Papers by Homer Rahnejat
Encyclopedia of Automotive Engineering, 2014
Volume 6: ASME Power Transmission and Gearing Conference; 3rd International Conference on Micro- and Nanosystems; 11th International Conference on Advanced Vehicle and Tire Technologies, 2009
ABSTRACT
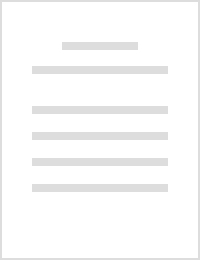
ASME 2012 Internal Combustion Engine Division Spring Technical Conference, 2012
ABSTRACT Both the piston ring and cylinder bore experience wear throughout their life cycle. Ther... more ABSTRACT Both the piston ring and cylinder bore experience wear throughout their life cycle. Therefore change occurs in the geometrical profile and topography of the ring. In addition, coating on the ring is also subject to wear, thus altering the physical/mechanical property of the contacting surface. These changes affect the tribological performance of the ring-bore conjunction. Geometrical changes often alter the ring contacting profile, which affects the entrainment of the lubricant into the conjunction. This can affect the regime of lubrication, thus mechanisms that contribute to friction. Wear of surfaces also plays some role in boundary friction in terms of topographical changes as well as surface properties such as hardness and asperity shear strength. Most analysis does not take into account changes in tribological conditions which occur as the result of these salient changes in practice. The paper intends to bridge this gap in the fundamental knowledge and provide explanations for some in-field experiences noted with wear of a compression ring in a typical engine test. The method of solution used is based on the average flow factors which are indicative of entrainment of the lubricant through the rough ring-bore conjunction. This approach was initiated by Patir and Cheng, for which realistic topographical parameters according to the stage of the wear process is included. Changes in friction and fuel energy consumed are predicted.
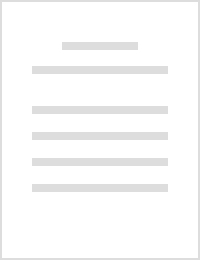
ASME/STLE 2012 International Joint Tribology Conference, 2012
ABSTRACT Engineering surfaces are never perfectly flat. They contain micro and nano-scale feature... more ABSTRACT Engineering surfaces are never perfectly flat. They contain micro and nano-scale features on multiple length scales. Predicting the amount of fluid trapped in these minute surface crevices and its controlled release could benefit a variety of practical applications. In a sliding contact, the released fluid could create an ultra-thin film, reducing the direct contact and consequently the boundary friction. Transdermal patches are the least invasive of available subcutaneous drug delivery techniques. The drug is stored in a micro-reservoir and it is released to the skin either through a permeable membrane or through a series of micro needles.The aim of the current paper represents the first attempt to investigate whether a modeling approach encompassing two complementary simulation techniques in an integrated framework can be used to predict the volume of fluid stored in a nano-scale surface feature. Molecular dynamics (MD) simulation could provide accurate modeling of fluid behavior at nano-scale, and statistical mechanics (SM) could provide a fast prediction.
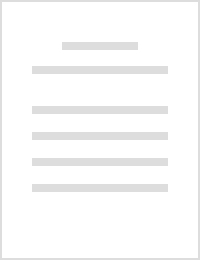
International Gear Conference 2014: 26th–28th August 2014, Lyon, 2014
ABSTRACT Differential hypoid gears play an important role on the Noise, Vibration and Harshness (... more ABSTRACT Differential hypoid gears play an important role on the Noise, Vibration and Harshness (NVH) signature of vehicles. Additionally, friction developed between their teeth flanks under extreme loading conditions adds another source of power loss in the drivetrain which can mitigate vibrational energy. The paper considers the coupling between dynamics and analytical tribology to study dynamic response of hypoid gear pairs with lateral motion of support shafts also included in the analysis framework. Friction of teeth flank pairs is assumed to follow elastohydrodynamic lubrication under elliptical point contact geometry with lubricant film behavior conforming to Non-Newtonian thermal shear, also with surface asperity interactions. Tooth Contact Analysis (TCA) has been used to obtain the input data required for the investigation. The dynamic behavior and efficiency of a differential hypoid gear pair under realistic operating conditions is determined. The proposed tribo-dynamic framework provides a useful platform to conduct an extensive series of parametric studies.
