Papers by Ronald K Faller
Transportation Research Record, Mar 6, 2023

The objective of this research study was to design and evaluate the MGS long-span design for use ... more The objective of this research study was to design and evaluate the MGS long-span design for use with unsupported spans greater than 25 ft (7.6 m). Two full-scale crash tests were conducted to evaluate the MGS long-span system with increased span lengths and the use of UBSP posts adjacent to the long span. Both tests were conducted according to the TL-3 criteria outlined in MASH. Both test nos. MGSLS-1 and MGSLS-2 were conducted with the 2270P vehicle impacting their respective critical impact points at a speed of 62 mph (100 km/h) and an angle of 25 degrees. Test no. MGSLS-1 was conducted to evaluate the potential for vehicle instability by selecting a critical impact point that maximized the interaction of the front wheel of the pickup truck with the wing wall of the culvert. Test no. MGSLS-2 was designed to evaluate the structural capacity of the system by selecting a critical impact point that maximized the potential for pocketing, wheel snag, and rail rupture. Test no. MGSLS-1 resulted in the vehicle being captured and redirected smoothly by the barrier system with all vehicle decelerations being within the recommended occupant risk limits. Therefore, test no. MGSLS-1 was deemed successful according to the TL-3 safety performance criteria found in MASH. Test no. MGSLS-2 resulted in the vehicle penetrating the barrier and creating multiple detached fragments that could present a safety hazard to oncoming traffic or the occupants of the vehicle. Therefore, test no. MGSLS-2 was deemed unsuccessful according to the TL-3 safety performance criteria. found in MASH.
Transportation Research Board eBooks, Nov 4, 2022

Three full-scale vehicle crash tests were conducted according to the Manual for Assessing Safety ... more Three full-scale vehicle crash tests were conducted according to the Manual for Assessing Safety Hardware (MASH) Test Level 3 (TL-3) safety performance criteria on a transition between the Midwest Guardrail System (MGS) and a portable concrete barrier (PCB) system. The transition system utilized for test nos. MGSPCB-1 through MGSPCB-3 consisted of a standard MGS that overlapped a series of Fshape PCB segments that approached the MGS at a 15H:1V flare. In the overlapped portion of the barrier systems, uniquely-designed blockout holders and a specialized W-beam end shoe mounting bracket were used to connect the systems. In test no. MGSPCB-1, a 5,079-lb (2,304-kg) pickup truck impacted the barrier at 63.2 mph (101.8 km/h) and 25.3 degrees. The barrier captured and redirected the 2270P vehicle, and the vehicle decelerations were within the recommended occupant risk limits. In test no. MGSPCB-2, a 2,601-lb (1,180-kg) car impacted the barrier at 65.1 mph (104.8 km/h) and 24.0 degrees. The barrier captured and redirected the 1100C vehicle, and the vehicle decelerations were within the recommended occupant risk limits. In test no. MGSPCB-3, a 5,177-lb (2,348-kg) pickup truck impacted the barrier at 63.1 mph (101.5 km/h) and 24.6 degrees. For this test, the system was impacted in the reverse direction. The barrier captured and redirected the 2270P vehicle, and the vehicle decelerations were within the recommended occupant risk limits. Based on the results of these successful crash tests, it is believed that the transition design detailed herein represents the first MASH TL-3 crashworthy transition between the MGS and PCBs.
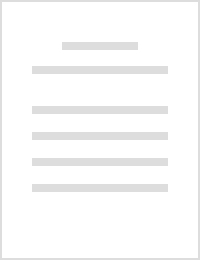
Although curbs have been discouraged on high-speed roads based on previous research, the use of c... more Although curbs have been discouraged on high-speed roads based on previous research, the use of curbs is often required for certain situations. There exists a need to examine the use of curbs in conjunction with the Midwest Guardrail System (MGS) in order to determine effective curb placement guidelines. Four vehicle crash tests were performed to investigate vehicle behaviors after traversing a 152-mm (6-in.) AASHTO Type B curb. Two tests with 2270P pickup trucks, one test with the 1100C passenger car, and one test with the 2000P pickup truck, were performed. All of the vehicles were tested at a target speed of 100 km/h (62.1 mph) and at a target angle of 25 degrees. Test data was collected by both low- and high-speed video cameras and transducers. An analysis was performed on vehicle trajectories with respect to the MGS height to determine the critical lateral offset locations for further investigation within the curb-MGS combination study.
