Papers by aslan khani sheykh rajab
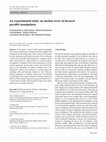
The International Journal of Advanced Manufacturing Technology, 2014
In this paper, a novel 6-DOF parallel manipulator with coaxial actuated arms is introduced and in... more In this paper, a novel 6-DOF parallel manipulator with coaxial actuated arms is introduced and investigated. This mechanism has six rotating arms, and by rotation of arms about the base, positioning and desired movement of the mechanism is achieved. Sine parallel mechanisms have a nonlinear motion while moving from an initial position to a desired position, investigation of nonlinear error in such mechanisms is of paramount importance. In this paper, inverse and forward kinematics of the mechanism are studied. Nonlinear error of the mechanism's motion in its workspace is extracted using midoscillating circle and kinematic relations as well. Moreover, effective parameters on nonlinear motion error of mechanism are determined. The results obtained by theoretical method are further verified through image processing experimental tests. It is found that the results of the theoretical analysis and experimental test are in good consistency.
Advanced Materials Research, 2011
Machine tool vibrations have great impact on machining process. In this paper the dynamic behavio... more Machine tool vibrations have great impact on machining process. In this paper the dynamic behavior and modal parameters of milling machine is presented. For this purpose, the CAD model of the milling machine structure is provided in CATIA and then Natural frequencies and mode shapes of the machine tool structure are carried out through FEM modal analysis under ANSYS Workbench. The model is evaluated and corrected with experimental results by modal testing on FP4M milling machine. Finally, the natural frequencies and mode shapes obtained by both experimental and FEM modal analysis are compared. The results of two methods are in widely agreement.
Advanced Materials Research, 2012
Machine tool vibrations have great impact on machining process. In this paper the dynamic behavio... more Machine tool vibrations have great impact on machining process. In this paper the dynamic behavior and modal parameters of surface grinding machine is presented. For this purpose, the CAD (computer aided design) model of the surface grinding machine structure is provided in catia and then Natural frequencies and mode shapes of the machine tool structure are carried out through FEM (finite element method) modal analysis under ansys. The model is evaluated and corrected with experimental results by modal testing on surface grinding machine. Finally, the natural frequencies and mode shapes obtained by both experimental and FEM modal analysis are compared. The results of two methods are in widely agreement.

The International Journal of Advanced Manufacturing Technology, 2014
In this paper, a novel 6-DOF parallel manipulator with coaxial actuated arms is introduced and in... more In this paper, a novel 6-DOF parallel manipulator with coaxial actuated arms is introduced and investigated. This mechanism has six rotating arms, and by rotation of arms about the base, positioning and desired movement of the mechanism is achieved. Sine parallel mechanisms have a nonlinear motion while moving from an initial position to a desired position, investigation of nonlinear error in such mechanisms is of paramount importance. In this paper, inverse and forward kinematics of the mechanism are studied. Nonlinear error of the mechanism's motion in its workspace is extracted using midoscillating circle and kinematic relations as well. Moreover, effective parameters on nonlinear motion error of mechanism are determined. The results obtained by theoretical method are further verified through image processing experimental tests. It is found that the results of the theoretical analysis and experimental test are in good consistency.
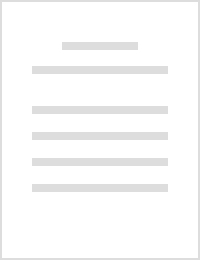
Robotica, 2014
SUMMARYParallel mechanisms possess several advantages such as the possibilities for high accelera... more SUMMARYParallel mechanisms possess several advantages such as the possibilities for high acceleration and high accuracy positioning of the end effector. However, most of the proposed parallel manipulators suffer from a limited workspace. In this paper, a novel 6-DOF parallel manipulator with coaxial actuated arms is introduced. Since parallel mechanisms have more workspace limitations compared to that of serial mechanisms, determination of the workspace in parallel manipulators is of the utmost importance. For finding position, angular velocity, and acceleration, in this paper, inverse and forward kinematics of the mechanism are studied and after presenting the workspace limitations, workspace analysis of the hexarot manipulator is performed by using MATLAB software. Next, using the obtained cloud of points from simulation, the overall borders of the workspace are illustrated. Finally, it is shown that this manipulator has the important benefits of combining a large positional works...

