Papers by Canan G Guleryuz Parasız
Advanced Composite Materials, Feb 9, 2023
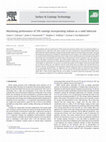
Surface & Coatings Technology, Aug 1, 2009
The machining and wear performance of TiN-coated and patterned carbide inserts incorporating indi... more The machining and wear performance of TiN-coated and patterned carbide inserts incorporating indium as a solid lubricant are reported in this study. Cutting tests were conducted by turning hardened 4340 steel in both lubricated and dry conditions. During turning, periodic flank wear measurements were made. The chips formed during cutting were examined by scanning electron microscopy, as the condition of the chip reflects the conditions obtained during machining. Inserts subject to dry machining were also examined using optical microscopy and X-ray photoelectron spectroscopy to determine the extent of damage on the rake surface as well as the degree of material transfer. The results showed indium to be effective in reducing flank wear during lubricated machining, but little additional benefit of patterning was observed. For dry machining, some degree of improvement was noted in the patterned sample, but the degree of lubricity brought about by the indium coating was not sufficient and the overall flank wear was higher than the lubricated tests. However, the wear and damage on the rake surface along the path of the chip was reduced by the presence of the In-containing microreservoirs. An additional test was conducted using an instrument that simulates temperature effects during machining, and it was found that the lubricity achieved by In coatings is lost above 450°C. These results suggest that the use of indium is limited to below this temperature, and above this temperature transforms to a less lubricious indium oxide.
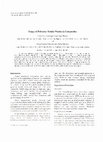
Journal of Scientific & Industrial Research, May 1, 2003
A composi te mat erial is prod uced by using pol yester textil e wastes as reiriforcement materia... more A composi te mat erial is prod uced by using pol yester textil e wastes as reiriforcement material and mainly urea formald ehyde as mat ri x material. This co mp osite is used in banks , tables, shelves , and pots. The bendin g st ren gth and absorption properti es of the tex til e rcinforced composite arc in ves tigated and ~.ompared with fibreboard and med ium density fibreboard whi ch are alternative materi als for the same end-uses' .. The polyes ter was tes such as, yarns, wove n, and knitted fa brics cut at random dimen sions are used as reinfo rcement mat erial. Matrix material is prepared by mixing urea formaldehyd e res in , ammoni um sulphate, and nour in a weight ra ti o of 100:5: 10 co nsecutively. The bendi ng strength of th e textil e rein forced composite is less than the fibreboard and the medium density 1ibreboard , but it ab so rbs less wate r. It seems that th e properti es of th e tex tile reinforced composite can be im proved by considering the test results obtained.
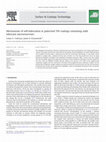
Surface & Coatings Technology, Apr 1, 2010
The tribological mechanisms of friction and lubrication have been investigated in TiN coatings pa... more The tribological mechanisms of friction and lubrication have been investigated in TiN coatings patterned to contain microscopic reservoirs for solid lubricant entrapment. Photo-lithography was used to fabricate three sets of samples on silicon wafers, varying the reservoir size (4 and 9 μm) and spacing (11 and 25 μm), which resulted in samples with a nominal reservoir area of either 2 or 10%. Pin-on-disk tests were run using lubricants of graphite and indium and counterfaces of alumina and steel (440C). In most cases, the samples with the 9 μm holes spaced 25 μm apart gave the lowest friction coefficients and longest wear life. Analysis of the wear tracks by SEM/EDS methods showed carbon to be present in the holes of the graphite/steel counterface samples, but TiO 2 was found in the holes of the graphite/alumina counterface samples. For the indium/steel counterface samples indium was detected within the microreservoirs, but iron was also found, transferred from the ball. These experiments highlight a variety of tribological mechanisms that can operate in microreservoir-patterned coatings.
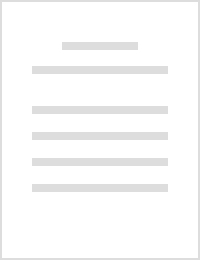
Surface & Coatings Technology, Feb 1, 2008
ABSTRACT The concept of incorporating microscopic reservoirs within a hard coating for the purpos... more ABSTRACT The concept of incorporating microscopic reservoirs within a hard coating for the purpose of solid lubricant storage and supply during wear of interacting surfaces has been investigated in this study. A novel method was devised using ceramic beads (1.5–10 μm diameter) as placeholders during the deposition of a TiN coating by reactive sputter deposition. A pin-on-disk wear test was used to test these coatings using graphite and sputter-deposited carbon as the solid lubricant, and an alumina counterface. When tested without any lubricant, the presence of the microreservoirs in the TiN coating appeared to degrade the mechanical integrity of the coating leading to rapid failure. With the graphite lubricant present, the frictional behavior ranged from levels similar to the TiN coating alone, to that of graphite alone. Tests of the TiN coating made using 10 μm beads running against an aluminum counterface showed substantial improvement when the microreservoirs were present. Optical microscopy examination of the wear tracks showed the microreservoirs were generally successful at trapping the graphite lubricant during wear. With a sufficient density and appropriate distribution of the microreservoirs significant improvements in tribological performance can be realized.