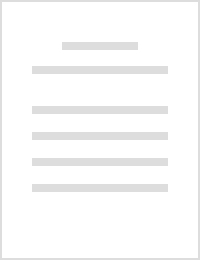
Three full-scale crash tests were performed on the New York Department of Transportation’s (NYSDO... more Three full-scale crash tests were performed on the New York Department of Transportation’s (NYSDOT’s) curved, low-tension, three-cable barrier systems utilizing the MASH Test Level 3 safety performance criteria. The cable barrier system for test no. NYCC-1 was 399.1 ft (121.6 m) long and used a radius of 360 ft (110 m). For test nos. NYCC-2 and NYCC-3, the cable barrier systems were 396.5 ft (120.9 m) long and used radii of 440 ft (134 m). In test nos. NYCC-1 and NYCC-2, the three cables were positioned at heights of 1 ft 3 in. (0.38 m), 1 ft 9 in. (0.53 m), and 2 ft 3 in. (0.69 m). In each of the tests, a 2270P vehicle was used. The first test redirected the pickup truck with all safety performance criteria being satisfied. During the second test, the pickup truck overrode the cable barrier and came to rest behind the system, thus resulting in unacceptable barrier performance. The barrier system was modified using a 2 in. (51 mm) height increase and retested with cables centered at 1 ft 5 in. (0.41 m), 1 ft 11 in.(0.58 m) and 2 ft 5 in. (0.74 m). In the third test, the pickup truck was redirected, and all safety performance criteria were satisfied.
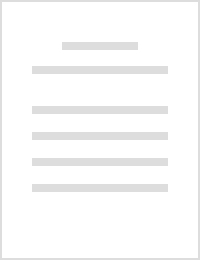
US Transportation Collection2020PDFTech ReportRosenbaugh, Scott K.DeLone, Jacob AFaller, Ronald K... more US Transportation Collection2020PDFTech ReportRosenbaugh, Scott K.DeLone, Jacob AFaller, Ronald K.Bielenberg, Robert W.Midwest Roadside Safety FacilityUniversity of Nebraska--Lincoln. Nebraska Transportation CenterNebraska. Department of TransportationUnited States. Department of Transportation. Federal Highway AdministrationMidwest Roadside Safety FacilityNebraska Transportation CenterNebraskaUnited StatesAcceptance testsBridge decksBridge railingsCrash testsGuardrailsHighway bridgesHighway safetyLow volume roadsSteel structuresComplianceCompliance TestMASH 2016TL-2TL-3Side-MountedW-BeamMGSTRP-03-407-20SPR-1(17)-M098Final Report: 2017 \u2013 2020A new steel bridge rail was developed for use on low-volume bridges. The railing consisted 31-in. tall, 12-gauge W-beam guardrail mounted on S3x5.7 posts, which were supported by steel square-tube sockets attached to the side of the bridge deck. The sockets were to be attached to the steel C-channel that is typically placed along the edges of rural bridge decks in the state of Nebraska. The bridge railing was developed for use on both 7-in. thick cast in place decks and 12-in. thick prestressed concrete beam slabs. Various welded and bolted socket-to-channel attachment designs were evaluated through dynamic bogie testing on both deck types. Posts were impacted both laterally and longitudinally to evaluate the strength of the attachments and the potential for deck damage during vehicle impacts. Upon reviewing the bogie testing results, the project sponsor selected the bolted attachment using embedded coupling nuts and threaded rods as the desired attachment design for full-scale testing. Full-scale crash testing was conducted according to test designation no. 2-11 of the American Association of State Highway Transportation Officials (AASHTO) Manual for Assessing Safety Hardware (MASH 2016). The 2270P vehicle impacted the bridge rail at 25.5 degrees and 44.2 mph and was successfully contained and redirected. Damage to the bridge rail consisted of bent posts and deformed guardrail. No damage to the deck or sockets was observed. Thus, the tests passed all evaluation criteria of MASH 2016 test designation no. 2-11. The new railing was deemed MASH TL-2 crashworthy with a post spacing of 75 in. and MASH TL-3 crashworthy with a post spacing of 37.5 in. BARRIER VII simulations showed that the new railing could be directly connected to the Midwest Guardrail System (MGS) without a transition. Guidance was provided pertaining to the length of guardrail required adjacent to the bridge rail.113
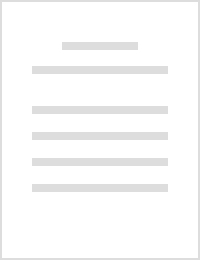
