Papers by Naumenko Alex
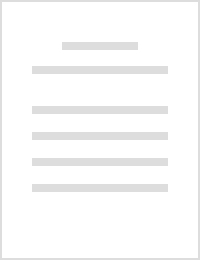
AIP Conference Proceedings
The paper deals with the challenges of the machinery vibroacoustic signal modeling. The purpose o... more The paper deals with the challenges of the machinery vibroacoustic signal modeling. The purpose of this paper is to form a phenomenological model for the structure of vibroacoustic oscillations and signals appeared in case of malfunctions and defects. It presents particular structural models for vibroacoustic signals of some reciprocating machine malfunctions. Mathematical description of the vibroacoustic signal reveals the informative parameters of the malfunction diagnostic signs. The model enables us to define in detail the informative vibroacoustic signal parameters. The model also allows us to select the diagnostic signs of the given malfunctions and defects in certain machine parts and components. At the same time, it is considered that the signal is received in certain points on the machine taking into account the excitation sources, conditioning channel and propagation of the vibroacoustic oscillations. The model has been constructed considering the presence and interaction of the three main sources of excitation of the asset vibroacoustic oscillations, which are identified by the types of excited oscillations. It is assumed that there are damped natural, undamped induced, random broadband and narrowband vibrations. The parameters of the vibroacoustic signal structural model also take into account the properties of converting the vibroacoustic oscillation to the vibroacoustic signal by means of a piezoelectric sensor. The model shows that the vibroacoustic signal has not only the components from each source, but their mutually modulated components. We developed partial models for mechanisms of structuring the vibroacoustic signal appeared in case of malfunctions and defects in rotating parts and couplings, machine shaft and drive shaft misalignment, increased clearances and other defects and failures of the rotating and reciprocating parts and components. The proposed phenomenological structural models of the vibroacoustic signals appeared in case of malfunctions of reciprocating machines show that for the diagnostic purposes it is necessary to analyze vibroacoustic signals either in the time domain according to the cyclogram of the reciprocating machine operation or in the envelope spectrum at characteristic frequencies or the noise component. In the event of defects and malfunctions in the centrifugal rotating parts and components, there are excited the vibroacoustic signals, which are advisable to analyze in the direct spectrum or in the spectrum of the noise component envelope. The proposed models enable us to select and form scientifically grounded systems of the machine failure diagnostic signs.
Journal of Physics: Conference Series
Proceding 22nd International Congress Condition Monitoring and Diagnostic Engineer Condition Management, 2009
Places and the reasons of refusals of the reciprocating compressors applied, mainly, for compress... more Places and the reasons of refusals of the reciprocating compressors applied, mainly, for compression of gases, containing hydrogen are analysed. Various methods of monitoring and diagnostics of a technical condition of compressors also are subjected to the analysis. Efficiency of a vibroacoustic method of diagnostics is shown high in comparison with others. The system of condition monitoring of reciprocating machines COMPACS is described.
Неразрушающий контроль и техническая диагностика в промышленности. 8-я Международная конференция. Москва, 18–20 марта 2009 г. , 2009
Степень обеспечения безопасной и безаварийной эксплуатации поршневых компрессоров (ПК) опасных пр... more Степень обеспечения безопасной и безаварийной эксплуатации поршневых компрессоров (ПК) опасных производственных объектов (ОПО) неразрывно связано с развитием методо-логии и средств диагностирования и мониторинга технического состояния машин и меха-низмов возвратно-поступательного действия. Поэтому разработка методологии и техноло-гии диагностирования и мониторинга ПК, в частности, методами виброакустической (ВА) диагностики, а также алгоритмов для автоматических систем диагностики и мониторинга (СДМ) ПК, обеспечивающих безаварийную их эксплуатацию, является актуальной проблемой.
articles by Naumenko Alex
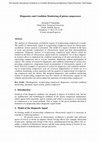
7th International Conference on Condition Monitoring and Machinery Failure Prevention Technologies 2010, CM 2010/MFPT 2010, 2010
The analysis of vibroacoustic oscillations sources of reciprocating compressors is made.
