Journal Papers by Navid Bahrani, PhD, PEng
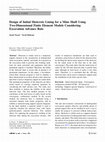
Geotechnical and Geological Engineering, 2021
Shotcrete is widely used as a temporary support element in the construction of underground mine e... more Shotcrete is widely used as a temporary support element in the construction of underground mine excavations, tunnels, and shafts. It is sprayed on the excavation walls to provide safe working conditions for mine personnel and equipment until the permanent support is installed. Therefore, the ability of the shotcrete liner to resists falls of ground is of paramount importance. In this paper, a two-dimensional finite element program is used to simulate a three-dimensional excavation advance and a shotcrete liner that is used as temporary support in a mine shaft. The mechanical properties of the shotcrete are determined based on existing empirical equations by considering the shaft advance rate. The study uses three methods to analyze the stability of the initial shotcrete liner. The first method pertains to the calculation of the load factor of safety based on the convergence confinement method. In the second method, the shotcrete liner is simulated using a structural element with elastic properties, and its stability is analyzed using support capacity diagrams. In the third method, a material model is used to explicitly simulate the shotcrete liner with elastic perfectly-plastic material behavior. This method allows for capturing the progressive yielding of the shotcrete liner during the excavation advance. The results of numerical simulations are then used to calculate a strain factor of safety for the shotcrete liner by dividing the lateral strain capacity of the shotcrete by the radial strain of the liner due to the shaft convergence. The study infers that the strain factor of safety for the 100 mm shotcrete liner is greater than unity although its load factor of safety is less than unity. Therefore, it is concluded that the 100 mm shotcrete liner can be used as temporary support until the installation of the final concrete liner.

Computers and Geotechnics, 2021
The discontinuum numerical modeling approaches widely used to simulate brittle rock failure emplo... more The discontinuum numerical modeling approaches widely used to simulate brittle rock failure employ the Voronoi tessellation technique to generate polygonal grain-like structures. Using this approach, called the grainbased model (GBM), the progressive micro-cracking leading to macroscopic fracturing and failure of brittle rocks can be realistically simulated. In this paper, a GBM is developed using the continuum numerical program RS2 to reproduce the laboratory behavior of intact and heat-treated (granulated) Wombeyan marble. An iterative calibration procedure is utilized to match the macro-properties of RS2-GBM to those of marble. It is found that RS2-GBM captures some of the most important characteristics of brittle rocks, including the non-linear strength envelope and the change in the failure mode and post-peak response with increasing confinement. It is demonstrated that the peak strength and failure mode of RS2-GBM are comparable to those of previously calibrated discontinuum GBMs. The advantage of the continuum over the discontinuum GBM is its shorter computation time. It is discussed that since the granulated marble serves as an analogue for a highly interlocked jointed rock mass, its calibrated continuum GBM can be used as an alternative tool for stability analyses and design of excavations and mine pillars in jointed rock masses.
The Journal of the Southern African Institute of Mining and Metallurgy, 2020
Numerical models are widely used to demonstrate the effect of ground support in stabilizing under... more Numerical models are widely used to demonstrate the effect of ground support in stabilizing underground excavations in rock. However, limited attention has been paid to the reliability of the employed models. This is surprising given that these models are often used to make important decisions on the selection or modification of ground support. This paper focuses on the simulation of resin-grouted rebar rockbolts to illustrate the sensitivity of numerical models to the stiffness of reinforcement elements. This was illustrated by employing in-situ pull test data from underground hard-rock mines. The numerical investigation demonstrated the implications for the performance of reinforcement as a function of input parameters based on pull tests undertaken in a range of ground conditions.

Journal of Rock Mechanics and Geotechnical Engineering, 2020
The strength of jointed rock mass is strongly controlled by the degree of interlock between its c... more The strength of jointed rock mass is strongly controlled by the degree of interlock between its constituent rock blocks. The degree of interlock constrains the kinematic freedom of individual rock blocks to rotate and slide along the block forming joints. The HoekeBrown (HB) failure criterion and the geological strength index (GSI) were developed based on experiences from mine slopes and tunneling projects in moderately to poorly interlocked jointed rock masses. It has since then been demonstrated that the approach to estimate the HB strength parameters based on the GSI strength scaling equations (called the 'GSI strength equations') tends to underestimate the confined peak strength of highly interlocked jointed rock masses (i.e. GSI > 65), where the rock mass is often non-persistently jointed, and the intact rock blocks are strong and brittle. The estimation of the confined strength of such rock masses is relevant when designing mine pillars and abutments at great depths, where the confining pressure is high enough to prevent block rotation and free sliding on block boundaries. In this article, a grain-based distinct element modeling approach is used to simulate jointed rock masses of various degrees of interlock and to investigate the influences of block shape, joint persistence and joint surface condition on the confined peak strengths. The focus is on non-persistently jointed and blocky (persistently jointed) rock masses, consisting of hard and homogeneous rock blocks devoid of any strength degrading defects such as veins. The results from this investigation confirm that the GSI strength equations underestimate the confined strength of highly interlocked and non-persistently jointed rock masses. Moreover, the GSI strength equations are found to be valid to estimate the confined strength of persistently jointed rock masses with smooth and non-dilatant joint surfaces.