2020PDFTech ReportBielenberg, Robert W.Faller, Ronald K.Jiang, HuaHolloway, James C.Midwest Roads... more 2020PDFTech ReportBielenberg, Robert W.Faller, Ronald K.Jiang, HuaHolloway, James C.Midwest Roadside Safety FacilityNebraska Transportation CenterUniversity of Nebraska--LincolnNew Jersey. Dept. of TransportationCalifornia. Dept. of Transportation. Division of Research, Innovation, and System InformationUnited States. Department of Transportation. Federal Highway AdministrationMidwest Roadside Safety FacilityNebraska Transportation CenterUniversity of Nebraska--LincolnUnited StatesBarriers (Roads)Crash testsThrie beamsHighway safetyCompliance TestMASH 2016Test Level 3 (TL-3)Roadside AppurtenancesModified Thrie Beam (MTB)TRP-03-417-20TPF-5(193) Supplement #132Final Report: 2018 \u2013 2020This report documents the evaluation of the New Jersey Department of Transportation (NJDOT) modified thrie beam (MTB) system in both a single-sided roadside configuration and a dual-sided median configuration under Manual for Assessing Safety Hardware 2016 (MASH 2016) Test-Level 3 (TL-3) criteria. The MTB system was previously tested and approved under National Cooperative Highway Research Program Report No. 350 TL-3 impact conditions. Two full-scale crash tests, test nos. MTB-1 and MTB-2, were conducted according to test designation nos. 3-11 and 3-10, respectively. In test no. MTB-1, a single-sided roadside barrier configuration was constructed using 81-in. long W6x8.5 steel posts at 75-in. post spacing, W14x22 blockouts, and 12-gauge guardrail sections. A 5,003-lb quad cab pickup truck impacted the critical impact point of the system at a speed of 62.9 mph and an angle of 25.4 deg. The test vehicle was satisfactorily captured and smoothly redirected. Therefore, test no. MTB-1 was deemed successful according to MASH 2016 TL-3 safety performance criteria. Test no. MTB-2 was conducted on a dual-sided median barrier configuration of the modified thrie beam. A 2,415-lb small car impacted the critical impact point of the system at a speed of 63.1 mph and an angle of 24.9 deg. The test vehicle was satisfactorily captured and smoothly redirected. Therefore, test no. MTB-2 was deemed successful according to MASH 2016 TL-3 safety performance criteria.112

Transportation Research Board 96th Annual MeetingTransportation Research Board, 2017
Often, road construction causes the need to create a work zone. In these scenarios, portable conc... more Often, road construction causes the need to create a work zone. In these scenarios, portable concrete barriers (PCBs) are typically installed to shield workers and equipment from errant vehicles as well as prevent motorists from striking other roadside hazards. For an existing W-beam guardrail system installed adjacent to the roadway and near the work zone, guardrail sections are removed in order to place the portable concrete barrier system. The focus of this research study was to develop a proper stiffness transition between W-beam guardrail and portable concrete barrier systems. This research effort was accomplished through development and refinement of design concepts using computer simulation with LS-DYNA. Several design concepts were simulated, and design metrics were used to evaluate and refine each concept. These concepts were then analyzed and ranked based on feasibility, likelihood of success, and ease of installation. The rankings were presented to the Technical Advisory Committee (TAC) for selection of a preferred design alternative. Next, a Critical Impact Point (CIP) study was conducted, while additional analyses were performed to determine the critical attachment location and a reduced installation length for the portable concrete barriers. Finally, an additional simulation effort was conducted in order to evaluate the safety performance of the transition system under reverse-direction impact scenarios as well as to select the CIP. Recommendations were also provided for conducting a Phase II study and evaluating the nested MGS configuration using three Test Level 3 (TL-3) full-scale crash tests according to the criteria provided in the Manual for Assessing Safety Hardware, as published by the American Association of Safety Highway and Transportation Officials (AASHTO).

