Papers by Evgueni Bordatchev

The International Journal of Advanced Manufacturing Technology, 2014
Laser polishing is presently regarded as one of the enabling technologies hoped to eventually rep... more Laser polishing is presently regarded as one of the enabling technologies hoped to eventually replace the need for time-consuming and error-prone manual polishing operations which are often required by metallic surfaces. During laser polishing, a thin layer of material is being melted as a result of laser irradiation. Since molten metal is characterized by increased relocation capabilities, laser polishing is generally accompanied by a more or less significant decrease in the surface roughness. The primary objective of this study is to present a comprehensive snapshot of the advancements made over more than one decade with respect to theoretical and experimental investigation of laser polishing technology. However, in addition to the usual review of the state-of-theart in the field, the study places an increased emphasis on the finishing performance of the process, defined through the perspective of pre-and postpolishing surface roughness. The implementation of this metric with strong practical implications has revealed that under appropriate process parameters, certain classes of metallic materials can reduce their average surface roughness by more than 80 %, possibly to R a =5 nm. Nonetheless, a more rigorous and fundamental understanding of the intrinsic mechanisms underlying laser polishing remains one of the currently unfulfilled premises toward a wider industrial adoption of the process.
Journal of Laser Applications, 2018
The study of laser textured surfaces has been carried out in the pursuit of superhydrophobic and ... more The study of laser textured surfaces has been carried out in the pursuit of superhydrophobic and superhydrophilic functional surfaces on stainless steel and silicon carbide substrate materials, respectively. The theoretical aspects of laser texturing a surface were investigated in order to understand how replication of micro-and nanoscale features could be achieved by high intensity picosecond pulsed laser systems. A series of laser parameters, pre-processing, and post-processing steps were developed to achieve contact angles of 152°as well as 0°on stainless steel and silicon carbide substrates, respectively. The substrates were used to demonstrate functional characteristics such as water repellency, self-cleaning, water adhesion, and dispersion of water using micro-capillary forces.
Computer-Aided Design and Applications, 2022
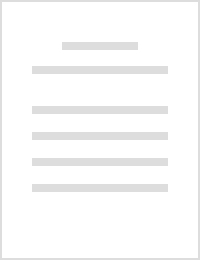
Lasers in Manufacturing and Materials Processing, 2020
Laser polishing is a surface finishing operation in which a superficial layer of material is bein... more Laser polishing is a surface finishing operation in which a superficial layer of material is being redistributed in a controlled manner, typically to achieve a better surface quality. In this study, three-dimensional numerical model has been developed to investigate the formation of remelted line during the laser polishing (LP) of H13 tool steel. To closely mimic the thermophysics of laser line formation, several different heat transfer mechanisms have been included in the simulation. Furthermore, to enhance model accuracy and applicability, experimental calibrations were conducted to determine more accurate representations of material absorptivity, a parameter that is typically assumed as constant in the literature. The experimental validations performed have proved that the model can constitute a reliable alternative to time and cost consuming trial-and-error physical LP experiments that are commonly used to analyze the effect of various process parameters on post-polished surface quality.
The International Journal of Advanced Manufacturing Technology, 2022
Laser Congress 2020 (ASSL, LAC), 2020
Present report introduces some of most valuable achievements and developments of laser surface po... more Present report introduces some of most valuable achievements and developments of laser surface polishing and laser surface functionalization F technologies at the National Research Council of Canada over the past five years.
Procedia Manufacturing, 2020

