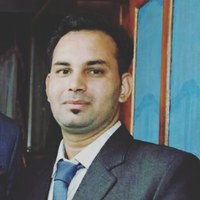
SANDEEP KUMAR
Sandeep Kumar is pursuing his PhD. In Mechanical Engineering From Anna University, Chennai (T.N.) and working as a Research Assistant. He received his Diploma (Mechanical Engineering) from Himachal Pradesh Takniki Shiksha Board, Dharmshala, India; B. Tech. (Mechanical Engineering) from Arni University and M.Tech (Production) from Himachal Pradesh Technical University. He has 3-years of teaching experience. He has published a number of papers in national and international conference and his field of interest is the Machining of difficult-to-machine super alloys, Artificial Intelligence methods for Optimization of Conventional and Non conventional Machining process parameters and Tolerance Analysis.
Supervisors: Dr. S. Dhanabalan (Ph.D., M.Tech, B.E., Diploma in ME) (Anna University), Dr. C. Sathiya Narayanan (NIT Trichy), Dr. C. Balamurgan (Anna University), Dr. T. Kartikhikeyan (Dean ME, MKCE, Karur), Dr. C. Ramesh (H.O.D. ME), MKCE, Karur., and Dr. Sivakumar (HOD ME), Bannari Amman College of Engg. Erode.
Supervisors: Dr. S. Dhanabalan (Ph.D., M.Tech, B.E., Diploma in ME) (Anna University), Dr. C. Sathiya Narayanan (NIT Trichy), Dr. C. Balamurgan (Anna University), Dr. T. Kartikhikeyan (Dean ME, MKCE, Karur), Dr. C. Ramesh (H.O.D. ME), MKCE, Karur., and Dr. Sivakumar (HOD ME), Bannari Amman College of Engg. Erode.
less
InterestsView All (18)
Uploads
Papers by SANDEEP KUMAR
industries because of their accuracy, the possibility to obtain complex shapes, close tolerances and economically. Therefore, the aim of this experimental work is to analyze the impact of pulse on time and wire feed rate on performance characteristics namely, kerf width and heat affected
zone (HAZ). In this experimental investigation, micro level slot cutting experiments were carried out on aluminum plate of 2 mm thickness by WEDM with response surface design. Multi-criteria decision making Grey relational analysis (GRA) technique has been utilized to find optimal
machine settings of process constraints. Polynomial models were developed for output constraints. From results, it is analyzed that the pulse on time has more dominance on kerfs width whereas wire feed rate has higher influence on HAZ. The obtained outcomes will expedite
the advanced machining industries to enhance machinability and dimensional accuracy.
of circular shape brass electrodes and process parameters on material removal rate, tool wear and part form deviations in the EDM process of Inconel 718 nickel-based alloy in the die-sinking EDM process. Three major process parameters, namely peak current, pulse on time and pulse off time, were selected to perform experiments using 3 mm diameter circular shape brass electrodes. The influence of the selected process parameters was analysed using hybrid Taguchi and multi-criteria decision grey relational analysis methods on workpiece form deviations, electrode wear rate and material removal rate. The dominance of each process parameter was analysed with an artificial intelligence-based ANFIS model and the developed model showed a minimum mean percentage error. Finally, the form deviations on the holes of two plates obtained by the EDM process were transferred to an assembled product to verify its assembling.
EO possess various constituents mainly sesquiterpenoids, benzenoids, phenylpropanoids etc. The demand for C. deodara plant material and its essential oil has been increasing in pharmaceutical, chemical, food and perfumery industries because of its favourable physicochemical characteristics and therapeutic efficacy. C. deodara has been used as antiseptic, insecticides, anti-inflammatory, molluscicidal and anti-fungal. Therefore, the main objective of this experimental work is to investigate the effect of different particle sizes of plant material on the yield of essential oil; to investigate the effect of processing time on C. deodara EO
yield and their physicochemical characteristics and analysis of essential oil constituents using GC-MS. Different size of C. deodara material namely, grade A (large size), grade B (medium size) and grade C (small size) material has been extracted using Clevenger’s apparatus to measure its physicochemical properties. The processed grade B material was extracted with n-hexane by the maceration process to analyse variation in physicochemical properties. From the results, it has been observed that medium-size material of C. deodara has a higher percentage of yield because it has an optimum surface area to release its constituents.
