Papers by Jawad Badreddine
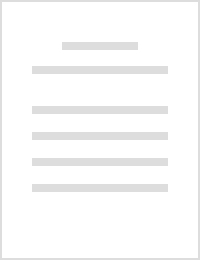
Le grenaillage ultrason est un procédé mécanique de traitement de surfaces. Il consiste à projete... more Le grenaillage ultrason est un procédé mécanique de traitement de surfaces. Il consiste à projeter des billes à la surface de pièces métalliques, à l’aide d’un système acoustique vibrant ultrasonore. Lors du traitement, les billes sont contenues dans une enceinte spécialement conçue pour la pièce à traiter, et adoptent un comportement similaire à celui d’un gaz granulaire vibré. Le grenaillage ultrason sert à introduire des contraintes résiduelles de compression dans le matériau traité. Ces contraintes de compression sont bénéfiques pour la tenue en fatigue de la pièce et sa résistance à la corrosion sous contraintes.L’objectif des présents travaux de thèse consiste à modéliser la dynamique des billes pendant le traitement, et pour des pièces et géométries complexes. En effet, depuis son industrialisation, la mise au point du procédé se fait de manière empirique qui, avec la complexification des pièces mécaniques traitées pousse cette approche à ses limites. La mise au point peut do...
1 A new method to quantify the heterogeneity of a shot stream – coverage and indent distribution ... more 1 A new method to quantify the heterogeneity of a shot stream – coverage and indent distribution J. Badreddinea,b,*, C. Ernoulda, E. Gueniera, Q. Puydta, A. Hazottea,c a IRT M2P, 4 rue Augustin Fresnel, 57070 Metz, France b Safran Group, rue des jeunes Bois, 78112Magny-Les-Hameaux, France c Laboratoire d’Etude des Microstructures et de Mécanique des Matériaux (LEM3), CNRS UMR 7239, Université de Lorraine, 57012 Metz Cedex, France * Corresponding author: [email protected]
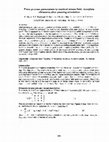
Shot peening is a pre-stressing surface treatment used in high-technological industries (aeronaut... more Shot peening is a pre-stressing surface treatment used in high-technological industries (aeronautics, nuclear) to enhance the mechanical characteristics and lifespan of mechanical parts. The component to be treated and spherical shot are placed within a treatment chamber; then the shot is projected onto the surface of the component. The multiple impacts induce compressive residual stresses in the material and enhance the surface characteristics and fracture resistance of the mechanical components. Modelling shot peening process is very complex as it involves several parameters such as shot velocity, mechanical properties of material, etc.The aim of this work is know the residual stress field after treatment using a simple model obtained with dimensional analysis exploiting experimental data. A comparison between experimental residual stress profile and computing residual stress profile is proposed. Using a model, which enables to track the motion of shot for ultrasonic shot peening ...
Method for determining the rate of recovery of a metal part having undergone a treatment modifyin... more Method for determining the rate of recovery of a metal part having undergone a treatment modifying the surface roughness of said workpiece, characterized in that it comprises the following steps: - a step of determining a calibration function (C ) of a parameter (L *) in the CIELAB color space depending on the recovery rate, so as to bind to a given value of said parameter (L *) the corresponding value of the recovery rate, - a step of measuring the value of said parameter (L *) of said workpiece, and - a step of determining of said workpiece recovery rates, by combining, using the calibration function, the thus-measured value of said parameter ( L *), the corresponding value of the part recovery rate.
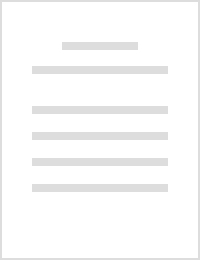
Materials Characterization, 2021
Abstract This paper presents a methodology to define and quantify the level of work hardening loc... more Abstract This paper presents a methodology to define and quantify the level of work hardening locally in a material. The methodology is proposed after a thorough experimental study based on three complementary experimental techniques for microstructural characterizations: microhardness, X-ray diffraction (XRD) and Electron Backscatter Diffraction (EBSD) applied on Inconel 718 samples. In our analysis, several loading histories including single tension, single compression, high strain rates and low cycle fatigue have been investigated. The effects of the microstructure have been further investigated by modifying the size of the grains and the size of the strengthening precipitates. Experimental tests have also been simulated to choose a model variable able to represent work hardening. A reciprocal link between work hardening and experimental characterizations has then been established. Correlation curves have been proposed that enable to quantify the level of work hardening from the knowledge of the experimental data. Accuracy and complementarity of the three experimental approaches are discussed as well as the impact of the microstructure of the material on the measured quantities.
