Trafilatura

La trafilatura è un processo di formatura che induce un cambiamento nella forma del materiale grezzo di partenza attraverso la deformazione plastica dovuta all'azione di forze impresse da attrezzature e matrici.
La trafilatura dei metalli realizza in continuo lunghi fili, barre con una sezione circolare oppure a profilo complesso con 3 o più lati e tubi (le barre entrano già con la loro forma finale, la trafilatura serve solo ad incrementare le proprietà meccaniche tramite incrudimento superficiale e a migliorare le tolleranze dimensionali). Le sue origini risalgono all'XI secolo e la sua continua evoluzione ha portato ad oltrepassare i limiti dimensionali progressivamente raggiunti.
Sebbene l'applicazione industriale più importante sia nella lavorazione del metallo, trattata in questa voce, il termine viene usato per un fattore di comodità anche per altri materiali tra cui la ceramica e la pasta. Quest'ultima viene prodotta mediante la tecnica di estrusione. La trafilatura viene molto usata anche per la creazione di mattoni[1].
Microtrafilatura
[modifica | modifica wikitesto]La crescita esponenziale del mercato mondiale di micro-componenti richiede fili con un diametro sempre inferiore e con ottime finiture e proprietà da impiegare nella realizzazione di componenti elettronici e meccanici miniaturizzati.
La trafilatura mirata alla produzione di microfili con un diametro di pochi micrometri viene nominata microtrafilatura. Come il diametro dei fili anche i lati delle barre possono essere di pochi micrometri, le quali prendono il nome di microfili a profilo complesso.
Le caratteristiche generali sopra dette rendono la trafilatura una tecnologia in grado di realizzare una produzione di massa di microfili e quindi di soddisfare le nuove esigenze della miniaturizzazione.
Ma il passaggio dal macro- al micro-mondo crea problemi anche alla trafilatura: le nuove dimensioni hanno conseguenze nel comportamento del materiale, nel processo, nelle matrici, nella manipolazione, nelle attrezzature e nei macchinari.
I costi da sostenere per la produzione di microfili aumentano e sono legati all'acquisto di nuovi impianti dedicati, alla ricerca e sviluppo (necessaria per raggiungere l'ulteriore miniaturizzazione e la produzione industriale di massa dei nuovi prodotti), all'esigenza di un filo di partenza di qualità superiore (più puro e con un'accuratezza superficiale e dimensionale migliore) e di personale più qualificato.
Descrizione generale
[modifica | modifica wikitesto]Il processo di trafilatura possiede le seguenti peculiarità generali:
- efficiente (realizza un tasso di produttività elevato);
- accurato (i prodotti finali hanno tolleranze ristrette, ottime finiture superficiali e la sezione desiderata);
- eccellente nelle proprietà meccaniche-elettriche del prodotto finale;
- economico ed ecologico grazie alle matrici e agli utensili multiuso, alla manodopera non necessariamente qualificata ed allo scarto minimo di materiale.
La trafilatura, in base alle classificazioni dei processi di deformazione, appartiene ai:
- processi di formatura massiva, distinti dai processi di formatura di fogli sottili;
- processi a freddo perché usualmente non viene effettuato un pre-riscaldamento del filo o della barra iniziale;
- processi di lavorazione secondaria (come la piegatura) perché trasforma i prodotti di lavorazione primaria (forgiati, laminati, estrusi, trafilati) in prodotti finiti o semi-finiti. Al più i suoi lavorati subiscono dei minimi cambiamenti di forma solitamente attraverso la piegatura (per formare molle, ganci, graffette, ecc.) o altre operazioni di rifinitura (ad esempio per ottenere delle viti o le punte degli ami da pesca)
Paragonata alle altre tecniche di formatura massiva, la trafilatura è simile all'estrusione a differenza che nell'estrusione il pezzo in lavorazione è sottoposto a forze di compressione mentre nella trafilatura a forze di trazione, e che nell'estrusione l'attrito si manifesta nella matrice e nel contenitore della preforma di partenza invece nella trafilatura solo nella matrice; però entrambe sono tecniche di deformazione senza superfici libere.
Prodotti di trafilatura
[modifica | modifica wikitesto]I fili metallici sono ampiamente impiegati nella realizzazione di tessiture e funi strutturali, cavi elettrici e componenti elettronici, attrezzature mediche, strumenti musicali, prodotti orafi, materiale edile, componenti metallici per i più svariati settori (automobili, giocattoli, giardinaggio, ecc.).
Nel macromondo le funi ottenute da più fili intrecciati o attorcigliati sono utilizzate nelle tensostrutture, negli ascensori, nelle reti da pesca, nel sollevamento speciale nei porti e nei cantieri, ecc.
Con i macro fili singoli si realizzano molle e ganci, viti, recinzioni, cesti, armature per cemento, fibre per il calcestruzzo, fili per il taglio del marmo, per gli impianti elettrici, ecc.
Nel micromondo i microfili sono impiegati nel campo dell'elettronica, dei componenti IT (Information Technology), dei micro sistemi elettro-meccanici (MEMS), ma anche in campo medico, automobilistico, delle telecomunicazioni e della radiofonia; vengono utilizzati sotto forma di molle di contatto, spirali, viti, mandrini, punzoni, fili elettrici, schermature, cavi di segnale per allarmi.
I microfili a profilo complesso divengono micro aste, mandrini, viti, punzoni.
I fili metallici sono prevalentemente in rame, in leghe di rame, in acciaio, in leghe di nichel, in alluminio e spesso sono rivestiti.
Il processo di trafilatura
[modifica | modifica wikitesto]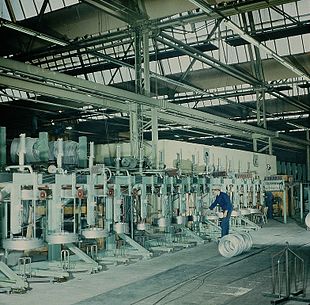
In questo paragrafo vengono descritti i processi di trafilatura e di ricottura con i loro componenti, i difetti e le rotture che possono verificarsi e gli adeguamenti osservati nella produzione di fili capillari dal confronto tra la letteratura esistente sulla trafilatura tradizionale e le realtà visitate di alcune trafilerie di fili sottili e capillari.
