology and Environment, Mar 1, 2021
Introduction The performance and efficiency of industrial production system depends to a great ex... more Introduction The performance and efficiency of industrial production system depends to a great extent on the quality of machineries, employees, as well as how facilities are positioned in a plant. Poorly designed facility, therefore, may result in loss in production time, efficiency and wastage of raw materials, while a well-designed production facility improves on the efficiency of production with fewer costs and time wastage (Tak and Yadav, 2012). Among the main goal of manufacturing system is to maximize productivity with regards to the complexity of the processes involved in manufacturing from raw materials to finished products and workstations (Carlo et al., 2013). Agricultural products are processed to among other things improve the shelf-life of the produce and acceptability for final consumption as food or ingredients for industrial production. The output of processing result is varieties of by-products. Vegetables such as onions, tomatoes and pepper are the major vegetables produced in Nigeria, and they play a significant role in health and nutrition due to their constituents that regulate digestion. Onions are processed to produce dehydrated onions, onions powder and puree. Despite the enormous economic potentials of onions, the processing of onions for national growth and development has little to no existence in Nigeria Ibeawuchi et al. (2015). According to Ugonna et al. (2017), Nigeria's vegetable processing industries need to be developed to reduce postharvest losses and enhance food nutrition security. The establishment of these industries will boost the nation's economy thereby creating employment, wealth, reduced rate of malnutrition and increased standards of living for the rural populace. According to Food and Agriculture Organization (FAO) Statistics FAO (2019) it estimated that Nigeria's tomatoes production is around 4.5 tons/ha with annual production of 3.8 million tonnes, while onions production is around 2.3tons/ha, with annual production of 1.3 million tonnes in the year 2019. Despite the huge contributions of agriculture (vegetables) to Nigeria's economic growth, about 50% of fruits and vegetables produced are lost as a result of their perishable nature, poor postharvest handling and mismanagement leading to a staggering 360 million USD losses annually ARTICLE INFORMATION ABSTRACT This study was conducted to determine an effective design for the processing of dehydrated tomatoes. The study proffer solutions to huge losses Nigeria encounters as a result of poor postharvest handling across the fruits and vegetables value chain. Despite the huge contributions of agriculture (vegetables) to Nigeria's economic growth, postharvest losses stands at $9 million with 50% losses in fruits and vegetables as a result of their perishable nature. Systematic layout planning (SLP) approach was used in designing the process layout for dehydrated tomatoes. The design approach was used to serve as an improvement layout and also as a new design for processing of dehydrated tomato plant, with estimated 5% material losses during processing, average temperature for dehydration as 65 o C, plant production time of 748.99 minutes/day, a throughput capacity of 10 tons/day is achievable. Additionally, the design was validated using computer simulation and the results obtained from the simulation analysis indicated that the method can be used to optimize process planning for several production processes of dehydrated fruit and vegetables

Arid Zone Journal of Engineering, Technology and Environment, 2020
Anaerobic co-digestion offers a prospective medium for transforming organic solid wastes into fue... more Anaerobic co-digestion offers a prospective medium for transforming organic solid wastes into fuel, thereby providing an extra source of energy. This study investigates the kinetics of anaerobic co-digestion of paunch manure and sugarcane peels using cow dung as inoculum for biogas production. Anaerobic assay setup was in 3 digesters of 4 replicates with a total of 12 replicate batch digesters under mesophilic temperature range (30-35°C) for a retention time of 30 days. Cumulative biogas production for all digesters were measured and fitted to some selected models. The modified Gompertz equation was tested for its fitness. The kinetic parameters viz., biogas yield potential (P), maximum biogas production rate (Rm) and the duration of lag phase (λ) were recorded for each case as the digester with 0g sugarcane peels (control) produced maximum biogas of (83.14 (mL/g VS)) and the kinetic parameters P, Rm and λ were 89.0018 ml (g VS-1), 4.7089 ml (g VS d)-1, 0.8734 days respectively. It ...