The mod... more The analysis of vibroacoustic oscillations sources of reciprocating compressors is made.
The model of vibroacoustic signal of reciprocating compressor based on vibroacoustic oscillations sources analysis is presented. The model of a signal is formed on the basis of noise and periodic components of vibroacoustic signal and their intermodulation component. Diagnostic features of reciprocating compressor units’ defects which are formed on the basis of vibroacoustic signal model are considered. Use of these diagnostic features allows to implement the condition monitoring of all units and details of a reciprocating compressor and to execute automatic diagnosing without participation of experts. The scheme of system for diagnostics and condition monitoring of various reciprocating compressors components based on parameters of vibroacoustic signals is offered.
Practical examples of operation of system for diagnostics and condition monitoring of reciprocating compressors state are reviewed. Opportunities of results use of a condition monitoring system operation with the purpose of improvement of reciprocating compressor state are shown. The designed diagnostics and condition monitoring system of reciprocating compressors uses five sensors of vibroacoustic signals on one cylinder and provides safe and accident-free operation of reciprocating compressors.
Key words: vibrodiagnostic, reciprocating compressor, diagnostics, real-time condition
monitoring, automatic expert system, piston compressor
8th International Conference on Condition Monitoring and Machinery Failure Prevention Technologies 2011, CM 2011/MFPT 2011, 2011
The paper is devoted to the current development and prospect development of modern
methods and m... more The paper is devoted to the current development and prospect development of modern
methods and means of condition monitoring and diagnostics of reciprocating
compressors in hazardous industries. The principles of condition control presented in
monitoring systems have been studied. Technology of condition monitoring systems
was examined.
Methodology, implementation technology and principles of construction of real-time
condition monitoring systems have been analyzed. The COMPACS system of real-time
condition monitoring of reciprocating compressors have been considered.
Keywords: reciprocators, reciprocating compressors, monitoring, diagnostics, vibration
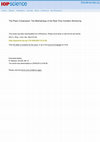
Journal of Physics: Conference Series, 2012
The methodology of a diagnostic signal processing, a function chart of the monitoring system are ... more The methodology of a diagnostic signal processing, a function chart of the monitoring system are considered in the article. The methodology of monitoring and diagnosing is based on measurement of indirect processes' parameters (vibroacoustic oscillations) therefore no more than five sensors is established on the cylinder, measurement of direct structural and thermodynamic parameters is envisioned as well. The structure and principle of expert system's functioning of decision-making is given. Algorithm of automatic expert system includes the calculation diagnostic attributes values based on their normative values, formation sets of diagnostic attributes that correspond to individual classes to malfunction, formation of expert system messages. The scheme of a real-time condition monitoring system for piston compressors is considered. The system have consistently-parallel structure of information-measuring equipment, which allows to measure the vibroacoustic signal for condition monitoring of reciprocating compressors and modes of its work. Besides, the system allows to measure parameters of other physical processes, for example, system can measure and use for monitoring and statements of the diagnosis the pressure in decreasing spaces (the indicator diagram), the inlet pressure and flowing pressure of each cylinder, inlet and delivery temperature of gas, valves temperature, position of a rod, leakage through compression packing and others.
9th International Conference on Condition Monitoring and Machinery Failure Prevention Technologies 2012, CM 2012 and MFPT 2012, 2012
The fundamental causes of operational problems of potentially dangerous and critical objects are ... more The fundamental causes of operational problems of potentially dangerous and critical objects are low objectivity of the technical condition evaluation and low observability of hidden degradation processes of technical state of these objects, flowing due to wear and inadequate actions of technological, servicing and repair personnel. These problems can be solved on the basis of results of technical condition monitoring of the objects in real-time. On the basis of the existing normative and scientific-methodical documents the goals and objectives of monitoring are formulated and their solutions are pointed. The complex real
time condition monitoring system is presented.
