Papers by Kerem Altug Guler
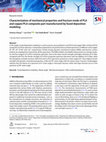
Practical Metallography, Dec 20, 2017
In this paper, fused deposition modeling is used to process pure polylactic acid (PLA) and copper... more In this paper, fused deposition modeling is used to process pure polylactic acid (PLA) and copper fiber reinforced PLA composite (Cu/PLA) specimen. Comparative experiments are performed on printed specimens of different raster angles (0°, 90°, 45°, 0°/90° and ± 45°, respectively). Tensile testing, dynamic mechanical analysis (DMA), and fracture surface analysis are employed to characterize all the specimens. The DMA exhibits remarkable improvement on storage modulus and loss tangent of Cu/PLA composite specimen. Due to the lower tensile strength and higher elasticity of Cu fiber compared with PLA, the tensile strength of Cu/PLA composite specimen decreases with the addition of Cu fiber, while the elongation-at-break increases. Both PLA and Cu/PLA specimens printed at a raster angle of 0° show highest tensile strength and dynamic mechanical properties, while the 90° raster angle with the lowest value. Fracture morphologies indicate that the failure of a specimen of 0° raster angle is intra-layer fracture, while inter-layer fracture occur in the specimen of 90° raster angle.
Gazi university journal of science, Dec 1, 2021
Highlights • This paper focuses on the recovery of turning chips. • Experimental studies have bee... more Highlights • This paper focuses on the recovery of turning chips. • Experimental studies have been carried out with A356 alloy. • Titanium transfer in pure aluminum was found twofold higher than that of A356.
Materials Chemistry and Physics, Jul 1, 2023
European Journal of Wood and Wood Products, Jun 1, 2004
International Journal of Metalcasting, May 5, 2022
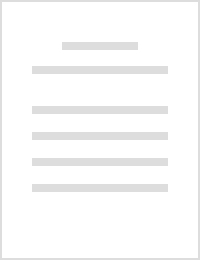
Practical Metallography, 2018
A356 aluminium alloy/commercially pure (CP) copper bimetal was produced via liquid-solid process ... more A356 aluminium alloy/commercially pure (CP) copper bimetal was produced via liquid-solid process by lost foam casting (LFC) technique. Cu rod was placed into an expanded polystyrene (EPS) pattern followed by applying thermoplastic adhesive to cover apertures between rod and foam, pattern coating, drying and moulding in a steel flask using free silica sand. Molten A356 alloy was poured into moulded pattern at 760 °C and 790 °C, respectively. Also, hot dip A356 coating was implemented on Cu rods for each casting temperature and the effect of pre-coating on the final product was studied. Optical microscopy, scanning electron microscopy (SEM), X-ray diffraction (XRD), energy-dispersive X-ray spectroscopy (EDS) and hardness devices were used to determine microstructural evaluation and interface features. No metallurgical bonding occurred between Al and both coated and uncoated Cu rods at 760 °C. However, better mechanical bonding was observed comparing to uncoated sample cast at 790 °C b...
High Temperature Materials and Processes, 2016
The wear behavior of cast A7075 and A7075/SAF 2205 composite material fabricated by vacuum-assist... more The wear behavior of cast A7075 and A7075/SAF 2205 composite material fabricated by vacuum-assisted investment flask casting was investigated under dry sliding condition. The wear tests were carried out using a “ball-on-disc” type tribometer. In the wear tests, 100Cr6 and ZrO2 balls were used as counterparts and the load, total distance and rotating speed were selected as 10 N, 100 m and 100 rpm, respectively. The results were evaluated using the friction coefficient–distance diagram, weight loss and wear rate. All worn surfaces were examined by scanning electron microscope and wear characteristics of the materials were discussed as a function of the microstructural features. It was concluded that composite material had lower friction coefficient, less weight loss and slower wear rate than that of cast material.

