Papers by Dr. Eng. Thiago Marques Ivaniski
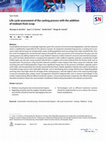
SN Applied Sciences, Nov 9, 2023
Sustainability has become increasingly important, given the scenario of environmental degradation... more Sustainability has become increasingly important, given the scenario of environmental degradation, and the industrial sector is significantly responsible for this adverse scenario. An important manufacturing process is casting, but it consumes many natural resources and generates waste, emitting pollutants and consuming much water and electricity. Thus, this work investigated the environmental impacts through life cycle assessment (LCA) arising from the gray cast iron casting process by adding niobium from scrap. Niobium improves molten material's structure and mechanical properties, and it has been obtained from a company that separates it with a ballistic magnetic separator. A production model of 800 ingots was devised, using recycled material from a supplier and reused material from the factory itself, such as recycled sand. The processes using recycled materials resulted in lower impacts than those using new materials. Sand recycling and sand mold preparation stages have significant impact due to the presence of binders, typically used in sand molds, and transportation by vehicles powered by fossil fuels. Abiotic depletion indicates the need to transition to renewable energy sources and sustainable materials, such as developing clean energy infrastructure. Regarding global warming, there were high values for all stages of the casting process, with the highest value in the sand recycling stage. To prevent eutrophication, proper waste management should be implemented, such as cleaner technologies in the smelter implementing efficient effluent treatment systems. Concerning freshwater ecotoxicity, the effluents generated should be treated to reduce the concentration of pollutants before being discarded in the aquatic environment. Article Highlights • Niobium recycling has low environmental impacts. • Regarding recycled sand, the supplier should be nearer, and vehicles should use fuel less damaging to the environment. • Technologies such as effluent treatment systems should be implemented so as to reduce the concentration of pollutants.
Lecture notes in mechanical engineering, Aug 22, 2023
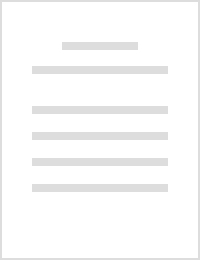
A redução de recursos operacionais, e.g. tempo e matéria prima, é um dos principais desafios da i... more A redução de recursos operacionais, e.g. tempo e matéria prima, é um dos principais desafios da indústria automotiva. A simulação numérica por elementos finitos atua como uma ferramenta computacional importante para a solução destes problemas, de forma a conferir precisão aos resultados calculados quando comparados aos fenômenos reais, ocorridos, por exemplo, em processos de estampagem. Este trabalho tem como objetivo abordar o efeito das condições de atrito utilizando a simulação numérica computacional, em uma chapa bifásica DP600 pelo ensaio de estiramento Erichsen, em que reproduz as condições biaxiais de deformação visando à ductilidade de chapas para estampagem. Criou-se o modelo a partir da inserção dos dados experimentais deste material no software FORGE. Foi observada a influência do coeficiente de atrito durante a simulação numérica na variação das distribuições de pressão, tensão equivalente, redução de espessura e taxa de deformação.The operational resources, i.e. raw mat...
Anais do IX Congresso Brasileiro de Engenharia de Fabricação, 2017
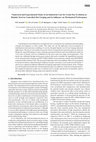
Materials Research
Controlling the recrystallization is an important way to reach grain size refinement and outstand... more Controlling the recrystallization is an important way to reach grain size refinement and outstanding strength and toughness on alloy metals. This study sets out the application and investigation of mathematical microstructure modeling of a newly designed bainitic steel for hot forging industrial applications. The macro-scale model was used to observe and predict the austenitic grain size behavior during the controlled forging of a gear. Arrhenius grain growth kinetic and recrystallization model for a new class of bainitic steel was established for the given strain rate ranges and temperatures. This model was calibrated through microscopic analysis and used to simulate the unpublished constants of low alloyed bainitic forging steel DIN 18MnCrSiMo6-4 microstructure module using DEFORM® commercial finite element code. The increased temperature due to the adiabatic effect was investigated by numerical analysis, demonstrating its influence on grain coarsening. Local tensile test and Charpy-V notch were compared at different industrial hot forging temperatures and local plastic strain. Changes in yield strength and ductility have demonstrated the grain size influence on the processing parameters. The employed numerical model was an efficient tool to predict and present an alternative path to develop robust industrial forging using semi-empirical models.
