Archaeological Science by Lesley D. Frame
Journal of Archaeological Science, 2010
Godin Tepe, a large tell situated in western Iran along the Silk Road (High Road) and excavated f... more Godin Tepe, a large tell situated in western Iran along the Silk Road (High Road) and excavated from 1965 to 1973 by T. Cuyler Young, Jr. (Young, 1974, 1972, 1969, 1968; Young and Levine, 1974), yielded over 200 metal artifacts dating to the Early Bronze through Iron Ages. Sixty-nine of these were investigated for this project using traditional metallography and
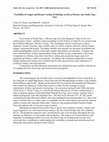
Mater. Res. Soc. Symp. Proc. Vol. 1047, 2007
Excavations at Godin Tepe-a Bronze Age site in the Kangavar Valley of the west-central region of ... more Excavations at Godin Tepe-a Bronze Age site in the Kangavar Valley of the west-central region of Iran-yielded a metal assemblage of 202 artifacts of which 91 are curated at the Royal Ontario Museum, Toronto, Canada. The assemblage consists of decorative objects (figurines, vessels, bracelets, rings, needles, pins) as well as weapons and tools (chisels, blades, daggers, and projectile points). Secondary dendrite arm spacing was measured on polished and etched metallographic sections of the eight samples that display cast structures. Cooling rates were calculated base on these measurements along with the average composition of the metal. Comparison to reference data shows that these cooling rates group into ranges typical of quenched and furnace cooled environments. In addition, the maximum temperatures reached during smelting and casting were estimated based on the microstructure and composition of technical ceramics and slag fragments. Composition and microstructure information was obtained for these artifacts with the use of scanning electron microscopy and electron beam microprobe.
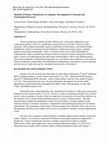
Mater. Res. Soc. Symp. Proc. Vol. 1319, 2011
Faience production methods include efflorescence, direct glaze application, and cementation glazi... more Faience production methods include efflorescence, direct glaze application, and cementation glazing. However, similar processing has been used with a variety of other materials, such as glazed monolithic quartz, ground and re-fired faience, and steatite bodies. Furthermore, faience technology has been linked by similar processing to glass, synthetic pigment and glazing technologies. Here we reinforce these cross-craft relationships by comparing the range of similar functioning chemical elements in faience and glazed artifacts from a variety of archaeological sites that range from the Indus Valley to the Mediterranean. This broad comparative method based primarily on x-ray fluorescence analysis reveals trends in faience production, relationships with metallurgical technologies, and aspects of processing that provide areas of study that may be considered more closely in the future.
Proceedings of the Fifth Forbes Symposium, 2012
Recent examination of ceramic manufacture and crucibles from the copper smelting industry at Tal-... more Recent examination of ceramic manufacture and crucibles from the copper smelting industry at Tal-i Iblis, Iran, dating to the fifth millennium bce, has shown that these technologies are closely related. Similar fabrication methods employing the same clay sources as well as mineral and vegetal tempers were used for the production of the local Lalehzar coarseware and the copper smelting crucibles. The crucible smelting industry at Tal-i Iblis shows careful control of temperature and atmosphere, while at the same time showing high variability in the selection of copper ores used in the smelting operations. This paper discusses the continuity in technological transitions on the Iranian plateau despite the new and experimental aspects of this early example of copper pyrotechnology.
... Authors: Frame, Lesley. Keywords: Godin Metal. Issue Date: 6-May-2011. Abstract: This documen... more ... Authors: Frame, Lesley. Keywords: Godin Metal. Issue Date: 6-May-2011. Abstract: This document is the Masters of Science thesis written by Lesley D. Frame about the metal finds from Godin Tepe. It contains her full analysis of select metal objects from the site. ...
