Papers by Jaroslav Kovacik

Engineering Failure Analysis, 2024
Currently, to reduce CO 2 emissions and fuel consumption, the automotive industry seeks to replac... more Currently, to reduce CO 2 emissions and fuel consumption, the automotive industry seeks to replace high-density components with low-density ones. Due to their advantageous properties (high stiffness/strength-to-weight ratio and high energy absorption performances), metallic foams (MFs) are identified as ideal candidates for this purpose. This paper investigates the influence of density (0.3-1.0 g/cm 3) and loading speed (1.74 mm/minstatic to 174000 mm/minimpact) on the mechanical behavior of MFs. Studied MFs have closed-cells and are manufactured from aluminum alloys (AlMg1Si0.5 + 0.4 wt.% Ti) through the powder metallurgy route. For this purpose, rectangular specimens with lateral notches and surface skin were used. A 3-point bending test was used for the static properties, while the instrumented Charpy hammer was adopted for the impact behavior. Following the experimental tests, a macrostructural analysis of the fracture surfaces of the specimens was performed to highlight the influences of the topology on the MF properties. It was found that both foam density and loading speed significantly influence their mechanical behavior. Significant increases in properties were obtained with the increase in foam density and test speed. Equations have been proposed that can predict with highaccuracy the main mechanical properties of MFs. It was observed that the mechanical properties of MFs are closely related to the topology of the fracture surface, as well as to the shape of the foam cells and the skin of the specimens.

Kovové materiály, 2016
Two patented tool materials cermet Ferro-titanit WFN and steel CPM 10V are evaluated from the poi... more Two patented tool materials cermet Ferro-titanit WFN and steel CPM 10V are evaluated from the point of view of their sonotrode properties. The comparison criterion was ultrasonic energy transmission for each tool material. The maximum oscillation amplitude at lowest input power at a constant resonant frequency of 30 kHz and given voltage was measured. Both particulate composite systems are prepared by the methods of powder metallurgy thus having high structural homogeneity. Structural analysis showed that the cermet Ferro-titanit WFN is a particulate composite material having aggregated hard TiC phase within the matrix. On the contrary, steel CPM 10V is a particulate composite material with segregated and homogeneously dispersed hard VC phase within the matrix. The difference in the spatial distribution and aggregation/segregation of hardening phase within the matrix is a key factor that affects their ability to transmit ultrasound energy. K e y w o r d s : ultrasonic, sonotrode materials, tool materials, sonotrode tool materials, powder metallurgy, microstructure, transmission of ultrasound energy

Acta Mechanica, Jul 15, 2015
Copper-graphite composite materials in the range of 0-10 vol% of carbon phase were prepared from ... more Copper-graphite composite materials in the range of 0-10 vol% of carbon phase were prepared from the mixture of copper and graphite powders by hot isostatic pressing. The microstructure, mechanical (tensile strength, elongation to fracture) and physical (electrical and thermal conductivity) properties of composite samples were investigated, and the cross-property connections were calculated. It was shown that electrical and thermal conductivity cross-property (Lorenz number) is almost constant and increases only slightly (no more than 10 % increase was observed). This implies that in the investigated composition range the Lorenz number of a copper-graphite composite system behaves according to Franz-Wiedemann law for pure metals at constant temperature. On the contrary, the conductivity to tensile strength cross-property connections showed significant linear increase (over 200 % in the investigated composition range) for both electrical conductivity and thermal conductivity of composite materials. The cross-property connections of conductivity to the elongation to fracture exhibit a nonlinear dependence on the volume fraction of graphite.
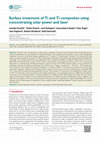
European Mechanical Science
Titanium and its composites are widely used in implants of bones and teeth. Besides mechanical pr... more Titanium and its composites are widely used in implants of bones and teeth. Besides mechanical properties also surface characteristics are very important in these biomaterials. Very important are properties such as surface topography, roughness, chemistry, and surface energy, wettability, and Ti oxides or Ti nitride layers thickness. The concentrated solar power was used successfully to nitride Ti Grade 2 and powder metallurgical Ti prepared from hydrogenated dehydrogenated Ti powder. The nitriding experiments were performed under nitrogen atmosphere at different temperatures and time in SF40 (40kW horizontal solar furnace) at PSA, Spain. Concentrated solar energy has been shown to be an economical alternative to conventional gas nitriding techniques in electric furnaces, CVD, PVD, plasma nitriding, or laser treatments. It has been observed that the solar process represents a significant reduction of the heating time to several minutes (up to 5 minutes at temperature range 500-1000 ...
IOP Conference Series: Materials Science and Engineering, 2020
MATEC Web of Conferences, 2019
Experimental results for solar metallurgy, solar powder metallurgy of titanium, solar surface tre... more Experimental results for solar metallurgy, solar powder metallurgy of titanium, solar surface treatment of titanium and titanium welding are briefly reviewed. Most of them were performed at Plataforma Solar de Almeria Spain using solar furnaces SF5 and SF40 in gas/vacuum furnace. Generally, it was observed that the time to achieve required sample temperature is very short when concentrated solar power used. Thanks to use of renewable solar energy these technologies starts to be attractive for industrial production of titanium in Earth solar belt. It can be expected that the obtained results and approaches are similar also in Space. According to the obtained knowledge, the possible solutions/necessary changes for solar furnaces on Moon, Mars and in main asteroids belt are discussed.