Nella lavorazione di trafilatura il filo subisce dei passaggi forzati attraverso delle matrici (filiere) con dei fori di diametro progressivamente decrescente che ne riducono la sezione.
Il volume del filo rimane costante dal momento che la trafilatura è un processo senza asportazione di materiale; con la riduzione diametrale ottengo l'incremento della sua lunghezza.
Il filo da lavorare viene fatto passare attraverso la prima filiera dopo aver subito una riduzione all'estremità da infilare. Tale estremità è resa conica da un'operazione di swagging (formatura a martellamento rotante) oppure, nel caso di microfili, da una rottura a trazione in corrispondenza della zona di strizione. Dopo il passaggio nella prima filiera, segue l'analogo inserimento in tutte le filiere successive.
I fili sono divisi in quattro categorie in base al loro diametro d:
- Vergelle, aventi diametro 5 mm <= d < 8 mm;
- Intermedi, con 1 mm <= d < 5 mm;
- Sottili, con 0.15 mm <= d < 1 mm;
- Capillari, con d < 0.15 mm.
Più in generale i microfili hanno un diametro d di pochi micrometri. I fili più fini realizzati in Europa presentano un diametro di 6 µm, sono in lega d'oro e vengono impiegati in componenti elettronici; nella produzione industriale di massa i fili più sottili sono in rame ed hanno un diametro di 10 µm.
Per una trafilatura ottimale con una buona finitura ed accuratezza dimensionale nei fili, bisogna selezionare accuratamente i parametri di processo, progettare adeguatamente il profilo delle filiere ed il loro angolo, scegliere la riduzione per passo, il lubrificante e i materiali delle matrici e delle attrezzature.
Il rapporto di riduzione ottimale per passo è inferiore a quello ideale ed è compreso tra il 10% e il 45%.
L'angolo e la riduzione per passo ideali si riducono, oltre che per la lavorazione di materiali duri, anche per la produzione di microfili al fine di evitare una cattiva finitura superficiale, maggiori difficoltà di lubrificazione e la possibile rottura. Quindi per ottenere il diametro desiderato si deve incrementare il numero di passaggi progressivi.
Per ridurre una vergella di 8 mm ad un filo di 2 mm di diametro si operano una decina di passaggi attraverso filiere decrescenti. Invece per passare da un filo di 2 mm ad uno sottile di 0,2 mm di diametro sono necessari una ventina di passaggi, da un filo di 1 mm ad uno capillare di 0.1 mm una trentina.
Il filo è trainato da un cabestano finale e da più anelli di tiro posti tra una filiera e l'altra e compie due o tre giri attorno ad ogni anello di tiro in rotazione per diminuire la tensione di trafilatura. Nel tratto che va da una filiera all'altra, il filo è in trazione prima dell'anello e a riposo tra l'anello e la filiera successiva.
Grazie al moto degli anelli di tiro è possibile applicare la tensione back spiegata precedentemente.
Il cabestano finale è collocato dopo l'ultima filiera all'esterno della macchina trafilatrice. Solitamente la velocità del cabestano di tiro è regolata in modo tale da avere uno slittamento sugli anelli di tiro i quali trasmettono la tensione di trafilatura. La velocità del cabestano è al massimo di 30 m/s per i fili sottili e capillari mentre arriva a 50 m/s per i fili con un diametro maggiore.
La temperatura del filo aumenta durante la lavorazione a causa dell'attrito, dello slittamento sugli anelli e dell'elevata velocità a cui viene trafilato.
L'uso di un lubrificante adeguato è indispensabile per ridurre l'attrito, per attenuare il riscaldamento del filo, per diminuire l'usura delle filiere e per evitare l'asportazione di materiale o del rivestimento dal filo.
In seguito ai molteplici passi di trafilatura, il filo incrudito subisce una ricottura per ripristinare le proprietà meccaniche ed elettriche di partenza.
I fili in acciaio per le corde degli strumenti musicali e le molle sono gli unici ad essere sottoposti a trattamenti a caldo prima e dopo la lavorazione.
Dopo la ricottura avviene un raffreddamento in emulsione, seguito da un'asciugatura ad aria che predispone il filo alla bobinatura.
Il bobinatore avvolge un filo o più fili insieme formando le bobine. Un ballerino/sensitivo pneumatico o a peso si muove regolando la velocità di avvolgimento della bobina per mantenere la tensione del filo costante. L'unico parametro monitorato in questa fase è la tensione del filo controllata con un tensimetro. Per calcolare la tensione (N/mm²) di bobinatura da applicare si usa la formula
- T = d² · p/4 · n°fili · k
dove d è il diametro del filo e k è una costante.
Successivamente i fili vengono sbobinati per andare a formare i cavi elettrici, le piattine per il computer, le schermature oppure per ottenere, con un'ulteriore lavorazione, molle e spirali.
Nella creazione dei cavi elettrici i fili vengono attorcigliati mentre, per realizzare delle schermature contro i disturbi elettrici, vengono disposti parallelamente (ad esempio 6-12 fili concentrici attorno a quello da schermare) o anche intrecciati (ad esempio più gruppi di 4 fili paralleli intrecciati attorno ad un cavo). I fili per tali applicazioni vengono avvolti con una bobinatura statica in bobine disposte verticalmente.
Invece le bobine dei fili che in seguito non devono subire delle torsioni sono in posizione orizzontalmente per evitare di torcere i fili una volta arrivati ad una estremità; qui il braccio guidafilo inverte la sua direzione di movimento ed i fili continuano ad avvolgersi senza torsione.
