تحليل نمط وآثار وحرجية الإخفاق
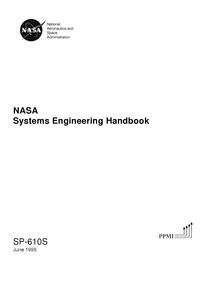
تحليل نمط وآثار وحرجية الإخفاق (بالإنجليزية: Failure mode, effects, and criticality analysis) اختصاراً: (FMECA) هي طريقة تحليل تُعتبر امتداداً لطريقة «تحليل نمط وآثار الإخفاق» (بالإنجليزية: Failure mode and effects analysis) المعروفة اختصاراً باسم (FMEA).
تحليل نمط وآثار الإخفاق FMEA هو أسلوب تحليلي استقرائي يعمل من أسفل إلى أعلى، يمكن إجراؤه إما على المستوى الوظيفي أو على المستوى الجزئي. وهو يوسِّع فكرة «تحليل نمط وآثار الإخفاق» FMEA من خلال تضمين وإضافة: «تحليل الحرجية» (بالإنجليزية: criticality analysis) الذي يُستخدم لرسم «احتمالية» أوضاع الإخْفاق (بالإنجليزية: probability) مقابل «شدة عواقبها» (بالإنجليزية: severity). تُبرز النتيجة أوضاع الإخْفاقات ذات «الاحتمالية» العالية نسبيًا و«شدة العواقب»، مما يسمح بتوجيه جهود الإصلاح إلى ما ينتج عنه أكبر قيمة مستفادة.
تحليل نمط وآثار وحرجية الإخفاق FMECA يميل إلى أن يكون مُفضلاً على تحليل نمط وآثار الإخفاق FMEA فيما يتعلق بالفضاء الخارجي والتطبيقات العسكرية الخاصة بمنظمة حلف شمال الأطلسي (الناتو)، بينما يسود تحليل نمط وآثار الإخفاق FMEA في مختلف أشكال الصناعات الأخرى.
المنهجية
[عدل]يتكون إجراء تحليل نمط وآثار وحرجية الإخفاق FMECA عادة من الخطوات المنطقية التالية:
- تحديد النظام
- تحديد القواعد والافتراضات الأساسية من أجل المساعدة على وضع التصميم
- بناء مخططات الكتلة للنظام
- تحديد أوضاع الإخْفاق (على مستوى الجزء-القطعة أو مستوى الوظيفة)
- تحليل آثار الإخْفاق / الأسباب
- تغذية النتائج مرة أخرى في عملية التصميم
- تصنيف تأثيرات الإخْفاق حسب الشدة
- أداء العمليات الحسابية لتقدير «الحرجية»
- ترتيب «وضع الإخْفاق» بحسب رتبته
- تحديد العناصر الحرجة
- تغذية النتائج مرة أخرى في عملية التصميم
- تحديد وسائل الكشف عن الإخْفاق والعزل والتعويض
- إجراء تحليل الصيانة
- توثيق التحليل، وتلخيص مجالات التصميم غير القابلة للتصحيح، وتحديد الضوابط الخاصة اللازمة للحد من مخاطر الإخْفاق
- تقديم التوصيات
- متابعة تنفيذ الإجراءات التصحيحية / والفعالية
مستوى الوظيفة ومستوى الجزء والقطعة
[عدل]قد يتم تنفيذ تحليل نمط وآثار وحرجية الإخفاق على مستوى الوظيفة أو مستوى الجزء-القطعة:
- ينظر تحليل نمط وآثار وحرجية الإخفاق «الوظيفي» في تأثيرات الإخْفاق على مستوى «الكتلة الوظيفية» (بالإنجليزية: functional block)، كمثال: مصدر الطاقة أو مكبر للصوت في جهاز الراديو.
