Papers by Janny Lindemann

Intermetallics, 2021
Lightweight intermetallic γ-TiAl based alloys are innovative high-temperature structural material... more Lightweight intermetallic γ-TiAl based alloys are innovative high-temperature structural materials. So far, these alloys are in use as turbine blades or turbocharger turbine wheels in advanced aerospace and automotive engines, where they are produced by means of investment casting as well as wrought processing, e.g. hot-forging. Through the development of powder-based additive manufacturing processes within the last decade, a real paradigm shift for future component production as well as their design and materials properties was created. While so-called proven alloy systems are presently used worldwide for additive manufacturing, the approach of this work is the development of novel process-adapted γ-TiAl based alloys, which on the one hand fulfill the specific requirements of additive manufacturing and on the other hand provide excellent high temperature properties after a suitable heat treatment. Based on the concept of an engineering γ-TiAl based alloy, i.e. the socalled TNM alloy, two alloys are presented. Due to the chemical reactivity of titanium aluminide alloys, electron beam melting processes come into consideration as production methods using optimized manufacturing parameters, providing dense components with only small variations in the Al content between the individual powder layers, which is a decisive factor for the subsequent heat treatment above the γ solvus temperature. The additively produced samples show a fine equiaxed microstructure, whereas the heat-treated samples exhibit a fully lamellar α₂/γ microstructure with an excellent creep resistance. In summary, the adaptation of the additive manufacturing parameters in combination with innovative alloys and subsequent heat treatments are the basis for producing reliable high-performance TiAl components in the near future.

Materials, 2020
Requirements and strict regulations for high-performance racing applications involve the use of n... more Requirements and strict regulations for high-performance racing applications involve the use of new and innovative lightweight structural materials. Therefore, intermetallic γ-TiAl-based alloys enable new opportunities in the field due to their lower density compared to commonly used Ni-base superalloys. In this study, a β-solidifying TiAl alloy was examined toward its use as structural material for inlet and outlet valves. The nominal composition of the investigated TNM alloy is Ti–43.5Al–4Nb–1Mo–0.1B (in at%), which enables an excellent formability at elevated temperatures due to the presence of bcc β-phase. Different hot-extrusion tests on an industrial scale were conducted on the cast and hot isostatic pressed material to determine the ideal microstructure for the respective racing application. To simulate these operation conditions, hot tensile tests, as well as rotational bending tests, at room temperature were conducted. With a higher degree of deformation, an increasing stre...
Materials Science and Engineering: A, 2020
Practical Metallography, 2018