Le bobine di microfilo singolo possono servire a realizzare fili elettrici con schermature, molle ecc. Se il filo non è sub-millimetrico può diventare un monofilo per gli impianti elettrici in Germania e nel Nord Europa, dove i fili elettrici sono rigidi al contrario di quelli flessibili del Sud Europa (ad esempio cavi con 1-7 fili contro i 126 nostri).
Le macchine trafilatrici sono classificate secondo diversi criteri.
Il primo criterio si basa sul diametro finale del filo lavorato: in commercio ci sono “sbozzatori” per fili da 4 mm a 1 mm di diametro a partire da una vergella, macchine “intermedie” per fili da 2 mm a 0.5 mm di diametro con un filo di partenza di circa 4 mm, macchine “per fili sottili” da 0.5 mm a 0.15 mm di diametro con un diametro di partenza di circa 2 mm ed infine macchine “per fili capillari” da 0.15 mm a 0.05 mm di diametro con un diametro di partenza di circa 1.5 mm.
Le dimensioni dell'intero impianto di trafilatura per fili capillari si dimezza rispetto a quelle dell'impianto per fili sottili.
Il secondo criterio è quello del numero di fili lavorati contemporaneamente: se il filo è singolo la macchina è detta monofilo, se i fili sono più di uno è multifilo. Nella tipologia multifilo, grazie a molteplici serie di filiere poste in parallelo e su più piani, è possibile lavorare ad esempio 32 fili contemporaneamente divisi in quattro piani da 8 fili; nella tipologia monofilo troviamo sia macchine con la struttura di quelle multifilo sia macchine con coni di tiro (invece di anelli di tiro cilindrici).
Un metodo diverso di lavorazione multifilo è quello di Brunswick in cui un fascio di fili è introdotto in uno strato di copertura duttile e trafilato insieme con esso: si ottengono diametri fino a 5 µm.
Il terzo criterio è basato sulla tecnica di avanzamento dei fili, che può essere a slittamento sugli anelli o non a slittamento.
Le macchine senza slittamento sono dotate di un cabestano e di anelli motorizzati che ruotano ad una velocità periferica uguale a quella del filo in uscita dalla filiera. La velocità è variabile e regolata attraverso appositi sistemi.
Invece il cabestano delle macchine a slittamento ha velocità periferica superiore di quella lineare del filo in uscita, causando così lo slittamento del filo su di esso e conseguentemente sugli altri anelli di tiro (che ruotano alla stessa velocità del filo in uscita).
Quasi tutte le macchine intermedie in uso sono a slittamento perché riducono le rotture legate all'usura delle filiere.
La riduzione diametrale del filo, che implica un aumento della sua lunghezza, deve essere accompagnato dall'aumento della velocità del filo (che altrimenti non sarebbe più in tensione attorno agli anelli situati tra una filiera e l'altra). Se le riduzioni di sezione fossero calcolate nello stesso rapporto dell'aumento delle velocità periferiche degli anelli di tiro, nel caso in cui avvenisse una minore riduzione del diametro per l'usura di una filiera ed il conseguente minore allungamento del filo, quest'ultimo si romperebbe sotto l'azione della tensione generata dalla velocità costante dell'anello di tiro. Invece nelle macchine a slittamento, l'eventuale usura della filiera dà luogo ad una variazione dello slittamento e non alla rottura del filo. Lo slittamento percentuale dovuto al ritardo del filo è:
- (Vanello – Vfilo) · 100 / Vanello
Lo slittamento deve in ogni caso essere controllato perché se eccessivo provoca vibrazioni del filo ed accavallamenti, un elevato riscaldamento, una rigatura precoce degli anelli di trafilatura e un'eccessiva formazione di polverino.
Spesso, per evitare di raggiungere il limite cinematico, viene imposta una percentuale di riduzione della sezione maggiore sia nelle macchine con slittamento sia in quelle senza: nelle prime si ha una variazione dello slittamento, nelle seconde si verifica l'apertura delle spire per la maggiore lunghezza del filo in uscita dalla filiera rispetto a quella prevista. Questa minore tensione viene compensata nelle filiere successive.
Nelle macchine per fili capillari non è produttivo lavorare con lo slittamento e con una riduzione percentuale maggiore della sezione del filo: si verificherebbero troppe rotture a trazione.
I parametri monitorati nella macchina trafilatrice sono principalmente tre:
- La velocità in uscita dalla trafilatrice (ad esempio di 20 m/s per fili con un diametro di 0.1 mm) e quindi di rotazione del cabestano;
- Il diametro finale;
- Il diametro prefinale corrispondente al penultimo passo.
Durante il processo la temperatura è mantenuta costante a 39 °C - 40 °C grazie a degli scambiatori di calore. Il filo in uscita ha una temperatura di 60 °C - 70 °C dovuta all'attrito nelle filiere ed allo slittamento attorno agli anelli di tiro.
Le trafilatrici multifilo hanno due motori: uno per la trasmissione del moto degli anelli presenti tra una filiera e l'altra, ed un altro per il cabestano di tiro finale e gli assi del forno di ricottura. Quando si avvia o si ferma la trafilatrice, la linea accelera o rallenta progressivamente fino a raggiungere le velocità di regime o a fermarsi perché altrimenti si verificherebbe la rottura del filo. Un apposito dispositivo “anti-ritorno” impedisce agli ingranaggi di invertire il senso di rotazione nel riavvio per effetto della tensione del filo a macchina ferma.
Quando si verifica la necessità di ottenere un diametro maggiore di quello per cui è programmata la macchina, si escludono le filiere nella parte finale (“salto passi”) senza dover spostare le filiere ed infilare nuovamente l'intera trafilatrice. Se la linea trafila fili sottili o intermedi, è possibile escludere le ultime filiere e posizionare quella con il diametro finale desiderato come ultima filiera prima dell'uscita. Invece per i fili capillari, è necessario saltare dei passi e mantenere gli ultimi perché meno rischioso nella messa in moto dell'impianto. Sia nelle zone di salto passi per fili sottili sia in quelle per fili capillari, vengono posizionate delle filiere in ottone con l'inserto in ceramica ed un foro maggiore del diametro del filo a quel punto della lavorazione per guidare e controllare le oscillazioni dei fili.