Roadway resurfacing and overlay projects effectively reduce the height of roadside barriers place... more Roadway resurfacing and overlay projects effectively reduce the height of roadside barriers placed adjacent to the roadway, which can negatively affect their crashworthiness. More recently, bridge rails and concrete barriers have been installed with slightly increased heights to account for future overlays. However, adjacent guardrails and approach transitions have not yet been modified to account for overlays. The objective of this project was to develop an increased-height, approach guardrail transition (AGT) to be crashworthy both before and after roadway overlays of up to 3 in. (76 mm). A 34-in. (864-mm) tall, thrie beam transition was designed such that the system would be at its nominal 31-in. (787-mm) height following a 3-in. (76-mm) roadway overlay. Additionally, the upstream end of the AGT incorporated a symmetric Wto-thrie transition segment, which would be replaced by an asymmetric transition segment after an overlay in order to keep the W-beam guardrail upstream from the transition at its nominal 31-in. (787-mm) height. The 34-in. (864-mm) tall AGT was connected to a modified version of the standardized buttress to mitigate the risk of vehicle snag below the rail. The barrier system was evaluated through two full-scale crash tests in accordance with Test Level 3 (TL-3) of the American Association of State Highway Transportation Officials' (AASHTO) Manual for Assessing Safety Hardware (MASH). Both MASH test nos. 3-21 and 3-20 were conducted near the upstream end of the rigid buttress and satisfied all safety performance criteria. Thus, the 34-in. (864-mm) tall AGT with modified transition buttress was determined to be crashworthy to MASH TL-3 standards. Finally, implementation guidance was provided for the increased height AGT and its crashworthy variations.
A full-scale crash test using Manual for Assessing Safety Hardware (MASH) Test Level 3 (TL-3) cri... more A full-scale crash test using Manual for Assessing Safety Hardware (MASH) Test Level 3 (TL-3) criteria was performed on the Midwest Guardrail System (MGS) offset 8 ft (2.44 m) behind a 6-in. (152-mm) high AASHTO Type B curb with a top mounting height of 31 in. (787 mm) relative to the ground [37 in. (940 mm) relative to the roadway]. In the test, the vehicle was contained by the guardrail, but became unstable and rolled over. Analysis of the test revealed that the right-front tire snagged on a post and detached. The right-rear tire of the pickup traversed over the detached tire, causing the rear of the vehicle to pitch upward. The vehicle subsequently became unstable and rolled over. Thus, the MGS offset 8 ft (2.44 mm) behind a 6-in. (152-mm) high curb with a top mounting height of 31 in. (787 mm) was deemed to be unacceptable according to TL-3 of MASH.
