Papers by Oleg Kolisnichenko
2022 IEEE 12th International Conference Nanomaterials: Applications & Properties (NAP)

List of Tables 2.1 Technological parameters of the electrolytic-plasma unit 2.2 Modes of electrol... more List of Tables 2.1 Technological parameters of the electrolytic-plasma unit 2.2 Modes of electrolytic-plasma hardening of the sample surface 2.3 Comparative analysis of the efficiency of shaft hardening by electrolytic-plasma technology and nitriding 2.4 Characteristics of the hardened layer depending on the material of the product and technological processing parameters 3.1 Modes of electrolytic-plasma technology for cleaning and heating rolled products 4.1 Content of Cr and Si after electrolytic-plasma heating of the surface in different modes 4.2 Content of chemical elements of a sample doped from an electrolyte containing copper oxide powder 4.3 Content of chemical elements on the sample surface (heating temperature is 900 °С) doped from an electrolyte containing powders of titanium oxide, aluminum oxide and carbon 4.4 Content of chemical elements on the sample surface (heating temperature 1100 °С), doped from an electrolyte containing powders of titanium oxide, aluminum oxide and carbon 5.1 Technical data of the reaction chamber 5.2 Phase composition of the ceramic layer 5.3 Modes and some characteristics of oxide films [106-109] viii List of Figures 1.1 Diagram of an electrolytic-plasma heater 1.2 Change in the strength of the electric field between the surface of the product, the cathode and the anode 1.3 View of the gap between the metal cathode-1 and the liquid electrode anode-2 at electric potential voltages: a-U 1 = 60-120 V; b-U 2 = 80-160 V; c-U 3 = 120-200 V; d-U 4 = 180-260 V; e-U 5 = 240-320 V 1.4 Layout of thermoelectric junctions in the surface layer of the sample when measuring temperature in the process of electrolyte-plasma heating 1.5 Temperatures of the surface of the product depending on the heating time (1; 2; 3) and cooling time (4; 5; 6; 7) with periodic connection of the electric potential, which has the following intensity: 1-U

The results of the study of the mechanical properties of the surface layers in the products made ... more The results of the study of the mechanical properties of the surface layers in the products made out of die steel, high-speed steel, high-strength cast iron and hard alloy modified by pulse plasma are presented. Processing of products was performed by a pulse plasma generator with speed and temperature of plasma flow of up to 6 km/s and 12000 K, respectively. Plasma produces a comlex cyclic pulse (ν=2 Hz;time<0.6 ms) impact on the surface:thermal impact (the thermal stream density of up 10 6 W/cm 2 ), and electromagnetic impact (current density of up to 10 kA/cm 2 , magnetic field strength of up to 4*10 5 A/m). The research of tool steel 60WCrV7 has shown that after processing the microstucture of the surface layer up to 60 mcm thick undergoes further refinement. The average micro-hardness of the layer thus processed increases up to HV 0.025 =9360 MPa, though standard heat treatment produces hardness of HV 0.025 =6740 MPa. The wear resistance of the modified tool steel surface in...

The report presents the results of studies of changes in the structure, phase composition, mechan... more The report presents the results of studies of changes in the structure, phase composition, mechanical and operational properties of the surface of metal products due to the impact of pulsed flow of ionizedgas and pulsed electric discharge. In the prototype of the industrial installation detonation products of gas mixture of propane, butane, oxygen, nitrogen are additionally heated up by the discharge of the 1000 microfarad capacity with voltage of up to 3500 V. Pulsed flow of ionized gas having temperature of up to 12000 K together with the pulsed electric discharge having a current density of up to 10000 A/cm 2 produce a manifold impact on the surface including the thermal impact with power density of up to 10 7 W/cm 2 , chemical impact, electromagnetic impact (stength of magnetic field up to 4*10 5 A/m) and mechanical impact. Pulse duration is up to 10 -3 s, pulse frequency is up to 5 Hz. Modification of the surface layer takes place at the depth of up to 60 microns and includs th...
High Temperature Material Processes An International Quarterly of High-Technology Plasma Processes, 2021

International Journal of Applied Ceramic Technology, 2020
A new multi-chamber cumulative detonation sprayer (MCDS) was applied to fabricate an aluminum oxi... more A new multi-chamber cumulative detonation sprayer (MCDS) was applied to fabricate an aluminum oxide coating on carbon/carbon composites. MCDS provides heating and acceleration of ceramic micropowders by means of combustible gas mixture detonation products with a frequency of 20 Hz and above. The ceramic aluminum oxide particle kinetic energy ensures the destruction of the weakened areas on the carbon-carbon composite material surface and the incorporation of these particles into the surface layer. The following powder particles decelerate on the already fixed particles and form a ceramic coating. The formed aluminum oxide coating is characterized by high hardness and low porosity (<1%). MCDS provides the formation of a high-quality ceramic layer, which can also serve as the basis for the formation of protective heat-resistant coatings.