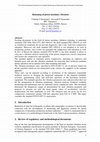
10th International Conference on Condition Monitoring and Machinery Failure Prevention Technologies 2013, CM 2013 and MFPT 2013, 2013
Existing documents in the field of piston machines vibration rationing, in particular standards V... more Existing documents in the field of piston machines vibration rationing, in particular standards VDI 2056, ISO 2372, ISO 10816-6, the draft standard ISO 10816-8, as well as commercial standards, do not provide diagnostics and a safe, fault free compressors operation. Moreover, the draft standard ISO 10816-8 is not intended to be used in monitoring systems, since it does not guarantee the compressors safe operation as well. In 2011 in Russia the industry standard STO 03-007-11 has been adopted; it allows to carry out a vibration analysis monitoring of the piston compressors crucial components and ensures the compressors safe operation.
The standard applies to stationary piston compressors, operating on explosive and harmful gases and sets the vibration standards for assessing their technical condition during operation and acceptance tests after mounting and repair.
The vibration parameters rates, specified in STO 03-007-11, are of advisory nature for all the machines which are not enumerated in the vehicles list, supplied in the standard appendix. These rates can be adjusted according to resolutions of the enterprise responsible technical services as bringing the diagnosed equipment to the required reliability activities, guaranteeing safety and fault-free operation of the hazardous facilities equipment. The standard specifies the vibration parameters rates and prescribes their use for the arrangement of vibration monitoring, vibration analysis, technical condition monitoring and operational risks for stationary piston compressor units. This document determines the frequencies ranges of measurement for each vibration parameter and proposes to measure not only the mean square values of acceleration, velocity, displacement, but their amplitudes as well. The vibration rates are given for the five compressors constructive groups with unit capacities from 0,02 to 2 MW. The paper considers the standard STO 03-007-11 main points.
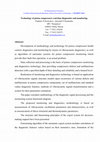
11th International Conference on Condition Monitoring and Machinery Failure Prevention Technologies, CM 2014 / MFPT 2014, 2014
Development of methodology and technology for piston compressors health control, diagnostics and ... more Development of methodology and technology for piston compressors health control, diagnostics and monitoring by means of vibroacoustic diagnostics, as well as algorithms of automatic systems for piston compressors monitoring which provide their fault-free operation, is an actual problem.
Data collection and processing is the basis of piston compressors monitoring and diagnostics technology, thus providing compressors defects and malfunctions detection with a specified depth of their detailing and reliability and a hazard level.
Realization of monitoring and diagnostics technology is based on application of vibroacoustic signals structure models upon occurrence of various defects and malfunctions in piston compressors components, set of malfunctions and standard values diagnostic features, methods of vibroacoustic signals transformation and a system for their parameters estimation.
The paper considers methodology of the diagnostic signal processing and the monitoring system functional diagram.
The proposed monitoring and diagnostics methodology is based on measurement of vibroacoustic oscillations parameters and characteristics, as well as measurement of direct structural and thermodynamic parameters.
The structure and functioning principles of the expert system for decision making support have been presented.
Functioning algorithm of the automatic expert system includes calculation of the diagnostic features values based on their normative ones, formation of the diagnostic features sets which correspond to individual malfunctions classes and formation of the expert system messages.
The scheme of the system for piston compressors real-time health monitoring has been considered.
The system has a series-parallel structure of a data-measuring complex for data collection and processing, which allows to measure the vibroacoustic signals parameters for piston compressors and their operating modes monitoring. Besides,
the system allows to measure other physical processes parameters, for example, for
monitoring and diagnosis-making purposes it has been provided to measure and apply pressure in decreasing spaces (an indicator diagram), gas temperature, a rod position, leakage through stuffing boxes and others.
Procedia Engineering, 2015
The current Russian and the International standards in the field of standardizing parameters for ... more The current Russian and the International standards in the field of standardizing parameters for piston machines vibration including piston compressors are reviewed. It is shown that the current standards do not meet safe operation requirements for piston compressors of hazardous production facilities. The Article describes the national standard of the Russian Federation "Condition monitoring and diagnostics of machines. Condition monitoring of hazardous industries. Vibration of stationary reciprocating compressor".