Temperature variations have a direct impact on physical as well as chemical properties. Higher temperatures and pressures result in a ‚harsh‘ aroma that changes the aromatic properties and decrease the oil‘s therapeutic values. Distillation time has also an impact on the yield as well
as on the physical and chemical properties of the material. Thin-layer chromatography showed 10 spots of different colours in essential oil. The major constituent‘s percentage obtained after GC-MS analysis as α-himachlene (13.83%), γ-himachlene (12.00%), β-himachlene (37.34%),
Deodaron (0.43%), α-atlantone (4.53%), Z, γ-atlantone (2.77%), E, γ-atlantone (3.34%) and E, α-atlantone (10.63%).
multi-parametric optimization of Universal Cylindrical grinding machine parameters such as Abrasive wheel speed, feed rate, work piece spindle rotation & depth of cut. The consequence of input process parameters was optimized for output responses such as surface roughness &
MRR of AISI 1040 medium carbon steel. The values of surface roughness were evaluated with the help of Mitutoyo Surf, test 4, L. C. 0.1μm surface roughness tester and MRR measurements were
calculated during the process by using an electronic digital weight balance. The experimental results and optimized parameters showed the considerable improvement in the process.
machining time, cutting angle and form tolerance, i.e. flatness and angularity were considered as output responses. The experimental outcomes were optimized by hybrid optimization using Taguchi and grey
relational analysis. The investigation outcomes had exposed that the machining presentation on multiple characteristics in the EDM technique was developed excellently concluded this attitude. The optimized parameters by hybrid optimization showed the considerable improvement in the process.
dies steel.
Design/methodology/approach – The experiments were performed on AGIE CUT 220 CNC WEDM. High chromium-high carbon dies steel (D3) was used in the form of a rectangular plate. The workpiece and the
Q2 brass wire having dia ɸ 0.25 mm had linked up with +ve and –ve polarity in the DC power source, respectively. De-ionized water having a conductivity level of 0.6 μs/cm was used as the dielectric medium. The
dielectric fluid was flushed from the top and bottom nozzles and material was submerged in the dielectric.
Findings – The WEDM process parameters for D3 die steel had optimized by using Grey relational analysis method couples with Taguchi method. The optimum solution has been calculated for MRR, cutting speed (Cs), machining time and surface roughness (SR) (Ra value). A fuzzy logic model using Matlab was developed for the prediction of performance parameters, namely MRR, cutting speed (Cs), machining time (M/c time) and SR with respect to changes in input parameters.
Research limitations/implications – The fuzzy model shows the 96.19 percent accuracy between the experimental values and the predicted values.
Practical implications – The optimized parameters by multi-parametric optimization method showed considerable improvement in the process and will facilitate the WEDM, tool and die industries, defense and
aerospace industries to improve the productivity with the higher surface finish.
Originality/value – The attained optimum outcomes had also been examined through a real experiment and established to
be satisfactory.
using steam/Hydro distillation, ingredient and uses. This article will facilitate the science students and small scale EO’s industries to improve their productivity with latest techniques.
close limits and tolerances, is one of the most important requirement. Abrasive machining processes are
generally the last operations performed on manufactured products for higher surface finishing and for fine or
small scale material removal. Higher surface finish and high rate of removal can be obtained if a large number of
grains act together. This is accomplished by using bonded abrasives as in grinding wheel or by modern
machining processes. In the present study, Taguchi method or Design of experiments has been used to optimize
the effect of cylindrical grinding parameters such as wheel speed (rpm), work speed, feed (mm/min.), depth of
cut and cutting fluid on the surface roughness of EN15AM steel. Ground surface roughness measurements were
carried out by Talysurf surface roughness tester. EN15AM steel has several industrial applications in
manufacturing of engine shafts, connecting rods, spindles, studs, bolt, screws etc. The results indicated that
grinding wheel speed, work piece speed, table feed rate and depth of cut were the significant factors for the
surface roughness and material removal rate. Surface roughness is minimum at 2000 r.p.m. of grinding wheel
speed , work piece speed 80 rpm, feed rate 275 mm/min. and 0.06 mm depth of cut
Conference Presentations by SANDEEP KUMAR
industries because of their accuracy, the possibility to obtain complex shapes, close tolerances and economically. Therefore, the aim of this experimental work is to analyze the impact of pulse on time and wire feed rate on performance characteristics namely, kerf width and heat affected
zone (HAZ). In this experimental investigation, micro level slot cutting experiments were carried out on aluminum plate of 2 mm thickness by WEDM with response surface design. Multi-criteria decision making Grey relational analysis (GRA) technique has been utilized to find optimal
machine settings of process constraints. Polynomial models were developed for output constraints. From results, it is analyzed that the pulse on time has more dominance on kerfs width whereas wire feed rate has higher influence on HAZ. The obtained outcomes will expedite
the advanced machining industries to enhance machinability and dimensional accuracy.
of circular shape brass electrodes and process parameters on material removal rate, tool wear and part form deviations in the EDM process of Inconel 718 nickel-based alloy in the die-sinking EDM process. Three major process parameters, namely peak current, pulse on time and pulse off time, were selected to perform experiments using 3 mm diameter circular shape brass electrodes. The influence of the selected process parameters was analysed using hybrid Taguchi and multi-criteria decision grey relational analysis methods on workpiece form deviations, electrode wear rate and material removal rate. The dominance of each process parameter was analysed with an artificial intelligence-based ANFIS model and the developed model showed a minimum mean percentage error. Finally, the form deviations on the holes of two plates obtained by the EDM process were transferred to an assembled product to verify its assembling.