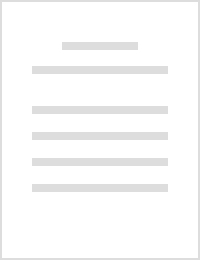
Procedia CIRP
Abstract Electrical Discharge Machining (EDM) is a commonly used process to manufacture of die an... more Abstract Electrical Discharge Machining (EDM) is a commonly used process to manufacture of die and molds, due to the capacity of generating deep and complex cavities. The removal of material occurs from a series of discharges between electrode and workpiece. Discharges melt and vaporize material in form of debris, flushed away by the dielectric flow. This work presents AISI H13 steel surface integrity study, machined by EDM process using constant parameters and a copper electrode with different depths of cavity and pulse times. Textures, crack density, roughness and affected layer were investigated. The collected data was submitted to an ANOVA statistical test. The study showed cavity depth as the only significant factor in roughness. Affected layer thickness is not affected by cavity depth and pulse time. Cracks depth and concentration rise with the increase of pulse time and depth of the cavity.
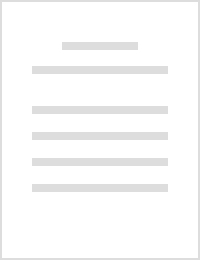
Advances in Materials and Processing Technologies
Abstract Electrical discharging machining is a process that uses high-frequency electrical discha... more Abstract Electrical discharging machining is a process that uses high-frequency electrical discharges to generate heat, melting and vaporising the workpiece material. Melted material is flushed away by dielectric flushing. However, only part of the molten material is removed, the remaining material resolidifies discharge craters, which affects the integrity of the workpiece. This paper discusses how the flushing flow and the radii of electrode under different machining conditions can affect the roughness and affected layer. Rectangular cavities were machined with a copper electrode in AISI H13 steel. Unilateral side flushing with an immersion flushing was used. An analysis of variance was used to verify the statistical relevance of the results. The obtained data appointed that, under the flushing condition used, independent of the electrode radii, some significant differences were found in roughness and scanning electron microscope (SEM) images. No difference was found in affected layer thickness in different analysed positions of flushing path.
Procedia CIRP, 2016
Electrical Discharge Machining (EDM) removes material by melting and vaporization as consequence ... more Electrical Discharge Machining (EDM) removes material by melting and vaporization as consequence of high temperatures generated by highfrequency electrical discharges. This result changes the material integrity, due to the production of an affected layer and micro-cracks. In this study, the integrity generated by the use of unilateral side flushing in EDM was evaluated. The experiment consisted of machining square cavities with different parameters. Analysis of texture, roughness, affected layer and micro-hardness were investigated. The results show variations in the thickness of the affected layer at different positions of the machined cavity and showed changes with machining conditions along the flushing path.
Anais do Congresso Anual da ABM
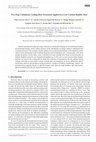
Materials Research
Thermo-mechanical treatments using continuous cooling after forging are an established method for... more Thermo-mechanical treatments using continuous cooling after forging are an established method for producing bainitic steels, mainly because of the elimination of energy intensive additional heat treatment processes. The cooling is usually employed in an uncontrolled manner in the industrial sector, which can be detrimental to the resulting microstructural morphology and, consequently, to the final product properties. In this study, a new controlled two-step cooling route based on the principles of bainitic displacive growth was designed and applied in a 0.18C (wt-%) steel. Inverse finite element method was used on the cooling data to obtain the evolution of temperatures for the samples during cooling, allowing to assess point to point cooling rates. Investigations via X-ray diffraction, optical microscopy analysis and hardness testing revealed a variation of bainitic morphology, namely, the transition from granular bainite to lath-like bainite with relatively high hardness and constituents/ phase boundaries than the pre-treated microstructure.
