Papers by Alireza Bahadorimehr
The effects of diffusion on an exonuclease/nanopore-based DNA sequencing engine J. Chem. Phys. 13... more The effects of diffusion on an exonuclease/nanopore-based DNA sequencing engine J. Chem. Phys. 137, 214903 (2012) Nanogap-based dielectric-specific colocalization for highly sensitive surface plasmon resonance detection of biotin-streptavidin interactions Appl. Phys. Lett. 101, 233701 (2012) Cell electroporation chip using multiple electric field zones in a single channel Appl. Phys. Lett. 101, 223705 (2012) Reactive oxygen species controllable non-thermal helium plasmas for evaluation of plasmid DNA strand breaks
Abstract This paper presents a simple process technique for the fabrication of valveless micro-pu... more Abstract This paper presents a simple process technique for the fabrication of valveless micro-pumps. The process design utilizes standard MEMS process using double-sided anisotropic silicon wet etching process with an additional adhesive bonding technique. The diffuser and nozzle element of the pump with depth of 50 µm, as well as a 150 µm thick silicon membrane are designed and fabricated using only 3 patterning process steps.
This index covers all papers that appeared in IAJIT during 2011. The author's index contains the ... more This index covers all papers that appeared in IAJIT during 2011. The author's index contains the primary entry for each item, listed under the first author's name. The primary entry includes the coauthor's names, the title of the paper, journal abbreviation, month, year, and inclusive pages. The subject's index contains entries describing the item under all appropriate subject headings based on the keywords specified by the authors.
Abstract This paper presents a low cost method for etching of glass based microfluidic devices. M... more Abstract This paper presents a low cost method for etching of glass based microfluidic devices. Microchannels with the depth up to 150 μm were achieved by implementing a photoresist and wet etching process. In particular, a photoresist based mask method is introduced for glass etching which can strongly resist against etchant attacks up to 2 hours, showing high adhesion properties on glass substrate for fabrication of microfluidic microchannels.
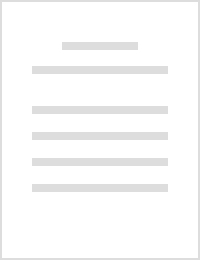
This paper presents a low cost method for fabrication of microchannels on glass substrates for mi... more This paper presents a low cost method for fabrication of microchannels on glass substrates for microfluidic devices applications. The channels with the depth up to 150μm can be achieved by implementing a typical photoresist and wet etching process without any complicated deposition methods such as CVD, evaporation or other sophisticated techniques. In particular, AZ5214 photoresist is for the first time introduced for glass etching mask which can strongly resist against etchant attacks up to 2 hours, showing high accuracy for fabrication of microfluidic microchannels. The width of the channels is determined by the width of the lines in photo-mask design and the etch rate of the substrate because of glass isotropic etching characteristics. In practical the channel width range about 30μm to 350μm is attainable. Commercially available inexpensive microscopic slides have been used as substrate for etching channels using special etchant solutions. The etch rate of the glass strongly depends on the concentration of the etchant Achieving smooth and clear surface after wet etching process is an important factor for easily flowing fluid through channels and monitoring purposes. A mixture of different solutions with special ratios has been applied to achieve smooth and clear surface of the etching regions. Two different bonding techniques, optical UV curable glue, and glass-PDMS-glass methods for adhering the etched glass substrate and non-etched glass cover is applied. A novel method for packaging, tubing and fittings for microfluidic devices using PMMA has been presented without the need for any drilling process.
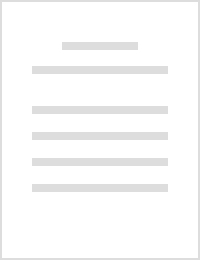
In this paper, an analytical and simulation solution for touch mode Micro-electromechanical syste... more In this paper, an analytical and simulation solution for touch mode Micro-electromechanical systems pressure
sensor operating in harsh environment is proposed. The principle of the paper is to design, obtain analytical solution and
compare the results with the simulation using finite elements analysis for a circular diaphragm deflection before and after
touch point. By looking at MEMS devices, when the diaphragm starts touching the fixed electrode by applying loads, it will
have a major effect on the overall performance of the device. Therefore, one should consider the effect of touch mode in the
system to achieve good linearity, large operating pressure range and large overload protection at output. As of so far the effect
of touch mode has not been evaluated efficiently in the literatures. The proposed touch mode MEMS capacitive pressure sensor
demonstrated diaphragm with radius of 180 µ m , the gap depth of 0.5 µ m and the sensor exhibit a linear response with
pressure from 0.05 Mpa to 2 Mpa.
