Papers by Mehmet Göl

OTEKON, 2024
This study explores advanced techniques for accurate range prediction in electric vehicles (EVs) ... more This study explores advanced techniques for accurate range prediction in electric vehicles (EVs) by leveraging both internal and external data sources. The paper aims to enhance range prediction accuracy by at least 10% through innovative data-driven estimation methods for State of Charge (SoC) and State of Health (SoH) using AI algorithms. The integration of live environmental data, such as weather conditions, road profiles, and traffic information, ensures a comprehensive approach to range prediction. Secure communication technologies and advanced sensing methods further support these predictions. Key results include the development of a HiL testing and debugging framework for AIsupported energy-efficient vision algorithms for driver assistance and vision-in-the-loop functions, a BMS AI optimization package solution for route planning and driver behavior prediction, and an accurate range prediction algorithm. These innovations are anticipated to lead to significant improvements in EV performance, including a 10% improvement in driving range through dynamic routing and energy-efficient algorithm design, more than a 10% reduction in energy consumption via smart BMS and algorithm design, and ±10% accurate range prediction using novel range estimators that incorporate both in-vehicle and out-vehicle data. These advancements are expected to contribute significantly to sustainable mobility and the reduction of CO2 emissions, addressing key challenges in the adoption and widespread use of electric vehicles.

Real-Time Implementable Intelligent Trajectory Controller Design for a Light Commercial Vehicle, 2022
Light Commercial Vehicles (LCVs) are widely used for last-mile delivery of goods to manufacturers... more Light Commercial Vehicles (LCVs) are widely used for last-mile delivery of goods to manufacturers and consumers due to their ease of manoeuvrability, better mileage, and lower operating costs. They account for over 80% of total commercial vehicle sales in the European Union. Therefore, automation of LCVs has a significant socioeconomic impact. A fuzzy trajectory controller with a minimum number of rules is designed for a hypothetical Level 3 autonomous vehicle (L3AV) and tested in a narrow road scenario. The analysis of the simulations showed that the maximum tracking error in the angular position was 4.1° at 4 m/s, 6.3° at 6 m/s, and 6.7° at 8 m/s, while the maximum lateral error was 0.1 m in all scenarios. The results have shown that the proposed controller achieves acceptable performance at different speeds with a minimum number of rules, leading to real-time implementation.
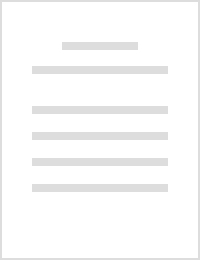
Recent extraordinary technological progress in the field of high-voltage-batteries has led an evo... more Recent extraordinary technological progress in the field of high-voltage-batteries has led an evolution in the automotive industry, resulting in vehicle manufacturers to shift from conventional powertrains towards electric ones. However, electrified road vehicles are amazingly complex. Today, the number of operations for a modern electric vehicle grew from millions to billions per second. This is mainly fueled by the electrification and safety requirements in addition to critical core functionalities. This emphasizes the importance of software development cost, effort, and production planning in the automotive industry. In this paper, in the framework of EU funded H2020 OBELICS project, a detailed-COCOMO approach is proposed for a manually coded safety-critical embedded SW for an electric vehicle not only to plan the project well in advance but also to assess its commercial viability using quantifiable cost metrics to make the process more objective and repeatable. In this context, a case study is given for a battery-management software using an algorithmic model. The case-study has demonstrated not only the planning requirements but also the impact of project type on effort and time estimation in each phase of the software lifecycle. The results have shown that inaccurate software project type estimation can lead an error of up to 16% in effort and 19% in development time according to the phase. It also shows that reliability, database size and complexity are the major contributors of the total time, effort and hence of the cost. The results have also demonstrated the impact of model-based design and automated code generation tools on planning for different phases of the V-cycle briefly.