Canadian Geotechnical Journal, 2019
A two-dimensional numerical model based on the Distinct Element Method, previously calibrated to ... more A two-dimensional numerical model based on the Distinct Element Method, previously calibrated to the laboratory properties of undamaged and damaged Lac du Bonnet (LdB) granite, was used to investigate the influence of stress path on the development of stress memory and stress fracturing in brittle rocks. Various cycles of loading and unloading, similar to those imposed during Kaiser Effect tests, were first applied to undamaged numerical specimens of LdB granite. The results of Kaiser Effect test simulations were found to be consistent with those of published laboratory and numerical investigations. Further simulations were conducted to investigate the influence of stress path resulting from the excavation of a tunnel on the depth of stress fracturing around the excavation boundary. For this purpose, the stress paths at points on and near the tunnel wall, obtained from a continuum finite element model, were applied to the calibrated numerical specimen. It was found that the amount of damage in the numerical specimens decreases rapidly with increasing distance from the excavation wall. The findings of this research shed some light on the influence of stress path and grain-scale heterogeneity on stress memory in brittle rocks and stress fracturing around underground openings.

Rock Mechanics and Rock Engineering, 2018
Numerical modeling is an important tool in rock engineering. The choice for a particular numerica... more Numerical modeling is an important tool in rock engineering. The choice for a particular numerical method is based on its capacity to represent the problem boundary conditions, the material behavior, and the pertinent rock mass failure mechanisms. It follows that there could be more than one numerical method suitable for a particular problem. In this respect, the selection of a particular method will be dictated by a series of technical and practical trade-offs. This paper addresses issues
associated with the simulation of jointed rock masses and ground support by employing both continuum and discontinuum numerical methods. The focus is on the explicit simulation of a jointed rock mass and the implementation of ground support
using a three-dimensional numerical code based on the distinct element method. 3DEC was used to generate continuum and discontinuum rock mass models, which were calibrated based on field instrumentation data from the George Fisher mine, in
Australia. In particular, the investigation focused on the response of the ground support system, consisting of both reinforcement and surface support elements, to stress changes associated with the excavation of nearby stopes. The main difference
between the constructed continuum and discontinuum 3DEC models was the representation of the rock mass at the location of the instrumented drift. In the continuum model, an equivalent continuum rock mass model, with the ubiquitous-joint (UJ) constitutive model, was used, whereas in the discontinuum model, joints were simulated explicitly. In this case study, it was observed that the adopted discontinuum modeling approach provided more realistic results than the continuum model with
the UJ constitutive model, in terms of the drift convergence, support behavior, and depth of yielded zone due to the excavation of stopes near the instrumented section of the drift.

Journal of Rock Mechanics and Geotechnical Engineering, 2017
This paper investigates the explicit use of rock reinforcement in a discontinuous stress analysis... more This paper investigates the explicit use of rock reinforcement in a discontinuous stress analysis model. A series of numerical experiments was undertaken to evaluate the performance of local and global reinforcement models implemented in universal distinct element code (UDEC). This was made possible by calibrating the reinforcement models to the laboratory behavior of a fully-grouted rebar bolt tested under pure pull and pure shear loading conditions. The model calibration focuses on matching different loading stages of the force–displacement curve including the initial elastic response, the hardening behavior and the bolt rupture. The paper concludes with a discussion on the suitability of the different reinforcement models in UDEC including their advantages and limitations. Finally, it addresses the choice of input parameters required for a realistic simulation of fully-grouted rebar bolts.