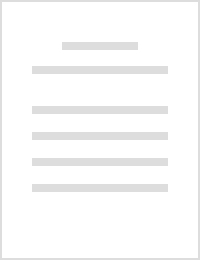
Poly-crystalline silicon carbide (polysic) Micro-electromechanical systems (MEMS) capacitive pres... more Poly-crystalline silicon carbide (polysic) Micro-electromechanical systems (MEMS) capacitive pressure sensors operating at harsh environments (e.g. high temperature) are proposed because of SiC owing excellent electrical stability, mechanical robustness, and chemical inertness properties. The principle of this paper is, design, simulation. The application of SiC pressure sensors are in a harsh environments such as automotive industries, aerospace, oil/logging equipments, nuclear station, power station. The sensor demonstrated a high temperature sensing capability up to 400degC, the device achieves a linear characteristic response and consists of a circular clamped-edges poly-sic diaphragm suspended over sealed cavity on a silicon carbide substrate. The sensor is operating in touch mode capacitive pressure sensor, The advantages of a touch mode are the robust structure that make the sensor to withstand harsh environment, near linear output, and large over-range protection, operating in wide range of pressure, higher sensitivity than the near linear operation in normal mode, so in this case some of stray capacitance effects can be neglected.
This paper presents a nonlinear model for a capacitive Micro-electromechanical accelerometer (MEM... more This paper presents a nonlinear model for a capacitive Micro-electromechanical accelerometer (MEMA). System parameters of the accelerometer are developed using the effect of cubic term of the folded-flexure spring. To solving this equation we use FEA method. The neural network (NN) uses Levenberg-Marquardt (LM) method for training the system to have more accurate response. The designed NN can identify and predict the displacement of movable mass of accelerometer. The simulation results are very promising.
This paper presents a nonlinear model for a capacitive Microelectromechanical accelerometer (MEMA... more This paper presents a nonlinear model for a capacitive Microelectromechanical accelerometer (MEMA). System parameters of the accelerometer are developed using the effect of cubic term of the folded-flexure spring. To solving this equation we use FEA method. The neural network (NN) uses Levenberg-Marquardt (LM) method for training the system to have more accurate response. The designed NN can identify and predict the displacement of movable mass of accelerometer. The simulation results are very promising.
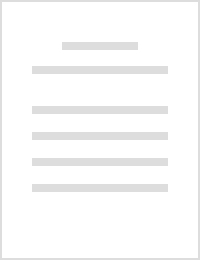
We present a simple and low cost fabrication of Microfluidic mixer using in different... more We present a simple and low cost fabrication of Microfluidic mixer using in different applications in Micro Total Analysis Systems especially for
automated perfusion of multiple solutions to a single cell culture chamber. This device consists of 6 inlets and 2 outlets with additional 3
inlet/outlet channels for flow rate alteration and other mixing purposes such as electrophoresis activation, which is capable of producing mixtures
of the various solutions. The volume of the microchamber is 600 pm³. All the inlets are connected to Polytetrafluoroethylene (PTFE) and silicone
tubings using special Polydimethylsiloxane (PDMS) fittings technique for fluid leakage avoidance. The inputs are controlled by a programmable
micro‐syringe pump in order to activate each input in any sequence of time. Typical microscopic glass slides are utilized as a substrate for
fabrication of microchannels and chamber which has the minimum effect on most of biology samples. The same un‐etched glass is used as cover
glass for bonding purposes. Using photoresist as an etch mask instead of some deposition methods makes the procedure more convenient and cost
effective compared to other expensive techniques such as Deep reactive‐ion etching (DRIE), laser, etc. The baking time of photoresist is a critical
factor for longer resistance against etchant solution which is optimized by this method. In addition the etchant concentration in wet etching process
is discussed to achieve a decent surface and wall characteristics for bio‐applications. A smooth channel surface with acceptable sharp wall edges
makes this procedure suitable for many applications which vertical walls are not crucial. Different dye samples are tested inside the chamber and
promising results attained. The mixing validation is performed using image processing technique.
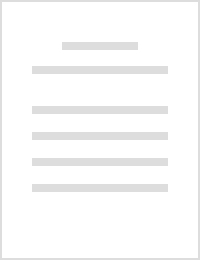
In this paper an automated control system of thick film resistive heater for gas sensor applicati... more In this paper an automated control system of thick film resistive heater for gas sensor applications has been designed using low cost technologies. To control the desired temperature of heater, a programmable voltage with 12 bits resolution applies which can be adjusted to the appropriate temperature. The circuit consists of ADC, DAC, microcontroller, and current buffer. This circuit compensates dropt voltage across the heater which has been resulted from the ambient temperature changes. In particular, using one microcontroller for entire heater process is for the first time introduced to drive the heater, control heater temperature, and compensate ambient temperature of heater all together automatically. Fabrication of this circuit using commercially available technologies and simplicity of the circuit make it a novel and simple design in gas sensor applications. This circuit has the ability to connect to alarms and computers in order to monitoring purposes.