Il tempo occorrente per escludere le filiere nella parte finale della trafilatrice è circa il 25% del tempo impiegato ad infilare tutta la linea. Grazie al sincronismo tra i due motori, è sufficiente selezionare i passi da saltare e la macchina aumenta automaticamente la velocità degli anelli, lasciando fissa quella del cabestano; il disinnesto degli assi interni avviene attraverso un azionamento elettro-pneumatico automatico.
Qualora avvenga una rottura del filo durante il funzionamento, un'estremità tocca la macchina che si blocca e scarica a terra; se la rottura avviene dopo le ultime filiere, due sonde elettriche posizionate nella zona del cabestano provocano l'arresto immediato della macchina.
Un'alternativa agli anelli di tiro cilindrici, sono i coni di trafilatura monofilo, citati prima. Invece di disporre gli anelli e le filiere in successione, gli anelli di tiro con diametri diversi in funzione delle riduzioni necessarie sono riuniti su uno stesso albero. Si ottiene un albero che porta numerosi anelli accostati tra loro in modo da formare un cono di trafilatura a gradini.
Dal momento che la velocità angolare del cono di trafilatura è costante, gli anelli con diametro minore avranno una velocità periferica inferiore e quindi su di essi si dovranno avvolgere i fili di diametro maggiore. Al crescere del diametro degli anelli e quindi della loro velocità periferica, il diametro dei fili diminuisce.
La macchina è costruita in modo da avere due coni adiacenti, con le filiere poste tra loro: il filo che attraversa le filiere tra un cono e l'altro si avvolge su anelli con diametro progressivamente maggiore per aumentare la sua velocità di trafilatura e subisce una lavorazione sia nel tratto di andata sia in quello di ritorno. Lavorando in queste condizioni, il filo non si dispone mai perpendicolarmente agli assi di rotazione degli anelli ed è sottoposto ad un ulteriore slittamento (laterale) non trascurabile.
Alcuni costruttori, allo scopo di diminuire le conseguenti sollecitazioni irregolari sul trafilato, hanno realizzato degli anelli leggermente conici che permettono al filo di spostarsi più facilmente e di uscire dagli anelli già angolato secondo la nuova posizione da assumere.
Un altro accorgimento può essere quello di dotare i portafiliere di un moto alternato parallelo agli assi degli anelli: in questo modo la posizione di uscita del filo cambia continuamente, l'usura dei coni diviene più uniforme e la loro durata nel tempo aumenta.
La riduzione per passo percentuale da una filiera all'altra è costante nelle macchine con anelli di tiro cilindrici e non lo è nelle macchine che lavorano con i coni di tiro. Nella prima tipologia ogni anello ha una velocità maggiore del precedente della stessa percentuale, a discapito della flessibilità ma con il vantaggio della costanza: se una filiera usurata riduce meno il diametro del filo o se un anello gira ad una velocità non appropriata, il difetto si compensa da una filiera all'altra attraverso lo slittamento o la riduzione maggiore della sezione del filo.
Nella seconda tipologia l'allungamento non è costante, ma lo sono la velocità di rotazione dei coni e la riduzione dei diametri degli anelli consecutivi, in relazione alla riduzione per passo.
Le filiere
[modifica | modifica wikitesto]Le filiere di trafilatura sono composte di tre parti:
- un inserto molto resistente che costituisce l'utensile vero e proprio. I materiali usati sono acciai alto legati, carburi sinterizzati oppure, per velocità più elevate, leghe dure o diamante naturale monocristallo o sintetico (policristallino PCD o monocristallo), anche se il diamante sintetico monocristallo non viene quasi mai impiegato.
Per trafilare fili capillari si preferisce il diamante naturale, per lavorare fili sottili il diamante sintetico policristallino (PCD con grani di pochi µm ottimali per una buona finitura superficiale) e per fili di diametro maggiore metallo duro. L'inserto di diamante sintetico policristallino consiste in un film sottile di cristalli di diamante, fissato su un substrato di carburo di tungsteno sinterizzato. Questa struttura è ottenuta mediante un processo di sintesi del diamante ad alta pressione ed alta temperatura (HPHT) che crea un diamante PCD noto per le ottime proprietà fisiche. L'inserto presenta una resistenza all'usura e all'urto più elevate rispetto al diamante naturale e l'usura della zona di contatto con il filo più uniforme. - un supporto di rinforzo per sostenere l'inserto ossia un anello di carburo di tungsteno;
- un telaio cilindrico in acciaio, che contiene le altre due parti. La sua altezza è in funzione della dimensione dell'inserto e il suo diametro in funzione del portafiliere dell'impianto di trafilatura (standardizzato per consentire l'intercambiabilità delle filiere nei vari impianti). Il telaio permette di supportare lo sforzo assiale che subisce l'inserto durante la trafilatura, di dissipare il calore che si genera per attrito durante il passaggio del filo e di prolungare il cono di entrata dell'inserto per favorire l'ingresso del lubrificante nel foro. Da un punto di vista più pratico, permette di manipolare e posizionare senza difficoltà la matrice e di imprimere su di essa codici e nomi per le specifiche di riconoscimento.
Analizzando l'aspetto del foro interno di una filiera secondo il verso di trafilatura, si osserva un cono di entrata, un cono di riduzione, un tratto parallelo, uno di rilascio ed infine un cono di uscita. Le dimensioni scelte per ciascuna di queste parti che formano il profilo interno della filiera sono in funzione delle proprietà fisiche del metallo da trafilare e contribuiscono ad ottenere migliori prestazioni e una elevata qualità. Il rispetto di queste dimensioni è fondamentale, soprattutto nelle macchine multifilo, per avere una costanza nella riduzione diametrale e nella tensione del filo.
Ogni zona interna ha le proprie caratteristiche:
- La zona di entrata conica consente l'entrata del lubrificante nella zona di trafilatura; l'angolo del cono è di 70º ± 20º.