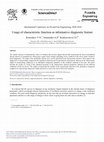
Procedia Engineering Volume 152, 2016, Pages 521-526, 2016
The statistic analysis of instantaneous values of vibration and acoustic signals showed that in p... more The statistic analysis of instantaneous values of vibration and acoustic signals showed that in particular the form of probability density function of instantaneous vibroacoustic signal values changes depending on the condition of the device under vibrationbased diagnostics. The shape of the probability density curve can be described by the characteristic function. With regard to the diagnostics of reciprocating compressors the hypothesis had been put forward that the characteristic function of the vibroacoustic signal of reciprocating compressor is an informative diagnostic parameter of the technical condition of the unit. The article presents the results of a study of the statistical moments of the characteristic function parameters obtained for the different conditions of the test device. The studies revealed that the module of the characteristic function is the informative diagnostic symptom of reciprocating compressors faults and allows to assess the state of their units and parts.
Advances in Technology to Support End User Mission - Proceedings of the 2016 Joint Conference/Symposium of the Society for Machinery Failure Prevention Technology and the International Society of Automation, 2016
The current Russian and the International standards in the field of standardizing parameters for ... more The current Russian and the International standards in the field of standardizing parameters for piston machines vibration including piston compressors are reviewed. It is shown that the current standards do not meet safe operation requirements for piston compressors of hazardous production facilities. The Article describes the national standard of the Russian Federation "Condition monitoring and diagnostics of machines. Condition monitoring of hazardous industries. Vibration of stationary reciprocating compressor".
13th International Conference on Condition Monitoring and Machinery Failure Prevention Technologies, CM 2016/MFPT 2016, 2016
The article considers the possibility of using the statistical characteristics – both numeric and... more The article considers the possibility of using the statistical characteristics – both numeric and functional - for the vibration processes assessment. The research revealed that the usage of an area under curve of module of characteristic function of the instantaneous values of vibroacoustic signals for different assemblies and mechanisms as a diagnostic sign and forming the vector of diagnostic signs on its basis make possible to suggest a fundamentally new diagnostic parameter that is invariant to the design of the machine and the parameter’s limiting values. The parameter application allows to increase the reliability of diagnostic results and, at the same time, to simplify the diagnostic algorithms.
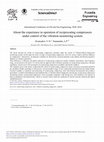
Procedia Engineering Volume 152, 2016, Pages 497-504, 2016
The article presents the results of reciprocating compressors operation under the control of Vibr... more The article presents the results of reciprocating compressors operation under the control of Vibration-Based Diagnostics monitoring systems, dwells upon the issues of usage of reciprocating compressors valves by various vendors and their influence
on compressors’ vibroactivity. An adequate evaluation of vibroactivity of piston machines is provided by the Russian regulative database on vibration parameters.
Main differences of Russian and global methods of reciprocating compressors health evaluation, particularly, used frequency range, are presented in the article. It is shown that the approach laid in Russian standards on reciprocating compressors vibration regulations, ensures true-to-life assessment of reciprocating compressors assemblies and details condition.
The examples given in the article confirm that the criteria of reciprocating compressors repair correctness assessment should be the machinery health, including its vibroactivity, not just mindless usage of new components purchased from the global brands.
Practical examples of operation and monitoring of reciprocating compressors show that Russian developments and products,
particularly, scientific-methodological and standards base of Vibration-Based Diagnostics monitoring, reciprocating compressors monitoring systems, reciprocating compressors valves are highly competitive with foreign ones, and sometimes even superior to them in parameters and characteristics, which is a positive factor under the conditions of current economic situation and import substitution policy.