Flexible optical sheets are thin large-area polymer light guide structures that can be used to cr... more Flexible optical sheets are thin large-area polymer light guide structures that can be used to create innovative passive light-harvesting and illumination systems. The optically transparent micro-patterned polymer sheet is designed to be draped over arbitrary surfaces or hung like a curtain. The light guidance sheet is fabricated by bonding two or more micro-patterned layers with different indices of optical refraction. By imprinting micro-optical elements on the constituent layers, it is possible to have portions of the optical sheet act as a light concentrator, near ‘lossless’ transmitter, or diffuser. However, the performance and efficiency of the flexible optical sheet depends on the overall curvature (κ) of the optical sheet and the relative orientation of incident light source. To illustrate this concept, the impact of key design parameters on the controlled guidance of light through a two-layer polydimethylsiloxane (PDMS) concentrator-transmitter-diffuser optical sheet is inv...
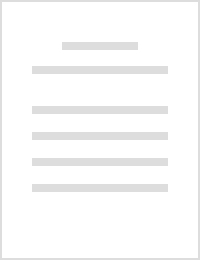
Procedia CIRP, 2020
Abstract Laser polishing (LP) is an advanced manufacturing process for improving surface quality ... more Abstract Laser polishing (LP) is an advanced manufacturing process for improving surface quality via laser remelting of the surface topography of the material. In this preliminary study, a high-speed thermographic imager was coaxially installed on a LP system and was used to capture the thermo-dynamics of the laser-material interactions under various process conditions. A visualization algorithm was developed and used to monitor the LP process dynamics along the laser path trajectory. This approach enables the analysis of LP process stability by means of reliable informational features of the individual images. Further, unsupervised machine learning analysis (Bayesian classifier) was used to reduce the number of informational variables/statistical characteristics of the images without compromising process predictability. These two techniques were applied for both monitoring and classification of the LP line experiments performed with a laser power of {5, 20, 35} W and a scanning speed of 75 mm/s. The preliminary results demonstrate the high potential of machine learning analysis towards the optimization and control of the LP process.
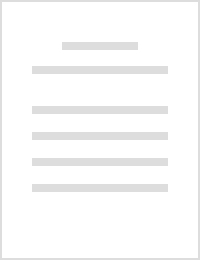
Precision Engineering, 2020
Abstract One of the versatile microstructures with numerous applications is represented by V-groo... more Abstract One of the versatile microstructures with numerous applications is represented by V-grooves. Their range of the applicability is broad and covers many types of components from mechanical to optical. Their fabrication process is accompanied by challenges related to their tight form accuracy, shape complexity and surface quality requirements. The vast majority of previously-reported axial cutting strategies rely on constant cutting depth approaches characterized by finish passes. The main objective of the current study was to investigate a newer constant cutting area (CCA) approach to be contrasted with a more conventional implementation involving a constant cutting thickness (CCT). However, unlike the previous axial cutting variants, both methods presented in this work lack finish passes that tend to increase the overall V-groove cutting time. The in-depth comparisons of the cutting force and V-groove facet surface quality seem to suggest even if CCA could generate slightly lower areal roughness for certain chip thickness values, its superior productivity might recommend it as the preferred V-groove axial cutting variant. Nonetheless, both CCT and CCA implementations detailed in this study were capable of generating V-groove surfaces characterized by optical surface quality (Sa
Procedia Manufacturing, 2017
Procedia Manufacturing, 2017
IEEE International Conference Mechatronics and Automation, 2005
Proceedings International Conference on MEMS, NANO and Smart Systems
READ THESE TERMS AND CONDITIONS CAREFULLY BEFORE USING THIS WEBSITE. https://nrc-publications.can... more READ THESE TERMS AND CONDITIONS CAREFULLY BEFORE USING THIS WEBSITE. https://nrc-publications.canada.ca/eng/copyright Vous avez des questions? Nous pouvons vous aider. Pour communiquer directement avec un auteur, consultez la première page de la revue dans laquelle son article a été publié afin de trouver ses coordonnées. Si vous n'arrivez pas à les repérer, communiquez avec nous à
Measurement Science and Technology, 2002
SPIE Proceedings, 2012
The solar energy industry strives to produce more and more efficient and yet cost effective photo... more The solar energy industry strives to produce more and more efficient and yet cost effective photovoltaic (PV) panels. Integration of specific micro/nano optical structures on the top surface of the PV panels is one of the efficient ways to increase their PV performance ...
Journal of Physics: Conference Series, 2007
Vous avez des questions? Nous pouvons vous aider. Pour communiquer directement avec un auteur, co... more Vous avez des questions? Nous pouvons vous aider. Pour communiquer directement avec un auteur, consultez la première page de la revue dans laquelle son article a été publié afin de trouver ses coordonnées. Si vous n'arrivez pas à les repérer, communiquez avec nous à
Experimental Thermal and Fluid Science, 2005

Computers & Industrial Engineering, 2012
This work proposes a process planning for machining of a Floor which is the most prominent elemen... more This work proposes a process planning for machining of a Floor which is the most prominent elemental machining feature in a 2½D pocket. Traditionally, the process planning of 2½D pocket machining is posed as stand-alone problem involving either tool selection, tool path generation or machining parameter selection, resulting in sub-optimal plans. For this reason, the tool path generation and feed selection is proposed to be integrated with an objective of minimizing machining time under realistic cutting force constraints for given pocket geometry and cutting tool. A morphed spiral tool path consisting of G 1 continuous biarc and arc spline is proposed as a possible tool path generation strategy with the capability of handling islands in pocket geometry. Proposed tool path enables a constant feed rate and consistent cutting force during machining in typical commercial CNC machine tool. The constant feed selection is based on the tool path and cutting tool geometries as well as dynamic characteristics of mechanical structure of the machine tool to ensure optimal machining performance. The proposed tool path strategy is compared with those generated by commercial CAM software. The calculated tool path length and measured dry machining time show considerable advantage of the proposed tool path. For optimal machining parameter selection, the feed per tooth is iteratively optimized with a pre-calibrated cutting force model, under a cutting force constraint to avoid tool rupture. The optimization result shows around 32% and 40% potential improvement in productivity with one and two feed rate strategies respectively.
Uploads
Papers by Evgueni Bordatchev