Drafts by Prof S.H. Masood
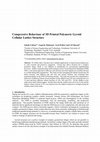
3D cellular lattice structures have multiple applications in engineering including uses in crash ... more 3D cellular lattice structures have multiple applications in engineering including uses in crash resistant and protective equipment. Gyroid type lattice structure has a complex geometric shape, which is very difficult to manufacture by conventional manufacturing processes. Additive manufacturing (AM) technique such as Fused Deposition Modelling (FDM) offers a convenient approach to fabricate such structure provided supports are carefully selected or avoided during their manufacture. This study involves designing the Schoen Gyroid type 3D lattice structure with different unit cell sizes and volume fractions and evaluating their manufacturability on the FDM 3D Printing machine. The study also presents the comprehensive behaviour of different Schoen Gyroid samples of four different unit cell sizes (ranging from 6 to 12 mm) and three different volume fractions of 14%, 20% and 25%. All the samples in this study where built without support. Results show that the smallest unit cell of size 6 mm and the highest volume fraction of 25% was found to have the highest compressive strength among the samples tested in this study. 1. Introduction During last twenty-five years, Additive Manufacturing (AM) has generated a significant impact on the techniques for producing complex cellular structures. Among various AM technologies, the Fused Deposition Modelling (FDM) is a polymer based process, which uses thermoplastic as the working material. The FDM is currently dominantly used for prototyping, modelling, and production applications. The possible limitations of FDM could be the longer build time and restricted set of materials but its significant advantages are that the FDM process is less complicated, safe and clean and compact. The FDM process allows removable supports, which is distinctly advantageous in producing complex geometrical shapes, which would otherwise have been extremely challenging to build through traditional manufacturing methods [1]. However, in manufacturing the complex cellular lattice structure by FDM, the support structures are not desirable because these would be very tedious to remove and result in wastage of material and energy.
Papers by Prof S.H. Masood
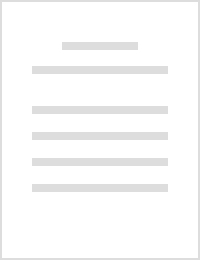
International Journal of Machine Tools and Manufacture, 2011
Laser-assisted machining has been considered as an alternative for hard-to-wear materials such as... more Laser-assisted machining has been considered as an alternative for hard-to-wear materials such as metallic alloys and ceramics. Machining of some materials such as high chromium alloys and high strength steels is still a delicate and challenging task and has received little attention. Conventional computer numerical control machines and cutting tools cannot adapt easily to such materials and induce very high tooling costs for operations of rough machining or finishing. This paper presents the results of research conducted on laser-assisted machining of one such hard-to-wear materials, high chromium white cast iron, used in making heavy duty mineral processing equipment for the mining industry. In particular, the effect of laser on temperature, cutting forces, surface profile, hardness and cutting chips are presented. Results show that laser-assisted machining causes more frequent shearing of material, less uniform surface formation, and the heat penetration increases as the distance between laser spot and tool increases. It also leads to reduction in cutting forces with expected improvement in tool life. The results indicate that laser-assisted machining of high chromium white cast iron shows potential to be a feasible alternative to hard machining of such materials.
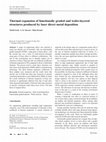
The International Journal of Advanced Manufacturing Technology, 2013
A range of engineering alloys was selected to create two distinct sets of structures. One was fun... more A range of engineering alloys was selected to create two distinct sets of structures. One was functionally graded materials (FGM)-using pairs of these alloys-and the second type was a series of wafer-layered structures using pairs of these alloys in different combinations. The aim of this investigation was to identify unique sets of structures of alloys which provide very different coefficients of thermal expansion (CTE) compared to those of individual elements. The process used to create these structures was laser direct metal deposition (DMD) additive manufacturing technology. The linear thermal expansion coefficients of these samples were measured and the results show that specific sets of FGM and wafer type structures of specific constituent metal alloys can be fabricated by DMD, in which the overall coefficient of thermal expansion of these new structures is significantly different from that of each alloy when measured individually. FGM and wafer type structures of specific constituent metal alloys have lower CTE than those of original alloys.