- La zona di riduzione conica, in cui avviene la riduzione plastica del filo, ha un'altezza minima determinata in modo che il diametro della base maggiore sia almeno uguale al diametro del filo all'entrata nella filiera. L'angolo è in funzione della riduzione da operare e varia di ± 2º. Si impiegano angoli minori (circa 14º) per metalli duri e meno duttili (come il ferro, l'acciaio, le leghe di alluminio) e angoli più aperti (16º - 18º) per metalli teneri come il rame.
- La zona di calibratura è il tratto che calibra il diametro finale. La lunghezza di questo tratto cilindrico è in funzione del diametro di uscita; solitamente è circa il 20%-50% del diametro per metalli teneri ed il 40%-80% per quelli più duri. La calibratura è un'operazione eseguita da una calibratrice a filo allo scopo di ottenere il diametro del foro voluto [la calibratrice a filo, utilizzata per la lavorazione della zona cilindrica di calibratura della filiera e per raccordare tale zona con quella di uscita, si basa sul movimento assiale di un tratto di filo di acciaio inossidabile (per filiere con un diametro finale inferiore a 1 mm) oppure di una barretta di acciaio ramato (per diametri superiori), inseriti nel foro della filiera insieme alla polvere abrasiva. Al movimento assiale del filo si combina la rotazione della filiera e l'inclinamento di questa in modo da arrotondare l'angolo di uscita ed evitare spigoli vivi. Con quest'ultima operazione si ottiene la zona di back relief]
- La zona di rilascio (back relief) è un piccolo arrotondamento che rende il raccordo tra la zona di calibratura e di uscita più dolce; evita graffiature e il grippaggio del filo in uscita dalla filiera. La sua lunghezza è pari al 10% del diametro del filo.
- La zona di uscita non influisce sul diametro finale del filo ma rende possibile l'arrotondamento dello spigolo di uscita. Il contatto del filo con lo spigolo causa delle vibrazioni che si propagano nella macchina e che portano ad un'ulteriore usura della filiera, ad una qualità inferiore del filo e addirittura alla rottura del trafilato. Per tale motivo e per impedire la produzione di scagliature che rischierebbero di accumularsi all'entrata della filiera successiva o di inquinare il lubrificante, lo spigolo viene arrotondato e prende il nome di zona di rilascio. L'angolo della zona di uscita, in generale, è di 40º ± 10º.
Attraverso il foro della filiera viene fatto passare il filo da lavorare, il quale si deforma plasticamente sotto l'azione di una forza di trazione e una di compressione: la forza di trazione è dovuta alla tensione di tiro applicata, la forza di compressione è conseguenza della geometria delle zone di riduzione e di calibratura del profilo.
L'inserto della filiera può lavorare solo in compressione perché in trazione si romperebbe.
Con la miniaturizzazione l'angolo e la riduzione per passo sono minori e quindi anche la lunghezza della zona di riduzione; diviene necessario considerare l'attrito pure nella zona di calibratura, la quale incide maggiormente rispetto a quella di riduzione sull'estensione dell'area di contatto tra il filo e la matrice.
L'usura delle filiere
[modifica | modifica wikitesto]Nonostante la durezza elevata dei materiali impiegati nelle filiere, anche questi utensili sono soggetti ad usura.
L'usura è conseguenza delle vibrazioni e della presenza di scaglie abrasive sulla superficie del filo. L'abrasione comincia nella zona di riduzione a causa della pressione maggiore e successivamente si porta nella zona di calibratura del filo; quando l'area si espande, è necessario togliere la filiera dalla trafilatrice per ricondizionarla attraverso un processo di lucidatura che non aumenta la dimensione del diametro del foro della filiera.
La lucidatura, come la calibratura e la rettifica, è ottenuta con l'inserimento di una polvere di diamante di adeguata granulometria mescolata ad olio e acqua.
Se in presenza di un leggero anello di usura non viene eseguita tempestivamente la sostituzione delle filiere, si innesca una rapida usura che si manifesta con la comparsa di una zona di abrasione più profonda che va ad estendersi a tutto il resto del profilo causando rigature, diametri maggiori o, nella peggiore delle ipotesi, incrinature o rotture dell'inserto.
Nel caso di forti usure è necessaria una rettifica con l'utilizzo di utensili abrasivi di diamante a grana più grossa di quelli usati per la lucidatura. Questa operazione deve essere fatta prima che la matrice cominci a lavorare per trazione perché non sopporterebbe la forza di Trafilatura. In presenza di una forte usura non è più possibile ricondizionare il profilo della filiera senza aumentare la dimensione del foro. Attraverso la rettifica viene tolto uno strato di matrice per ottenere la stessa angolazione e utilizzarla ancora per diametri maggiori.
La rettifica è un'operazione effettuata con una macchina ad ultrasuoni. La macchina ad ultrasuoni consiste in un trasduttore efficiente con una sonda adatta che conferisce le vibrazioni meccaniche ad un ago d'acciaio armonico temprato. Questo ago, con una punta a forma conica, viene introdotto nel profilo della filiera insieme con una polvere di diamante abrasiva con aggiunta di acqua e olio. A seconda del ricondizionamento da eseguire, della dimensione e dei tipi di matrice, vengono usate polveri di diamante di diversa struttura granulare con grani da 0,25 µm a 200 µm (minori nella lucidatura e maggiori nella rettifica). La rettifica è seguita da un'operazione di lucidatura perché è noto che, per un rendimento ottimale, la filiera deve avere un profilo lucido, ben raccordato e privo di spigoli.
Rapportando l'usura al materiale dell'inserto, si osserva che nel diamante sintetico policristallino l'usura della filiera avviene in modo uniforme mentre nel diamante naturale ciò non avviene.
Il diamante naturale, infatti, presenta una struttura con piani teneri e piani duri che offrono una diversa resistenza all'abrasione; ne consegue che l'usura è maggiore nei punti della superficie in cui la resistenza all'abrasione è minore.