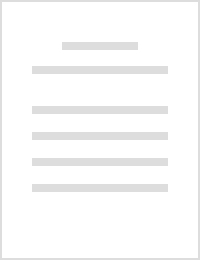
MRS Proceedings, 2007
ABSTRACTHard coatings containing microscopic reservoirs for solid lubricant storage have the pote... more ABSTRACTHard coatings containing microscopic reservoirs for solid lubricant storage have the potential to advance the development of dry, self-lubricating coatings. In the present study we have investigated several methods for fabricating hard coatings that incorporate microscopic reservoirs. These methods all involve the use of placeholders on the substrate surface that are later removed after deposition of the hard coating. One method uses a solution containing ceramic beads, while the second method uses conventional photolithography methods. Coatings using both of these methods were fabricated using TiN as the hard coating. The effectiveness of the microreservoirs for solid lubricant storage was examined by conducting pin-on-disk test using various solid lubricants, including graphite and indium. The performance of coatings with random arrangements of microreservoirs was scattered while samples with the ordered arrangements of microreservoirs all performed well. Optical microscopy examination of the wear tracks showed the microreservoirs were generally successful at trapping the graphite lubricant during wear. With a sufficient density and appropriate distribution of the microreservoirs, the significant improvements in tribological performance can be realized.
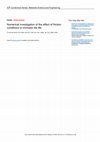
IOP Conference Series: Materials Science and Engineering, 2017
The standard die materials in aluminium extrusion offer good mechanical properties like high temp... more The standard die materials in aluminium extrusion offer good mechanical properties like high tempering resistance, high strength and ductility. On the other hand, they struggle with the problem of sliding wear. As a result, there is a growing interest in using surface treatment techniques to increase the wear resistance of extrusion dies. In this study, it is aimed to observe the effects of the different friction conditions on material flow and contact pressure in extrusion process. These friction conditions can be obtained with the application of a variety of surface treatment. In this way, it is expected to decrease the friction force on the die bearing area and to increase the homogeneity of the material flow which will result in the increase of the quality of the extrudate as well as the improvement of the process economically by extending die life. For this purpose, an extrusion process is simulated with a finite element software. A die made of 1.2344 hot work tool steel-commonly used die material for aluminium extrusion process-has been modelled and Al 1100 alloy used as billet material. Various friction factor values defined on the die surface under the same process parameters and effects of changing frictional conditions on the die and the extrusion process have been discussed.
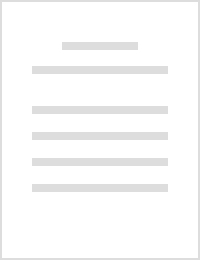
PubMed, Oct 9, 2003
This study determined the three-body abrasive wear resistance of two packable composites (P-60; S... more This study determined the three-body abrasive wear resistance of two packable composites (P-60; Solitaire 2), an ion-releasing composite (Ariston AT), a hybrid composite (Tetric Ceram) and an ormocer (Admira). The study also looked at the correlation between wear resistance and hardness of the composites. Three-body wear testing was performed using an ACTA wear machine with 15 N contact force using millet seed as the third body. Wear depth (microm) was measured by profilometry after 200,000 cycles. The hardness test was performed using a digital microhardness tester (load: 500 g; dwell time: 15 seconds). The data were analyzed by using Kruskal Wallis (p < 0.05). There were statistically significant differences among the three body abrasive wear of the composites. The ranking from least to most were as follows: Filtek P-60 < Solitaire 2 < Ariston AT < Tetric Ceram < Admira. Filtek P-60 showed the highest microhardness value. No other significant differences in hardness were observed among the different resin composites (P-60 > AristonAT = Tetric Ceram = Solitaire 2 = Admira). The results of this study indicate that there are significant differences in the wear resistance of the resin composites. The correlation between hardness and wear was significant with a correlation coefficient of r:-0.91. A significant negative correlation exists between hardness and three-body wear of resin composites.