WCCM 2017 - 1st World Congress on Condition Monitoring 2017, 2017
The article considers the issues of using different physical processes parameters in systems for ... more The article considers the issues of using different physical processes parameters in systems for real-time condition monitoring of reciprocating compressors. The locations for sensors of absolute and relative vibration are defined. Trends of parameters of absolute and relative vibration at emergence of malfunctions and defects are given. Examples of diagnosing of reciprocating compressors in parameters of relative and absolute vibration are reviewed. It is shown that real-time monitoring of the absolute vibration parameters and the relative position of rod provides observability of the piston compressors’ condition and, consequently, their safe operation.
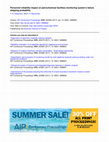
AIP Conference Proceedings, 2017
The paper dwells upon urgent issues of evaluating impact of actions conducted by complex technolo... more The paper dwells upon urgent issues of evaluating impact of actions conducted by complex technological systems operators on their safe operation considering application of condition monitoring systems for elements and subsystems of petrochemical production facilities. The main task for the research is to distinguish factors and criteria of monitoring system properties description, which would allow to evaluate impact of errors made by personnel on operation of real-time condition monitoring and diagnostic systems for machinery of petrochemical facilities, and find and objective criteria for monitoring system class, considering a human factor. On the basis of real-time condition monitoring concepts of sudden failure skipping risk, static and dynamic error, monitoring systems, one may solve a task of evaluation of impact that personnel’s qualification has on monitoring system operation in terms of error in personnel or operators’ actions while receiving information from monitoring systems and operating a technological system.
Operator is considered as a part of the technological system. Although, personnel’s behavior is usually a combination of the following parameters: input signal - information perceiving, reaction – decision making, response – decision implementing. Based on several researches on behavior of nuclear powers station operators in USA, Italy and other countries, as well as on researches conducted by Russian scientists, required data on operator’s reliability were selected for analysis of operator’s behavior at technological facilities diagnostics and monitoring systems. The calculations revealed that for the monitoring system selected as an example, the failure skipping risk for the set values of static (less than 0.01) and dynamic (less than 0.001) errors considering all related factors of data on reliability of information perception, decision-making, and reaction fulfilled is 0.037, in case when all the facilities and error probability are under control – not more than 0.027. In case when only pump and compressor units are under control, the failure skipping risk is not more than 0.022, when the probability of error in operator’s action is not more than 0.011. The work output shows that on the basis of the researches results an assessment of operators’ reliability can be made in terms of almost any kind of production, but considering only technological capabilities, since operators’ psychological and general training considerable vary in different production industries. Using latest technologies of engineering psychology and design of data support systems, situation assessment systems, decision-making and responding system, as well as achievement in condition monitoring in various production industries one can evaluate hazardous condition skipping risk probability considering static, dynamic errors and human factor.
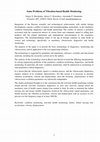
15th International Conference on Condition Monitoring and Machinery Failure Prevention Technologies, CM 2018/MFPT 2018, 2018
Integration of the Russian scientific and technological achievements with similar foreign develop... more Integration of the Russian scientific and technological achievements with similar foreign developments caused a conflict of interest and misunderstanding, particularly, in the machinery condition monitoring, diagnostics and health monitoring. The conflict of interest is primarily associated with the commercial interest of certain firms and companies aimed at selling their products and the related intentional and unintentional misconception in the machinery diagnostics. The misunderstanding relates to the lag of foreign countries in some fields of science and technology, specifically, in machinery vibroacoustic diagnostics and health monitoring.
The purpose of the paper is to present the basic terminology of diagnostics, monitoring and vibroacoustics and its application to the real engineering solutions.
The terminology is suggested by guidelines and regulations, reference, scientific and educational materials, including the researches carried out by the authors.
The analysis of the terminology used in Russia and abroad revealed the differing interpretations in solving engineering problems of the machinery condition monitoring, diagnostics, and health monitoring. In particular, the term “condition monitoring” shall be understood as monitoring of state parameters without diagnostics.
It is shown that the vibroacoustic signal is a random process, and the vibroacoustic diagnostics requires analysis of its stochastic characteristics. For this reason, it is necessary to measure vibration acceleration, velocity and displacement, since the stochastic characteristics of these vibroacoustic oscillation parameters are statistically independent.