Transactions of Nonferrous Metals Society of China, 2019
Cooling slope casting has been applied to aluminium casting alloys for producing ingots with non-... more Cooling slope casting has been applied to aluminium casting alloys for producing ingots with non-dendritic microstructure. Semi-solid forming of the AA7075 was studied via cooling slope casting, reheating and thixoforging processes in order to determine the effect of semi-solid casting on the microstructure of the alloy. AA7075 ingots with non-dendritic microstructure were produced with cooling slope pouring. Castings were characterized by light microscopy, image analysis, scanning electron microscopy and EDS analysis. The resulting structures are promising in terms of grain size and sphericity. It was realized that grain coarsening may occur very suddenly in the reheating process. Cooling slope castings were obtained with 30° and 60° inclination angles, and in comparison, 60° castings showed better results. Moreover, by using short reheating periods, semi-solid forging causes trace formation in the solid grains.
Materials research express, Jan 6, 2020
MP MATERIALPRUEFUNG - MP MATERIALS TESTING, 2013
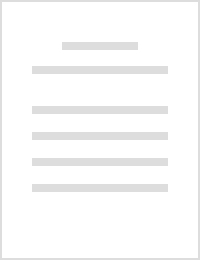
Practical Metallography, 2016
Naval brasses consisting of the α–β duplex phases are a special kind of Cu-Zn alloys. They are kn... more Naval brasses consisting of the α–β duplex phases are a special kind of Cu-Zn alloys. They are known to have excellent corrosion resistance to sea water and marine conditions. The aim of this study is the investigation of properties and behaviours of naval brass parts formed by different casting processes. A medium leaded naval brass alloy with 60 % Cu, 39 % Zn and 1 % Pb approximate composition was used. Several samples were subjected to mechanical testing by means of tensile and hardness tests. Light optical microscopy with image analyser and scanning electron microscopy were used for microstructure observations. The corrosion test was applied in sea water conditions. Results reveal that besides hot forging also casting is a very suitable technique for naval brass shaping. Casting does not have a negative effect on the most important property corrosion resistance. Furthermore, the obtained mechanical properties are satisfactory.
International Journal of Metalcasting

Russian Journal of Non-Ferrous Metals
Thixoforging combined with low superheat casting (LSC) is a promising shaping process for alumini... more Thixoforging combined with low superheat casting (LSC) is a promising shaping process for aluminium casting alloys. LSC process is based on rapid solidification of an alloy which cast with low pouring temperature. With this method, a feedstock material is produced with non-dendritic microstructure that ready for spherisation in reheating sequence of further semi-solid process. Al-Si alloys are still castable even at low temperatures due to their excellent fluidities. This study subjects to present spherisation of A356 and A380 alloy billets cast with LSC process that provides appropriate beginning material with relatively high sphericity. Obtained billet parts were reheated for different times at a semi-solid state temperature. Some of these billets were directly quenched for observing the effects of reheating and the others were thixoforged. With sufficient reheating time, deformation of thixoforging process did not significantly affect on the spherical microstructure. Unnecessarily long reheating period caused excessive grain growth. A356 alloy had higher spherisation tendency than A380 alloy under similar process conditions.
wax pattern in the lost wax casting, the shell fabricated outside the foam pattern would produce ... more wax pattern in the lost wax casting, the shell fabricated outside the foam pattern would produce a relatively high surface roughness of the castings [7-9]. In the solid mould investment casting technique, lots of factors like pattern thick-ness, type of metal and alloy, average particle size of investment powder, type of casting machine, etc. effect the surface quality of the castings [10]. However, the surface condition of the pattern is the most significant one. Defeng et al. studied wax film and nitro-cellulose film formations on the EPS foam patterns to improve the surface quality of the shell mould investment cast parts and
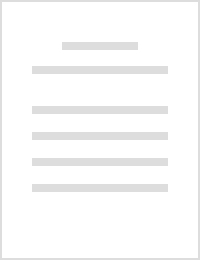
Practical Metallography, 2017
Abstract Semi-solid processes of aluminium alloys have been a focus of interest for many years. T... more Abstract Semi-solid processes of aluminium alloys have been a focus of interest for many years. Thixoforging is a kind of forging process which is carried out in the semi-solid region of the alloy. Ingots used in thixoforging process cannot be produced by conventional ways; they must be prepared with different processing routes. In this study, low superheat casting (LSC) technique was used for ingot fabrication in thixoforging process. LSC can be summarized as the pouring of molten metal at a temperature very close to liquidus followed by rapid solidification. Low heat input combined with sudden cooling suppresses dendritic growth and the conventional casting structure converts into a more spherical structure. A356 and A380 are well-known casting aluminium alloys which are commonly used in sand and die casting processes. These alloys are appropriate for semi-solid process and there are many applications that researches have been carried out in time. In view of that, A356 and A380 alloys were selected as subject of this comparative study and final structures were evaluated together. A LSC combined thixoforging process was successfully applied to both alloys and a spherical microstructure was obtained. High sphericity with a simple microstructure is the characteristic of the A356 alloy. A380 shows relatively lower sphericity with more complex microstructure which has numerous different intermetallic compounds.