Materials, 2019
Intermetallic γ-TiAl based alloys are innovative lightweight structural high-temperature material... more Intermetallic γ-TiAl based alloys are innovative lightweight structural high-temperature materials used in aerospace and automotive applications due to already established industrial-scale processing routes, like casting and hot-working, i.e., forging. A promising alternative method of production, regarding manufacturing of near net-shape components, goes over the powder metallurgy route, more precisely by densification of TiAl powder via spark plasma sintering. In this study, gas atomized powder from the 4th generation TNM alloy, Ti-43.5Al-4Nb-1Mo-0.1B (in at.%), was densified and the microstructure was investigated by means of electron microscopy and X-ray diffraction. The sintered microstructure exhibits lamellar α2-Ti3Al /γ-TiAl colonies surrounded by globular γ- and ordered βo-TiAl phase. The coarse lamellar spacing stems from the low cooling rate after densification at sintering temperature. Against this background, subsequent heat treatments were designed to decrease the lame...
Scripta Materialia, 2005
Roller burnishing improves the high cycle fatigue performance of AZ80. An improvement of 110% in ... more Roller burnishing improves the high cycle fatigue performance of AZ80. An improvement of 110% in the fatigue strength is achieved at the optimum condition. Roller burnishing is more effective than shot peening in enhancing the fatigue life of AZ80.
Materials Science and Engineering: A, 2016
Abstract A composite material consisting of a Ti-6Al-4V matrix and 10 wt% and 20 wt% TiAl particl... more Abstract A composite material consisting of a Ti-6Al-4V matrix and 10 wt% and 20 wt% TiAl particles respectively, was synthesized by Spark Plasma Sintering (SPS). The microstructure and mechanical properties of both composite conditions are investigated and compared with those of the unreinforced matrix material. Tensile properties are analyzed in the temperature range from room temperature to 550 °C. Due to the particle reinforcement, the ultimate tensile strength increases in the temperature range between 300 °C and 550 °C significantly. The results prove the potential of TiAl particle reinforced titanium alloys as light weight material in the temperature range between 450 and 650 °C.
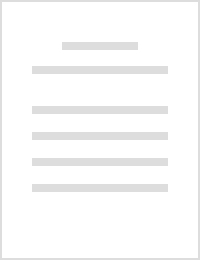
BHM Berg- und Hüttenmännische Monatshefte, 2014
ABSTRACT In the present study, the high-temperature deformation behavior of a cast and subsequent... more ABSTRACT In the present study, the high-temperature deformation behavior of a cast and subsequently hot-isostatic pressed (HIPed) b-solidifying γ-TiAl-based alloy with a nominal composition of Ti-43.5Al-4Nb-1Mo-0.1B (in at.%), termed TNM alloy, is investigated. Isothermal compression tests on cylindrical specimens are carried out on a Gleeble 3500 simulator in order to investigate the dynamic recrystallization processes in the three-phase field region (α/α2+b/b0+γ−phase field) of the TNM alloy. The deformed microstructure along with the dynamically recrystallized grain size during hot deformation is examined by scanning electron microscopy (SEM). Two phenomenological-type constitutive models are presented and compared to experimental flow stress data. Zusammenfassung In der vorliegenden Arbeit wird das Hochtemperatur-Verformungsverhalten einer gegossenen und anschließend heiß-isostatisch gepressten (geHIPten) b-erstarrenden γ-TiAl Legierung, mit einer nominellen Zusammensetzung von Ti-43.5Al-4Nb-1Mo-0.1B (in at.%), der sogenannten TNM-Legierung, untersucht. Isotherme Druckversuche an Zylinderproben erfolgen an einem Gleeble 3500 Simulator, um die dynamischen Rekristallisationsprozesse im drei-Phasengebiet (α/α2+b/b0+γ−Phasengebiet) der TNM-Legierung zu untersuchen. Die verformte Mikrostruktur wird zusammen mit der sich während der Warmumformung einstellenden dynamisch rekristallisierten Korngröße mittels Rasterelektronenmikroskopie (REM) untersucht. Zwei phänomenologische Konstitutivmodelle werden vorgestellt und mit den experimentell ermittelten Fließkurvendaten verglichen.
Materials Science and Engineering: A, 2014
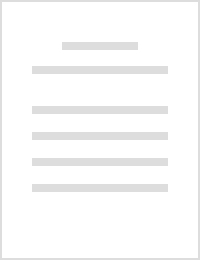
Advanced Materials Research, 2014
In the present study the high-temperature deformation behavior of a caste and subsequently HIPed ... more In the present study the high-temperature deformation behavior of a caste and subsequently HIPed β-solidifying γ-TiAl-based alloy with a nominal composition of Ti-43.5Al-4Nb-1Mo-0.1B (in at. %), termed TNM alloy, is investigated. At room temperature this alloy consists of ordered γ-TiAl, α2-Ti3Al and βo-TiAl phases. By increasing the temperature, α2 and βo disorder to α and β, respectively. In order to get a better understanding of dynamic recovery and recrystallization processes during thermomechanical processing, isothermal compression tests on TNM specimens are carried out on a Gleeble®3500 simulator. These tests are conducted at temperatures ranging from 1100 °C to 1250 °C (in the α/α2+β/βo+γ phase field region) applying strain rates in the range of 0.005 s-1 to 0.5 s-1 up to a true strain of 0.9. The evolution of microstructure along with the dynamically recrystallized grain size during hot deformation is examined by scanning electron microscopy (SEM). The flow softening behavi...
Practical Metallography, 2015
In this contribution, the microstructure of two intermetallic γ-TiAl-based alloys with different ... more In this contribution, the microstructure of two intermetallic γ-TiAl-based alloys with different Al contents were examined after high-temperature deformation. To investigate the dynamic recrystallization of these alloys, isothermal compression tests were performed using a Gleeble® 3500 simulator. For the experiments, a temperature range of 1 150 °C to 1 300 °C and strain rates of 0.005 s−1, 0.05 s−1 and 0.5 s−1 were applied, up to a true strain of 0.9. The deformed microstructural states, particularly the multiphase alloys' dynamically recrystallized grain sizes were characterized via Scanning Electronic Microscopy (SEM) and Electron Back Scatter Diffraction (EBSD). The recrystallized grain sizes obtained from the experiments could be linked with the calculated Zener-Hollomon parameter through a power law.
WAGNER:SHOT PEENING O-BK, 2006
Janny ~indemann'), Rlm ~r o s s m a n n~) , Thomas ~a c z e k ') and Lothar wagnerl)
Uploads
Papers by Janny Lindemann