As the global population surges, the demand for food increases and meeting these demands requires... more As the global population surges, the demand for food increases and meeting these demands requires new approach as traditional practices cannot be sustainable and efficient. Nigeria also faces these challenges, with a population of 180 million people making available and cost effective food is never and easy task. The evolution of digital technologies and their integration to Agriculture will give way for increased economic growth and development to the Agricultural sector in Nigeria. Industry 4.0 is a new approach to digitalization and developing intelligent manufacturing processes over and entire value chain of products with increased customization and individualization. This study reviewed some of the key challenges the Nigerian Agricultural sector faces along the agricultural value/supply chains to pave way for the successful implementation of industry 4.0 to some key areas of the sector

ijetrm journal, 2020
As the global population surges, the demand for food increases and meeting these demands requires... more As the global population surges, the demand for food increases and meeting these demands requires new approach as traditional practices cannot be sustainable and efficient. Nigeria also faces these challenges, with a population of 180 million people making available and cost effective food is never and easy task. The evolution of digital technologies and their integration to Agriculture will give way for increased economic growth and development to the Agricultural sector in Nigeria. Industry 4.0 is a new approach to digitalization and developing intelligent manufacturing processes over and entire value chain of products with increased customization and individualization. This study reviewed some of the key challenges the Nigerian Agricultural sector faces along the agricultural value/supply chains to pave way for the successful implementation of industry 4.0 to some key areas of the sector. INTRODUCTION As the global population grows and technology advances, the demand for effective, fast, reliable, timely production has been a factor of discussions from academia to industry. The Academia focuses on finding concepts, developing systems, methodologies and business models while the Industry focuses on changing the machine dominant manufacturing to an intelligent machines and processes to effect on productivity and increased customer satisfaction [1]. Agriculture was the leading contributor to the Gross Domestic Product (GDP) of Nigeria prior to the discovery of crude oil with 57% to GDP and 64.5% of export earnings from 1960-1969, between 1970-2000 the sector contribution declined to 23.5% and 5.1% as export earnings [2], in 2017 the production increased to 29.15% of GDP while in the second quarter of 2020 it declined to 24.6% as the result of the global pandemic(COVID-19) [3] Nigeria's agriculture potential is high with a population of around 180 million people, an estimated 82 Million Hectares of arable land of which on 34 million is being cultivated, feeding such population is a huge task indeed for the Government and its farmers. The sector is still underutilized as a result of inability to add value to produced products the Country losses an estimated 9 million USD annually to post harvest losses [4, 3]. Some researchers[5] defined Industry 4.0 as an approach that creates an environment in which elements, devices, functionalities are continuously linked together to have a constant communication with a high degree of coordination [5] while other researchers perceived it as a new level of organization and control over an entire value chain of products, increased customer individualization requirements, creates connection of physical systems, internet, designing and drafting production development, integrated approaches, processes and Information Technology driven solutions [6], the author's see it as a collective approach that integrates machines, work schedule and manufacturing systems through integrated networks and value chain to enable constant communication and high level of coordination between each other. The advancement of science and technology dynamically improve on industrialization globally, industrial development have evolved over three stages before the commencement of the fourth industrial revolution [7], these industrial achievements developed over two hundred years ago; the first industrial revolution paved way for steam and water powered facilities, the second gave birth to mass production and assembly systems while the third came with the integration of electronics and information technology (IT) to further automate and simplify manufacturing systems [8] [9].