L'usura è rilevabile mediante un'osservazione al microscopio oppure grazie ad una misurazione del diametro del filo trafilato con un calibro laser o con un micrometro meccanico munito di comparatore.
Le filiere si mantengono inalterate per mesi e vengono cambiate quando si rischia di ottenere fili con una tolleranza maggiore di quella consentita dalle norme in vigore. La loro vita utile è determinata su una media di tonnellate di filo trafilato. Il tempo di fermo necessario per cambiare metà delle filiere di una macchina multifilo a trenta passi e infilarle nuovamente è di circa 10 ore.
Gli anelli di tiro
[modifica | modifica wikitesto]Nelle trafilatrici multifilo gli anelli di tiro sono generalmente lunghi anelli cilindrici con “n” fasce ricavate sulla superficie esterna.
L'anello è di acciaio e sulle fasce è presente una lega di carburo di tungsteno sinterizzato dello spessore di pochi decimi di millimetro compenetrato perfettamente nel supporto di acciaio in modo da formare con esso un corpo unico. Il carburo di tungsteno offre risultati eccellenti contro l'usura e l'abrasione nelle più svariate condizioni di trafilatura. Invece sugli anelli di tiro per i fili sottili e capillari vengono predisposti riporti ceramici per avere un'aderenza maggiore tra il filo e l'anello ed una minore forza di trafilatura. Le fasce di lavoro, ricavate sull'anello, hanno una conicità di 1º-5º per consentire al filo di scorrere meglio durante la trafilatura. Quando la macchina lavora a regime, le spire si spostano verso il punto in cui la fascia ha diametro maggiore, secondo il grado di lubrificazione: se questa è troppo elevata le spire si posizionano dove il diametro è minore, se troppo bassa traslano dove il diametro è maggiore.
I cabestani finali hanno la stessa struttura e composizione degli anelli di tiro. Nelle macchine intermedie e per fili sottili vi è un solo cabestano, mentre in quelle per fili capillari i cabestani sono due. Impiegando due cabestani si può ridurne le dimensioni e quindi il momento d'inerzia, si può avvicinarli alle ultime filiere ed evitare ai fili percorsi lunghi senza lubrificazione (come avviene tra l'uscita delle ultime filiere ed il cabestano singolo di diametro maggiore nonché più lontano). A volte nella parte inferiore del cabestano è installata una serie di carrucole di rinvio per favorire il distacco delle spire, poiché i cabestani non sono lubrificati.
Gli intagli che si verificano sulla superficie delle fasce di lavoro sono conseguenza dell'attrito continuo e dell'elevata temperatura del filo (anche se attenuati dal lubrificante), dell'elevata velocità di trafilatura e della tensione che stringe le molteplici spire di filo attorno all'anello. Nella trafilatura di fili capillari, attorno ai primi anelli della trafilatrice, viene fatto un giro in più di filo rispetto agli ultimi: il filo diventa più fragile man mano che si assottiglia e solo un giro o due usurano meno la ceramica degli anelli. Nelle macchine di trafilatura a slittamento e con una riduzione percentuale maggiore della sezione del filo, il continuo scivolamento in senso assiale tra il filo e gli anelli di tiro e tra il filo ed il cabestano provoca delle rigature precoci. Per limitare tale usura viene innescato sul cabestano un movimento trasversale attraverso un apparecchio meccanico azionato dalle oscillazioni della macchina. Invece sugli anelli di rinvio verso il forno di ricottura, lo scivolamento trasversale è dovuto sia ad un congegno elettro-meccanico che muove gli anelli sia ad un pettine che movimenta i fili trasversalmente e assialmente. Il pettine ha anche la funzione di mantenere i fili separati tra loro.
Gli anelli di rinvio al forno di ricottura e quelli di ricottura sono in acciaio e non hanno fasce ricavate sulla superficie esterna; alcuni sono ricoperti da uno strato di ceramica. Quando si presentano rigature sulla superficie vengono sottoposti ad una lucidatura o ad una rettifica (se le rigature sono incisioni troppo profonde). Come gli anelli di tiro ed i cabestani, hanno uno spessore dimensionato in modo tale da impedire ovalizzazioni o deformazioni.
I lubrificanti
[modifica | modifica wikitesto]La lubrificazione è indispensabile nella trafilatura: durante la lavorazione la superficie del filo è ricoperta da un lubrificante, scelto a seconda delle caratteristiche di resistenza ed attrito dei materiali a contatto. Un comune lubrificante è il sapone ed un altro molto usato è l'emulsione: olio emulsionato con una percentuale dell'1-2% di acqua che passa al 5% nella lavorazione di fili capillari perché una eccessiva lubrificazione porterebbe le spire di filo a slittare sugli anelli e di conseguenza a rovinarne la ceramica o a rompersi (il filo che entra nelle filiere è minore, ma il cabestano ruota ad una velocità costante e richiede la stessa lunghezza di filo da mandare al forno di ricottura).
Il lubrificante arriva a contatto delle spire dei fili capillari e sottili per caduta dai numerosi ugelli di un condotto situato sopra ad ogni serie di anelli. Ulteriori ugelli sono posti prima di ogni filiera e, spruzzandovi contro, permettono al lubrificante di accompagnare il filo nella matrice (facilitato dalla zona di entrata del profilo). Nelle trafilatrici per fili sottili l'emulsione spesso non viene iniettata per caduta ma attraverso due tipi di ugelli: il primo tipo posto come nelle macchine per fili capillari prima della filiera e l'altro dopo la filiera diretto verso l'anello di tiro successivo.
Le ultime filiere prima del cabestano sono le meno lubrificate dato che sono posizionate sulla parete che divide l'impianto di trafilatura dal forno di ricottura e quindi sono bagnate solo da un lato. Il maggior numero di rotture avviene in queste ultime filiere a causa dell'attrito eccessivo, dell'accumulo di polverino in uscita e quindi del danneggiamento dell'inserto della filiera o della superficie del filo (nei fili sottili e capillari il rapporto tra la superficie ed il volume è molto elevato quindi avviene la rottura).