Automotive manufacturers tried to meet challenges created by clean transport revolution. As more ... more Automotive manufacturers tried to meet challenges created by clean transport revolution. As more emphasis is put on the request for clean transport, as well as passenger cars, demand for electrified medium/heavy duty vehicles that can fully function on the road will increase. However, even though, electric/hybrid electric vehicles (EVs/HEVs) have demonstrated significant fuel consumption and emissions reductions, range and cost effectiveness has still been a barrier faced by many vehicle manufacturers. And this shifts the balance of technologies used in the vehicles even further in the direction of electrically powered auxiliary systems. The focus of this study is on energy consumption of the auxiliary systems. In this study, detailed vehicle simulation MATLAB/SIMULINK is used to investigate how to reduce the auxiliary sub system systems energy consumption. The methods used for reducing energy and fuel consumption are better control of the auxiliary system loading vehicle driveline and selection of more energy efficient components for the auxiliary systems.
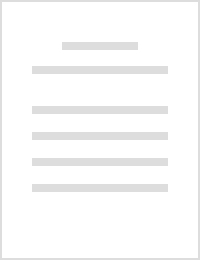
Recent extraordinary technological progress in the field of high-voltage-batteries has led an evo... more Recent extraordinary technological progress in the field of high-voltage-batteries has led an evolution in the automotive industry, resulting in vehicle manufacturers to shift from conventional powertrains towards electric ones. However, electrified road vehicles are amazingly complex. Today, the number of operations for a modern electric vehicle grew from millions to billions per second. This is mainly fueled by the electrification and safety requirements in addition to critical core functionalities. This emphasizes the importance of software development cost, effort, and production planning in the automotive industry. In this paper, in the framework of EU funded H2020 OBELICS project, a detailed-COCOMO approach is proposed for a manually coded safety-critical embedded SW for an electric vehicle not only to plan the project well in advance but also to assess its commercial viability using quantifiable cost metrics to make the process more objective and repeatable. In this context, a case study is given for a battery-management software using an algorithmic model. The case-study has demonstrated not only the planning requirements but also the impact of project type on effort and time estimation in each phase of the software lifecycle. The results have shown that inaccurate software project type estimation can lead an error of up to 16% in effort and 19% in development time according to the phase. It also shows that reliability, database size and complexity are the major contributors of the total time, effort and hence of the cost. The results have also demonstrated the impact of model-based design and automated code generation tools on planning for different phases of the V-cycle briefly.

Lowering emission levels and reducing fuel consumptions, have made the electrically propelled veh... more Lowering emission levels and reducing fuel consumptions, have made the electrically propelled vehicles, a topic of interest. However, the concerns related to the driving range of electric vehicles (EV) still cannot be overcome. Therefore, proper selection of electric powertrain (e-powertrain) becomes vital to accomplish the market needs. There is a broad range of factors related to the e-powertrain such as electrical machine type, powertrain layout, transmission, differential, tires and etc. which influence both the energy consumption and performance of an EV. So as to achieve optimum energy economy and acceleration performance, it is crucial to be able to assess the impact of selected powertrain layout and its components reasonably accurate in prior to the development process. In this study a simulation system with a user friendly graphical user interface (GUI) is developed in MATLAB®/Simulink environment to allow the evaluation of more alternatives at a fraction of the time and cost. Finally, simulation results for an EV with different powertrains for different drive cycles are presented to highlight the consequences and risks of decisions made at earlier stages. ELEKTRİKLİ ARAÇLARDAKİ GÜÇ SİSTEMLERİNİN ENERJİ TÜKETİMİ VE PERFORMANS ÜZERİNDEKİ ETKİLERİNİN DEĞERLENDİRİLMESİ İÇİN EFEKTİF GRAFİKSEL KULLANICI ARAYÜZÜ ÖZET Emisyon seviyelerinin ve yakıt tüketiminin azaltılması ihtiyacı, yakın gelecek için elektrikli araçları odak noktası haline getirmiştir. Ancak elektrikli araçların menzil yetersizliği problemi henüz çözülemeyen bir konu olarak karşımıza çıkmaktadır. Bu neden ile elektrikli araçlardaki güç sistemlerinin doğru seçimi, pazar ihtiyaçlarının karşılanabilmesi adına, hayati bir önem taşımaktadır. Elektrikli araçların enerji tüketimi ve performansı üzerinde, elektrikli güç sistemlerinin tasarımları önemli bir etkiye sahiptir. Bu tasarım yapılırken elektrik makinasının çeşidi, aktarma organlarının yerleşimi, şanzıman, diferansiyel ve tekerleklerin seçimi dikkat edilmesi gereken etkenlere örnek olarak verilebilir. En uygun enerji ekonomisi ve ivmelenme performansını elde etmek için, ön tasarım sürecinde, güç sistemi elemanlarının dizilimine dair seçimin ve kullanılan ekipmanların etkilerini belirleyebilmek çok önemlidir. Bu çalışma kapsamında, kısa zaman ve daha az maliyetle farklı alternatifleri değerlendirmeye izin veren, kullanışlı bir grafiksel kullanıcı arayüzü ve arkasında çalıştırılan sistem modelleri MATLAB®/Simulink ortamında geliştirilmiştir. Çalışmanın son kısmında ise, tasarımın başlangıç aşamasında verilen kararların faydalarını ve risklerini vurgulamak amacıyla, farklı sürüş çevrimlerine tabi tutulan birbirinden farklı elektrikli güç sistemlerinin benzetim sonuçları sunulmuştur. Anahtar kelimeler: Grafiksel kullanıcı arayüzü, elektrikli güç sistemi, enerji tüketimi, performans, elektrikli araç