IJETRM, 2020
As the global population surges, the demand for food increases and meeting these demands requires... more As the global population surges, the demand for food increases and meeting these demands requires new approach as traditional practices cannot be sustainable and efficient. Nigeria also faces these challenges, with a population of 180 million people making available and cost effective food is never and easy task. The evolution of digital technologies and their integration to Agriculture will give way for increased economic growth and development to the Agricultural sector in Nigeria. Industry 4.0 is a new approach to digitalization and developing intelligent manufacturing processes over and entire value chain of products with increased customization and individualization. This study reviewed some of the key challenges the Nigerian Agricultural sector faces along the agricultural value/supply chains to pave way for the successful implementation of industry 4.0 to some key areas of the sector. INTRODUCTION As the global population grows and technology advances, the demand for effective, fast, reliable, timely production has been a factor of discussions from academia to industry. The Academia focuses on finding concepts, developing systems, methodologies and business models while the Industry focuses on changing the machine dominant manufacturing to an intelligent machines and processes to effect on productivity and increased customer satisfaction [1]. Agriculture was the leading contributor to the Gross Domestic Product (GDP) of Nigeria prior to the discovery of crude oil with 57% to GDP and 64.5% of export earnings from 1960-1969, between 1970-2000 the sector contribution declined to 23.5% and 5.1% as export earnings [2], in 2017 the production increased to 29.15% of GDP while in the second quarter of 2020 it declined to 24.6% as the result of the global pandemic(COVID-19) [3] Nigeria's agriculture potential is high with a population of around 180 million people, an estimated 82 Million Hectares of arable land of which on 34 million is being cultivated, feeding such population is a huge task indeed for the Government and its farmers. The sector is still underutilized as a result of inability to add value to produced products the Country losses an estimated 9 million USD annually to post harvest losses [4, 3]. Some researchers[5] defined Industry 4.0 as an approach that creates an environment in which elements, devices, functionalities are continuously linked together to have a constant communication with a high degree of coordination [5] while other researchers perceived it as a new level of organization and control over an entire value chain of products, increased customer individualization requirements, creates connection of physical systems, internet, designing and drafting production development, integrated approaches, processes and Information Technology driven solutions [6], the author's see it as a collective approach that integrates machines, work schedule and manufacturing systems through integrated networks and value chain to enable constant communication and high level of coordination between each other. The advancement of science and technology dynamically improve on industrialization globally, industrial development have evolved over three stages before the commencement of the fourth industrial revolution [7], these industrial achievements developed over two hundred years ago; the first industrial revolution paved way for steam and water powered facilities, the second gave birth to mass production and assembly systems while the third came with the integration of electronics and information technology (IT) to further automate and simplify manufacturing systems [8] [9].
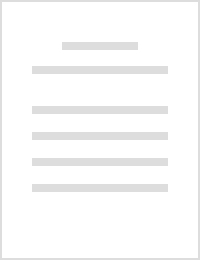
AZOJETE, 2020
Anaerobic co-digestion offers a prospective medium for transforming organic solid wastes into fue... more Anaerobic co-digestion offers a prospective medium for transforming organic solid wastes into fuel, thereby providing an extra source of
energy. This study investigates the kinetics of anaerobic co-digestion of paunch manure and sugarcane peels using cow dung as inoculum for biogas production. Anaerobic assay setup was in 3 digesters of 4
replicates with a total of 12 replicate batch digesters under mesophilic temperature range (30-35°C) for a retention time of 30 days. Cumulative biogas production for all digesters were measured and fitted to some selected models. The modified Gompertz equation was tested for its fitness. The kinetic parameters viz., biogas yield potential (P), maximum biogas production rate (Rm) and the duration of lag
phase (λ) were recorded for each case as the digester with 0g sugarcane peels (control) produced maximum biogas of (83.14 (mL/g VS)) and the
kinetic parameters P, Rm and λ were 89.0018 ml (g VS-1), 4.7089 ml (gVS d)-1, 0.8734 days respectively. It was observed that biogas