- يأخذ تحليل نمط وآثار وحرجية الإخفاق «للجزء والقطعة» بعين الاعتبار تأثيرات إخْفاق المكون الفردي، مثل المقاومات أو الترانزستورات أو الدوائر الدقيقة أو الصمامات في جهاز الراديو مثلا.
يتطلب تحليل نمط وآثار وحرجية الإخفاق على مستوى «الجزء-القطعة» بذل المزيد من الجهد، لكنه يوفر الاستفادة من تقديرات أفضل لاحتمالات حدوثها. أما تحليل نمط وآثار وحرجية الإخفاق «الوظيفي» فيمكن إجرائه مبكراً بكثير في وقت أسرع، وقد يساعد في هيكلة تقييم المخاطر بشكل أفضل وتوفير نوع آخر من البصيرة في خيارات تخفيف الأثر.
قد يكون تحليل الأهمية كميًا أو نوعيًا، وذلك اعتمادًا على توفر بيانات إخْفاق الجزء الداعمة.
تعريف النظام
[عدل]في هذه الخطوة، يتم تعريف النظام الرئيسي المطلوب تحليله وتقسيمه إلى تسلسل هرمي مثل الأنظمة أو الأنظمة الفرعية أو المعدات أو الوحدات أو المجموعات الفرعية وأجزاء القطعة. يتم إنشاء أوصاف وظيفية للأنظمة وتخصيصها للأنظمة الفرعية، والتي تغطي جميع أوضاع التشغيل ومراحل المهمة المطلوبة.
القواعد الأساسية والافتراضات
[عدل]قبل إجراء تحليل مفصل، يتم عادةً تحديد القواعد والافتراضات الأساسية والموافقة عليها. قد يشمل ذلك على سبيل المثال:
- وضع تعريف «عيارى موحد القياس» للمهمة مع تحديد قيم زمنية لكل مرحلة من مراحل المهمة
- مصادر «معدلات الإخْفاق» وبيانات «وضعية الإخْفاق»
- طريقة اكتشاف الأخطاء التي سيحققها النظام المدمج في الاختبار
- ما إذا كان التحليل سيكون وظيفيًا أم جزئيًا
- المعايير الواجب مراعاتها (إحباط المهمة، السلامة، الصيانة، إلخ)
- وضع نظام لتحديد الأجزاء أو الوظائف
- تعاريف فئات الخطورة
بعد ذلك يتم توصيف الأنظمة والأنظمة الفرعية بواسطة «مخططات الكتل الوظيفية» (بالإنجليزية: Functional block diagrams).
عادة ما يتم إنشاء «مخططات كتل الموثوقية» (بالإنجليزية: Reliability block diagrams) أو «أشجار الخطأ» (بالإنجليزية: Fault tree) في نفس الوقت. تُستخدم هذه المخططات لتتبع تدفق المعلومات على مستويات مختلفة من التسلسل الهرمي للنظام، ولتحديد المسارات و«الواجهات البينية / الفواصل» الحرجة، ولتحديد آثار إخْفاق المستوى الأدنى على المستوى الأعلى.
تحديد وضع الإخْفاق
[عدل]لكل جزء أو لكل وظيفة يغطيها التحليل، يتم تطوير قائمة كاملة من أوضاع الإخْفاق. بالنسبة لنظام FMECA الوظيفي، تشمل أوضاع الإخْفاق النموذجية ما يلي:
- إدارة العملية في غير أوانها
- الإخْفاق في العمل عند الطلب
- فقدان الإنتاج
- الإنتاج المتقطع
- الناتج الخاطئ (بالنظر إلى الوضع الحالي)
- الإنتاج غير الصالح (تحت أي شرط)
بالنسبة لتحليل نمط وآثار وحرجية الإخفاق على مستوى «الجزء-القطعة»، يمكن الحصول على بيانات وضع الإخْفاق من قواعد البيانات مثل RAC FMD-91 [1] أو RAC FMD-97.[2] لا توفر قواعد البيانات هذه أوضاع الإخْفاق فحسب، بل توفر أيضًا نسب وضع الإخْفاق. فعلى سبيل المثال:
نوع الجهاز | وضع الإخْفاق | النسبة (α) |
---|---|---|
المرحل | إخْفاق في الإغلاق | 0.55 |
إغلاق عَرَضي | 0.26 | |
دائرة مقصورة | 0.19 | |
المقاومة | تغيير المعامل | 0.66 |
دائرة مقصورة | 0.31 | |
دائرة مفتوحة | 0.03 |
ثم يتم بعدها احصاء كل وظيفة أو جزء في شكل مصفوفة، وتعيين صف واحد لكل وضع من أوضاع الإخْفاق.