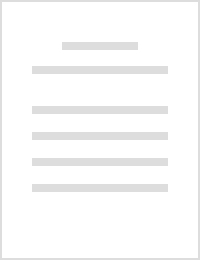
SAE Technical Paper Series, 2014
ABSTRACT The automotive industry is subject to increasing pressure to reduce the CO2 emissions an... more ABSTRACT The automotive industry is subject to increasing pressure to reduce the CO2 emissions and improve fuel efficiency in internal combustion engines. Improvements may be achieved in a number of ways. The parasitic losses throughout the engine cycle emanate from friction in all engine contact conjunctions in addition to pumping losses. In particular one main contributory conjunction is the piston ring pack assembly. At low engine speeds, the contribution of friction to the total losses within the engine is increased significantly compared with the thermodynamic losses. Additionally, the sealing capability of the ring is crucial in determining the power output of the engine with any loss of sealing contributing to power loss, as well as blowby. Most reported studies on compression ring-cylinder conjunction do not take into account complex ring in-plane and out-of-plane elastodynamics. Hitherto, there has not been a numerical methodology which integrates tribology of an elastic compression ring, subject to modal behaviour in a coupled solution. This paper discusses the inclusion of transient ring elastodynamics of the top compression ring, interacting with blowby effects within the ring pack. The ring dynamics methodology is briefly highlighted for both in-plane and out-of-plane motions. In addition, a one-dimensional gas flow model that captures blowby behaviour is included. A case study is presented, using measured engine data. Gas flow and frictional losses at various engine speeds are predicted. The effect of gas blowby on the ring's tribological response can be ascertained, as well as the ring's dynamic motion within its retaining groove.
Volume 7A: Fluids Engineering Systems and Technologies, 2013
ABSTRACT The main function of piston compression ring is to seal the space between the piston and... more ABSTRACT The main function of piston compression ring is to seal the space between the piston and the liner, acting as slider bearing, subjected to reciprocating motion. The compression ring-cylinder liner conjunction has been extensively studied and it is responsible for a significant part of the total frictional parasitic power losses of an engine. Paradoxically, the required sealing function of the compressions ring can result in increased friction. Therefore, in order to improve engine efficiency, it is important to fundamentally understand and subsequently palliate some of these losses. Another problem in any slider bearing-type contact is lubricant film rupture and cavitation in the conjunctional outlet zone, reducing load carrying capacity and potentially leading to erosion damage.
STLE/ASME 2008 International Joint Tribology Conference, 2008
ABSTRACT
Vehicle System Dynamics, 2005
... frictional properties GEORGE MAVROS*, HOMER RAHNEJAT and PAUL KING Loughborough University, L... more ... frictional properties GEORGE MAVROS*, HOMER RAHNEJAT and PAUL KING Loughborough University, Loughborough, UK The ... of freedom. The well-known Kelvin element is used for the representation of bristle viscoelasticity. This ...
Journal Papers by Homer Rahnejat

The piston ring/cylinder liner conjunction can experience various regimes of lubrication during p... more The piston ring/cylinder liner conjunction can experience various regimes of lubrication during piston strokes inside the engine cylinder. In the current engines, the nature of lubrication usually remains hydrodynamic at mid-stroke, while a mixed regime of lubrication may be experienced at and near reversals. The direct contact between the tips of some of the asperities of opposing surfaces leads to mixed (partial) regime of lubrication. A model proposed by Greenwood and Tripp can be used to predict asperity-level contribution to the total piston friction. At the same time, Reynolds equation can be employed to predict the portion of load carried by the lubricant trapped between the asperities. Friction between the asperity tips is usually proportional to the load that they support, stated in terms of a proportionality factor, that is, coefficient of friction. The surfaces are usually furnished with hard wear-resistant coatings and in parts by solid lubricants. Both the piston rings and cylinder liner surfaces are usually coated. These coatings change the friction characteristics of the counterfaces because of their surface topography as well as material mechanical properties. Atomic force microscope is used to obtain surface topographical parameters in contact tapping mode. The corresponding surface topographical parameters are obtained from representative regional areas of the contacting solid surfaces, using a Talysurf. The combination of topography and coating characteristics are used to develop the necessary parameters for a boundary friction model. A numerical model of the top compression ring to cylinder liner is developed based on mixed-hydrodynamic regime of lubrication. The results for friction and the effect of coating on the power loss and wear of the conjunction are discussed in this article.
Prediction of load capacity and friction depend on the assumed boundary conditions. The inlet com... more Prediction of load capacity and friction depend on the assumed boundary conditions. The inlet comprises swirl and counter flows, admitting only a portion of the inward flow into the conjunctional gap. At the contact exit, the lubricant film ruptures with multi-phase flow through a cavitation region. Therefore, the boundary conditions affect the load carrying capacity and friction. A Navier-Stokes solution of multi-phase flow, including vapour transport is presented, with determined realistic boundary conditions.
On the boundary conditions in multi-phase flow through the piston ring-cylinder liner conjunction. Available from: https://www.researchgate.net/publication/276164062_On_the_boundary_conditions_in_multi-phase_flow_through_the_piston_ring-cylinder_liner_conjunction [accessed May 18, 2015].
Uploads
Papers by Homer Rahnejat
Journal Papers by Homer Rahnejat
On the boundary conditions in multi-phase flow through the piston ring-cylinder liner conjunction. Available from: https://www.researchgate.net/publication/276164062_On_the_boundary_conditions_in_multi-phase_flow_through_the_piston_ring-cylinder_liner_conjunction [accessed May 18, 2015].
On the boundary conditions in multi-phase flow through the piston ring-cylinder liner conjunction. Available from: https://www.researchgate.net/publication/276164062_On_the_boundary_conditions_in_multi-phase_flow_through_the_piston_ring-cylinder_liner_conjunction [accessed May 18, 2015].