Il lubrificante può anche essere solido per fili ad alta resistenza (in acciaio, in acciaio inossidabile, in lega alto legata): viene fatto aderire sotto forma di un rivestimento di metallo più tenero, ad esempio di rame o di stagno, depositato chimicamente sulla superficie. Per la trafilatura del titanio vengono utilizzati dei polimeri come lubrificanti solidi
Nelle macchine con coni di trafilatura monofilo, i coni e le filiere sono completamente immersi nel lubrificante liquido che può essere olio o emulsione (contenente additivi grassi o clorurati oppure altri composti chimici).
Non ci sono macchine trafilatrici che lavorano a secco: l'attrito eccessivo porterebbe al surriscaldamento del filo, ad un'usura precoce delle filiere e della superficie del filo e per di più ad un'alterazione delle proprietà del trafilato che, se in rame, verrebbe quasi ricotto e ossidato. Con una lavorazione a secco si arriverebbe alla rottura del filo in brevissimo tempo.
Per concludere i lubrificanti sono tenuti a svolgere le seguenti funzioni:
- lubrificare,
- raffreddare,
- detergere,
- proteggere il filo di rame e la macchina dall'ossidazione.
e devono:
- possedere una stabilità chimico e fisica,
- non produrre schiuma,
- non essere nocivi nei confronti dell'operatore.
In particolare, l'emulsione utilizzata nel forno di ricottura deve garantire una efficace protezione del filo dall'ossidazione in quanto è l'ultimo bagno a contatto del filo prima della bobinatura.
I fattori che possono creare difficoltà all'emulsione nel corretto svolgimento dell'azione lubrificante possono essere:
- una temperatura inferiore o superiore a quella di utilizzo ideale (30 °C - 40 °C) dell'emulsione;
- un attacco batterico che può causare la separazione dell'olio dall'acqua e la conseguente diminuzione dell'effetto lubrificante oltre che la perdita della proprietà antiossidante e la diminuzione del valore del pH accompagnato da uno sgradevole odore;
- i sali minerali nell'acqua;
- la schiuma dovuta alle bolle d'aria che penetrano all'interno dell'emulsione durante l'agitazione creata dagli anelli in rotazione.
Il continuo miglioramento dei lubrificanti ha come obiettivi:
- Il prolungamento della vita delle filiere;
- La riduzione delle rotture;
- La pulizia della macchina;
- Una superficie del filo migliorata;
- L'allungamento del tempo utile dell'emulsione.
L'impianto di ricottura
[modifica | modifica wikitesto]L'impianto di ricottura continua è indispensabile per la purificazione, la ricottura ed il raffreddamento dei fili trafilati. Nella lavorazione la tensione iniziale del filo deve superare il carico di snervamento per determinare la deformazione e la tensione finale del filo deve essere inferiore al carico di snervamento che porterebbe a rottura. Questa situazione si verifica solo se il filo incrudisce durante la trafilatura.
I fili presentano una struttura cristallina modificata in seguito alla trafilatura: i grani, durante la lavorazione, ruotano in maniera da allungarsi determinando delle orientazioni preferenziali (texture) che causano il comportamento anisotropo del metallo di cui sono costituiti. Si ha una conseguente alterazione delle proprietà fisiche del metallo: una riduzione della duttilità, della conduttività, della resistenza alla corrosione, della deformazione a rottura ed un incremento del carico di rottura.
Il filo incrudito non è utilizzabile senza un'opportuna ricottura di ricristallizzazione (ad esempio il rame non sarebbe sufficientemente flessibile per i cavi elettrici e per di più presenterebbe una conducibilità limitata).
La ricottura di ricristallizzazione è un trattamento termico utilizzato per eliminare l'incrudimento e le tensioni residue e per dare la possibilità di effettuare una successiva lavorazione a freddo.
La ricottura è costituita da tre stadi:
- Recovery o “ricottura di distensione” in cui le dislocazioni si muovono e vanno a formare i bordi di una struttura di sottograni poligonalizzati. Si verifica la riduzione delle tensioni residue ed il ripristino della conduttività elettrica;
- Ricristallizzazione in cui nucleano nuovi grani ai bordi delle celle della struttura poligonalizzati con un minor numero di dislocazioni, producendo una fine struttura ricristallizzata. Si ha un minore carico di rottura ma una duttilità migliorata. Questa seconda fase avviene ad una temperatura uguale al 40% della temperatura assoluta di fusione del metallo e si riduce tanto più, quanto più è deformato il metallo. La temperatura di ricristallizzazione del rame è compresa tra i 200 °C e i 250 °C;
- Ingrossamento del grano, meno rapido delle prime due fasi, porta dalla nuova struttura instabile a grani più grandi.
I fili trafilati entrano nel forno di ricottura, una struttura monoblocco in lamiera d'acciaio, e dopo il passaggio sul cabestano vengono rinviati in una cassa situata tra gli anelli. Tale cassa ha le pareti laterali apribili ed è bagnata nella parte inferiore dall'emulsione di ricottura; una parete viene lasciata aperta quando il filo è rivestito perché nella lavorazione si creano più residui di materiale, che possono accumularsi e divenire potenziali inclusioni. Le emulsioni di ricottura contengono degli antiossidanti oppure è possibile aggiungervi dei prodotti antiossidanti specifici.
L'interno della cassa è mantenuta in atmosfera modificata da un'altissima percentuale di azoto che evita il contatto dei fili con l'acqua e quindi l'ossidazione.
Il percorso di ricottura dei fili è il seguente:
- Dall'anello di rinvio al primo anello di ricottura avviene un preriscaldamento iniziale (tra 160 °C e 280 °C).
- Dal primo al secondo anello di ricottura si effettua la ricottura per effetto Joule (nel tratto dal primo anello al livello dell'emulsione refrigerante) cioè dovuta al passaggio di corrente secondo la legge P=VI² ed al conseguente riscaldamento del filo per conduzione, e l'inizio del raffreddamento nell'emulsione. L'emulsione, necessaria per raffreddare e pulire il filo, è regolata ad una altezza non casuale perché determina la lunghezza del tratto di ricottura del filo e quindi il tempo di ricottura.