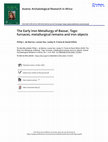
Azania: Archaeological Research in Africa , 2020
An extensive iron production industry flourished in the Bassar region of northern Togo from as ea... more An extensive iron production industry flourished in the Bassar region of northern Togo from as early as the Early Iron Age. However, it was during the Later Iron Age that this witnessed a period of rapid growth, with locally produced iron increasingly feeding into regional trade networks. This paper discusses the archaeology, archaeometallurgy and metallography of the earliest iron production in Bassar through the examination of two sites. The first, BAS-252 (Dekpassanware), is a large ironworking village (in operation throughout the Early and Later Iron Ages) with six zones devoted primarily to smithing. The second, the nearby site of BAS-273, was found to be a smaller smelting site and operated in the Early Iron Age. The paper presents a metallographic analysis of the EIA iron artefacts excavated at BAS-252, in conjunction with an archaeometallurgical analysis of EIA smelting remains from BAS-273. The close association of smithing and smelting sites has provided an unparalleled opportunity to consider the chaîne opératoire of iron production in EIA Bassar, with insights into the production of iron alloyed with carbon and phosphorus and the possible symbolic behaviours of past smelters at a time when the foundations were being laid for Bassar to develop subsequently into a regional hub of iron production.
Manufacturing and Materials Properties by Lesley D. Frame
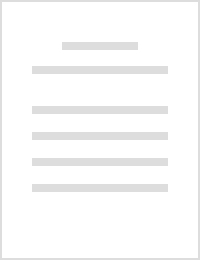
Journal of Materials Engineering and Performance, 2020
Machining and thermal processing can introduce undesirable residual stresses and distortion in ti... more Machining and thermal processing can introduce undesirable residual stresses and distortion in titanium alloy components, and although the distribution and magnitude of these residual stresses is highly relevant for component and process design in the aerospace industry, the relationships between processing variables, processing steps, residual stress signature, and subsurface microstructures are not well understood. The current study reports on the preliminary results of experiments designed to mimic typical machining and thermal processing practices for aerospace alpha-beta Ti alloys. Traditional climb cutting and high-speed peel cutting operations are included in CNC machining experiments, and both solution treating and aging heat treatments are considered for thermal processing experiments. Characterization of samples includes strain measurement using the sin2ψ and cosine α methods with x-ray diffraction as well as microstructural characterization using traditional metallographic techniques. The results of this study show a large tool-path dependence for residual stresses in machined surfaces as well as a significant difference in the residual stress behavior for solution treated and quenched compared to solution treated and aged samples of Ti 6Al-4V alloy.
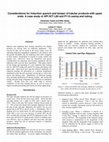
Proceedings of Heat Treat 2017, ASM, 2017
Quench and tempering heat treating operations for tubular products are relying more on induction ... more Quench and tempering heat treating operations for tubular products are relying more on induction equipment. The reasons for this can be traced to the lower energy costs for operating induction equipment compared to gas furnaces and the greater flexibility that the induction lines offer compared to their furnace counterparts in regards to recipe control and product mix. However, there are limitations and special considerations for induction heat treating equipment and the induction coils used for these operations. This paper reports on the design and operation of a new induction heat treating line for API 5CT grade L80 and P110 casing and tubing with upset ends. Upset ends pose special technical challenges for induction heating; the generation of a uniform temperature distribution relies heavily on proper coil design as well as line layout and heating time. Simulations of induction heating have provided predictions of heating profiles, and on-the-line testing allowed recipe refinement and validation of simulation models. Results from this case study help to increase confidence in this heat treating process as well as create an improved induction heating line layout for future applications.
Proceedings of Heat Treat 2017, ASM, 2017
High frequency welding is a thermo-mechanical process that relies on precise heat input as well a... more High frequency welding is a thermo-mechanical process that relies on precise heat input as well as mechanical control as strip edges are heated and forged together to result in a seam weld. Heat input can be defined as a way of characterizing the temperature distribution at the strip edges prior to forging them together. Heat input is affected by several process variables ranging from raw material properties to welder settings and weld area setup. These are summarized in this paper, with special attention on the effects of welder frequency, welder power, line speed, and steel alloy composition on heat input and the resulting weld quality. Frequencies in the range of 100-800 kHz are considered. Data from tube mills (including general data and controlled on-the-mill experiments) and laboratory evaluations are included in this paper.