Robotica, 2015
Parallel mechanisms possess several advantages such as the possibilities for high acceleration an... more Parallel mechanisms possess several advantages such as the possibilities for high acceleration and high accuracy positioning of the end effector. However, most of the proposed parallel manipulators suffer from a limited workspace. In this paper, a novel 6-DOF parallel manipulator with coaxial actuated arms is introduced. Since parallel mechanisms have more workspace limitations compared to that of serial mechanisms, determination of the workspace in parallel manipulators is of the utmost importance. For finding position, angular velocity, and acceleration, in this paper, inverse and forward kinematics of the mechanism are studied and after presenting the workspace limitations, workspace analysis of the hexarot manipulator is performed by using MATLAB software. Next, using the obtained cloud of points from simulation, the overall borders of the workspace are illustrated. Finally, it is shown that this manipulator has the important benefits of combining a large positional workspace in relation to its footprint with a sizable range of platform rotations.
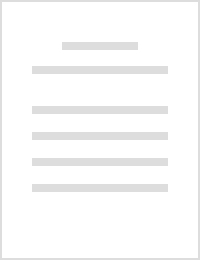
AIM OF THE PROJECT 1 - stair climbing to be quite intelligent image processing system to a height... more AIM OF THE PROJECT 1 - stair climbing to be quite intelligent image processing system to a height of 25 cm 2 - Crossing the Bridge to the pit or pits or raceway without having a width of 80 cm to be quite intelligent image processing system 3 - Raising a disabled wheelchair seat height to the height of about one meter every time a disabled person wants to move in the same state 4 - The final speed of 27 kilometers per hour (as a vehicle for disabled people ) 5 - Handling very easy ( the wheelchair for easy disassembly and separate into 8 pieces and includes a removable passenger car 6 - wheelchair batteries charged by solar batteries 7-Controll system via manual control system and image process auto controlling and computer brain interface system GENERAL INFORMATION ABOUT THE PROJECT Wheelchair movement generally by mechanical force on the thrust ring is installed on the rear wheel rim are being This method of movement, limitations and complications, especially in wheelchair riders ...

AIM OF THE PROJECT Dentistry is the branch of medicine that requires a lot of power for a dentist... more AIM OF THE PROJECT Dentistry is the branch of medicine that requires a lot of power for a dentist. To enhance the quality of dental services and avoid all the problems mentioned and For ease of operation such as (Anesthetic infusion, X-RAY Photography, Time Management and milling tooth and …) we have decided to design this robot to earn these benefits: 1- avoid touch the Dental ando system to lips and tongue 2- Tooth milling operations by robot 3- dental radiography by robot 4- video record via robot system in 5MP resolution 5- Anesthetic infusion To the target by robot 6- Time management 7- reduce of the extra costs 8- to avoid being exposed to infectious agents such as practitioners (HCV, HBV «hepatitis B, C», and bacterial and fungal infections) 9- Prevention of Musculoskeletal Disorders as "back pain, wrist pain, headaches, shoulder pain, back pain, neck pain" 10- Avoid visual fatigue and premature fatigue. 11- Avoid exposure to noise pollution 12- Abatement of exposur...
. Machine tool vibrations have great impact on machining process. In this paper the dynamic
beh... more . Machine tool vibrations have great impact on machining process. In this paper the dynamic
behavior and modal parameters of milling machine is presented. For this purpose, the CAD model of
the milling machine structure is provided in CATIA and then Natural frequencies and mode shapes of
the machine tool structure are carried out through FEM modal analysis under ANSYS Workbench.
