Journal Articles by Vincent B.C. Tan
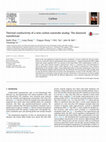
Based on the non-equilibrium molecular dynamics simulations, we have studied the thermal conducti... more Based on the non-equilibrium molecular dynamics simulations, we have studied the thermal conductivities of a novel ultra-thin one-dimensional carbon nanomaterial e diamond nanothread (DNT). Unlike single-wall carbon nanotube (CNT), the existence of the Stone-Wales (SW) transformations in DNT endows it with richer thermal transport characteristics. There is a transition from wave-dominated to particle-dominated transport region, which depends on the length of poly-benzene rings. However, independent of the transport region, strong length dependence in thermal conductivity is observed in DNTs with different lengths of poly-benzene ring. The distinctive SW characteristic in DNT provides more to tune the thermal conductivity not found in the homogeneous structure of CNT. Therefore, DNT is an ideal platform to investigate various thermal transport mechanisms at the nanoscale. Its high tunability raises the potential to design DNTs for different applications, such as thermal connection and temperature management.
Papers by Vincent B.C. Tan

Journal of the European Ceramic Society, 2006
The chemical interaction between Fe-Cr alloy interconnect and constituent oxides of Sr-doped LaMn... more The chemical interaction between Fe-Cr alloy interconnect and constituent oxides of Sr-doped LaMnO 3 (LSM) coating, La 2 O 3 , SrO and Mn 2 O 3 , is investigated at 800-900 • C in air. The Cr deposition reaction between the Fe-Cr alloy metallic interconnect and oxides varies significantly with the nature of the oxides. The interaction between the Fe-Cr alloy and La 2 O 3 and Mn 2 O 3 oxide coatings primarily results in the formation of LaCrO 3 and (Cr, Mn) 3 O 4 while in the case of SrO oxide coating, Cr 2 O 3 is the main product. In the case of LSM coating, the formation of (Cr, Mn) 3 O 4 and Cr 2 O 3 is identified. The results indicate that the chemical interaction between the Fe-Cr alloy interconnect and LSM coating is most likely related to the surface oxide species such as SrO and MnO x initially enriched or segregated on the surface of LSM particularly in the early stages of the reaction.
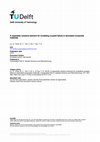
Composites Part A: Applied Science and Manufacturing, 2018
A three-dimensional separable cohesive element (SCE) is proposed to enable the modelling of inter... more A three-dimensional separable cohesive element (SCE) is proposed to enable the modelling of interaction between matrix cracking and interfacial delamination in laminated fibre-reinforced composite materials. It is demonstrated that traditional cohesive elements are incapable of modelling the coupled failure mechanisms accurately if partitioning is not allowed. The SCE may be partitioned according to the configuration and geometry of matrix cracks in adjacent plies, thus maintaining appropriate connection between plies. Physically, the original interface is split and new interfaces are formed to bond the homologous cracked solids during fracturing process. The stress concentration induced by matrix cracks and the load transfer from cracked solid elements to interface cohesive element are effectively modelled. A comprehensive set of cases of multiple matrix crack configurations from plies of different fiber angles is considered. The proposed SCE is applied to model progressive failure in composite laminates and the results are found to agree with experiments.

International Journal for Numerical Methods in Biomedical Engineering, 2017
Blast-induced traumatic brain injury (TBI) has been on the rise in recent years due to the increa... more Blast-induced traumatic brain injury (TBI) has been on the rise in recent years due to the increasing use of improvised explosive devices (IEDs) in conflict zones. Our study investigates the response of a helmeted human head subjected to a blast of 1 atm peak overpressure, for cases with and without a standard polycarbonate (PC) face shield and for face shields comprising of composite PC and aerogel materials and with lateral edge extension. The novel introduction of aerogel into the laminate face shield is explored and its wave-structure interaction mechanics and performance in blast mitigation is analysed. Our numerical results show that the face shield prevented direct exposure of the blast wave to the face and help delays the transmission of the blast to reduce the intracranial pressures (ICPs) at the parietal lobe. However, the blast wave can diffract and enter the midface region at the bottom and side edges of the face shield, resulting in TBI. This suggests that the bottom and sides of the face shield are important regions to focus on to reduce wave ingress. The

