Papers by Maulana Azmi AG
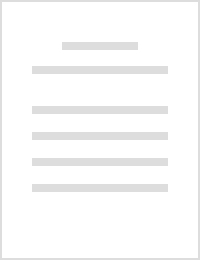
Key Engineering Materials
The development of micro-products in industry, like aviation, medical equipment, electronics, etc... more The development of micro-products in industry, like aviation, medical equipment, electronics, etc, has been increasing lately. The need for scaling down of product has been increasing to make the product simpler and complex. Micro-milling has capabilities in producing complex parts. In this study, mapping and comparing the result of the machining process of Inconel 718 and Aluminum Alloy 1100 was employed. In this experiment, Inconel 718 was used as workpiece material and the result of Aluminum Alloy taken from recent studies. Then, A cutting tool with a diameter 1 mm carbide coating TiAlN was used in this experiment. The machining process was performed with three varieties of spindle speed and feed rate with a constant depth of cut. After the machining is done, the mapping of the result surface roughness of Inconel 718 and AA1100 performed. It was found that Inconel 718 has poor machinability compared with AA 1100. Inconel 718 also has a high manufacturing cost compared to AA 1100 ...
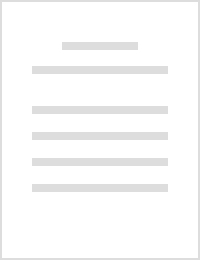
Key Engineering Materials, 2020
Micro-milling offers high flexibility by producing complex 3D micro-scale products. Weight reduct... more Micro-milling offers high flexibility by producing complex 3D micro-scale products. Weight reduction are one of the optimizations of the product that can make it stronger and more efficient nowadays. Titanium are the most commonly used for micro-scale products especially in biomedical industries because of the biocompatibility properties. Titanium alloys offers high strength with low density and high corrosion resistance that is suitable for weight reduction. This study aims to investigate the influence of high speed cutting parameters to the surface roughness in micromilling of titanium alloy Ti-6Al-4V as high speed cutting offers more productivity since producing more cutting length in the same time. experiments are carried out by micromilling process with variations in high speed cutting parameters of spindle speed and feed rate with a constant depth of cut using a carbide cutting tool of with a diameter of 1 mm. The machining results in the form of a 4 mm slot with a depth as th...

IOP Conference Series: Materials Science and Engineering, 2019
In recent years, the rapid technology development in industry sector, especially in aviation indu... more In recent years, the rapid technology development in industry sector, especially in aviation industry has been increasing. So that we need more capabilities in the micro-scale manufacturing process, especially micro-milling process which can produce good surface roughness and high complexity parts. In this study, the effect of machining parameters to the surface roughness investigated by using Inconel 718 material with cutting tool diameter 1 mm, carbide material with coating TiAlN. The machining process was performed in low speed machining category. There are three variations of spindle speed (3.000, 7.000, 10.000 RPM) and also feed rate (0.5, 1, 2 mm/s) with constant depth of cut 10 μm. The relationship between machining parameters and surface roughness was obtained. The higher the feed rate, the higher the surface roughness produced. On the other hand, the higher the spindle speed the smaller the surface roughness. It also found that the machining process with low spindle speed, ...

IOP Conference Series: Materials Science and Engineering, 2019
The demand for micro-scale products is increasing rapidly in various fields of industries such as... more The demand for micro-scale products is increasing rapidly in various fields of industries such as electronics, bio-medical, optical industry, and so on. Titanium alloys especially Ti-6Al-4V is one of the commonly used in bio-medical industries because of its biocompability properties. However, poor surface quality in terms of surface roughness commonly occurs because of unappropriate cutting parameters to machine this hard to cut material. This study aims to investigate the influencing machining parameters to produce micro-products with a low level of surface roughness in Titanium Alloy (Ti-6Al-4V) material using a miniaturized micro-milling machine. Experiments carried out by micromilling process with variations in low rpm spindle speed and feed rate with a constant depth of cut using a carbide cutting tool of with a diameter of 1 mm. The machining results in the form of a 4 mm slot with a depth of 10 μm, which then measures its surface roughness. It was found that as the feed rate...
E3S Web of Conferences, 2018
Micro milling is currently being used to make micro-sized products, such as in MEMS, medical devi... more Micro milling is currently being used to make micro-sized products, such as in MEMS, medical devices, etc. But in the process of machining, especially in roughing process, micro milling spends a lot of energy that can still be reduced to contribute to green manufacturing. This study focuses on developing the model of energy consumption during the micro milling processes. The model is then used to map the energy consumption from different cutting toolpaths and strategies. Furthermore this study also comparing and characterizing the energy consumed between macro milling and micro milling of the same part shape but with significant different in size. In conclusion, this study shows different characteristics and comparison in energy consumption between micro milling and macro milling.
Uploads
Papers by Maulana Azmi AG