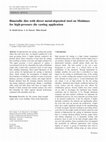
The International Journal of Advanced Manufacturing Technology, 2010
In high-pressure die casting, cooling time greatly affects the total cycle time. As thermal condu... more In high-pressure die casting, cooling time greatly affects the total cycle time. As thermal conductivity is the main governing factor, a higher thermal conductive die material allows faster extraction of heat from the casting, thus resulting in shorter cycle time and higher productivity. This paper presents a novel approach to replace a conventional steel die by a bimetallic die made of Moldmax copper alloy coated with a protective layer of steel using laser cladding technology, direct metal deposition on the cavity surface for high-pressure die casting of aluminum alloys. Study includes the investigation of suitable steel layer thickness on Moldmax substrate in terms of porosity, hardness, presence of copper content, and copper particle. Results obtained from the scanning electron microscope and energy dispersive spectroscopy display a metallurgicallly sound and fully dense steel layer on copper alloy. Results of finite element heat transfer analysis also show that bimetallic die offers superior thermal performance compared with monolithic steel die.
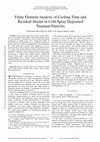
In this article, using finite element analysis (FEA) and an X-ray diffractometer (XRD), cold-spra... more In this article, using finite element analysis (FEA) and an X-ray diffractometer (XRD), cold-sprayed titanium particles on a steel substrate is investigated in term of cooling time and the development of residual strains. Three cooling-down models of sprayed particles after deposition stage are simulated and discussed: the first model (m1) considers conduction effect to the substrate only, the second model (m2) considers both conduction as well as convection effect to the environment, and the third model (m3) which is the same as the second model but with the substrate heated to a near particle temperature before spraying. Thereafter, residual strains developed in the third model is compared with the experimental measurement of residual strains, which involved a Bruker D8 Advance Diffractometer using CuKa radiation (40kV, 40mA) monochromatised with a graphite sample monochromator. For deposition conditions of this study, a good correlation was found to exist between the FEA results ...
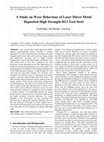
Manufacturing Science and Technology, 2015
Laser assisted direct metal deposition (DMD) additive manufacturing process provides a realistic ... more Laser assisted direct metal deposition (DMD) additive manufacturing process provides a realistic opportunity to create solid and porous structures from high strength metallic alloys that can be used as coatings, foams and sandwiched structures and as highly stressed components in contact with other metallic components. Very little studies seem to have been reported on the wear behaviour of parts fabricated by the laser DMD process in relation to various design parameters for various metals. This paper presents an investigation on the sliding wear behaviour of the DMD generated structures of high strength H13 tool steel using the pin-on-disc machine. The structures were machined and finished as pins for subsequent wear testing against a solid disc made of high carbon steel surface. The study includes effect on abrasive wear by variation of several design variables which include contact load, sliding speed and sliding distance. The mode of wear is chosen to be severe which consists of dry wear and speeds near or above 1 m/s. Wear volume and coefficient of frictions are the two main wear parameters analysed in combination with the primary or design variables. The relationship between the design factors and the ensuing wear loss is discussed which proves the highly non-linear frictional behaviour. The results highlight a wear performance for laser generated H13 specimen that is strong and consistent although inferior to the wear behaviour of wrought tool steels. Despite lack of hot and cold working and any heat treatment, H13 specimens show little signs of micro-chipping and flaking under high loads.
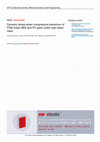
IOP Conference Series: Materials Science and Engineering, 2018
This paper presents an investigation on dynamic compressive behavior of ABS and Polycarbonate (PC... more This paper presents an investigation on dynamic compressive behavior of ABS and Polycarbonate (PC) parts fabricated by Fused Deposition Modelling (FDM) additive manufacturing process when such parts are subjected to high strain rate loading conditions in engineering applications. Split Hopkinson Pressure Bar was used to carry out high strain rate compression tests on cylindrical test specimens fabricated by the FDM process using different FDM process parameters. The dynamic true stress strain curves at high strain rates were compared with quasi-static curves obtained from static compression tests at low strain rates. Results of dynamic compression tests show that FDM process parameter of build style has significant influence on the dynamic response of FDM made ABS and PC parts under high strain rate loading. FDM made PC materials exhibit higher compressive stress than ABS material under static and dynamic conditions. FDM parameters also affect the static compressive strength for both materials.