Coatings, 2019
Composite ZrB2–MoSi2 coating modified by Y2O3 and Al was prepared by a new multi-chamber detonati... more Composite ZrB2–MoSi2 coating modified by Y2O3 and Al was prepared by a new multi-chamber detonation accelerator (MCDS) on carbon/carbon composites. Postdeposition heat treatment of the samples at 1500 °C for 1 and 6 h was carried out in air. The effect of heat treatment on the microstructure and phase composition of the ZrB2–MoSi2 coating was investigated by scanning electron microscopy and X-ray diffraction phase analysis. The as-sprayed coating presented as a dense lamellar structure, composed of m-ZrO2, t-ZrO2, some hexagonal ZrB2, and cubic Al phases. The m-ZrO2, c-ZrO2, and h-(α-Al2O3) formed at 1500 °C. The coatings after heat treatment (1 and 6 h) exhibited a structure without cracks. The porosity (~1%) of the coating did not change after heat treatment. Thin, continuous, silica-rich film covered the surfaces of ZrO2 and Al2O3 particles, and could have played a role during heat treatment by acting as a grain lubricant for particle rearrangement.

Coatings, 2017
In this work, dense zircon-based ceramic coatings were obtained from inexpensive zircon powder on... more In this work, dense zircon-based ceramic coatings were obtained from inexpensive zircon powder on a steel substrate by using a new multi-chamber gas-dynamic accelerator. The microstructure and phase composition of the coating were characterized by scanning electron microscopy, optical microscopy, and X-ray diffraction. The mechanical properties of the coatings were evaluated using microindentation, wear tests and bonding strength tests. The results showed that the obtained zircon-based ceramic coatings were continuous without cracks and bonded well with substrate without a sublayer. The zircon-based ceramic coatings consisted of c-ZrO 2 (major phase), m-ZrO 2 and SiO 2. The zircon-based ceramic coatings had a porosity of 0.1%, hardness of 526 ± 65 HV 0.2 , and a fracture toughness of 2.5 ± 0.6 (MPa•m 1/2). The coatings showed the low specific wear rate and average erosion rate. The failure mode occurring in the tested coatings was cohesive.
MATEC Web of Conferences, 2015
The alumina powder was treated at a high temperature (1000°C). Dense (porosity of less than 2%), ... more The alumina powder was treated at a high temperature (1000°C). Dense (porosity of less than 2%), solid (1280 ± 30 HV0.3) and wear-resistant coatings based on heat-treated alumina powder were obtained by a multi-chamber detonation sprayer on the steel substrate. The microstructure, microhardness and the wear resistance of the alumina coatings were investigated.
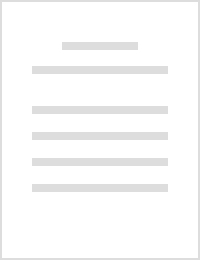
Abstract The paper presents the results of investigating the properties of metal and ceramic coat... more Abstract The paper presents the results of investigating the properties of metal and ceramic coatings deposited on the steel or the aluminium substrates by using a multi-chamber gas-dynamic accelerator. The multi-chamber gas-dynamic accelerator (MCDS) has replaceable nozzles and operates with a fuel mixture of low-pressure gases – propane (30 %) + butane (70 %) – oxygen – air. The velocity of the frontal area of the cloud of the Al 2 O 3 powder with particle sizes of 5.6 – 22.5 μm at a nozzle length of 500 mm is 1300 ± 200 m/s. MCDS with a nozzle length of 500 mm provides the conditions for formation of a dense ceramic layer having hardness of 1320 ± 25 HV 0.3 and porosity of less than 1 %. Productivity of the technology is 0.72 kg/h at a deposition efficiency - 65 %, flow rate of oxygen equal to 7.7 m 3 /h, and flow rate of propane + butane equal to 1.3 m 3 /h. High adhesion of the ceramic layer to the substrate is provided by the transition layer up to 15 μm thick. MCDS allows form Nano-crystalline coating of the titanium or nickel based alloy powders. The dense layer of lamellas and deformed particles of powder is formed on the sample surface. Lamellas consist of Nano-crystalline grains size of 30 – 100 nm. Scratch-test has shown that the coatings are plastic and have high adhesive and cohesive strength.
Vacuum, 2001
Using the Rutherford back scattering method and elastic recoil detection analysis of protons, X-r... more Using the Rutherford back scattering method and elastic recoil detection analysis of protons, X-ray diffraction analysis, transmission electron microscopy as well as tests for hardness, adhesion and heat conductivity, coatings of Al2O3 and Al2O3+Cr2O3 deposited using a plasma-detonation technique, were investigated. The coating was deposited by means of a plasmotron, in which the jet velocity reached 8000m/s and the temperature

The book contains data on development of the technologies based on the use of non-stationary elec... more The book contains data on development of the technologies based on the use of non-stationary electric discharges in plasma jets. Formation of a plasma jet takes place under the effect of non-stationary detonation waves propagating between electrode units. In this case the energy parameters of the plasma can be controlled by a fuel mixture composition, electric potential and geometric characteristics of a device. As a result of interaction with plasma, the treated surface is subjected to pulsed electromagnetic, thermal and elastic-deformation influence. The results of studies of modified layers subjected to pulse plasma treatment are presented. The book describes technologies and equipment that are commercially applied for modification of working surfaces of machine parts and tools. Examples of application of the technologies in metallurgy, mining industry, wood working, machine building and other industrial sectors are given. For engineering and technical workers of machine-building enterprises and institutions specializing in the field of hardening processing of products.
Uploads
Papers by Oleg Kolisnichenko