Rock Mechanics and Rock Engineering, 2017
It is known that the unconfined compressive strength of rock decreases with increasing density of... more It is known that the unconfined compressive strength of rock decreases with increasing density of geological features such as micro-cracks, fractures, and veins both at the laboratory specimen and rock block scales. This article deals with the confined peak strength of laboratory-scale rock specimens containing grain-scale strength dominating features such as micro-cracks. A grain-based distinct element model, whereby the rock is simulated with grains that are allowed to deform and break, is used to investigate the influence of the density of cracks on the rock strength under unconfined and confined conditions. A grain-based specimen calibrated to the unconfined and confined strengths of intact and heat-treated Wombeyan marble is used to simulate rock specimens with varying crack densities. It is demonstrated how such cracks affect the peak strength, stress–strain curve and failure mode with increasing confinement. The results of numerical simulations in terms of unconfined and confined peak strengths are used to develop semi-empirical relations that relate the difference in strength between the intact and crack-damaged rocks to the confining pressure. It is shown how these relations can be used to estimate the confined peak strength of a rock with micro-cracks when the unconfined and confined strengths of the intact rock and the unconfined strength of the crack-damaged rock are known. This approach for estimating the confined strength of crack-damaged rock specimens, called strength degradation approach, is then verified by application to published laboratory triaxial test data.
Computers and Geotechnics, 2016
A grain-based distinct element model (GBM) is used to investigate the influence of specimen size ... more A grain-based distinct element model (GBM) is used to investigate the influence of specimen size on the
strength of intact (not defected) and defected rocks. The defected specimens are simulated by integrating
a previously calibrated GBM with Discrete Fracture Network models representing defect geometries.
The results of scale effect analysis conducted on synthetic specimens show that the strength of intact
specimens is independent of specimen size. However, depending on the orientation of defects relative
to the loading direction, the strength of defected specimens may decrease, increase or fluctuate with
increasing specimen size.
International Journal of Rock Mechanics and Mining Sciences, 2015

International Journal of Rock Mechanics and Mining Sciences, 2014
A grain-based distinct element model is used to reproduce the laboratory response of both intact ... more A grain-based distinct element model is used to reproduce the laboratory response of both intact and granulated Wombeyan marble. The term “granulated” refers to a heat treated marble where the cohesion of grain boundaries has been destroyed. The unconfined compressive strength of granulated marble is less than 50% of that of intact marble, while the strength of the granulated marble increases to about 80% of that of the intact marble at higher confining stresses. An iterative calibration approach is developed to match the unconfined and confined strengths of the models to those of intact and granulated marble. The simulation test results of the models of intact and granulated marble including the transition in the failure mode, stress–strain response, and the evolution of inter- and intra-grain micro-cracks with increasing confinement are discussed. The observed rapid strengthening effect, in terms of increasing confinement, is interpreted to be due to the high degree of grain assembly geometric interlock, which arises from the tight fit geometric shape of the grains as well as the roughness of the grain boundaries. It is suggested that the granulated marble can be considered to be an analogue for a highly interlocked, non-persistently jointed rockmass. It is shown that when the generalized Hoek–Brown failure criterion and the Geological Strength Index (GSI) are used to match the strength of the granulated marble at zero confinement, the confined strength of the granulated marble is under-estimated by as much as a factor of two. Therefore, the confined strength of a highly interlocked, non-persistently jointed rockmass, with strong, brittle rock blocks, could be significantly higher than that predicted by commonly adopted empirical approaches. This has practical implications for the design of highly confined pillars and abutments, which is discussed in this paper.

Rock Mechanics and Rock Engineering, 2014
A particle-based distinct element method and its grain-based method are used to generate and simu... more A particle-based distinct element method and its grain-based method are used to generate and simulate a synthetic specimen calibrated to the rupture characteristics of an intact (non-jointed) low-porosity brittle rock deformed in direct shear. The simulations are compared to the laboratory-generated ruptures and used to investigate rupture at various normal stress magnitudes. The fracturing processes leading to shear rupture zone creation and the rupture mechanism are found to be normal stress dependent (progressing from tensile splitting to shear rupture) and show partial confirmation of rupture zone creation in nature and in experiments from other materials. The normal stress dependent change is found to be due to the orientation of the major principal stress and local stress concentrations internal to the synthetic specimens being deformed. The normal stress dependent rupture creation process results in a change to the rupture zone’s geometry, shear stress versus horizontal displacement response, and thus ultimate strength.
International Journal of Rock Mechanics and Mining Sciences, 2013