Medical & biological engineering & computing, Jan 13, 2016
The current study aims to investigate the effectiveness of two different designs of helmet interi... more The current study aims to investigate the effectiveness of two different designs of helmet interior cushion, (Helmet 1: strap-netting; Helmet 2: Oregon Aero foam-padding), and the effect of the impact directions on the helmeted head during ballistic impact. Series of ballistic impact simulations (frontal, lateral, rear, and top) of a full-metal-jacketed bullet were performed on a validated finite element head model equipped with the two helmets, to assess the severity of head injuries sustained in ballistic impacts using both head kinematics and biomechanical metrics. Benchmarking with experimental ventricular and intracranial pressures showed that there is good agreement between the simulations and experiments. In terms of extracranial injuries, top impact had the highest skull stress, still without fracturing the skull. In regard to intracranial injuries, both the lateral and rear impacts generally gave the highest principal strains as well as highest shear strains, which exceed t...
International Journal of Solids and Structures, 2006
The objective of this paper is to evaluate a number of shell elements. At the same time, a new el... more The objective of this paper is to evaluate a number of shell elements. At the same time, a new element is presented that is inspired by the quadrilateral heterosis element, Q8H, and is designated herein as the triangular heterosis element, T6H. Both elements employ the selectively reduced integration method. The elements investigated in this study include ABAQUS's three general-purpose shell elements, ANSYS's six-noded triangular element, T6, and the high-performance MITC9 element available in ADINA. The assessment is carried out by subjecting the various elements to several benchmark problems. It is found that for regular meshes, Q8H out-performs other elements and is comparable to MITC9. The performance of T6H is shown to be comparable to that of T6 in most test cases, but superior when very thin shells are considered.

Carbon, 2016
Based on the non-equilibrium molecular dynamics simulations, we have studied the thermal conducti... more Based on the non-equilibrium molecular dynamics simulations, we have studied the thermal conductivities of a novel ultra-thin one-dimensional carbon nanomaterial-diamond nanothread (DNT). Unlike single-wall carbon nanotube (CNT), the existence of the Stone-Wales transformations in DNT endows it with richer thermal transport characteristics. There is a transition from wave-dominated to particle-dominated transport region, which depends on the length of poly-benzene rings. However, independent of the transport region, strong length dependence in thermal conductivity is observed in DNTs with different lengths of poly-benzene ring. The distinctive SW characteristic in DNT provides more degrees of freedom to tune the thermal conductivity not found in the homogeneous structure of CNT. Therefore, DNT is an ideal platform to investigate various thermal transport mechanisms at the nanoscale. Its high tunability raises the potential to design DNTs for different applications, such as thermal connection and temperature management.
Nanotechnology, 2009
Presented herein is an investigation into the buckling behavior of single-walled carbon nanotubes... more Presented herein is an investigation into the buckling behavior of single-walled carbon nanotubes (SWCNT) subjected to axial compression and torsion at high temperatures. This study is carried out by performing molecular dynamics (MD) simulations at both room temperature and extremely high temperatures. It is observed that the SWCNT becomes more susceptible to buckling in a higher temperature environment, especially when the SWCNT is subject to axial compression. The high thermal energy enhances the vibration of carbon atoms in the SWCNT significantly, which leads to bond breaking and the formation of sp(3) bonds as well as Stone-Wales (SW) defects in the postbuckling stage.
Computational Materials Science, 2006
ABSTRACT