نظرًا لأن FMECA يشتمل عادة على مجموعة بيانات كبيرة جدًا، لذا يجب اختيار اسم تعريف فريد لكل عنصر (سواء وظيفة أو جزء-قطعة)، وأيضا لكل «وضع إخْفاق» لكل عنصر على حده.
تحليل آثار الإخْفاق
[عدل]يتم تحديد تأثيرات الإخْفاق وإدخالها في كل صف من مصفوفة تحليل نمط وآثار وحرجية الإخفاق مع مراعاة المعايير المحددة في القواعد الأساسية. يتم وصف التأثيرات بشكل منفصل للمستويات المحلية والأعلى منها والمستويات النهائية (للنظام). قد تشمل تأثيرات مستوى النظام:
- إخْفاق النظام.
- تدهور العملية.
- إخْفاق حالة النظام.
- لا يوجد تأثير فوري.
يتم تفصيل فئات تأثير الإخْفاق المستخدمة في مختلف المستويات الهرمية من قبل المُحلل، بواسطة التقدير الحكم الهندسي.
تصنيف الخطورة
[عدل]يتم تعيين وتصنيف درجة الخطورة لكل وضع فشل لكل عنصر بعينه ويتم إدخاله في مصفوفة تحليل نمط وآثار وحرجية الإخفاق، استنادًا إلى عواقب مستوى النظام. يتم استخدام مجموعة صغيرة من التصنيفات وعادة ما تكون من 3 إلى 10 مستويات شدة.
على سبيل المثال، عند التحضير باستخدام معيار MIL–STD–1629A، عادة ما يتبع تصنيف خطورة الفشل أو الخطأ معيار MIL-STD–882.[3]
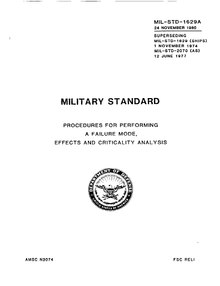
الفئة | وصف | المعايير |
---|---|---|
I | كارثي | قد يؤدي إلى الوفاة أو العجز الكلي الدائم أو الخسارة التي تتجاوز مليون دولار، أو الأضرار البيئية الشديدة التي لا رجعة فيها والتي تنتهك القانون أو اللوائح. |
II | حرج | يمكن أن يؤدي إلى عجز جزئي دائم أو إصابات أو مرض مهني قد يؤدي إلى دخول ثلاثة أفراد على الأقل في المستشفى، وخسارة تتجاوز 200 ألف دولار ولكن أقل من مليون دولار، أو أضرار بيئية قابلة للعكس تسبب انتهاكًا للقانون أو اللوائح. |
III | هامشي | يمكن أن يؤدي إلى إصابة أو مرض مهني يؤدي إلى يوم (أو أيام) عمل أو أكثر ضائعة، أو خسارة تتجاوز 10 آلاف دولار ولكن أقل من 200 ألف دولار، أو أضرار بيئية مخففة دون انتهاك للقانون أو اللوائح حيث يمكن القيام بأنشطة الاستعادة. |
IV | ضئيل | يمكن أن يؤدي إلى إصابة أو مرض لا يؤدي إلى فقدان يوم عمل، أو خسارة تتجاوز 2000 دولار ولكن أقل من 10 آلاف دولار، أو الحد الأدنى من الأضرار البيئية التي لا تنتهك القانون أو اللوائح. |
الفئات الحالية لشدة FMECA لتطبيقات إدارة الطيران الفيدرالية الأمريكية (FAA)، ووكالة الفضاء الأمريكية (ناسا)، ووكالة الفضاء الأوروبية، مشتقة من معيار MIL–STD–882.[4][5][6]
طرق الكشف عن الإخْفاق
[عدل]لكل مكوِّن ووضع إخْفاق، يتم تحليل قدرة النظام على الكشف عن الإخْفاق والإبلاغ عنه. يتم إدخال أحد الدرجات التالية في كل صف من مصفوفة FMECA:
- عادي: يشير النظام بشكل صحيح إلى حالة آمنة للطاقم.