This paper presents an analysis on the design of coupled coil. The coil platform that has been de... more This paper presents an analysis on the design of coupled coil. The coil platform that has been developed is a single layer coil structure on the planar surface of the substrate, the structure offers an integrated solution for customizable application due to its compact and small size. The design of the spiral coil has been analysed using field solver analysis ASITIC. As a demonstration of the usefulness of such analysis, a coupled coil is fabricated on a glass substrate and measured at frequency range between 50 MHz and 800 MHz. A coupling factor of about 0.7 and self inductance of 12.7 nH were achieved which show a good agreement with the simulation.
Microfluidic systems are one of the new growing technologies which offer miniaturization of analy... more Microfluidic systems are one of the new growing technologies which offer miniaturization of analysis systems. In this paper we present a simple and low cost fabrication of microchannels using in different applications in Micro Total Analysis Systems. This method uses typical microscopic glass slides as a substrate for fabrication of microchannels. Using photo-resist as a mask instead of some deposition methods makes the procedure more convenient and cost effective compare to other techniques. A smooth channel surface with acceptable sharp wall edges makes this procedure suitable for so many applications that vertical walls are not crucial. The comparison between fabrication of channels using wet etching procedures and molding techniques can help to select the more suitable one for any application which needs specific characteristics.
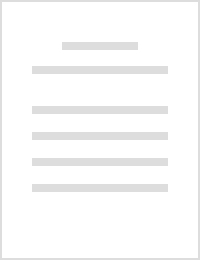
In this paper, Poly-crystalline silicon carbide (poly-sic) Micro-electromechanical systems (MEMS)... more In this paper, Poly-crystalline silicon carbide (poly-sic) Micro-electromechanical systems (MEMS) capacitive pressure sensor operating in harsh environment in touch mode is proposed, The principle of the paper is to design, obtain analytical solution and compare the results with the simulation for a circular diaphragm deflection before and after touch point. The sensor demonstrated a high temperature sensing capability up to 400° C, the device achieves a linear characteristic response and consists of a circular clamped-edges poly-sic diaphragm suspended over sealed cavity on a silicon carbide substrate. The sensor is operating in touch mode capacitive pressure sensor, The advantages of a touch mode are the robust structure that make the sensor to withstand harsh environment, near linear output, and large over-range protection, operating in wide range of pressure, higher sensitivity than the near linear operation in normal mode, The material is considered to be used for harsh environment is SiC (Silicon Carbide), Because of SiC owing excellent electrical stability, mechanical robustness, and chemical inertness properties and the application of pressure sensors in harsh environments are, such as automotive industries, aerospace, oil/logging equipments, nuclear station, and power station. We are simulating MEMS capacitive pressure sensor to optimize the design, improve the performance and reduce the time of fabricating process of the device. The proposed touch mode MEMS capacitive pressure sensor demonstrated diaphragm ranging from 150µm to 360µmin diameter, with the gap depth from 0.5µm to 7.5µmand the sensor exhibit a linear response with pressure from 0.05 Mpa to 10 Mpa.
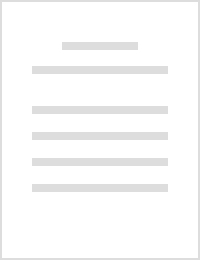
In this paper, we present a simple, rapid, and low-cost procedure for fabricating micro-nozzles a... more In this paper, we present a simple, rapid, and low-cost procedure for fabricating micro-nozzles and micro-diffusers using in microfluidic devices to control the flow of the fluid which pass through the microchannels. This procedure uses commercially accessible and typical materials, which is used in several applications in microelectronic labs. Glass is used as main substrate to get advantages of photo transparent specifications of this material. In this method a thick layer of positive photoresist on the glass substrate for fabrication of lens is utilized. A mild BOE solution with additional HCL is employed to achieve an excellent etching quality and a smoother etched surface. The depth of the surface can be reach to 100 μm without PR damage effect after 1 hour of etching process. The aluminum evaporation process produces a thin layer of aluminum across the substrate which makes it as a block against passing the light. Dispensing SU-8 on Al layer and using UV back-exposure technique the tapered structured is fabricated as a mold for PDMS which can be used in different microfluidic applications. The simulation results shows that the focal length up to 800 μm with the lens curvature of 150 μm is achievable.