The studies performed brought us to the conclusion that the real-time health monitoring systems should provide real-time machinery diagnostics at such time intervals, during which the machinery state of health cannot change from normal to limit. In order to minimize the failure missing risk and ensure reliable diagnostics based-on the vibroacoustic signal parameters, one should measure the vibration acceleration, velocity and displacement with an accuracy of few percent over the frequency range of at least 3000 Hz.
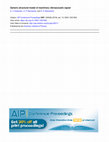
AIP Conference Proceedings 2007, 050008 (2018), 2018
The paper deals with the challenges of the machinery vibroacoustic signal modeling. The purpose o... more The paper deals with the challenges of the machinery vibroacoustic signal modeling. The purpose of this paper is to form a phenomenological model for the structure of vibroacoustic oscillations and signals appeared in case of malfunctions and defects. It presents particular structural models for vibroacoustic signals of some reciprocating machine malfunctions. Mathematical description of the vibroacoustic signal reveals the informative parameters of the malfunction diagnostic signs. The model enables us to define in detail the informative vibroacoustic signal parameters. The model also allows us to select the diagnostic signs of the given malfunctions and defects in certain machine parts and components. At the same time, it is considered that the signal is received in certain points on the machine taking into account the excitation sources, conditioning channel and propagation of the vibroacoustic oscillations. The model has been constructed considering the presence and interaction of the three main sources of excitation of the asset vibroacoustic oscillations, which are identified by the types of excited oscillations. It is assumed that there are damped natural, undamped induced, random broadband and narrowband vibrations. The parameters of the vibroacoustic signal structural model also take into account the properties of converting the vibroacoustic oscillation to the vibroacoustic signal by means of a piezoelectric sensor. The model shows that the vibroacoustic signal has not only the components from each source, but their mutually modulated components. We developed partial models for mechanisms of structuring the vibroacoustic signal appeared in case of malfunctions and defects in rotating parts and couplings, machine shaft and drive shaft misalignment, increased clearances and other defects and failures of the rotating and reciprocating parts and components. The proposed phenomenological structural models of the vibroacoustic signals appeared in case of
malfunctions of reciprocating machines show that for the diagnostic purposes it is necessary to analyze vibroacoustic signals either in the time domain according to the cyclogram of the reciprocating machine operation or in the envelope spectrum at characteristic frequencies or the noise component. In the event of defects and malfunctions in the centrifugal rotating parts and components, there are excited the vibroacoustic signals, which are advisable to analyze in the direct spectrum or in the spectrum of the noise component envelope. The proposed models enable us to select and form scientifically grounded systems of the machine failure diagnostic signs.
Uploads
Papers by Naumenko Alex
articles by Naumenko Alex
The model of vibroacoustic signal of reciprocating compressor based on vibroacoustic oscillations sources analysis is presented. The model of a signal is formed on the basis of noise and periodic components of vibroacoustic signal and their intermodulation component. Diagnostic features of reciprocating compressor units’ defects which are formed on the basis of vibroacoustic signal model are considered. Use of these diagnostic features allows to implement the condition monitoring of all units and details of a reciprocating compressor and to execute automatic diagnosing without participation of experts. The scheme of system for diagnostics and condition monitoring of various reciprocating compressors components based on parameters of vibroacoustic signals is offered.
Practical examples of operation of system for diagnostics and condition monitoring of reciprocating compressors state are reviewed. Opportunities of results use of a condition monitoring system operation with the purpose of improvement of reciprocating compressor state are shown. The designed diagnostics and condition monitoring system of reciprocating compressors uses five sensors of vibroacoustic signals on one cylinder and provides safe and accident-free operation of reciprocating compressors.
Key words: vibrodiagnostic, reciprocating compressor, diagnostics, real-time condition
monitoring, automatic expert system, piston compressor
methods and means of condition monitoring and diagnostics of reciprocating
compressors in hazardous industries. The principles of condition control presented in
monitoring systems have been studied. Technology of condition monitoring systems
was examined.