International Journal of Rock Mechanics and …, Jan 1, 2011
When designing high steep footwall slopes, an accurate assessment of the dilational shear strengt... more When designing high steep footwall slopes, an accurate assessment of the dilational shear strength component is necessary. Bedding surface profiles taken from a detailed digital terrain model of a slip surface exposed by a large slab-type footwall failure were used to characterize the geometric roughness and dilation angles in the sliding direction. The dilation angles predicted from best-fit dilatancy curves are sensitive to the base distance or shear displacement. The dilation angle for a given shear displacement (or base distance) is not sensitive to the profile length if it exceeds the typical in situ block size. For the case history, a 2D finite element analysis was performed to back-calculate the effective dilation angle assuming no cohesion was present and the basic friction angle was 25°. This analysis suggested that a dilation angle of 12° was required to create a condition of incipient slab failure. Using dilatancy curve equations, it is possible to convert dilation angles back-calculated from finite element stability analyses into shear displacements required to mobilize the peak strength. The shear displacement required to mobilize a dilation angle of 12° is estimated to be 0.02–0.15 m for the slab failure that was studied. Analysis of profile geometries to estimate the shear displacement needed to reach peak shear strength will improve the interpretation of slope displacement monitoring data.

CIM Bulletin, 2009
Photogrammetry surveys were used to document a footwall slab failure that occurred at a surface c... more Photogrammetry surveys were used to document a footwall slab failure that occurred at a surface coal mine located on the eastern slope of the Rocky Mountains. Photographs taken before and after the failure provided the pre- and post-failure geometry of the slope and the failed slab. A 2D finite element model was constructed using slope profiles. The model contained joint elements that represented the bedding surface upon which the slab slid and the model was used to analyze the footwall slope. The in situ stresses, rock properties and the bedding surface shear strength and stiffness properties are discussed. The process of mining out a valley and exposing a highwall was modelled. As expected, elastic valley rebound occurred in the model, but shear stress and shear displacement reversals along the slip surface were also observed. The modelling results provided new insight into shear strength degradation that occurs when the pit floor approaches and then passes
a specific point in the highwall.
Conference Papers by Navid Bahrani, PhD, PEng
54th US Rock Mechanics/Geomechanics Symposium , 2020
This paper was selected for presentation at the symposium by an ARMA Technical Program Committee ... more This paper was selected for presentation at the symposium by an ARMA Technical Program Committee based on a technical and critical review of the paper by a minimum of two technical reviewers. The material, as presented, does not necessarily reflect any position of ARMA, its officers, or members. Electronic reproduction, distribution, or storage of any part of this paper for commercial purposes without the written consent of ARMA is prohibited. Permission to reproduce in print is restricted to an abstract of not more than 200 words; illustrations may not be copied. The abstract must contain conspicuous acknowledgement of where and by whom the paper was presented.

54th US Rock Mechanics/Geomechanics Symposium , 2020
A two-dimensional grain-based model (GBM) is developed using the finite element program RS2 to re... more A two-dimensional grain-based model (GBM) is developed using the finite element program RS2 to reproduce the laboratory behavior of intact and granulated Wombeyan marble subjected to unconfined compression. The term “granulated” refers to a heat-treated marble of which the grains have been separated at their boundaries due to the anisotropy of the thermal expansion of calcite grains. Medium regular Voronoi cells are employed in RS2-GBM to mimic the microstructure of Wombeyan marble. RS2-GBM is first calibrated to the Unconfined Compressive Strength (UCS) and the Young’s modulus (E) of intact and granulated marble. The simulation results of elastic GBMs demonstrate that the orientation of grain boundaries has a significant impact on the generation of tensile stresses within the specimen. Next, calibrated plastic models are used to better understand the fracturing processes of intact and granulated marble under unconfined compression. The granulated marble has been suggested to serve as an analogue for a highly interlocked jointed rock mass. In this regard, a highly interlocked joined pillar with a width-to-height ratio of 1 is simulated using the calibrated model of granulated marble. The simulation results of the jointed pillar suggest a higher strength and elastic modulus than those of the calibrated model of granulated marble under unconfined compression. The failure of the pillar model is initiated by the yielding of sub-vertical joints near the walls of the pillar during the early stages of pillar loading. This condition is similar to “spalling” and “slabbing” observed in the field. With further increase of the load on the pillar, block yielding initiates from the pillar walls and then propagates towards the core. The overall failure mode of the pillar model resembles the “crushed” pillars observed in hard rock mines.
5th International FLAC/DEM Symposium, 2020
5th International FLAC/DEM Symposium, 2020

