Papers by Kausik Chattopadhyay
Journal of manufacturing and materials processing, May 31, 2022

International Journal of Surface Science and Engineering, 2017
Solution treated samples of titanium alloy Ti-6Al-4V were subjected to ultrasonic shot peening (U... more Solution treated samples of titanium alloy Ti-6Al-4V were subjected to ultrasonic shot peening (USSP) for different durations of 5, 15, and 30 minutes with hard steel balls of 3 mm diameter and examined for modification of microstructure, surface roughness and hardness profile. Based on microhardness profile a nanostructured layer of approximately 100 µm thickness resulted from the USSP. The shot peened surfaces were examined also by XRD for phase transformation, if any, resulting from USSP. Grain refinement was observed to nano scale due to USSP without any phase transformation. However, surface cracking was observed in the sample subjected to longer duration of 30 minutes and surface roughness was increased with duration of USSP. Microhardness of the 30 minutes shot peened surface was increased by ~34%, however, the increased hardness level was reduced by ~14%, following stress relieving treatment (400°C-1 h). The results are discussed in terms of the processes of grain refinement through USSP.
Journal of Nuclear Materials, Aug 1, 2016
Ratcheting strain accumulation occurred due to asymmetric cyclic loading. Accumulation of ratchet... more Ratcheting strain accumulation occurred due to asymmetric cyclic loading. Accumulation of ratcheting strain increased with mean stress and stress amplitude. Ratcheting strain accumulation decreased with increase in stress rate. With increase in mean stress and stress amplitude there was reduction in fatigue life. Fatigue life is improved with increase in stress rate.

Ultrasonics, 2019
This investigation was carried out following our earlier work on the effect of ultrasonic shot pe... more This investigation was carried out following our earlier work on the effect of ultrasonic shot peening (USSP) on corrosion resistance of the 7075 aluminium alloy in 3.5wt% NaCl solution to optimize the duration of USSP. The un-USSP treated and different USSP treated samples were subjected to potentiodynamic polarization and electrochemical impedance spectroscopy. Among the specimens USSP treated from 5 to 30 seconds, the one USSP treated for 15 seconds (USSP 15) was found to exhibit highest corrosion potential (E corr) and lowest corrosion current density (i corr). Corrosion products were characterized by Scanning Electron Microscopy (SEM) and Xray Photoelectron Spectroscopy (XPS). Scanning Kelvin Probe Force Microscopy (SKPFM) was used to measure the surface free potential. The enhanced corrosion resistance of the USSP 15 sample was found to be due to combined effect of surface nanostructure of the matrix, homogeneity and refinement of second phase precipitates. There was enhancement in formation of adherent passive layer in the USSP15 specimen.

Surface & Coatings Technology, Dec 1, 2020
Low cycle fatigue (LCF) behavior of the AA7075 was studied in the solution treated-ultrasonic sho... more Low cycle fatigue (LCF) behavior of the AA7075 was studied in the solution treated-ultrasonic shot peened and the peak aged (ST-USSP-PA) condition and was compared with that of the peak aged and ultrasonic shot peened (PA-USSP) as well the peak aged-ultrasonic shot peened and stress relieved (PA-USSP-SR) condition, studied earlier. LCF tests were carried out under fully reversed axial strain control at different total strain amplitudes (Δε t /2) from ± 0.38% to ± 0.60%. LCF life was highest in the ST-USSP-PA followed by the PA-USSP and PA-USSP-SR conditions. It was found that nanostructure of comparable size (~22 nm) was developed up to a depth of~50 μm in all the three conditions, however, there was much variation in the type, size, distribution and number density of the metastable of η precipitates in the three conditions. While the size of the strengthening precipitates η′ was~20 nm in the ST-USSP-PA, it was much smaller (~10 nm) in the other two conditions. High resolution TEM examination revealed high density of dislocations in the matrix and also within the equilibrium η precipitates in the PA-USSP condition whereas dislocations were not observed in η precipitates of the PA-USSP-SR and ST-USSP-PA conditions. Highest fatigue life in the ST-USSP-PA condition is attributed to more homogeneous distribution, larger size and higher volume fraction of the strengthening precipitates η′ and consequent increase in the resistance against fatigue crack initiation.