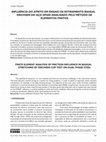
A redução de recursos operacionais, e.g. tempo e matéria prima, é um dos principais desafios da i... more A redução de recursos operacionais, e.g. tempo e matéria prima, é um dos principais desafios da indústria automotiva. A simulação numérica por elementos finitos atua como uma ferramenta computacional importante para a solução destes problemas, de forma a conferir precisão aos resultados calculados quando comparados aos fenômenos reais, ocorridos, por exemplo, em processos de estampagem. Este trabalho tem como objetivo abordar o efeito das condições de atrito utilizando a simulação numérica computacional, em uma chapa bifásica DP600 pelo ensaio de estiramento Erichsen, em que reproduz as condições biaxiais de deformação visando à ductilidade de chapas para estampagem. Criou-se o modelo a partir da inserção dos dados experimentais deste material no software FORGE . Foi observada a influência do coeficiente de atrito durante a simulação numérica na variação das distribuições de pressão, tensão equivalente, redução de espessura e taxa de deformação. Palavras-chave: Coeficiente de atrito; Ensaio Erichsen; Simulação numérica.

Yield strength and toughness in steels are directly associated with hot forging processes, especi... more Yield strength and toughness in steels are directly associated with hot forging processes, especially by controlling austenitic grain size and cooling conditions. The phenomenological JMAK model in macroscale has been applied in different material classes to predict grain size after hot forming. However, on an industrial application, there is still a lack of understanding concerning the synergic effects of strain rate and temperature on recrystallization. This preliminary study aimed at investigating the applicability of coupled semi-empirical JMAK and visco-elastoplastic models in numerical simulation to predict austenitic grain size (PAGS). Hot forging of cylindrical samples of a ferritic-perlitic DIN 20MnCr5 steel was performed followed by water quenching. The main influences, such as temperature, strain and strain rate fields following the recrystallization model were investigated using the subroutine of FORGE NxT 2.1 software. The results were evaluated by comparing experimenta...

Materials Research
It is well recognized the importance of the rheological characterization for the development of t... more It is well recognized the importance of the rheological characterization for the development of the steel in thermomechanical treatments, especially for the mechanical properties improvement of bainitic steels in subsequent hot forging optimization. Therefore, the plastic strain behaviour of a low carbon high silicon bainitic steel was studied through isothermal compression tests using a thermomechanical simulator at temperatures of 1123 K-1423 K and strain rates of 0.1-5 s-1. Arrhenius equation was used to obtain the constitutive constants, which represents the material behaviour of flow stress in high temperature. Besides, work hardening, dynamic recovery, and the JMAK model in the dynamic recrystallization (DRX) of the steel parameters were determined. The second part of this research compared two proposed modified models from the literature, which showed the differences in modelled flow curves behaviour when they are applied for high strain levels. The flow curves were modelled in high strain levels for further implementation in numerical simulation, thus allowing an adjustment of parameters in hot forming processes for this bainitic steel. The proposed models presented an agreement with experimental values. However, only the Avrami equation to DRX showed the dynamic recovery mechanism in high strain levels, which has represented physical behaviour during the thermomechanical process.

Materials Research
Over the last decades, alloy 718 usage has expanded and requirements imposed by its industrial ap... more Over the last decades, alloy 718 usage has expanded and requirements imposed by its industrial applications became more critical. The knowledge about grain boundary character distribution (GBCD) in alloy 718 and its effect on properties improvement is mostly built based on iterative processing through cold rolling steps interspersed with solution annealing. Alloy 718 is found in the industry in many different forms and geometries, and fabricated by multiple thermomechanical processes such as wire drawing, rolling, forging or extrusion. The present study focused on understanding how wires respond to deformation mode related to drawing in regard to GBCD evolution, crystallographic orientation, precipitation of δ-phase and grain size. Lastly, assessing the resulting mechanical properties. The findings show that microstructural evolution is a consequence of competing mechanisms such as strain induced boundary migration, recrystallization, grain growth and phase precipitation. The deformation gradient along wire cross section plays an important role in affecting microstructural features, such as δ precipitation, GBCD and microtexture.