- غير طبيعي: يشير النظام بشكل صحيح إلى حدوث عطل يتطلب تحرّك الطاقم.
- غير صحيح: إنذار خاطئ - يشير النظام عن طريق الخطأ إلى حالة آمنة في حالة حدوث خلل، أو ينبه طاقم العمل إلى خلل غير موجود.
تصنيف الحرجية
[عدل]قد يكون تقييم خطورة وضع الفشل نوعيًا أو كميًا.
- بالنسبة للتقييم النوعي: يتم تعيين رمز أو رقم احتمال حدوث خطأ وإدخاله في المصفوفة. على سبيل المثال، يستخدم MIL – STD – 882 خمسة مستويات احتمالية:
وصف | مستوى | البند الفردية | سريع |
---|---|---|---|
متكرر | ا | من المرجح أن يحدث في كثير من الأحيان في حياة العنصر | من ذوي الخبرة باستمرار |
محتمل | ب | سيحدث عدة مرات في حياة عنصر | سيحدث كثيرا |
عرضي | C | من المحتمل أن يحدث بعض الوقت في حياة عنصر | سيحدث عدة مرات |
التحكم عن بعد | د | غير محتمل ولكن من الممكن أن يحدث في حياة عنصر | غير محتمل، ولكن يمكن توقع حدوثه بشكل معقول |
غير محتمل | E | من غير المرجح، فإنه يمكن افتراض حدوث قد لا يكون من ذوي الخبرة | من غير المحتمل أن يحدث، لكن ممكن |
- بالنسبة للتقييم الكمي، يتم حساب «رقم الأهمية المشروط» Cm لكل طريقة فشل لكل عنصر، ويتم حساب «رقم درجة الأهمية» Cr لكل عنصر. يتم حساب أرقام الأهمية باستخدام القيم التالية:
- معدل الفشل الأساسي λp
- نسبة وضع الفشل α
- الاحتمال الشرطي β
- مدة مرحلة المهمة t
العنصر الحرج / قائمة الإخْفاقات الحرجة
[عدل]بمجرد اكتمال تقييم الأهمية لكل وضع إخْفاق لكل عنصر، يمكن تصنيف مصفوفة FMECA بحسب درجة الخطورة والاحتمالية النوعية أو رقم الأهمية الكمية. يمكّن هذا التحليل من تحديد العناصر الحرجة وأنماط الإخْفاق الحرجة التي يكون التخفيف من تصميمها مرغوبًا فيه.