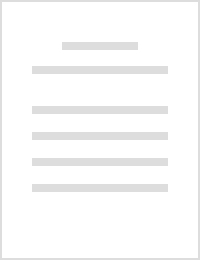
Operative dentistry, 2003
This study determined the three-body abrasive wear resistance of two packable composites (P-60; S... more This study determined the three-body abrasive wear resistance of two packable composites (P-60; Solitaire 2), an ion-releasing composite (Ariston AT), a hybrid composite (Tetric Ceram) and an ormocer (Admira). The study also looked at the correlation between wear resistance and hardness of the composites. Three-body wear testing was performed using an ACTA wear machine with 15 N contact force using millet seed as the third body. Wear depth (microm) was measured by profilometry after 200,000 cycles. The hardness test was performed using a digital microhardness tester (load: 500 g; dwell time: 15 seconds). The data were analyzed by using Kruskal Wallis (p < 0.05). There were statistically significant differences among the three body abrasive wear of the composites. The ranking from least to most were as follows: Filtek P-60 < Solitaire 2 < Ariston AT < Tetric Ceram < Admira. Filtek P-60 showed the highest microhardness value. No other significant differences in hardness...
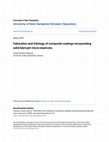
The tribological behavior of composite coating incorporating solid lubricant reservoirs has been ... more The tribological behavior of composite coating incorporating solid lubricant reservoirs has been investigated in this study. A new method, termed " microbeading" was devised to create microscopic reservoirs on the surface of sputter-deposited hard coatings. Pin-on-disk tests were used to evaluate the lubricating performance of these newly devised composite coatings. Three sizes of the reservoirs were investigated: 1.5, 5 and 10 microm. The 10 microm-sized-reservoirs performed better in terms of reducing friction and extending wear life. These coatings were also evaluated with finite element models. It was found that during ball-coating surface interaction, the lowest stresses and calculated work done were obtained at a critical location at the bottom of hole on the coating with 10 microm holes. Further investigations were conducted using photolithography to fabricate the coatings, which allows a more controlled reservoir distribution on the surface. For these tests, silico...
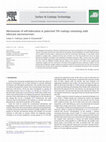
Surface Coatings Technology, 2010
The tribological mechanisms of friction and lubrication have been investigated in TiN coatings pa... more The tribological mechanisms of friction and lubrication have been investigated in TiN coatings patterned to contain microscopic reservoirs for solid lubricant entrapment. Photo-lithography was used to fabricate three sets of samples on silicon wafers, varying the reservoir size (4 and 9 μm) and spacing (11 and 25 μm), which resulted in samples with a nominal reservoir area of either 2 or 10%. Pin-on-disk tests were run using lubricants of graphite and indium and counterfaces of alumina and steel (440C). In most cases, the samples with the 9 μm holes spaced 25 μm apart gave the lowest friction coefficients and longest wear life. Analysis of the wear tracks by SEM/EDS methods showed carbon to be present in the holes of the graphite/steel counterface samples, but TiO 2 was found in the holes of the graphite/alumina counterface samples. For the indium/steel counterface samples indium was detected within the microreservoirs, but iron was also found, transferred from the ball. These experiments highlight a variety of tribological mechanisms that can operate in microreservoir-patterned coatings.
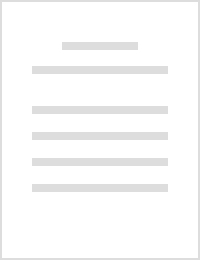
Operative dentistry
This study determined the three-body abrasive wear resistance of two packable composites (P-60; S... more This study determined the three-body abrasive wear resistance of two packable composites (P-60; Solitaire 2), an ion-releasing composite (Ariston AT), a hybrid composite (Tetric Ceram) and an ormocer (Admira). The study also looked at the correlation between wear resistance and hardness of the composites. Three-body wear testing was performed using an ACTA wear machine with 15 N contact force using millet seed as the third body. Wear depth (microm) was measured by profilometry after 200,000 cycles. The hardness test was performed using a digital microhardness tester (load: 500 g; dwell time: 15 seconds). The data were analyzed by using Kruskal Wallis (p < 0.05). There were statistically significant differences among the three body abrasive wear of the composites. The ranking from least to most were as follows: Filtek P-60 < Solitaire 2 < Ariston AT < Tetric Ceram < Admira. Filtek P-60 showed the highest microhardness value. No other significant differences in hardness...
Operative …, 2003
This study determined the three-body abrasive wear resistance of two packable composites (P-60; S... more This study determined the three-body abrasive wear resistance of two packable composites (P-60; Solitaire 2), an ion-releasing composite (Ariston AT), a hybrid composite (Tetric Ceram) and an ormocer (Admira). The study also looked at the correlation between wear ...