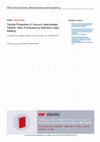
IOP Conference Series: Materials Science and Engineering, 2018
This study presents an investigation on the tensile behaviour of heat-treated titanium alloy (Ti6... more This study presents an investigation on the tensile behaviour of heat-treated titanium alloy (Ti6Al4V) parts, which have been manufactured by Selective Laser Melting (SLM) additive manufacturing. The parts were heat treated at a temperature of 850ºC for 2 hours with and without Argon inert gas in a vacuum furnace. The tensile properties of the SLM samples with and without heat treatment have been compared to evaluate the mechanical performance of the 3D printed samples. The ultimate tensile strength (UTS) of as built Ti6Al4V part was found to be1175 MPa. The UTS of heat-treated Ti6Al4V sample in vacuum without Argon gas was found to be 750MPa, while the UTS of heat-treated sample in vacuum with Argon gas was recorded as 980MPa. These values compare well with other published values of UTS for SLM built Ti6Al4V alloys with similar heat-treated conditions. The work also studied the microhardness of all the samples and compared the values with each other and found that the heat treated sample have lower average Vickers hardness values compared to as built samples.
IOP Conference Series: Materials Science and Engineering, 2018
In this study, an economically-viable methodology is discussed where a blend of postconsumer recy... more In this study, an economically-viable methodology is discussed where a blend of postconsumer recycled (PCR) plastics and post-industrial scrap (PIS) polymers is refined and used as the feedstock for manufacturing of interior structural products for automotive industry. A comprehensive thermo-mechanical characterisation suggest that feedstock obtained using a meltfiltering based refin ing process, offers performance on par with the virgin materials with reduced cost and environmental impact. Using both lab-scale prototyping and pilot plant trials, interior trim parts have successfully been produced to demonstrate the viability of using this new feedstock in mainstream polymer production processes such as injection moulding and thermoforming for automotive applications.
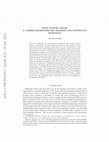
Journal of Thermal Spray Technology, 2017
Motivated by constructions in topological data analysis and algebraic combinatorics, we study hom... more Motivated by constructions in topological data analysis and algebraic combinatorics, we study homotopy theory on the category of ÄŒech closure spaces Cl, the category whose objects are sets endowed with a ÄŒech closure operator and whose morphisms are the continuous maps between them. We introduce new classes of ÄŒech closure structures on metric spaces, graphs, and simplicial complexes, and we show how each of these cases gives rise to an interesting homotopy theory. In particular, we show that there exists a natural family of ÄŒech closure structures on metric spaces which produces a non-trivial homotopy theory for finite metric spaces, i.e. point clouds, the spaces of interest in topological data analysis. We then give a ÄŒech closure structure to graphs and simplicial complexes which may be used to construct a new combinatorial (as opposed to topological) homotopy theory for each skeleton of those spaces. We further show that there is a Seifert-van Kampen theorem for closure spaces, a well-defined notion of persistent homotopy, and an associated interleaving distance. As an illustration of the difference with the topological setting, we calculate the fundamental group for the circle, 'circular graphs', and the wedge of circles endowed with different closure structures. Finally, we produce a continuous map from the topological circle to 'circular graphs' which, given the appropriate closure structures, induces an isomorphism on the fundamental groups.
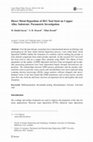
Lasers in Manufacturing and Materials Processing, 2015
Over the past decade, researchers have demonstrated interest in tribology and prototyping by the ... more Over the past decade, researchers have demonstrated interest in tribology and prototyping by the laser aided material deposition process. Laser aided direct metal deposition (DMD) enables the formation of a uniform clad by melting the powder to form desired component from metal powder materials. In this research H13 tool steel has been used to clad on a copper alloy substrate using DMD. The effects of laser parameters on the quality of DMD deposited clad have been investigated and acceptable processing parameters have been determined largely through trial-and-error approaches. The relationships between DMD process parameters and the product characteristics such as porosity, micro-cracks and microhardness have been analysed using scanning electron microscope (SEM), image analysis software (ImageJ) and microhardness tester. It has been found that DMD parameters such as laser power, powder mass flow rate, feed rate and focus size have an important role in clad quality and crack formation.
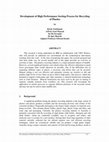
This research is being undertaken by IRIS in collaboration with VISY Plastics, who will provide a... more This research is being undertaken by IRIS in collaboration with VISY Plastics, who will provide an industrial test environment for the technological innovations resulting from this work. At the time of preparing this paper, the research program had only been under way for several months and so this paper provides an overview of activities to date. The plastics recycling industry is a major potential reducer of landfill. However, several significant barriers exist which reduce the effective utilisation to much lower percentages than would otherwise be possible. One of the difficulties lies in separating different types of plastic, a necessary step before they can be recycled. Manual sorting is not cost effective and automatic systems are sensitive to dirt and produce high levels of loss when setup to deliver high purity. One process, which has potential to improve both purity and value retention, is mineral benefaction technology such as froth flotation. Mineral benefaction has been used in the past in mining to separate valuable minerals from worthless ore. This research will investigate the application of similar processes to separate different polymers in the recyclate stream and may one day be used to mine landfill sites.