Materials Characterization, May 1, 2019
A nanostructured surface layer with average grain size of about 25 nm was developed through ultra... more A nanostructured surface layer with average grain size of about 25 nm was developed through ultrasonic shot peening (USSP) on the peak aged and retrogressed aluminium alloy 7075 (AA7075). Thermal stability and other features such as precipitation of hardening particles, grain growth kinetics and microstructural evolution of the nanostructured surface were investigated using XRD and TEM, following annealing at different temperatures from 150°C to 350°C. Small peaks of MgZn 2 precipitates were observed in the as USSP treated condition and also after annealing at 150°C for 30 min. The intensity of these peaks was increased from annealing at 200°C and the size of precipitates was increased. The nanograins formed from the USSP treatment were thermally stable up to 200°C, recrystallized at 250°C and started coarsening at 300°C, however, the grain size following annealing even at 350°C was < 500 nm. Quantitative evaluation of the different strengthening processes showed that grain boundary strengthening as per the Hall-Petch relationship and dislocation induced hardening based on the Bailey-Hirsch relationship were the dominant mechanisms of strengthening.
Materials Letters, Nov 1, 2023
Materials today communications, Jun 1, 2023

Journal of Materials Research
The present work deals with powder metallurgical processing of AA 6082 Al matrix composite reinfo... more The present work deals with powder metallurgical processing of AA 6082 Al matrix composite reinforced with non-equiatomic AlSiCrMnFeNiCu high-entropy alloy (HEA). The structure, microstructure, morphology, and phase composition of these Al-HEA nanocomposite powders were discerned through XRD and TEM, SEM–EDS, respectively. The AlSiCrMnFeNiCu HEA used as reinforcement was found to have a two-phase microstructure with a major and minor fraction corresponding to the B2-type (a = 0.29 nm; cP2) and Cr5Si3-type (a = b = 0.9165 nm, c = 0.4638 nm; tI32) phases, respectively. Mechanical milling (MM) imparts significant refinement, and nanostructuring of grains (~ 10–12 nm) for Al-HEA for nanocomposite powder was observed. These powders of Al-HEA was found to be thermally stable up to 650 ℃. Further, these Al-HEA nanocomposite powders were consolidated through pressure-less sintering at 560 ℃, which led to the formation of a thin ~ 400–500 nm transitional layer at the interface. The microhard...