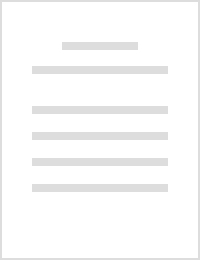
Operative dentistry
This study determined the three-body abrasive wear resistance of two packable composites (P-60; S... more This study determined the three-body abrasive wear resistance of two packable composites (P-60; Solitaire 2), an ion-releasing composite (Ariston AT), a hybrid composite (Tetric Ceram) and an ormocer (Admira). The study also looked at the correlation between wear resistance and hardness of the composites. Three-body wear testing was performed using an ACTA wear machine with 15 N contact force using millet seed as the third body. Wear depth (microm) was measured by profilometry after 200,000 cycles. The hardness test was performed using a digital microhardness tester (load: 500 g; dwell time: 15 seconds). The data were analyzed by using Kruskal Wallis (p < 0.05). There were statistically significant differences among the three body abrasive wear of the composites. The ranking from least to most were as follows: Filtek P-60 < Solitaire 2 < Ariston AT < Tetric Ceram < Admira. Filtek P-60 showed the highest microhardness value. No other significant differences in hardness...
Journal of Scientific Industrial Research, 2003
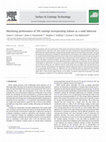
Surface and Coatings Technology, 2009
The machining and wear performance of TiN-coated and patterned carbide inserts incorporating indi... more The machining and wear performance of TiN-coated and patterned carbide inserts incorporating indium as a solid lubricant are reported in this study. Cutting tests were conducted by turning hardened 4340 steel in both lubricated and dry conditions. During turning, periodic flank wear measurements were made. The chips formed during cutting were examined by scanning electron microscopy, as the condition of the chip reflects the conditions obtained during machining. Inserts subject to dry machining were also examined using optical microscopy and X-ray photoelectron spectroscopy to determine the extent of damage on the rake surface as well as the degree of material transfer. The results showed indium to be effective in reducing flank wear during lubricated machining, but little additional benefit of patterning was observed. For dry machining, some degree of improvement was noted in the patterned sample, but the degree of lubricity brought about by the indium coating was not sufficient and the overall flank wear was higher than the lubricated tests. However, the wear and damage on the rake surface along the path of the chip was reduced by the presence of the In-containing microreservoirs. An additional test was conducted using an instrument that simulates temperature effects during machining, and it was found that the lubricity achieved by In coatings is lost above 450°C. These results suggest that the use of indium is limited to below this temperature, and above this temperature transforms to a less lubricious indium oxide.

Surface and Coatings Technology, 2010
The tribological mechanisms of friction and lubrication have been investigated in TiN coatings pa... more The tribological mechanisms of friction and lubrication have been investigated in TiN coatings patterned to contain microscopic reservoirs for solid lubricant entrapment. Photo-lithography was used to fabricate three sets of samples on silicon wafers, varying the reservoir size (4 and 9 μm) and spacing (11 and 25 μm), which resulted in samples with a nominal reservoir area of either 2 or 10%. Pin-on-disk tests were run using lubricants of graphite and indium and counterfaces of alumina and steel (440C). In most cases, the samples with the 9 μm holes spaced 25 μm apart gave the lowest friction coefficients and longest wear life. Analysis of the wear tracks by SEM/EDS methods showed carbon to be present in the holes of the graphite/steel counterface samples, but TiO 2 was found in the holes of the graphite/alumina counterface samples. For the indium/steel counterface samples indium was detected within the microreservoirs, but iron was also found, transferred from the ball. These experiments highlight a variety of tribological mechanisms that can operate in microreservoir-patterned coatings.
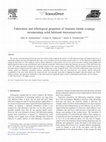
Surface and Coatings Technology, 2008
The concept of incorporating microscopic reservoirs within a hard coating for the purpose of soli... more The concept of incorporating microscopic reservoirs within a hard coating for the purpose of solid lubricant storage and supply during wear of interacting surfaces has been investigated in this study. A novel method was devised using ceramic beads (1.5-10 μm diameter) as placeholders during the deposition of a TiN coating by reactive sputter deposition. A pin-on-disk wear test was used to test these coatings using graphite and sputter-deposited carbon as the solid lubricant, and an alumina counterface. When tested without any lubricant, the presence of the microreservoirs in the TiN coating appeared to degrade the mechanical integrity of the coating leading to rapid failure. With the graphite lubricant present, the frictional behavior ranged from levels similar to the TiN coating alone, to that of graphite alone. Tests of the TiN coating made using 10 μm beads running against an aluminum counterface showed substantial improvement when the microreservoirs were present. Optical microscopy examination of the wear tracks showed the microreservoirs were generally successful at trapping the graphite lubricant during wear. With a sufficient density and appropriate distribution of the microreservoirs significant improvements in tribological performance can be realized.
Uploads
Papers by Canan G Guleryuz Parasız