Fourth Internationl Symposium on Block and Sublevel Caving, 2018
A grain-based model based on the Distinct Element Method previously calibrated to the laboratory ... more A grain-based model based on the Distinct Element Method previously calibrated to the laboratory properties of intact and heat-treated (granulated) marble is used to simulate grain-scale heterogeneities, such as grain boundary cracks, and laboratory specimen-scale heterogeneities (often referred to as defects), such as veins. The semi-empirical Strength Degradation Approach (SDA), originally developed for the estimation of the confined strength of crack-damaged rocks, is first applied and tested for the estimation of confined strength of laboratory specimen-scale rocks and rock blocks containing defects. In the second approach, called the explicit numerical modelling approach, the grain-based model is integrated with Discrete Fracture Network (DFN) models, to construct defected rock models and to investigate the influence of defect orientation on the confined strength of defected rocks. It is concluded that the SDA can be used at the early stages of geotechnical projects, when limited information on the properties and geometrical characteristics of defects is available. The explicit numerical modelling approach provides more representative results than the SDA, as it requires a detailed knowledge of the properties of intact rock as well as the properties and geometrical characteristics of defects obtained from field mapping and laboratory testing. Step-by-step procedure is provided for the application of these two methods to estimate the confined strength of defected rocks.
Uploads
Journal Papers by Navid Bahrani, PhD, PEng
associated with the simulation of jointed rock masses and ground support by employing both continuum and discontinuum numerical methods. The focus is on the explicit simulation of a jointed rock mass and the implementation of ground support
using a three-dimensional numerical code based on the distinct element method. 3DEC was used to generate continuum and discontinuum rock mass models, which were calibrated based on field instrumentation data from the George Fisher mine, in
Australia. In particular, the investigation focused on the response of the ground support system, consisting of both reinforcement and surface support elements, to stress changes associated with the excavation of nearby stopes. The main difference
between the constructed continuum and discontinuum 3DEC models was the representation of the rock mass at the location of the instrumented drift. In the continuum model, an equivalent continuum rock mass model, with the ubiquitous-joint (UJ) constitutive model, was used, whereas in the discontinuum model, joints were simulated explicitly. In this case study, it was observed that the adopted discontinuum modeling approach provided more realistic results than the continuum model with
the UJ constitutive model, in terms of the drift convergence, support behavior, and depth of yielded zone due to the excavation of stopes near the instrumented section of the drift.
strength of intact (not defected) and defected rocks. The defected specimens are simulated by integrating
a previously calibrated GBM with Discrete Fracture Network models representing defect geometries.
The results of scale effect analysis conducted on synthetic specimens show that the strength of intact
specimens is independent of specimen size. However, depending on the orientation of defects relative
to the loading direction, the strength of defected specimens may decrease, increase or fluctuate with
increasing specimen size.
a specific point in the highwall.
Conference Papers by Navid Bahrani, PhD, PEng
associated with the simulation of jointed rock masses and ground support by employing both continuum and discontinuum numerical methods. The focus is on the explicit simulation of a jointed rock mass and the implementation of ground support
using a three-dimensional numerical code based on the distinct element method. 3DEC was used to generate continuum and discontinuum rock mass models, which were calibrated based on field instrumentation data from the George Fisher mine, in
Australia. In particular, the investigation focused on the response of the ground support system, consisting of both reinforcement and surface support elements, to stress changes associated with the excavation of nearby stopes. The main difference
between the constructed continuum and discontinuum 3DEC models was the representation of the rock mass at the location of the instrumented drift. In the continuum model, an equivalent continuum rock mass model, with the ubiquitous-joint (UJ) constitutive model, was used, whereas in the discontinuum model, joints were simulated explicitly. In this case study, it was observed that the adopted discontinuum modeling approach provided more realistic results than the continuum model with
the UJ constitutive model, in terms of the drift convergence, support behavior, and depth of yielded zone due to the excavation of stopes near the instrumented section of the drift.
strength of intact (not defected) and defected rocks. The defected specimens are simulated by integrating
a previously calibrated GBM with Discrete Fracture Network models representing defect geometries.
The results of scale effect analysis conducted on synthetic specimens show that the strength of intact
specimens is independent of specimen size. However, depending on the orientation of defects relative
to the loading direction, the strength of defected specimens may decrease, increase or fluctuate with
increasing specimen size.
a specific point in the highwall.