Sustainable Civil Infrastructures
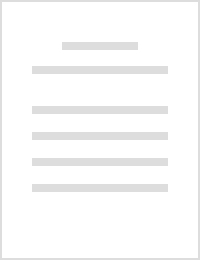
Midwest Roadside Safety Facility, Dec 11, 2019
2019PDFTech ReportStolle, Cody S.Lechtenberg, Karla A.Pajouh, Mojdeh AsadollahiFaller, Ronald K.U... more 2019PDFTech ReportStolle, Cody S.Lechtenberg, Karla A.Pajouh, Mojdeh AsadollahiFaller, Ronald K.Urbank, Erin LMidwest Roadside Safety FacilityNebraska Transportation CenterUniversity of Nebraska--LincolnMidwest States Pooled Fund ProgramNebraska. Department of TransportationUnited States. Department of Transportation. Federal Highway AdministrationMidwest Roadside Safety FacilityNebraska Transportation CenterUniversity of Nebraska--LincolnUnited StatesBracketsCablesCrash testsDesignMedian barriersNuts (Fasteners)PrototypesTension testsHighway safetyRoadside Safety AppurtenancesMASHCable BarrierSleeve NutClosed-Section PostTensile TestingTRP-03-412-19TPF-5(193) Supplement #118Final Report: 2017-2019The Midwest Pooled Fund Program has been developing a prototype of a non-proprietary, high-tension, four-cable, median barrier for use anywhere in a 6H:1V median V-ditch. This system incorporates four evenly-spaced cables, Midwest Weak Posts (MWPs) spaced at 8 to 16 ft (2.4 to 4.9 m) intervals, and a bolted, tabbed bracket to attach the cables to each post. Full-scale crash testing was needed to evaluate the barrier\u2019s safety performance. According to the Manual for Assessing Safety Hardware 2016 (MASH 2016) testing matrix for cable barriers installed within a 6H:1V median V-ditch, a series of eight full-scale crash tests are required to evaluate the safety performance of a system. Previous full-scale tests conducted on this system have indicated potential cable snag on the cable bracket nuts and exposed threaded studs. Cable snagging can limit vertical cable movement and post deflection, which could then lead to significant occupant compartment deformation and penetration, and therefore failed tests. Consequently, new nut designs were investigated for use with the cable brackets in attempt to eliminate cable snagging. Tensile testing was performed on multiple sleeve nut prototypes and all were deemed acceptable.112
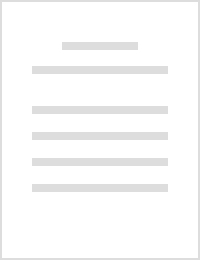
Midwest Roadside Safety Facility, Aug 27, 2020
2020PDFTech ReportRonspies, KellonRosenbaugh, ScottBielenberg, Robert W.Faller, Ronald K.Stolle, ... more 2020PDFTech ReportRonspies, KellonRosenbaugh, ScottBielenberg, Robert W.Faller, Ronald K.Stolle, Cody S.Midwest Roadside Safety FacilityNebraska Transportation CenterUniversity of Nebraska--LincolnMidwest States Pooled Fund ProgramNebraska. Department of TransportationUnited States. Department of Transportation. Federal Highway AdministrationMidwest Roadside Safety FacilityNebraska Transportation CenterUniversity of Nebraska--LincolnUnited StatesCrash testsCrashworthinessCurbsGuardrailsHighway safetyRoadside AppurtenancesCompliance TestMASH 2016Midwest Guardrail System (MGS)CurbTest Level 3 (TL_3)TRP-03-390-20TPF-5 (193) Supplement #106Final Report: 2017-2020The use of curbs along roads is often required for certain functions such as drainage control, right-of-way reduction and sidewalk separation. However, curbs along roadways can adversely affect the interaction of errant vehicles with roadside barriers. Curbs placed near guardrail systems increase the propensity for vehicle override, vehicle underride, vehicle instability, and excessive rail loading during impact events. The Midwest Guardrail System (MGS) installed behind curbs was evaluated under National Cooperative Highway Research Program (NCHRP) Report 350 Test Level 3 (TL-3) criteria but has not been evaluated to American Association of State Highway Transportation