Even when properly controlled, shot peening treatment may induce a complex residual stresses (RS)... more Even when properly controlled, shot peening treatment may induce a complex residual stresses (RS) field depending on the geometry of the treated part. Hence, among the variables which affect the fatigue behaviour of shot peened components, the geometry could play a major role. The more widespread method for predicting RS after shot peening consists in modelling the process by simulating the impacts between the shot and the treated part. When the geometry become complex, this method is not consistent with industrial constraints in terms of computing time. Thus the need is to develop a methodology in order to generate the RS field into a shot peened mechanical part with complex non flat geometries, and consequently predict the lifetime in a high cycle fatigue (HCF) regime.
Advances in Engineering Software, 2014
This paper presents a numerical model developed specifically for ultrasonic shot peening (USP). I... more This paper presents a numerical model developed specifically for ultrasonic shot peening (USP). It allows simulating the shot dynamics (trajectories in the chamber and impacts on the peened sample) in industrial configurations. The model supports complex 3D geometries, rotating parts and employs efficient collision detection algorithms for short computation times. The aim is to improve peening chamber designs and the choice of process parameters. The algorithm and main assumptions are presented. Numerical studies are then conducted to determine the performances of the model, in terms of computation time. Finally, a case study on a spur gear tests the model in an industrial configuration and shows a high correlation between the numerical results and experimental data.
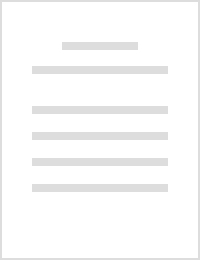
Materials Science Forum, 2013
This paper presents a 3D model that simulates an ultrasonic shot peening (USP) operation, using r... more This paper presents a 3D model that simulates an ultrasonic shot peening (USP) operation, using realistic process parameters and peening setups (part and chamber geometries). By simulating the shot dynamics (shot trajectories and impacts), statistical and spatial data are obtained for the peened component, i.e. surface coverage and coverage rate, impact speeds and angles, dissipated energy... This data can then be used for i) optimizing the design of peening chambers and process parameters and ii) predicting the residual stress and displacement fields induced by USP in the peened component. In fact, data from the 3D model can be used as initial data in existing residual stress prediction models. A chaining methodology was developed for this purpose and allows linking the choice of process parameters and USP setup to the induced residual stress displacement fields.
International Journal of Mechanical Sciences, 2014
Ultrasonic shot peening is a pre-stressing process that enhances the life span of mechanical part... more Ultrasonic shot peening is a pre-stressing process that enhances the life span of mechanical parts. The spheres constituting the shot are set in motion with a sonotrode and impact the treated part to generate a compressive residual stress field, hence increasing fatigue life. A model predicting the dynamics of the shot within the ultrasonic shot peening chamber is proposed. The influence of the initial conditions on the shot dynamics is first studied. The model is then used to obtain predictive values for the impact density and the spatial distribution of the velocity of the spheres before the impacts. The influence of the ultrasonic shot peening parameters is also evaluated. The variation of the geometry of the shot peening chamber is further considered with the use of a prismatic geometry.
We study the dynamic of shot during an ultrasonic shot peening process from two aspects. The firs... more We study the dynamic of shot during an ultrasonic shot peening process from two aspects. The first consists in running various calculations of spheres placed in a cylindrical chamber (radius 35 mm, height 40 mm) and propelled by a sonotrode (frequency 20 kHz, amplitude 25 µm). This allows for a better understanding of the minimal peening time needed to reach a stationary regime. The second aspect deals with the relationship between spatial impact distributions and normal impact velocities. Results show that after a specific peening time, initial conditions such as shot position and velocity have no influence on the calculation output. We also found that the surface impact frequency on a peened sample placed on top of a cylindrical or parallelepiped chamber with same inner volumes does not vary much, and that low velocity impacts are mainly concentrated at the edge of the chamber.