Composites Science and Technology, 2005
The element-failure method (EFM) is a novel finite element-based method for the modelling of dama... more The element-failure method (EFM) is a novel finite element-based method for the modelling of damage, fracture and delamination in fibre-reinforced composite laminates. The nature of damage in composite laminates is generally diffused and complex, characterized by multiple matrix cracks, fibre pullout, fibre breakage and delaminations. It is usually not possible to model or identify crack tips in the conventional fashion of fracture mechanics. The central idea of the EFM, on the other hand, is to model the damaged portions with partially failed elements, whose nodal forces have been modified to take into account the local damage modes. This has the additional benefit of unconditional computational stability compared to other methods such as material property degradation (MPD) models. Here, we present the application of EFM with a recently-proposed failure criterion called the Strain Invariant Failure Theory (SIFT) in the prediction of damage progression in a composite laminated structure, and show that the damage patterns are in very good agreement with experiments. It is also shown that the EFM is more versatile and general than the MPD method.

Acta Mechanica, 2013
This paper presents a general and efficient stress analysis strategy for hollow composite cylindr... more This paper presents a general and efficient stress analysis strategy for hollow composite cylindrical structures consisting of multiple layers of different anisotropic materials subjected to different loads. Cylindrical material anisotropy and various loading conditions are considered in the stress analysis. The general stress solutions for homogenized hollow anisotropic cylinders subjected to pressure, axial force, torsion, shear and bending are presented with explicit formulations under typical force and displacement boundary conditions. The stresses and strains in a layer of the composite cylindrical structures are obtained from the solutions of homogenized hollow cylinders with effective material properties and discontinuous layer material properties. Effective axial, torsional, bending and coupling stiffness coefficients taking into account material anisotropy are also determined from the strain solutions for the hollow composite cylindrical structures. Examples show that the material anisotropy may have significant effects on the effective stiffness coefficients in some cases. The stress analysis method is demonstrated with an example of stress analysis of a 22-layer composite riser, and the results are compared with numerical solutions. This method is efficient for stress analysis of thin-walled or moderately thick-walled hollow composite cylindrical structures with various multiple layers of different materials or arbitrary fiber angles because no explicit interfacial continuity parameters are required. It provides an efficient and easy-to-use analysis tool for assessing hollow composite cylindrical structures in engineering applications.

International Journal of Damage Mechanics, 2007
Modeling progressive damage in composite materials and structures poses considerable challenges b... more Modeling progressive damage in composite materials and structures poses considerable challenges because damage is, in general, complex and involves multiple modes such as delamination, transverse cracking, fiber breakage, fiber pullout, etc. Clearly, damage in composites can be investigated at different length scales, ranging from the micromechanical to the macromechanical specimen and structural scales. In this article, a simple but novel finite-element-based method for modeling progressive damage in fiber-reinforced composites is presented. The element-failure method (EFM) is based on the simple idea that the nodal forces of an element of a damaged composite material can be modified to reflect the general state of damage and loading. This has an advantage over the usual material property degradation approaches, i.e., because the stiffness matrix of the element is not changed, computational convergence is theoretically guaranteed, resulting in a robust modeling tool. The EFM, when ...

Composites Part C: Open Access, 2021
In this study, the strain-rate dependent compressive failure of cylindrical carbon fiber reinforc... more In this study, the strain-rate dependent compressive failure of cylindrical carbon fiber reinforced plastics (CFRP) is simulated by using Direct FE 2. The Direct FE 2 method can reduce the computational cost compared with conventional FE 2 multiscale simulation. It can be implemented with commercial FE code, without the complicated coding usually required for conventional FE 2. At the microscale level, the true dimension of the individual fibers, failure of the fiber/matrix interface, and the strain-rate dependence of failure strength of the matrix material are modeled. These microscale characteristics are used to directly model the macroscale strain-rate dependent failure of a cylindrical CFRP specimen subjected to the Split Hopkinson Pressure Bar (SHPB) test. The obtained FE 2 numerical results are in good agreement with the experimental results.