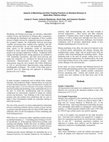
Proceedings of Heat Treat 2019, ASM, 2019
Machining and thermal processing can introduce undesirable residual stresses and distortion in ti... more Machining and thermal processing can introduce undesirable residual stresses and distortion in titanium alloy components, and although the distribution and magnitude of these residual stresses is highly relevant for component and process design in the aerospace industry, the relationships between processing variables, processing steps, residual stress signature, and sub-surface microstructures are not well understood. The current study reports on the preliminary results of experiments designed to mimic typical machining and thermal processing practices for aerospace alpha-beta Ti alloys. Traditional climb cutting and high-speed peel cutting operations are included in CNC machining experiments, and both stress-relieving and aging heat treatments are considered for thermal processing experiments. Characterization of samples includes strain measurement using the sin 2 method with X-Ray Diffraction as well as microstructural characterization using traditional metallographic techniques. The results of this study point to potential areas for improving tool approach in machining practices for - Ti alloys.
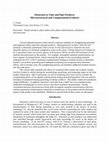
Current industrial practices often involve extensive methods for straightening quenched and tempe... more Current industrial practices often involve extensive methods for straightening quenched and tempered carbon steel tube and pipe products. Relying heavily on these " after-the-fact " methods is inherently problematic both in terms of time and resources; therefore the more desirable option is to eliminate straightness issues at the outset. During Quench and Temper (Q & T) operations, there are several aspects of the process which can allow the formation of non-uniform microstructures in the product. For example, incomplete austenite transformation can leave regions of retained ferrite, which constrain the product as the surrounding austenite undergoes the FCC to BCT martensite transformation leading to residual stresses or distortion. Further, non-uniform quenching and inadequate tempering can compound these distortion effects, and in extreme cases, the straightening process can introduce additional residual stresses into the work piece. The current study examines the effects of variations bulk volume due to phase volume fractions formed or altered during the austenitizing, quenching, and tempering stages on the final product dimensions. Q&T experiments, as well as modeling, have been used to consider the compounding effects of incomplete transformation during austenitizing paired with non-uniform formation of martensite during quenching of tubular products. The author conducted simulations using SolidWorks. In addition, distorted 1 inch tube from a Q&T line was examined using traditional metallography as well as micro-and macro-hardness measurements. Strong correlations between microstructure (from both incomplete austenite transformation and non-uniform martensite transformation around the circumference of the product) and the distortion pattern of the product were identified. Methods to prevent both of these issues are discussed.
Papers by Lesley D. Frame
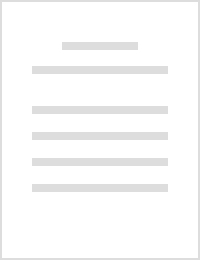
Current industrial practices often involve extensive methods for straightening quenched and tempe... more Current industrial practices often involve extensive methods for straightening quenched and tempered carbon steel tube and pipe products. Relying heavily on these " after-the-fact " methods is inherently problematic both in terms of time and resources; therefore the more desirable option is to eliminate straightness issues at the outset. During Quench and Temper (Q & T) operations, there are several aspects of the process which can allow the formation of non-uniform microstructures in the product. For example, incomplete austenite transformation can leave regions of retained ferrite, which constrain the product as the surrounding austenite undergoes the FCC to BCT martensite transformation leading to residual stresses or distortion. Further, non-uniform quenching and inadequate tempering can compound these distortion effects, and in extreme cases, the straightening process can introduce additional residual stresses into the work piece. The current study examines the effects of variations bulk volume due to phase volume fractions formed or altered during the austenitizing, quenching, and tempering stages on the final product dimensions. Q&T experiments, as well as modeling, have been used to consider the compounding effects of incomplete transformation during austenitizing paired with non-uniform formation of martensite during quenching of tubular products. The author conducted simulations using SolidWorks. In addition, distorted 1 inch tube from a Q&T line was examined using traditional metallography as well as micro-and macro-hardness measurements. Strong correlations between microstructure (from both incomplete austenite transformation and non-uniform martensite transformation around the circumference of the product) and the distortion pattern of the product were identified. Methods to prevent both of these issues are discussed.