Methodology, implementation technology and principles of construction of real-time
condition monitoring systems have been analyzed. The COMPACS system of real-time
condition monitoring of reciprocating compressors have been considered.
Keywords: reciprocators, reciprocating compressors, monitoring, diagnostics, vibration
time condition monitoring system is presented.
The standard applies to stationary piston compressors, operating on explosive and harmful gases and sets the vibration standards for assessing their technical condition during operation and acceptance tests after mounting and repair.
The vibration parameters rates, specified in STO 03-007-11, are of advisory nature for all the machines which are not enumerated in the vehicles list, supplied in the standard appendix. These rates can be adjusted according to resolutions of the enterprise responsible technical services as bringing the diagnosed equipment to the required reliability activities, guaranteeing safety and fault-free operation of the hazardous facilities equipment. The standard specifies the vibration parameters rates and prescribes their use for the arrangement of vibration monitoring, vibration analysis, technical condition monitoring and operational risks for stationary piston compressor units. This document determines the frequencies ranges of measurement for each vibration parameter and proposes to measure not only the mean square values of acceleration, velocity, displacement, but their amplitudes as well. The vibration rates are given for the five compressors constructive groups with unit capacities from 0,02 to 2 MW. The paper considers the standard STO 03-007-11 main points.
Data collection and processing is the basis of piston compressors monitoring and diagnostics technology, thus providing compressors defects and malfunctions detection with a specified depth of their detailing and reliability and a hazard level.
Realization of monitoring and diagnostics technology is based on application of vibroacoustic signals structure models upon occurrence of various defects and malfunctions in piston compressors components, set of malfunctions and standard values diagnostic features, methods of vibroacoustic signals transformation and a system for their parameters estimation.
The paper considers methodology of the diagnostic signal processing and the monitoring system functional diagram.
The proposed monitoring and diagnostics methodology is based on measurement of vibroacoustic oscillations parameters and characteristics, as well as measurement of direct structural and thermodynamic parameters.
The structure and functioning principles of the expert system for decision making support have been presented.
Functioning algorithm of the automatic expert system includes calculation of the diagnostic features values based on their normative ones, formation of the diagnostic features sets which correspond to individual malfunctions classes and formation of the expert system messages.
The scheme of the system for piston compressors real-time health monitoring has been considered.
The system has a series-parallel structure of a data-measuring complex for data collection and processing, which allows to measure the vibroacoustic signals parameters for piston compressors and their operating modes monitoring. Besides,
the system allows to measure other physical processes parameters, for example, for
monitoring and diagnosis-making purposes it has been provided to measure and apply pressure in decreasing spaces (an indicator diagram), gas temperature, a rod position, leakage through stuffing boxes and others.
on compressors’ vibroactivity. An adequate evaluation of vibroactivity of piston machines is provided by the Russian regulative database on vibration parameters.
Main differences of Russian and global methods of reciprocating compressors health evaluation, particularly, used frequency range, are presented in the article. It is shown that the approach laid in Russian standards on reciprocating compressors vibration regulations, ensures true-to-life assessment of reciprocating compressors assemblies and details condition.
The examples given in the article confirm that the criteria of reciprocating compressors repair correctness assessment should be the machinery health, including its vibroactivity, not just mindless usage of new components purchased from the global brands.
Practical examples of operation and monitoring of reciprocating compressors show that Russian developments and products,
particularly, scientific-methodological and standards base of Vibration-Based Diagnostics monitoring, reciprocating compressors monitoring systems, reciprocating compressors valves are highly competitive with foreign ones, and sometimes even superior to them in parameters and characteristics, which is a positive factor under the conditions of current economic situation and import substitution policy.