The model is evaluated and corrected with experimental results by modal testing on FP4M milling
machine. Finally, the natural frequencies and mode shapes obtained by both experimental and FEM
modal analysis are compared. The results of two methods are in widely agreement.
Machine tool vibrations have great impact on machining process. In this paper the
... more Machine tool vibrations have great impact on machining process. In this paper the
dynamic behavior and modal parameters of surface grinding machine is presented. For this purpose,
the CAD (computer aided design) model of the surface grinding machine structure is provided in
catia and then Natural frequencies and mode shapes of the machine tool structure are carried out
through FEM (finite element method) modal analysis under ansys. The model is evaluated and
corrected with experimental results by modal testing on surface grinding machine. Finally, the
natural frequencies and mode shapes obtained by both experimental and FEM modal analysis are
compared. The results of two methods are in widely agreement.

Parallel mechanisms possess several advantages such as the possibilities for high acceleration an... more Parallel mechanisms possess several advantages such as the possibilities for high acceleration and
high accuracy positioning of the end effector. However, most of the proposed parallel manipulators
suffer from a limited workspace. In this paper, a novel 6-DOF parallel manipulator with coaxial
actuated arms is introduced. Since parallel mechanisms have more workspace limitations compared
to that of serial mechanisms, determination of the workspace in parallel manipulators is of the
utmost importance. For finding position, angular velocity, and acceleration, in this paper, inverse and
forward kinematics of the mechanism are studied and after presenting the workspace limitations,
workspace analysis of the hexarot manipulator is performed by using MATLAB software. Next,
using the obtained cloud of points from simulation, the overall borders of the workspace are
illustrated. Finally, it is shown that this manipulator has the important benefits of combining a large
positional workspace in relation to its footprint with a sizable range of platform rotations.
KEYWORDS: Parallel manipulator; Hexarot; Kinematics; Jacobian matrix; Workspace

a novel 6-DOF parallel manipulator
with coaxial actuated arms is introduced and investigated. T... more a novel 6-DOF parallel manipulator
with coaxial actuated arms is introduced and investigated. This
mechanismhassixrotatingarms,andbyrotationofarmsabout
the base, positioning and desired movement of the mechanism
is achieved. Sine parallel mechanisms have a nonlinear motion
while moving from an initial position to a desired position,
investigation of nonlinear error in such mechanisms is of par-
amount importance. In this paper, inverse and forward kine-
matics of the mechanism are studied. Nonlinear error of the
mechanism’s motion in its workspace is extracted using mid-
oscillating circle and kinematic relations as well. Moreover,
effective parameters on nonlinear motion error of mechanism
are determined. The results obtained by theoretical method are
further verified through image processing experimental tests. It
is found that the results of the theoretical analysis and experi-
mental test are in good consistency.
Uploads
Papers by aslan khani sheykh rajab
behavior and modal parameters of milling machine is presented. For this purpose, the CAD model of
the milling machine structure is provided in CATIA and then Natural frequencies and mode shapes of
the machine tool structure are carried out through FEM modal analysis under ANSYS Workbench.
The model is evaluated and corrected with experimental results by modal testing on FP4M milling
machine. Finally, the natural frequencies and mode shapes obtained by both experimental and FEM
modal analysis are compared. The results of two methods are in widely agreement.
dynamic behavior and modal parameters of surface grinding machine is presented. For this purpose,
the CAD (computer aided design) model of the surface grinding machine structure is provided in
catia and then Natural frequencies and mode shapes of the machine tool structure are carried out
through FEM (finite element method) modal analysis under ansys. The model is evaluated and
corrected with experimental results by modal testing on surface grinding machine. Finally, the
natural frequencies and mode shapes obtained by both experimental and FEM modal analysis are
compared. The results of two methods are in widely agreement.
high accuracy positioning of the end effector. However, most of the proposed parallel manipulators
suffer from a limited workspace. In this paper, a novel 6-DOF parallel manipulator with coaxial
actuated arms is introduced. Since parallel mechanisms have more workspace limitations compared
to that of serial mechanisms, determination of the workspace in parallel manipulators is of the
utmost importance. For finding position, angular velocity, and acceleration, in this paper, inverse and
forward kinematics of the mechanism are studied and after presenting the workspace limitations,
workspace analysis of the hexarot manipulator is performed by using MATLAB software. Next,
using the obtained cloud of points from simulation, the overall borders of the workspace are
illustrated. Finally, it is shown that this manipulator has the important benefits of combining a large
positional workspace in relation to its footprint with a sizable range of platform rotations.