Bioengineering, 2023
In this study, the surface laser treatment of a new type of dental biomaterial, a Ti-graphite com... more In this study, the surface laser treatment of a new type of dental biomaterial, a Ti-graphite composite, prepared by low-temperature powder metallurgy, was investigated. Different levels of output laser power and the scanning speed of the fiber nanosecond laser with a wavelength of 1064 nm and argon as a shielding gas were used in this experiment. The surface integrity of the machined surfaces was evaluated to identify the potential for the dental implant’s early osseointegration process, including surface roughness parameter documentation by contact and non-contact methods, surface morphology assessment by scanning electron microscopy, and surface wettability estimation using the sessile drop technique. The obtained results showed that the surface roughness parameters attributed to high osseointegration relevance (Rsk, Rku, and Rsm) were not significantly influenced by laser power, and on the other hand, the scanning speed seems to have the most prevalent effect on surface roughness when exhibiting statistical differences in all evaluated profile roughness parameters except Rvk. The obtained laser-modified surfaces were hydrophilic, with a contact angle in the range of 62.3° to 83.2°.
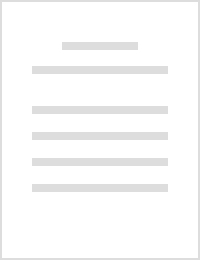
Journal of Composite Materials, Apr 27, 2022
This paper presents the thermal behavior of ZrB2 skeletal material (38% porosity) infiltrated wit... more This paper presents the thermal behavior of ZrB2 skeletal material (38% porosity) infiltrated with pure Cu or CuCrZr alloy. Gas-assisted pressure infiltration technology was used to prepare the composites. Thermal diffusivity, density and specific heat measurements were used to calculate the thermal conductivity—the room temperature values of the Cu-ZrB2 and the CuCrZr-ZrB2 material were 157 W m−1 K−1 and 146 W m−1 K−1, respectively, and they decreased with increasing temperature. Analysis of the results showed significant influence of the interface on the thermal conductivity of the CuCrZr-ZrB2 composite. The results indicate that the improved interfacial conductivity was formed due to the presence of the Zr in both the copper alloy and the ceramic skeleton. During infiltration, Zr atoms diffused from the liquid metal to the interface between the metal and the matrix. Here, they created a layer that had metal-related properties. The layer improved wettability of the interface and at the same time the thermal conductivity of the whole composite. The values were compared with the data of the Cu–graphite composite made by the powder metallurgical route where heat transfer through the interface approaches zero. Obtained experimental data were analyzed using the Differential Effective Media (DEM) technique, showing high thermal conductance of the interface between the CuCrZr metal matrix and ceramic skeleton.
Materials, Mar 13, 2023
This article is an open access article distributed under the terms and conditions of the Creative... more This article is an open access article distributed under the terms and conditions of the Creative Commons Attribution (CC BY
Journal of Materials Science, 2016
Materials Science and Engineering A-structural Materials Properties Microstructure and Processing, 2017
Video Proceedings of Advanced Materials, Nov 1, 2020