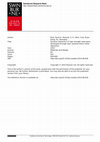
Materials & Design, 2014
High strength steel alloys are good candidates for many engineering applications particularly tho... more High strength steel alloys are good candidates for many engineering applications particularly those involving high strains and impact loads. Such applications in energy absorption devices require materials that can sustain dynamic loading and remain strong under demanding conditions. But the processing cost of these alloys has been a prohibitive factor, thus re-enforcing the research on porous and cellular structures made of stainless steels. Direct metal deposition (DMD) is a process which employs the power of a CO 2 laser to melt and deposit metallic powders onto steel substrates. Such structures offer advantages of creating novel configurations only by computer control of laser "tool path". This research investigates the mechanical behaviour of solid and porous parts with prismatic cavities under quasi-static and dynamic compressive loading. Apart from two main deficiencies of relatively large variations of properties among the test specimen and sufficiently low modulus of elasticity, the stress strain behaviour is very close to the commercial grades of stainless steel produced by rolling and forming. The energy absorption behaviour of porous specimen is also very encouraging and renders DMD as a suitable process for manufacturing of customized sandwich and graded structures that can be used as a substitution for many engineering applications such as monolithic compression plates and explosion shields.
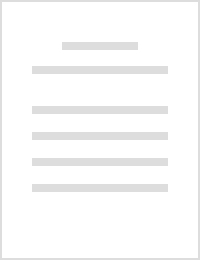
Advanced Materials Research, 2011
This paper presents an investigation on laser direct metal deposition of tool steel on copper all... more This paper presents an investigation on laser direct metal deposition of tool steel on copper alloy substrate both directly and using high nickel stainless steel as buffer layer. The bond strength between the clad and the substrate has been investigated. Tensile testing was employed to measure the bond strength. The characteristics of the fracture surfaces have also been analyzed. Bond strength measurement revealed that the ultimate tensile strength of the substrate material was higher compared to the bond strength between the clad and the substrate. In addition, the experimental result revealed that use of high nickel stainless steel reduced the bond strength with substrate. However, the bond strength measured in this experiment between laser cladded tool steel and copper alloy substrate was much higher compared to the bond strength between these two metals coated using other techniques.
This paper presents an investigation on the microstructure analysis of a bimetallic component con... more This paper presents an investigation on the microstructure analysis of a bimetallic component consisting of the steel powder deposited on the solid copper substrate using laser cladding technology, Direct Metal Deposition (DMD). Study includes the variation of formation of microstructures of copper particles and porosity in the laser cladded structure at various thicknesses. Results obtained from the Scanning Electron Microscope (SEM) and Energy Dispersive Spectroscopy (EDS) display a metallurgically sound and fully dense steel layer, where copper in rounded form was seen in the layer, which decreased with the increase of layer thickness. It is observed that porous holes also reduce with the increase of the thickness.
Advanced Materials Research, 2011
Laser cladding is a thermal process for depositing a metallic alloy on to a parent metal to repai... more Laser cladding is a thermal process for depositing a metallic alloy on to a parent metal to repair corrosion, erosion, wear or other physical damage. The present work studies the effects of the laser cladding process on the integrity of metal substrates and the bond between the cladding layer and the base metal. It also evaluates some physical characteristics of the cladding layer, in this case grade 420 stainless steel. The research compares the work with Tungsten Inert Gas (TIG) welding and concludes that, due to the small size of the heat-affected zone, this laser cladding process does not adversely affect the physical properties of the metallic substrates.
Smart Electronics and MEMS II, 2001
A study of pressure-driven liquid flow in microchannels is presented with the aim of providing a ... more A study of pressure-driven liquid flow in microchannels is presented with the aim of providing a simple model for microfluidics. The paper presents the initial research effort, which covers a survey of CFD packages, the general principles for fluid dynamics, and a simple model of flow in microchannels formulated from these governing equations. The model demonstrates how the capillary force affects the flow and the applicability of boundary layer theory to the flow in a microchannel. The simulation of textures in a microchannel, and difficulties in modelling, are then discussed.
Uploads
Drafts by Prof S.H. Masood
Papers by Prof S.H. Masood