Carbon, 2016
In this work, we report on the effective implementation of the direct and scalable floating catal... more In this work, we report on the effective implementation of the direct and scalable floating catalyst method to synthesize self-supporting carbon nanotube (CNT) aerogels at high deposition rates. Through the adaptable process conditions, the highly porous and ultralight CNT aerogels with densities ranging from 0.55 to 32 mg/cm 3 are synthesized. The aerogels exhibit high porosity (>98%) and surface areas of up to 170 m 2 /g with tortuous pores easy accessible to molecules of interest. Their superior electrical conductivity (up to 106 S/m), in comparison with CNT aerogels produced through other methods, indicates high potential for energy applications. The thermal conductivity has been observed to be within the range of 0.127e0.137 W/m$K as a consequence of the ultralight structure. Polymer infiltration and subsequent curing do not disturb the three-dimensional percolating CNT network and constitute an accessible method for the production of various lightweight polymeric composites. The polydimethylsiloxane-based composites (4.5% wt) with electrical conductivity enhanced by~16 orders of magnitude and thermal conductivity double that of pure matrix are particularly promising for use in biointegrated devices and flexible composites.
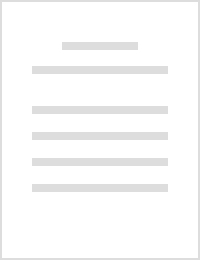
Journal of Multiscale Modelling
Structural performance of unidirectional composites (UD) is directly dependent on its ingredient’... more Structural performance of unidirectional composites (UD) is directly dependent on its ingredient’s properties, ply configurations and the manufacturing effects. Prediction of mechanical properties using multiscale manufacturing simulation and micromechanical models is the focus of this study. Particular problem of coupled dual-scale deformation-flow process such as the one arising in RTM, Vacuum-Assisted Resin Infusion (VARI) and Vacuum Bag Only (VBO) prepregs is considered. A finite element formulation of porous media theory framework is employed to predict the element-wise local volume fractions and the deformation of a preform in a press forming process. This formulation considers coupling effects between macro-scale preform processes and mesoscale ply processes as well as coupling effects between the solid and fluid phases. A number of different micromechanical models are assessed and the most suitable one is used to calculate mechanical properties from volume fractions. Structu...
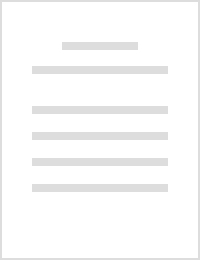
Composite Structures
Abstract In obtaining mechanical properties of filament-wound fibre reinforced plastic pipes, sta... more Abstract In obtaining mechanical properties of filament-wound fibre reinforced plastic pipes, standardized tests are often used to obtain bulk properties. Being a laminated composite, individual layers of the lamina will behave differently and therefore pipe-level characterizations are usually unable to fully describe the localised responses in detail. Unlike flat composite layups, obtaining unidirectional ply properties in cylindrical filament-wound composites is not as straight-forward. In this work, the composite pipe stress homogenization theory was applied in reverse to obtain the corresponding ply properties in the filament-wound pipe through successive iterations towards experimentally obtained bulk properties. Initial estimates of ply properties were obtained through a combination of extensive literature search and applications of micromechanics theories. With the iterated ply properties, finite element models simulating the tests used to obtain bulk properties were performed to validate the accuracy of the material properties. In addition, additional validation was performed on a smaller pipe section to evaluate the scalability of using ply properties across pipes of different dimensions. It was found that the ply properties obtained was able to accurately predict the responses for pipes of various dimensions.