High frequency welding is a thermo-mechanical process that relies on precise heat input as well a... more High frequency welding is a thermo-mechanical process that relies on precise heat input as well as mechanical control as strip edges are heated and forged together to result in a seam weld. Heat input can be defined as a way of characterizing the temperature distribution at the strip edges prior to forging them together. Heat input is affected by several process variables ranging from raw material properties to welder settings and weld area setup. These are summarized in this paper, with special attention on the effects of welder frequency, welder power, line speed, and steel alloy composition on heat input and the resulting weld quality. Frequencies in the range of 100-800 kHz are considered. Data from tube mills (including general data and controlled on-the-mill experiments) and laboratory evaluations are included in this paper.
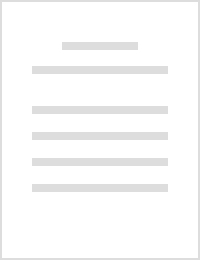
A coupled thermomechanical finite element analysis is performed in order to simulate orthogonal c... more A coupled thermomechanical finite element analysis is performed in order to simulate orthogonal cutting of normalized AISI 9310. Damage parameters are optimized to define the behavior of the material subjected to orthogonal cutting. AISI 1045, AISI 4140, and A2024-T351 are selected as precursors to validating the present finite element approach for orthogonal cutting of normalized AISI 9310. The numerical results obtained in this study include the average cutting force, residual stresses and strains, chip morphology, and tool temperature. These results are validated for each material with experimental results found in literature. The current study optimizes the Johnson–Cook damage parameters for steel materials in order to capture physical chip morphology. A correlation analysis is then performed using the validated finite element model for the AISI 9310 material to better understand the effect of specific input parameters such as the damage parameters, coefficient of friction, frac...

Heat Treat 2021: Proceedings from the 31st Heat Treating Society Conference and Exposition
Determination of flow stress behavior of materials is a critical aspect of understanding and pred... more Determination of flow stress behavior of materials is a critical aspect of understanding and predicting behavior of materials during manufacturing and use. However, accurately capturing the flow stress behavior of a material at different strain rates and temperatures can be challenging. Non-uniform deformation and thermal gradients within the test sample make it difficult to match test results directly to constitutive equations that describe the material behavior. In this study, we have tested AISI 9310 steel using a Gleeble 3500 physical simulator and Digital Image Correlation system to capture transient mechanical properties at elevated temperatures (300°C – 600°C) while controlling strain rate (0.01 s-1 to 0.1 s-1). The data presented here illustrate the benefit of capturing non-uniform plastic strain of the test specimens along the sample length, and we characterize the differences between different test modes and the impact of the resulting data that describe the flow stress be...
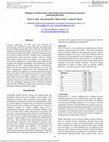
Heat Treat 2021: Proceedings from the 31st Heat Treating Society Conference and Exposition
Vacuum carburizing of 9310 gear steel followed by austenitizing, oil quench, cryogenic treatment,... more Vacuum carburizing of 9310 gear steel followed by austenitizing, oil quench, cryogenic treatment, and tempering is known to impact residual stress state of the steel. Residual stress magnitude and depth distribution can have adverse effects on part distortion during intermediary and finish machining steps. The present research provides residual stress measurement, microstructural, and mechanical property data for samples taken along a specific heat treat sequence. Test rings of AISI 9310 steel are subjected to a representative gear manufacturing sequence that includes normalizing, rough machining, vacuum carburizing to 0.03”, austenitizing, quench, cryo-treatment, temper, and finish machining. Characterization of a test ring and a metallurgical sample after each manufacturing step allows tracking of residual stress and microstructural changes along the sequence. The results presented here are particularly interesting because the highest compressive residual stresses appear after rem...
Uploads
Archaeological Science by Lesley D. Frame
Manufacturing and Materials Properties by Lesley D. Frame
Papers by Lesley D. Frame