Officials (AASHTO) Manual for Assessing Safety Hardware (MASH) TL-3. Test nos. MGSC-7 and MGSC-8 were conducted on the MGS offset by 6 in. behind a 6-in. tall AASHTO Type B curb in accordance with MASH 2016 test designation nos. 3-10 and 3-11, respectively. During test no. MGSC-7, the 1100C vehicle impacted the system at 63.6 mph at an angle of 25.0 degrees and was successfully contained and redirected by the system. The system was rebuilt and tested again according to MASH test designation no. 3-11. In test MGSC-8, the 2270P vehicle impacted the system at 63.4 mph at an angle of 25.7 degrees and was successfully contained and redirected by the system. Upon the successful completion of the two full-scale crash tests, the MGS was deemed crashworthy to MASH 2016 TL-3 when placed within 6 in. behind a curb. Installation guidelines were presented to address implementation of the MGS with curb in various barrier configurations as well as in conjunction with a number of roadside features and special applications.112
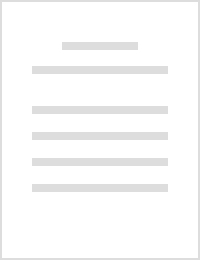
US Transportation Collection2020PDFTech ReportFaller, Ronald K.Rosenbaugh, Scott K.Stolle, Cody S... more US Transportation Collection2020PDFTech ReportFaller, Ronald K.Rosenbaugh, Scott K.Stolle, Cody S.Bielenberg, Robert W.Rasmussen, Jennifer D.Steelman, Joshua S.Holloway, James C.Midwest Roadside Safety FacilityNebraska Transportation CenterUniversity of Nebraska--LincolnMinnesota. Department of TransportationUnited States. Department of Transportation. Federal Highway AdministrationMidwest Roadside Safety FacilityUniversity of Nebraska--LincolnUnited StatesBikewaysBridge railingsCrash testsFootbridgesHighway safetyRoadside AppurtenancesCompliance TestMASH 2016Test Level 3Pedestrian RailConcrete Safety ShapeTRP-03-433-20TPF-5(193) Suppl. #153Final Report: 2019-2020The Minnesota Department of Transportation (MnDOT) desires to use a vehicle, bicycle, and pedestrian combination bridge railing system along pedestrian and bicycle bridge paths. A variation of the MnDOT combination bicycle and pedestrian railing was full-scale crash tested according to the Test Level 3 (TL-3) procedures described in the Manual for Assessing Safety Hardware (MASH 2016). The combination bicycle and pedestrian railing included a 32-in. tall concrete barrier consistent with the MnDOT \u201cJ\u201d-shaped barrier and a steel rail constructed from upper and lower longitudinal rails, welded vertical spindles, and steel posts mounted to the backside of the concrete barrier. Two longitudinal cables were threaded through the longitudinal rail elements and anchored to the backside of the concrete barrier at the upstream and downstream ends. For the tested system, an existing New Jersey (NJ) safety shape concrete barrier was modified for use as a J-shape barrier, and the steel rail was fastened to the back-side face of the barrier using a welded post and plate assembly. In full-scale crash test no. MNPD-3, the system was evaluated according to MASH test designation no. 3-11. The 2014 Dodge Ram 1500 crew cab pickup truck impacted the system 71\ubc in. upstream from the centerline of post no. 4 with a speed of 63.4 mph at an angle of 25.3 degrees. The vehicle was successfully redirected, resulting in minimal plastic deformation to the steel rail and minimal scraping and gouging to the concrete barrier. This bicycle and pedestrian railing system minimized the potential for vehicle snag on the vertical spindles by welding them on the back-side faces of the top and bottom longitudinal tubular rails. The combination railing system was found to meet the AASHTO MASH 2016 TL-3 impact safety criteria.110
Uploads
Papers by Ronald K Faller