Materials Science and Engineering A-structural Materials Properties Microstructure and Processing, Apr 1, 2017
The collapse mechanisms of metal foam matrix composites under static and dynamic loading conditio... more The collapse mechanisms of metal foam matrix composites under static and dynamic loading conditions were experimentally and analytically investigated. Closed-cell aluminium foam AlSi10 with 325 ± 10 kg/m 3 density was used as core material, while stainless-steel-mesh is the faces materials. Prior to characterizing the composite sandwich structure, the stainless steel mesh face material and closed-cell aluminium foam were characterized by tensile testing and compression testing, respectively. Experimental tests were performed on sandwich beams using both High Speed Camera and Digital Image Correlation system for strain distribution. All experimental tests were performed at room temperature with constant crosshead speed of 1.67×10 −4 m/s for static tests and 2 m/s impact loading speed for dynamic tests. Two main deformation behaviours of investigated metal foam matrix composites were observed following post-failure collapse: face failure and core shear. It was showed that the initiation, propagation and interaction of failure modes depend on the type of loading, constituent material properties and geometrical parameters.
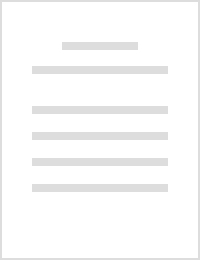
Mathematics and Mechanics of Solids
This paper focuses on the electrical conductivity and thermal expansion coefficient of copper–gra... more This paper focuses on the electrical conductivity and thermal expansion coefficient of copper–graphite composites in the range of 50–90 vol.% graphite. In the previous authors’ work, elastic and conductive properties for the range of 0–50 vol% graphite were studied and cross-property connections were established between (1) electrical and thermal conductivities and thermal expansion coefficient and (2) electrical resistivity and shear modulus. Copper–graphite composites are prepared using hot isostatic pressing from the mixture of copper and graphite powders. The microstructure of the composites consists of copper particles that are homogeneously distributed within the dominant graphite phase (50–90 vol% graphite). The density, electrical conductivity, and thermal expansion coefficients of copper–graphite composites for the range of 0–90 vol% graphite are measured. Cross-property connections between electrical resistivity and thermal expansion coefficients are modeled using various ...

Energies
The liquid metal infiltration of carbon preformed with copper and its alloys is already an establ... more The liquid metal infiltration of carbon preformed with copper and its alloys is already an established and well-known process. It is extensively used by the electronic industry to produce heat sinks of power electronics and electric contacts and sliding electric contacts. The advantage of the process is its ability to produce near net shape components with high volume fractions of carbon at a relatively low price. The process is carried out in a vacuum and with low applied pressure. However, a strong dependence on the temperature of infiltration and its precise control is significant for the sound final product. For certain pair carbon matrix–copper alloys, different results could be obtained according to the infiltration temperature. If the temperature is too low, the solidification may occur prior to complete infiltration (high final porosity). When the temperature is too high, undesirable reactions may occur at the fiber–matrix interface (e.g., corrosive carbides). Therefore, the...
Advances in Manufacturing Engineering and Materials, 2018
Process parameters of abrasive water jet (AWJ) machining of TiB 2 +Ti ceramic matrix composites w... more Process parameters of abrasive water jet (AWJ) machining of TiB 2 +Ti ceramic matrix composites with 10%, 15% and 20% of Ti reinforcement were investigated. The article focuses on microstructure damage processes and kerf geometry in AWJ machining of TiB 2 +Ti composites. Two different abrasive water jet cutting speeds and three sorts of composite materials, together with a reference monolithic one, are considered. Microstructure in machined samples was observed using scanning electron microscope. The characteristics of the cuts such as kerf top width, kerf angle and surface roughness were studied. The influence of cutting speed on abrasive process in composites with various amounts of Ti was investigated. It was found that roughness decreases and kerf taper ratio increases with increase in amount of Ti.

This paper presents the results of the investigation of composite sinters W-TiB2 which were used ... more This paper presents the results of the investigation of composite sinters W-TiB2 which were used as an electrode in the process of electro-spark deposition (ESD) and the examination of the deposited layers. The scope of the study includes detailed characteristics of powder mixtures, composite sinters made using the spark plasma sintering method (SPS) and layers deposited in the electro-spark process. The ESD process, using the W+30 vol.% TiB2 electrode, was carried out using an automated device. The substrates were made of copper and aluminium. The topography analysis of the surfaces of the composite layer and the evaluation of their wear resistance properties are also presented. The analysis of the results of research showed the possibility to obtain, using the SPS method, composite materials of good quality, which can be used as electrodes in the ESD process. The obtained layers had increased wear resistance in relation to the substrate material.
Uploads
Papers by Jaroslav Kovacik