production potential was inversely proportional to the substrate concentration of sugarcane peels in the digesters, the highest
concentration of sugarcane peels (1.8g SP) recorded the lowest quantity
of biogas with 37.9075 mL/g VS, 1.4547 g VS-1, 1.0891 days. Therefore, sugarcane peels should be co-digested with other substrates. The
experimental kinetic data in-line with the Gompertz Model, Modified Gompertz Model Equation

BJET, 2020
In this research study, the process layout for dehydration of fruits and vegetables processing pl... more In this research study, the process layout for dehydration of fruits and vegetables processing plant was examined using computer simulation software. Nigeria's production of fruits and vegetables is around 16.4 million metric tonnes, which makes Nigeria the 14 th largest producer of tomatoes in the World, 2 nd largest in Africa and sadly the 3 rd largest importer of processed tomato commodities in the World as the result of our inability to refine and add value, Nigeria losses an estimated $9 million to postharvest losses annually. The essence of performing simulation is to experiment and analyse a manufacturing process to reduce the time, cost of procurement of equipment for construction, upgrading and testing the performance in real-life situations. Flexsim software was used to perform simulation runs and optimization alternatives on production lines were drawn, with special emphasis on tomatoes. The simulation was done on the basis of flow chart of the processing of dehydrated fruit and vegetables and design data. Based on the analysis of the simulation data, the study identified the bottlenecks in processing and proffer alternative solutions for improved and optimal output respectively. The Initial model had machine buffer due to the capacity of the dehydrators which made the production to lag by 20% in output stuck as Work-in-process over simulation period. The optimized production line scheme 1 had additional processors for dehydration and milling, it was found suitable for the production process as it addresses the issues of bottlenecks in production with increased production capacity, reduced work-in-process and complete production cycle of 50000 seconds per day.
Uploads
Papers by Abdulhakeem H Nurudeen
energy. This study investigates the kinetics of anaerobic co-digestion of paunch manure and sugarcane peels using cow dung as inoculum for biogas production. Anaerobic assay setup was in 3 digesters of 4
replicates with a total of 12 replicate batch digesters under mesophilic temperature range (30-35°C) for a retention time of 30 days. Cumulative biogas production for all digesters were measured and fitted to some selected models. The modified Gompertz equation was tested for its fitness. The kinetic parameters viz., biogas yield potential (P), maximum biogas production rate (Rm) and the duration of lag
phase (λ) were recorded for each case as the digester with 0g sugarcane peels (control) produced maximum biogas of (83.14 (mL/g VS)) and the
kinetic parameters P, Rm and λ were 89.0018 ml (g VS-1), 4.7089 ml (gVS d)-1, 0.8734 days respectively. It was observed that biogas
production potential was inversely proportional to the substrate concentration of sugarcane peels in the digesters, the highest
concentration of sugarcane peels (1.8g SP) recorded the lowest quantity
of biogas with 37.9075 mL/g VS, 1.4547 g VS-1, 1.0891 days. Therefore, sugarcane peels should be co-digested with other substrates. The
experimental kinetic data in-line with the Gompertz Model, Modified Gompertz Model Equation
energy. This study investigates the kinetics of anaerobic co-digestion of paunch manure and sugarcane peels using cow dung as inoculum for biogas production. Anaerobic assay setup was in 3 digesters of 4
replicates with a total of 12 replicate batch digesters under mesophilic temperature range (30-35°C) for a retention time of 30 days. Cumulative biogas production for all digesters were measured and fitted to some selected models. The modified Gompertz equation was tested for its fitness. The kinetic parameters viz., biogas yield potential (P), maximum biogas production rate (Rm) and the duration of lag
phase (λ) were recorded for each case as the digester with 0g sugarcane peels (control) produced maximum biogas of (83.14 (mL/g VS)) and the
kinetic parameters P, Rm and λ were 89.0018 ml (g VS-1), 4.7089 ml (gVS d)-1, 0.8734 days respectively. It was observed that biogas
production potential was inversely proportional to the substrate concentration of sugarcane peels in the digesters, the highest
concentration of sugarcane peels (1.8g SP) recorded the lowest quantity
of biogas with 37.9075 mL/g VS, 1.4547 g VS-1, 1.0891 days. Therefore, sugarcane peels should be co-digested with other substrates. The
experimental kinetic data in-line with the Gompertz Model, Modified Gompertz Model Equation