Efforts for mitigating the CO 2 and local pollution levels resulted in the development of advance... more Efforts for mitigating the CO 2 and local pollution levels resulted in the development of advanced powertrains for passenger vehicles and light duty vehicles. However, world's major cities ambitious emissions targets to reduce carbon dioxide emission levels further, enforces the use of the electrified powertrains in public transport as well. Even though the electrification of these vehicles is seen as a solution, bus manufacturers face off against the range anxiety problem because of the high energy density difference between current batteries and diesel fuel. Therefore, future of the bus manufacturers depends upon the ability to produce low cost, safe, efficient, and clean buses. The challenges that the bus manufacturers faced in prior to the development phase can be resumed as the vehicle designer to make the best possible decision. To be able to do that, researchers and industrial development engineers required to evaluate alternatives and make decisions regarding a wide range of choices by taking into account the returns of investment. Therefore, the focus of this paper is on a set of key parameters such as vehicle weight, rolling resistance and auxiliary load of a Hypotetical electric city bus proposed by Anadolu Isuzu Automotive Industry over various drive cycles which has a greater impact on the range of an electric city bus. The effects were investigated in MATLAB/Simulink environment which helps the decision maker to make effective decisions on a certain design in the shortest possible time. Moreover, it is believed that the information gathered through the analyses will broaden the insight of bus manufacturers and can provide essential information for future electric bus deployment projects.

The main challenge in search of the competitive electric bus development is to make the best poss... more The main challenge in search of the competitive electric bus development is to make the best possible decision among diverse technologies that can overcome the range anxiety within a reasonable cost limit. Therefore electric bus manufacturers have to consider different alternatives. However, to be able to evaluate this wide range of choices, detailed understanding of the impact of diverse technologies on the vehicle energy performance is essential. In this paper different vehicle architectures and different powertrain components for an electric city bus are studied and compared in order to find out the more suitable one in terms of energy efficiency. The model of a 12m long hypothetical electric city bus proposed by Anadolu Isuzu Automotive Industry and Trade Inc. is built in MATLAB ® /Simulink environment with a modular structure to help the decision maker to make effective decisions on the overall energy performance of a certain design in the shortest possible time. Furthermore, analyses were conducted for all alternatives over various drive cycles ranging from standard drive cycles to real-world drive cycle for a fair evaluation. Finally, findings gathered through the analyses are represented in the concluding section of the study.
Teaching Documents by Mehmet Göl
MSP430 and Android Communication
Uploads
Papers by Mehmet Göl
Teaching Documents by Mehmet Göl