MEMS offer different fabrication process to fabricate diaphragms in various applications such as ... more MEMS offer different fabrication process to fabricate diaphragms in various applications such as microphones, pressure sensors and micro-pumps, etc. The working principle of all these devices is based on the force applies on the one side of the diaphragm and cause the diaphragm deflects. The parameter optimization of diaphragm is the prime challenge due to achieve the best performance of the device. In this paper Displacement, Stress and Vibration analysis which affect on the operation of the diaphragm under pressures is considered. The different shapes of diaphragms (square, rectangular and circular shapes) are also play a significant role in operation in different applications. The purpose of this research is to design a framework to show which kind of diaphragm with what kind of parameters can be chosen for specific MEMS devices.
Uploads
Papers by Alireza Bahadorimehr
sensor operating in harsh environment is proposed. The principle of the paper is to design, obtain analytical solution and
compare the results with the simulation using finite elements analysis for a circular diaphragm deflection before and after
touch point. By looking at MEMS devices, when the diaphragm starts touching the fixed electrode by applying loads, it will
have a major effect on the overall performance of the device. Therefore, one should consider the effect of touch mode in the
system to achieve good linearity, large operating pressure range and large overload protection at output. As of so far the effect
of touch mode has not been evaluated efficiently in the literatures. The proposed touch mode MEMS capacitive pressure sensor
demonstrated diaphragm with radius of 180 µ m , the gap depth of 0.5 µ m and the sensor exhibit a linear response with
pressure from 0.05 Mpa to 2 Mpa.
automated perfusion of multiple solutions to a single cell culture chamber. This device consists of 6 inlets and 2 outlets with additional 3
inlet/outlet channels for flow rate alteration and other mixing purposes such as electrophoresis activation, which is capable of producing mixtures
of the various solutions. The volume of the microchamber is 600 pm³. All the inlets are connected to Polytetrafluoroethylene (PTFE) and silicone
tubings using special Polydimethylsiloxane (PDMS) fittings technique for fluid leakage avoidance. The inputs are controlled by a programmable
micro‐syringe pump in order to activate each input in any sequence of time. Typical microscopic glass slides are utilized as a substrate for
fabrication of microchannels and chamber which has the minimum effect on most of biology samples. The same un‐etched glass is used as cover
glass for bonding purposes. Using photoresist as an etch mask instead of some deposition methods makes the procedure more convenient and cost
effective compared to other expensive techniques such as Deep reactive‐ion etching (DRIE), laser, etc. The baking time of photoresist is a critical
factor for longer resistance against etchant solution which is optimized by this method. In addition the etchant concentration in wet etching process
is discussed to achieve a decent surface and wall characteristics for bio‐applications. A smooth channel surface with acceptable sharp wall edges
makes this procedure suitable for many applications which vertical walls are not crucial. Different dye samples are tested inside the chamber and
promising results attained. The mixing validation is performed using image processing technique.
sensor operating in harsh environment is proposed. The principle of the paper is to design, obtain analytical solution and
compare the results with the simulation using finite elements analysis for a circular diaphragm deflection before and after
touch point. By looking at MEMS devices, when the diaphragm starts touching the fixed electrode by applying loads, it will
have a major effect on the overall performance of the device. Therefore, one should consider the effect of touch mode in the
system to achieve good linearity, large operating pressure range and large overload protection at output. As of so far the effect
of touch mode has not been evaluated efficiently in the literatures. The proposed touch mode MEMS capacitive pressure sensor
demonstrated diaphragm with radius of 180 µ m , the gap depth of 0.5 µ m and the sensor exhibit a linear response with
pressure from 0.05 Mpa to 2 Mpa.
automated perfusion of multiple solutions to a single cell culture chamber. This device consists of 6 inlets and 2 outlets with additional 3
inlet/outlet channels for flow rate alteration and other mixing purposes such as electrophoresis activation, which is capable of producing mixtures
of the various solutions. The volume of the microchamber is 600 pm³. All the inlets are connected to Polytetrafluoroethylene (PTFE) and silicone
tubings using special Polydimethylsiloxane (PDMS) fittings technique for fluid leakage avoidance. The inputs are controlled by a programmable
micro‐syringe pump in order to activate each input in any sequence of time. Typical microscopic glass slides are utilized as a substrate for
fabrication of microchannels and chamber which has the minimum effect on most of biology samples. The same un‐etched glass is used as cover
glass for bonding purposes. Using photoresist as an etch mask instead of some deposition methods makes the procedure more convenient and cost
effective compared to other expensive techniques such as Deep reactive‐ion etching (DRIE), laser, etc. The baking time of photoresist is a critical
factor for longer resistance against etchant solution which is optimized by this method. In addition the etchant concentration in wet etching process
is discussed to achieve a decent surface and wall characteristics for bio‐applications. A smooth channel surface with acceptable sharp wall edges
makes this procedure suitable for many applications which vertical walls are not crucial. Different dye samples are tested inside the chamber and
promising results attained. The mixing validation is performed using image processing technique.