KEYWORDS: Parallel manipulator; Hexarot; Kinematics; Jacobian matrix; Workspace
with coaxial actuated arms is introduced and investigated. This
mechanismhassixrotatingarms,andbyrotationofarmsabout
the base, positioning and desired movement of the mechanism
is achieved. Sine parallel mechanisms have a nonlinear motion
while moving from an initial position to a desired position,
investigation of nonlinear error in such mechanisms is of par-
amount importance. In this paper, inverse and forward kine-
matics of the mechanism are studied. Nonlinear error of the
mechanism’s motion in its workspace is extracted using mid-
oscillating circle and kinematic relations as well. Moreover,
effective parameters on nonlinear motion error of mechanism
are determined. The results obtained by theoretical method are
further verified through image processing experimental tests. It
is found that the results of the theoretical analysis and experi-
mental test are in good consistency.
behavior and modal parameters of milling machine is presented. For this purpose, the CAD model of
the milling machine structure is provided in CATIA and then Natural frequencies and mode shapes of
the machine tool structure are carried out through FEM modal analysis under ANSYS Workbench.
The model is evaluated and corrected with experimental results by modal testing on FP4M milling
machine. Finally, the natural frequencies and mode shapes obtained by both experimental and FEM
modal analysis are compared. The results of two methods are in widely agreement.
dynamic behavior and modal parameters of surface grinding machine is presented. For this purpose,
the CAD (computer aided design) model of the surface grinding machine structure is provided in
catia and then Natural frequencies and mode shapes of the machine tool structure are carried out
through FEM (finite element method) modal analysis under ansys. The model is evaluated and
corrected with experimental results by modal testing on surface grinding machine. Finally, the
natural frequencies and mode shapes obtained by both experimental and FEM modal analysis are
compared. The results of two methods are in widely agreement.
high accuracy positioning of the end effector. However, most of the proposed parallel manipulators
suffer from a limited workspace. In this paper, a novel 6-DOF parallel manipulator with coaxial
actuated arms is introduced. Since parallel mechanisms have more workspace limitations compared
to that of serial mechanisms, determination of the workspace in parallel manipulators is of the
utmost importance. For finding position, angular velocity, and acceleration, in this paper, inverse and
forward kinematics of the mechanism are studied and after presenting the workspace limitations,
workspace analysis of the hexarot manipulator is performed by using MATLAB software. Next,
using the obtained cloud of points from simulation, the overall borders of the workspace are
illustrated. Finally, it is shown that this manipulator has the important benefits of combining a large
positional workspace in relation to its footprint with a sizable range of platform rotations.
KEYWORDS: Parallel manipulator; Hexarot; Kinematics; Jacobian matrix; Workspace
with coaxial actuated arms is introduced and investigated. This
mechanismhassixrotatingarms,andbyrotationofarmsabout
the base, positioning and desired movement of the mechanism
is achieved. Sine parallel mechanisms have a nonlinear motion
while moving from an initial position to a desired position,
investigation of nonlinear error in such mechanisms is of par-
amount importance. In this paper, inverse and forward kine-
matics of the mechanism are studied. Nonlinear error of the
mechanism’s motion in its workspace is extracted using mid-
oscillating circle and kinematic relations as well. Moreover,
effective parameters on nonlinear motion error of mechanism
are determined. The results obtained by theoretical method are
further verified through image processing experimental tests. It
is found that the results of the theoretical analysis and experi-
mental test are in good consistency.