Computer Methods in Applied Mechanics and Engineering
This paper presents the modelling of tensile failure of composites using novel enriched elements ... more This paper presents the modelling of tensile failure of composites using novel enriched elements defined based on the floating node method. An enriched ply element is developed, such that a matrix crack can be modelled explicitly within its domain. An enriched cohesive element is developed to incorporate the boundaries of matrix cracks on the interface, such that the local stress concentrations on the interface can be captured. The edge status variable approach allows the automatic propagation of a large number of matrix cracks in the mesh. A laminate element is formed, such that a fixed, planar mesh can be used for laminates of arbitrary layups. The application examples demonstrate that the proposed method is capable of predicting several challenging scenarios of composites tensile failure, such as the large number matrix cracks, grip-to-grip longitudinal splits, widespread delamination, explosive splitting and distributed fibre breaking in the 0 plies, etc. The complete failure process of ply-blocked composite laminates, up to the final breaking of the loosened 0 ¶ strips, are here firstly reproduced by modelling.
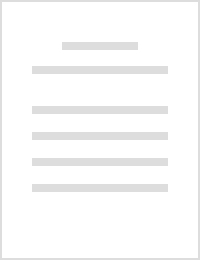
Structural and Multidisciplinary Optimization
The development of flapping wing micro air vehicles (MAVs) has yielded remarkable progress over t... more The development of flapping wing micro air vehicles (MAVs) has yielded remarkable progress over the last decades. Achieving high component stiffness is often in conflict with low weight requirement, which is highly desirable for longer flight time and higher payload. Moreover, vibration originated predominantly from the wings, gears and frames excitations, may compromise the flapping wing MAV’s stability and fatigue life. In order to improve the vehicle’s efficiency and performance, optimization of these various parameters is necessary. In this work, we present the structural optimization of a flapping wing micro air vehicle. We focus particularly on the gearbox optimization using Simulia Tosca Structure in Abaqus, which is a robust tool for designing lightweight, rigid and durable components. Various numerical experiments have been conducted towards optimizing the components’ topology, aimed at increasing the stiffness and reducing weight. The finding and results provide a better understanding of the optimal design topology for a spur gear among other structural components used in MAVs.

Journal of Reinforced Plastics and Composites
The high strength to weight ratio, good corrosion resistance, and excellent fatigue property make... more The high strength to weight ratio, good corrosion resistance, and excellent fatigue property make carbon fiber-reinforced plastics a competitive material solution to replace steel in deepwater riser application. In this work, scaled-down composite riser joints were fabricated using a filament-winding machine. The prototypes comprise several carbon fiber-reinforced plastic layers wound over an aluminum liner. They consist of a middle tubular section and two metal-composite interface end fittings for the transfer of load between joints. A series of mechanical tests, including tension and combined tension-bending loading tests were performed to characterize their structural capacity and evaluate the improvement in performance over a purely metallic mandrel. In addition, finite element analyses incorporating elastic–plastic properties of the metallic liner, interfacial failure, and complex carbon fiber-reinforced plastics failure modes were carried out. The numerical predictions are in ...
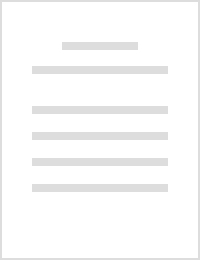
Experimental Mechanics
A novel method for dynamic testing of small specimens, based on impact loading, is proposed. This... more A novel method for dynamic testing of small specimens, based on impact loading, is proposed. This is motivated by the desire to elicit the dynamic mechanical response of single solder joints measuring 0.5 mm smaller in size. Impact loading is generated through impact of a tubular striker against a loading plate which is initially in contact with the specimen. The mechanical response of the specimen is derived from noting the stress waves generated in slender bars attached to the loading plate and specimen. Through this approach, dynamic tension or compression can be conveniently applied using the same test apparatus, and exact alignment of the slender bars attached is not critical. In addition, wave dispersion or attenuation in the bars (e.g., when polymer bars are used) has much less influence on the accuracy of results obtained. The equations governing this novel approach are derived and validated by finite element modeling. A prototype of a miniature impact tester was consequently fabricated, and tests on small aluminum specimens showed results comparable to that employing traditional split Hopkinson bar systems. The test arrangement was utilized for dynamic testing of lead-free single solder joint specimens, and initial results obtained are presented.
Uploads
Journal Articles by Vincent B.C. Tan
Papers by Vincent B.C. Tan