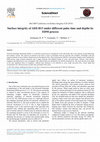
4th CIRP Conference on Surface Integrity (CSI 2018), 2018
Electrical Discharge Machining (EDM) is a commonly used process to manufacture of die and molds, ... more Electrical Discharge Machining (EDM) is a commonly used process to manufacture of die and molds, due to the capacity of generating deep and complex cavities. The removal of material occurs from a series of discharges between electrode and workpiece. Discharges melt and vaporize material in form of debris, flushed away by the dielectric flow. This work presents AISI H13 steel surface integrity study, machined by EDM process using constant parameters and a copper electrode with different depths of cavity and pulse times. Textures, crack density, roughness and affected layer were investigated. The collected data was submitted to an ANOVA statistical test. The study showed cavity depth as the only significant factor in roughness. Affected layer thickness is not affected by cavity depth and pulse time. Cracks depth and concentration rise with the increase of pulse time and depth of the cavity.

Journal Advances in Materials and Processing Technologies , 2016
Electrical discharging machining is a process that uses high-frequency electrical discharges to g... more Electrical discharging machining is a process that uses high-frequency electrical discharges to generate heat, melting and vaporising the workpiece material. Melted material is flushed away by dielectric flushing. However, only part of the molten material is removed, the remaining material resolidifies discharge craters, which affects the integrity of the workpiece. This paper discusses how the flushing flow and the radii of electrode under different machining conditions can affect the roughness and affected layer. Rectangular cavities were machined with a copper electrode in AISI H13 steel. Unilateral side flushing with an immersion flushing was used. An analysis of variance was used to verify the statistical relevance of the results. The obtained data appointed that, under the flushing condition used, independent of the electrode radii, some significant differences were found in roughness and scanning electron microscope (SEM) images. No difference was found in affected layer thickness in different analysed positions of flushing path.

Tecnologia em Minas, Materiais e Mineraçãov. 15, n. 4, , 2018
A redução de recursos operacionais, e.g. tempo e matéria prima, é um dos principais desafios da i... more A redução de recursos operacionais, e.g. tempo e matéria prima, é um dos principais desafios da indústria automotiva. A simulação numérica por elementos finitos atua como uma ferramenta computacional importante para a solução destes
problemas, de forma a conferir precisão aos resultados calculados quando comparados aos fenômenos reais, ocorridos,
por exemplo, em processos de estampagem. Este trabalho tem como objetivo abordar o efeito das condições de atrito
utilizando a simulação numérica computacional, em uma chapa bifásica DP600 pelo ensaio de estiramento Erichsen, em
que reproduz as condições biaxiais de deformação visando à ductilidade de chapas para estampagem. Criou-se o modelo a
partir da inserção dos dados experimentais deste material no software FORGE. Foi observada a influência do coeficiente de atrito durante a simulação numérica na variação das distribuições de pressão, tensão equivalente, redução de espessura
e taxa de deformação.
Uploads
Papers by Dr. Eng. Thiago Marques Ivaniski
problemas, de forma a conferir precisão aos resultados calculados quando comparados aos fenômenos reais, ocorridos,
por exemplo, em processos de estampagem. Este trabalho tem como objetivo abordar o efeito das condições de atrito
utilizando a simulação numérica computacional, em uma chapa bifásica DP600 pelo ensaio de estiramento Erichsen, em
que reproduz as condições biaxiais de deformação visando à ductilidade de chapas para estampagem. Criou-se o modelo a
partir da inserção dos dados experimentais deste material no software FORGE. Foi observada a influência do coeficiente de atrito durante a simulação numérica na variação das distribuições de pressão, tensão equivalente, redução de espessura
e taxa de deformação.
problemas, de forma a conferir precisão aos resultados calculados quando comparados aos fenômenos reais, ocorridos,
por exemplo, em processos de estampagem. Este trabalho tem como objetivo abordar o efeito das condições de atrito
utilizando a simulação numérica computacional, em uma chapa bifásica DP600 pelo ensaio de estiramento Erichsen, em
que reproduz as condições biaxiais de deformação visando à ductilidade de chapas para estampagem. Criou-se o modelo a
partir da inserção dos dados experimentais deste material no software FORGE. Foi observada a influência do coeficiente de atrito durante a simulação numérica na variação das distribuições de pressão, tensão equivalente, redução de espessura
e taxa de deformação.