China Foundry, 2018
L ost foam casting (LFC), also known as full mould casting, was invented and patented by Shoyer i... more L ost foam casting (LFC), also known as full mould casting, was invented and patented by Shoyer in 1958 [1-3]. LFC is evaluated as a new casting method to obtain near net shaped products which is carried out with expendable patterns produced from polymeric materials [4, 5]. In order to prepare a mould for LFC process, the polymeric pattern is coated with water-based refractory slurry, then placed in a fl ask, and fi nally the rest of the fl ask is fi lled with unbonded (loose) sand with the help of vibration to compress the sand. After the mould is prepared, the molten metal is poured directly onto the pattern [5, 6]. At the end of process, the foam polymer undergoes thermal degradation with high heat input and the liquid metal takes the solid pattern's place. Subsequent to solidification, a cast product with high dimensional accuracy is obtained [5, 7]. The LFC process is applied to produce engine components, intake manifolds, brake pump housings, etc.

Transactions of Nonferrous Metals Society of China, 2018
The effects of T6 heat treatment on thixoforged A356 and A380 aluminium alloys were studied. Low ... more The effects of T6 heat treatment on thixoforged A356 and A380 aluminium alloys were studied. Low superheat casting (LSC) technique was carried out to prepare proper specimens for thixoforging process. The samples were poured at 20 °C above their liquidus temperatures which provided the formation of equiaxed grains instead of dendritic growth. Produced billets were reheated for varied time from 20 to 80 min and thixoforged with 50% deformation rate. After thixoforging process, the samples were T6 heat treated for both A356 and A380 alloys. The microstructural evaluation and hardness alteration of thixoforged, solution treated and aged specimens were examined comparatively by using optical microscopy, scanning electron microscopy with energy-dispersive X-ray spectroscopy and Brinell hardness equipment. T6 heat treatment provided relatively uniform microstructure with newly formed precipitates that are Mg 2 Si and Al 2 Cu for A356 and A380 billets, respectively. Accordingly, hardness after artificial aging was increased considerably and reached HB 93 for A356 and HB 120 for A380 alloys.
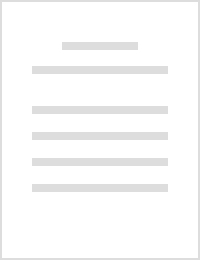
International Journal of Cast Metals Research, 2017
An attempt has been made to develop an investment powder which expands significantly in the setti... more An attempt has been made to develop an investment powder which expands significantly in the setting period to meet the solidification shrinkage of most metals and alloys. Investment powders consisting of tricalcium aluminate, quartz, various sulphate bearing compounds and a small amounts of controlling agents (additives) were used in the preparation of the block investment molds. A413 Al-Si (Etial 140) alloy was melted and poured in these molds to cast a test specimen of a special geometry. The preliminary results show that it is possible to produce dimensionally accurate castings by using expansive type investment powders. Samples cast into block investment molds prepared from ordinary non-expansive investment powder were smaller than the pattern size, while those poured into molds produced from expansive type powders were the same size or greater than the pattern size.
Uploads
Papers by Kerem Altug Guler