- Infine dal secondo al terzo anello avviene la seconda parte del raffreddamento nell'emulsione e l'asciugatura ad aria compressa.
Nel forno di ricottura solo il secondo anello è bagnato dall'emulsione di ricottura, invece gli anelli di rinvio e l'altro anello di ricottura non sono lubrificati. Per tale motivo subiscono periodicamente una lucidatura o una rettifica.
I due parametri monitorati nella fase di ricottura sono la corrente I e la tensione V. La tensione di ricottura si calcola con la seguente formula
dove v è la velocità del cabestano in m/s e k è una costante del forno.
Nei fili sottili e capillari i valori della corrente ed il tempo di ricottura sono molto ridotti a causa della sezione minima da sottoporre a ricottura.
La temperatura di ricottura del rame è tra i 500 °C e i 550 °C mentre l'emulsione viene mantenuta a 37-40 °C. È necessario controllare attentamente la temperatura del filo di rame all'uscita del forno di ricottura in quanto, se elevata (> 50 °C), si ha a contatto dell'aria la formazione di ossidi.
Le rotture nel processo di trafilatura possono essere dovute a difetti nel materiale o a difetti nella trafilatura.
I difetti del materiale possono essere:
- Inclusioni di due tipi:
- introdotte dal processo di colata (inclusioni di ossigeno che causano cavità o cricche o fessure, porosità gassose);
- metalliche introdotte durante il trasporto, la manipolazione, la trafilatura.
La rottura del filo avviene quando l'inclusione occupa il 40-50% della sezione. Si verificano differenti profili di rotture a seconda che l'inclusione sia trattenuta o non trattenuta, solitamente in rapporto 1 a 3. È importante individuare la provenienza dell'inclusione: se introdotta durante la Trafilatura è bene controllare tutte le filiere, gli anelli ed i cabestani, se già presente prima della Trafilatura è fondamentale non destinare i fili in cui si trovano alla realizzazione di fili sottili o capillari. Nei fili capillari il 96% delle rotture avviene a causa di inclusioni. Per facilitare l'individuazione della natura dell'inclusione, è opportuno stilare una lista dei materiali con cui viene a contatto il filo durante la Trafilatura ed il trasporto.
- Difetti di saldatura, eseguita per creare continuità tra i fili provenienti da bobine diverse, portano a rotture a bocca di pesce.
I difetti conseguenti alla trafilatura, simili a quelli nell'estrusione, sono:
- Difetti superficiali come rigature longitudinali o pieghe nel materiale che possono aprirsi durante un'ulteriore lavorazione a freddo; possono essere conseguenza di un'impropria selezione dei parametri di processo (ad esempio della velocità del cabestano e della temperatura) o del lubrificante. Invece le rigature dovute al contatto occasionale con materiali più duri si possono definire dei danneggiamenti meccanici.
- Tensioni residue dovute alla deformazione plastica non omogenea. Nel caso di una riduzione veramente leggera, la deformazione tende a limitarsi sulle zone esterne. In questo caso le tensioni residue superficiali sono compressive e si ha un miglioramento del limite di fatica. Le tensioni residue possono influire sulla formazione di cricche nel tempo dovute alla tensione o alla corrosione oppure possono portare all'incurvatura del filo dopo la rimozione di uno strato superficiale di materiale (in ulteriori lavorazioni o in seguito ad una rettifica).
- Chevron cracking, cricche interne influenzate dall'angolo di riduzione della matrice, dalla riduzione per passo, dall'attrito e dalla presenza di inclusioni nel materiale. Le cricche al centro, ulteriormente allungate e sottoposte alla tensione di trafilatura, portano a rotture a coppa e cono.
Le rotture a trazione nella trafilatura possono essere identificate dalla forma conica identica delle due estremità e sono conseguenza di:
- Errata geometria o posizione delle filiere;
- Usura delle filiere;
- Insufficiente lubrificazione;
- Accumulo di polverino, impurità o corpi estranei all'ingresso della filiera che possono causare rigature o divenire delle inclusioni;
- Accavallamento e sovrapposizione delle spire del filo che possono essere evitati con un basso numero di spire ed una adeguata tensione back, che mantenga le spire in trazione attorno all'anello e che non permetta l'allentamento;
La rottura nel forno, dove il filo viene ricotto in atmosfera controllata, avviene a causa della formazione di zone fuse che operano come inclusioni o difetti superficiali nel filo. La formazione di zone fuse può avvenire anche a causa della presenza di vere inclusioni che riducono la sezione di passaggio della corrente causandone un surriscaldamento. È necessario controllare periodicamente il corretto stato del forno e degli anelli di ricottura.
Nei fili utilizzati rispettivamente per la realizzazione di fili sottili e capillari è essenziale l'assenza di inclusioni di ossigeno (che causano cavità, cricche o fessure), porosità gassose, inclusioni metalliche, impurità superficiali. Il prodotto finale deve presentare particolari caratteristiche dimensionali (diametro nominale ed effettivo, tolleranza, ovalizzazione), meccaniche (allungamento percentuale a rottura, carico di rottura) ed elettriche (resistenza elettrica).
Note
[modifica | modifica wikitesto]- ^ Giampietro Paci, Riccardo Paci, Progettare e fare multimediale, Tecnologia, Zanichelli 2011
Altri progetti
[modifica | modifica wikitesto]Wikimedia Commons contiene immagini o altri file su trafilatura
Collegamenti esterni
[modifica | modifica wikitesto]- (EN) wire drawing, su Enciclopedia Britannica, Encyclopædia Britannica, Inc.
Controllo di autorità | Thesaurus BNCF 23639 · LCCN (EN) sh85147078 · GND (DE) 4012892-1 · BNF (FR) cb12036442j (data) · J9U (EN, HE) 987007558576305171 |
---|