تقييم الحرجية
[عدل]درجة الخطورة | |||||
---|---|---|---|---|---|
عديم الأهمية | هامشي | حرج | كارثي | ||
التكرار | متكرر | غير مرغوب | غير مقبول | غير مقبول | غير مقبول |
محتمل | مقبول | غير مرغوب | غير مقبول | غير مقبول | |
تصادفي | مقبول | غير مرغوب | غير مرغوب | غير مقبول | |
نادر | يمكن إهماله | مقبول | غير مرغوب | غير مرغوب | |
غير مرجح | يمكن إهماله | يمكن إهماله | مقبول | غير مرغوب | |
بعيد | يمكن إهماله | يمكن إهماله | يمكن إهماله | مقبول |
التوصيات
[عدل]بعد إجراء تحليل نمط وآثار وحرجية الإخفاق، يتم تقديم توصيات للتصميم لتقليل عواقب الإخفاقات الحرجة. قد يشمل ذلك اختيار المكونات ذات الموثوقية العالية، أو تقليل مستوى إجهاد التشغيل الذي يعمل به عنصر حرج، أو إضافة عنصر مكرر احتياطي (بالإنجليزية: redundancy)أو دوام المراقبة، إلى النظام.
تحليل الصيانة
[عدل]يتم تغذية FMECA عادة في كل من تحليل الصيانة وتحليل الدعم اللوجستي، وكلاهما يتطلب بيانات من تحليل نمط وآثار وحرجية الإخفاق.
تحليل نمط وآثار وحرجية الإخفاق هي الأداة الأكثر شعبية لتحليل الإخْفاق والحرجية للأنظمة لتحسين الأداء. في عصر الصناعة 4.0 الحالي، تنفذ الصناعات إستراتيجية صيانة تنبؤية لأنظمتها الميكانيكية. يستخدم تحليل نمط وآثار وحرجية الإخفاق على نطاق واسع لتحديد وضع الإخْفاق وتحديد أولويات الأنظمة الميكانيكية وأنظمتها الفرعية للصيانة التنبؤية.[7]
تقرير تحليل نمط وآثار وحرجية الإخفاق
[عدل]يتكون تقرير FMECA من وصف النظام والقواعد الأساسية والافتراضات والاستنتاجات والتوصيات والإجراءات التصحيحية التي يجب تتبعها ومصفوفة FMECA المرفقة والتي قد تكون في جدول بيانات أو ورقة عمل أو نموذج قاعدة بيانات.
انظر أيضًا
[عدل]- تحليل نمط وآثار الإخفاق.
- هندسة الوثوقية.
- الموثوقية والتوفر والصيانة والسلامة.
- تقييم المخاطر.
- هندسة وقائية.
- سلامة النظام.
المراجع
[عدل]- ^ Chandler، Gregory؛ Denson, W.؛ Rossi, M.؛ Wanner, R. (1991). Failure Mode/Mechanism Distributions (PDF). Reliability Analysis Center. FMD–91. مؤرشف من الأصل (pdf) في 2020-01-26. اطلع عليه بتاريخ 2010-03-14.
- ^ Failure Mode/Mechanism Distributions. Reliability Analysis Center. 1997. FMD–97. مؤرشف من الأصل في 2014-07-15.
- ^ Standard Practice for System Safety. D. وزارة الدفاع. 1998. MIL–HDBK–882D. مؤرشف من الأصل (pdf) في 2011-07-22. اطلع عليه بتاريخ 2010-03-14.
- ^ NASA Systems Engineering Handbook (PDF). National Aeronautics and Space Administration. SP–610S. مؤرشف من الأصل (PDF) في 2019-09-04.
- ^ Failure Modes, Effects and Criticality Analysis (FMECA). D. European Space Agency. 1991. ECSS–Q–30–02A.
- ^ Reusable Launch and Reentry Vehicle System Safety Processes (PDF). Federal Aviation Administration. 2005. AC 431.35–2A. مؤرشف من الأصل (pdf) في 2017-02-10. اطلع عليه بتاريخ 2010-03-14.
- ^ Thoppil, Nikhil M.; Vasu, V.; Rao, C. S. P. (27 Aug 2019). "Failure Mode Identification and Prioritization Using FMECA: A Study on Computer Numerical Control Lathe for Predictive Maintenance". Journal of Failure Analysis and Prevention (بالإنجليزية). DOI:10.1007/s11668-019-00717-8. ISSN:1864-1245. Archived from the original on 2021-02-14.