International Journal of Fatigue, 2017
Ultrasonic Shot Peening (USSP) is a novel process of refinement of surface grain to nanoscale and... more Ultrasonic Shot Peening (USSP) is a novel process of refinement of surface grain to nanoscale and inducing compressive residual stress in surface region of metallic materials. The effect of USSP is studied on microstructure and low cycle fatigue (LCF) behavior of peak aged 7075 aluminium alloy, in the present investigation. The microstructure in surface region of the USSPed specimens is found nanostructured. Phase stability, crystallite size, and lattice strain resulting from USSP are analyzed by X-ray diffraction (XRD). The effect of surface roughness and the compressive residual stress induced by USSP is examined on LCF behavior of the material. Enhancement in LCF life is observed by USSP treatment up to the duration of 180 seconds, however, fatigue life is reduced from longer duration of USSP for 300 seconds. The enhancement in LCF life is from combined effects of the surface nanostructure and the associated compressive residual stresses.
IOP Conference Series: Materials Science and Engineering, 2017
The effect of ultrasonic shot peening (USSP) on low cycle fatigue (LCF) behavior of the 7075 alum... more The effect of ultrasonic shot peening (USSP) on low cycle fatigue (LCF) behavior of the 7075 aluminium alloy was studied at room temperature. There was grain refinement approximately to 20 nm size, appreciable increase in micro hardness, and inducement of residual compressive stress in the surface region, due to the USSP treatment. The modified microstructure in surface region of the specimens subjected to USSP was characterized by Xray diffraction and transmission electron microscopy. There was marked increase in LCF life of the specimens due to USSP, however, LCF life of the USSP specimens was reduced due to subsequent treatment of stress relieving. The results are discussed in terms of the process of crack initiation and propagation in the different conditions.
IOP Conference Series: Materials Science and Engineering, 2014
View the article online for updates and enhancements. Related content Fatigue properties of a bio... more View the article online for updates and enhancements. Related content Fatigue properties of a biomedical 316L steel processed by surface mechanical attrition Z Sun, M Chemkhi, P Kanoute et al.
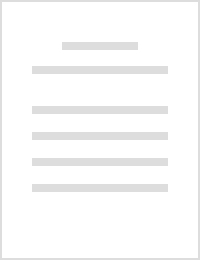
Surface and Coatings Technology, 2015
Abstract LASER shock peening (LSP) is an effective process of surface modification. This work is ... more Abstract LASER shock peening (LSP) is an effective process of surface modification. This work is concerned with the effect of LSP on the modification of microstructure, hardness, microhardness profile, residual stress, tensile properties and corrosion behavior of interstitial free (IF) steel. In order to study the effect of pulse energy on hardness, samples were subjected to LSP at pulse energy of 170, 230, 290 and 340 mJ respectively. The effect of LSP time on hardness, microhardness profile and tensile properties was investigated by processing the samples for 5, 10, 15 and 20 min at pulse energy of 230 mJ and there was found to be significant increase in tensile strength. There was grain refinement to nano level in the surface region due to LSP. Hardness was observed to increase by LSP up to 10 min and tensile strength increased up to LSP of 5 min. However with the increase in LSP time beyond 10 min there was prominent ablation and melting. The effect of overlapped (OV) LASER shocks was also studied by comparing their behavior with that of single shock. The potentiodynamic polarization study showed significant increase in corrosion resistance of the LSPed IF steel.
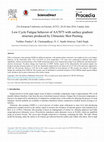
Procedia Structural Integrity, 2016
During their operation, modern aircraft engine components are subjected to increasingly demanding... more During their operation, modern aircraft engine components are subjected to increasingly demanding operating conditions, especially the high pressure turbine (HPT) blades. Such conditions cause these parts to undergo different types of time-dependent degradation, one of which is creep. A model using the finite element method (FEM) was developed, in order to be able to predict the creep behaviour of HPT blades. Flight data records (FDR) for a specific aircraft, provided by a commercial aviation company, were used to obtain thermal and mechanical data for three different flight cycles. In order to create the 3D model needed for the FEM analysis, a HPT blade scrap was scanned, and its chemical composition and material properties were obtained. The data that was gathered was fed into the FEM model and different simulations were run, first with a simplified 3D rectangular block shape, in order to better establish the model, and then with the real 3D mesh obtained from the blade scrap. The overall expected behaviour in terms of displacement was observed, in particular at the trailing edge of the blade. Therefore such a model can be useful in the goal of predicting turbine blade life, given a set of FDR data.
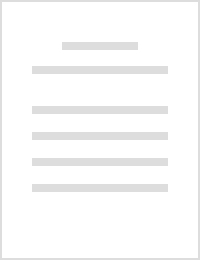
Materials Science and Engineering: A, 2015
Abstract Effect of ultrasonic shot peening (USSP) on microstructure and low cycle fatigue behavio... more Abstract Effect of ultrasonic shot peening (USSP) on microstructure and low cycle fatigue behavior of the aluminium alloy 2014 and in general in age hardened condition was studied at room temperature. No phase change was observed due to USSP. The grains of the ultrasonic shot peened (USSPed) region were refined to nanosize (~30 nm). Microhardness of the USSPed surface was increased by 45% from shot peening for 15 min. Compressive residual stress of 550 MPa was maximum at the surface of the USSPed specimens. Ultrasonic shot peening was found to enhance the low cycle fatigue as well as high cycle fatigue life. LCF life of the USSPed specimens was further increased by the subsequent stress relieving treatment at 150 °C for 2 h, in particular at low strain amplitudes. The results are discussed in terms of increased resistance against fatigue crack initiation.