EO possess various constituents mainly sesquiterpenoids, benzenoids, phenylpropanoids etc. The demand for C. deodara plant material and its essential oil has been increasing in pharmaceutical, chemical, food and perfumery industries because of its favourable physicochemical characteristics and therapeutic efficacy. C. deodara has been used as antiseptic, insecticides, anti-inflammatory, molluscicidal and anti-fungal. Therefore, the main objective of this experimental work is to investigate the effect of different particle sizes of plant material on the yield of essential oil; to investigate the effect of processing time on C. deodara EO
yield and their physicochemical characteristics and analysis of essential oil constituents using GC-MS. Different size of C. deodara material namely, grade A (large size), grade B (medium size) and grade C (small size) material has been extracted using Clevenger’s apparatus to measure its physicochemical properties. The processed grade B material was extracted with n-hexane by the maceration process to analyse variation in physicochemical properties. From the results, it has been observed that medium-size material of C. deodara has a higher percentage of yield because it has an optimum surface area to release its constituents.
Temperature variations have a direct impact on physical as well as chemical properties. Higher temperatures and pressures result in a ‚harsh‘ aroma that changes the aromatic properties and decrease the oil‘s therapeutic values. Distillation time has also an impact on the yield as well
as on the physical and chemical properties of the material. Thin-layer chromatography showed 10 spots of different colours in essential oil. The major constituent‘s percentage obtained after GC-MS analysis as α-himachlene (13.83%), γ-himachlene (12.00%), β-himachlene (37.34%),
Deodaron (0.43%), α-atlantone (4.53%), Z, γ-atlantone (2.77%), E, γ-atlantone (3.34%) and E, α-atlantone (10.63%).
multi-parametric optimization of Universal Cylindrical grinding machine parameters such as Abrasive wheel speed, feed rate, work piece spindle rotation & depth of cut. The consequence of input process parameters was optimized for output responses such as surface roughness &
MRR of AISI 1040 medium carbon steel. The values of surface roughness were evaluated with the help of Mitutoyo Surf, test 4, L. C. 0.1μm surface roughness tester and MRR measurements were
calculated during the process by using an electronic digital weight balance. The experimental results and optimized parameters showed the considerable improvement in the process.
machining time, cutting angle and form tolerance, i.e. flatness and angularity were considered as output responses. The experimental outcomes were optimized by hybrid optimization using Taguchi and grey
relational analysis. The investigation outcomes had exposed that the machining presentation on multiple characteristics in the EDM technique was developed excellently concluded this attitude. The optimized parameters by hybrid optimization showed the considerable improvement in the process.
dies steel.
Design/methodology/approach – The experiments were performed on AGIE CUT 220 CNC WEDM. High chromium-high carbon dies steel (D3) was used in the form of a rectangular plate. The workpiece and the
Q2 brass wire having dia ɸ 0.25 mm had linked up with +ve and –ve polarity in the DC power source, respectively. De-ionized water having a conductivity level of 0.6 μs/cm was used as the dielectric medium. The
dielectric fluid was flushed from the top and bottom nozzles and material was submerged in the dielectric.
Findings – The WEDM process parameters for D3 die steel had optimized by using Grey relational analysis method couples with Taguchi method. The optimum solution has been calculated for MRR, cutting speed (Cs), machining time and surface roughness (SR) (Ra value). A fuzzy logic model using Matlab was developed for the prediction of performance parameters, namely MRR, cutting speed (Cs), machining time (M/c time) and SR with respect to changes in input parameters.
Research limitations/implications – The fuzzy model shows the 96.19 percent accuracy between the experimental values and the predicted values.
Practical implications – The optimized parameters by multi-parametric optimization method showed considerable improvement in the process and will facilitate the WEDM, tool and die industries, defense and
aerospace industries to improve the productivity with the higher surface finish.
Originality/value – The attained optimum outcomes had also been examined through a real experiment and established to
be satisfactory.
using steam/Hydro distillation, ingredient and uses. This article will facilitate the science students and small scale EO’s industries to improve their productivity with latest techniques.
close limits and tolerances, is one of the most important requirement. Abrasive machining processes are
generally the last operations performed on manufactured products for higher surface finishing and for fine or
small scale material removal. Higher surface finish and high rate of removal can be obtained if a large number of
grains act together. This is accomplished by using bonded abrasives as in grinding wheel or by modern
machining processes. In the present study, Taguchi method or Design of experiments has been used to optimize
the effect of cylindrical grinding parameters such as wheel speed (rpm), work speed, feed (mm/min.), depth of
cut and cutting fluid on the surface roughness of EN15AM steel. Ground surface roughness measurements were
carried out by Talysurf surface roughness tester. EN15AM steel has several industrial applications in
manufacturing of engine shafts, connecting rods, spindles, studs, bolt, screws etc. The results indicated that
grinding wheel speed, work piece speed, table feed rate and depth of cut were the significant factors for the
surface roughness and material removal rate. Surface roughness is minimum at 2000 r.p.m. of grinding wheel
speed , work piece speed 80 rpm, feed rate 275 mm/min. and 0.06 mm depth of cut