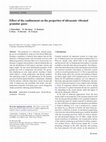
Granular Matter, 2013
The properties of a ultrasonic vibrated granular gas are investigated by using an event-driven Mo... more The properties of a ultrasonic vibrated granular gas are investigated by using an event-driven Molecular Dynamics simulation of inelastic hard spheres that are fluidized by a vibrating bottom wall (sonotrode) in boxes with different geometries showing either no or an increased confinement. It appears that geometry controls dramatically not only the distribution of wall impacts and their velocity and impact angles, but also more fundamental properties of the granular gas such as temperature and density. For geometries displaying an acute angle (prism), stacking is found, which induces a strong temperature and density gradient. The underlying origin of such phenomena for the granular gas arises from the spatial limitation, confinement, combined with the inelastic collisions induced by closely located side walls. It underscores the possibility that kinetic and thermodynamic properties of granular gases can be changed by simple geometries inducing spatial limitation.
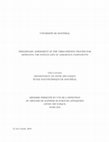
Vibratory peening derives from vibratory finishing and aims to induce beneficial compressive resi... more Vibratory peening derives from vibratory finishing and aims to induce beneficial compressive residual stresses while simultaneously polishing the treated part. Even though this process appeared in literature since the 2000s, only a few public articles have been published on this topic. This study, realized in partnership with Safran Aerospace Defense and Security and VibraFinish Ltd, investigates the vibratory peening effects, in terms of residual stresses, roughness and hardening, on aerospace alloys. The investigation focused on titanium alloy Ti-6Al-4V and case hardened steel E-16NiCrMo13 samples provided by Safran. The effects induced by the vibratory peening process have been compared to the effects induced by the shot peening process, using Almen intensity as a control parameter. The measured effects were surface roughness, sub-surface compressive residual stresses fields and hardness profiles. The literature review identifies the tub vibration frequency and the mass of media ...
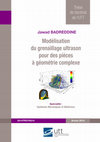
Le grenaillage ultrason est un procede mecanique de traitement de surfaces. Il consiste a projete... more Le grenaillage ultrason est un procede mecanique de traitement de surfaces. Il consiste a projeter des billes a la surface de pieces metalliques, a l’aide d’un systeme acoustique vibrant ultrasonore. Lors du traitement, les billes sont contenues dans une enceinte specialement concue pour la piece a traiter, et adoptent un comportement similaire a celui d’un gaz granulaire vibre. Le grenaillage ultrason sert a introduire des contraintes residuelles de compression dans le materiau traite. Ces contraintes de compression sont benefiques pour la tenue en fatigue de la piece et sa resistance a la corrosion sous contraintes.L’objectif des presents travaux de these consiste a modeliser la dynamique des billes pendant le traitement, et pour des pieces et geometries complexes. En effet, depuis son industrialisation, la mise au point du procede se fait de maniere empirique qui, avec la complexification des pieces mecaniques traitees pousse cette approche a ses limites. La mise au point peut do...
The process of ultrasonic shot peening has been studied from two aspects: a) a 3D numerical model... more The process of ultrasonic shot peening has been studied from two aspects: a) a 3D numerical model of the shot motion in the peening chamber based on the theory of granular gases, b) an experimental setup developed for measuring the shot velocity distribution in the chamber and impact locations on the peened surface. The aim of such study is to propose an experimental method providing shot trajectories in order to validate the 3D model for the process parameter optimization, used for example in the aeronautic industry. Mots clés : grenaillage ultrason, expérience, simulation
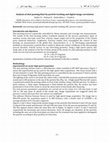
Introduction and objectives Shot peening process is generally controlled by Almen intensity and c... more Introduction and objectives Shot peening process is generally controlled by Almen intensity and coverage rate measurements. The results of the shot peening surface treatment depend on the process parameters (type of machine, nozzle, shot type, mass flow, velocity, impact angle) and on the properties of the treated parts (material behaviour, roughness). Previous studies have investigated the control of shot peening via measurement of the global flow characteristics [1, 2, 3]. Developing experimental methods to characterize a particle flux is useful to obtain the contact conditions of the shot peening process (location, velocity vector) on any interesting geometry. Using a high speed camera, this study aims at the analysis of the flux of shots ahead of the nozzle of a shot peening machine. In this study two set of process parameters are investigated: S1: P= 1 bar, D=3 kg/min S2: P= 1 bar, D=13 kg/min Quantitative evolution of the particle velocity and density in the flux is studied.
Uploads
Papers by Jawad Badreddine