Journal of Alloys and Compounds, 2017
This investigation addresses the effect of surface nanostructure developed through ultrasonic sho... more This investigation addresses the effect of surface nanostructure developed through ultrasonic shot peening (USSP) on corrosion behavior of 7075 aluminum alloy. USSP develops surface nanostructure, induces severe plastic deformation, refines grain size up to certain depth and imparts compressive residual stress in the surface region. The sample USSPed for 15 seconds (USSP 15) exhibited lower current density (0.564 μA/cm 2) and higher corrosion potential (-0.695 V) as compared with that of the un-USSP specimen with 1.269 μA/cm 2 and-0.839 V respectively. The enhancement in corrosion resistance of USSPed sample is due to rapid development of uniform, homogeneous and effective passive layer on the nano-structured surface coupled with refinement of the coarse precipitates. Also, there is optimum combination of surface roughness, compressive residual stress, and dislocation density in the surface region to produce highest corrosion resistance in the USSP 15 condition.
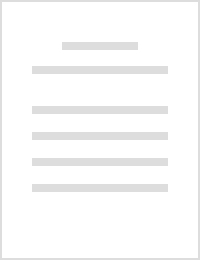
Materials Science and Engineering A-structural Materials Properties Microstructure and Processing, May 1, 2014
ABSTRACT Serrated plastic flow was observed in cyclic stress–strain hysteresis loops both in tens... more ABSTRACT Serrated plastic flow was observed in cyclic stress–strain hysteresis loops both in tensile and in compressive components during strain controlled low cycle fatigue of annealed Zircaloy-2 at a strain rate of 10−4 s−1 and different strain amplitudes, at room temperature. Although there were only D-type serrations at higher strain amplitudes (&gt;±0.75%) there were mixed serrations of D, A, B and C type at lower strain amplitudes (≤±0.75%). Depending on the cyclic stress response, transitions in dislocation structure from dislocation pile-ups to cell structure and cells to Corduroy structure were observed in the region of softening and secondary hardening. Disappearance and reappearance of serrated flow in the hysteresis loops were observed with number of cycles and it was proposed to be associated with transition in dislocation structure from planar to cell walls and finally from cell wall to Corduroy structure.
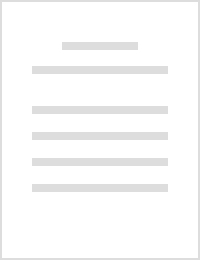
Transactions of the Indian Institute of Metals, 2021
Composite powders of pre-alloyed 316 L austenitic stainless steel with yttria (Y2O3) powder in va... more Composite powders of pre-alloyed 316 L austenitic stainless steel with yttria (Y2O3) powder in various compositions (0.3, 1.0, 1.5 and 2 wt%) were synthesized by mechanical alloying using a high energy ball mill. The 25-h milled powder has shown no changes other than exhibiting an austenite phase of FCC (a = 3.54 Å) structure. Milled powders were found to contain nano-yttria dispersed in the austenitic stainless steel matrix of nano-crystallite size and with high lattice strain. Milled powders were cold pressed and sintered at 1100 °C (1373 K) in a controlled atmosphere. It can be inferred that nano-yttria dispersion restricts grain growth of matrix even during conventional sintering. The present yittria dispersed austenitic alloy showed the low physical density and increase in compressive strength (194–374 MPa) and hardness (477–528 HV). The compressive strength and hardness enhancement can be attributed primarily to the dispersoids of nano-yttria in the austenitic matrix by dispersion strengthening/hardening mechanisms.

Materials Today: Proceedings, 2018
Nickel-ferrous based superalloy IN718 is used in gas turbine engine as compressor disk and blade.... more Nickel-ferrous based superalloy IN718 is used in gas turbine engine as compressor disk and blade. The performance of these components is severely affected in marine environment. This investigation deals with NaCl salt induced corrosion of the superalloy IN718 at 600 o C. NaCl was deposited on the sample using spray gun technique. The uncoated and NaCl coated samples were exposed in air at 600°C under cyclic heating and cooling for 100hrs. Various characterization techniques such as XRD, SEM and EDS were used to identify the oxidation and corrosion products. It was observed from the XRD and SEM/EDS analysis that the uncoated sample did not oxidize at 600°C, however, the NaCl coated sample was heavily corroded and various complex oxides were observed on the sample. Weight gain/loss measurements were made to determine the corrosion kinetics. The coating of NaCl was found to be highly detrimental for corrosion resistance of this alloy.
Uploads
Papers by Kausik Chattopadhyay