Operator is considered as a part of the technological system. Although, personnel’s behavior is usually a combination of the following parameters: input signal - information perceiving, reaction – decision making, response – decision implementing. Based on several researches on behavior of nuclear powers station operators in USA, Italy and other countries, as well as on researches conducted by Russian scientists, required data on operator’s reliability were selected for analysis of operator’s behavior at technological facilities diagnostics and monitoring systems. The calculations revealed that for the monitoring system selected as an example, the failure skipping risk for the set values of static (less than 0.01) and dynamic (less than 0.001) errors considering all related factors of data on reliability of information perception, decision-making, and reaction fulfilled is 0.037, in case when all the facilities and error probability are under control – not more than 0.027. In case when only pump and compressor units are under control, the failure skipping risk is not more than 0.022, when the probability of error in operator’s action is not more than 0.011. The work output shows that on the basis of the researches results an assessment of operators’ reliability can be made in terms of almost any kind of production, but considering only technological capabilities, since operators’ psychological and general training considerable vary in different production industries. Using latest technologies of engineering psychology and design of data support systems, situation assessment systems, decision-making and responding system, as well as achievement in condition monitoring in various production industries one can evaluate hazardous condition skipping risk probability considering static, dynamic errors and human factor.
The purpose of the paper is to present the basic terminology of diagnostics, monitoring and vibroacoustics and its application to the real engineering solutions.
The terminology is suggested by guidelines and regulations, reference, scientific and educational materials, including the researches carried out by the authors.
The analysis of the terminology used in Russia and abroad revealed the differing interpretations in solving engineering problems of the machinery condition monitoring, diagnostics, and health monitoring. In particular, the term “condition monitoring” shall be understood as monitoring of state parameters without diagnostics.
It is shown that the vibroacoustic signal is a random process, and the vibroacoustic diagnostics requires analysis of its stochastic characteristics. For this reason, it is necessary to measure vibration acceleration, velocity and displacement, since the stochastic characteristics of these vibroacoustic oscillation parameters are statistically independent.
The studies performed brought us to the conclusion that the real-time health monitoring systems should provide real-time machinery diagnostics at such time intervals, during which the machinery state of health cannot change from normal to limit. In order to minimize the failure missing risk and ensure reliable diagnostics based-on the vibroacoustic signal parameters, one should measure the vibration acceleration, velocity and displacement with an accuracy of few percent over the frequency range of at least 3000 Hz.
malfunctions of reciprocating machines show that for the diagnostic purposes it is necessary to analyze vibroacoustic signals either in the time domain according to the cyclogram of the reciprocating machine operation or in the envelope spectrum at characteristic frequencies or the noise component. In the event of defects and malfunctions in the centrifugal rotating parts and components, there are excited the vibroacoustic signals, which are advisable to analyze in the direct spectrum or in the spectrum of the noise component envelope. The proposed models enable us to select and form scientifically grounded systems of the machine failure diagnostic signs.
The model of vibroacoustic signal of reciprocating compressor based on vibroacoustic oscillations sources analysis is presented. The model of a signal is formed on the basis of noise and periodic components of vibroacoustic signal and their intermodulation component. Diagnostic features of reciprocating compressor units’ defects which are formed on the basis of vibroacoustic signal model are considered. Use of these diagnostic features allows to implement the condition monitoring of all units and details of a reciprocating compressor and to execute automatic diagnosing without participation of experts. The scheme of system for diagnostics and condition monitoring of various reciprocating compressors components based on parameters of vibroacoustic signals is offered.
Practical examples of operation of system for diagnostics and condition monitoring of reciprocating compressors state are reviewed. Opportunities of results use of a condition monitoring system operation with the purpose of improvement of reciprocating compressor state are shown. The designed diagnostics and condition monitoring system of reciprocating compressors uses five sensors of vibroacoustic signals on one cylinder and provides safe and accident-free operation of reciprocating compressors.
Key words: vibrodiagnostic, reciprocating compressor, diagnostics, real-time condition
monitoring, automatic expert system, piston compressor
methods and means of condition monitoring and diagnostics of reciprocating
compressors in hazardous industries. The principles of condition control presented in
monitoring systems have been studied. Technology of condition monitoring systems
was examined.
Methodology, implementation technology and principles of construction of real-time
condition monitoring systems have been analyzed. The COMPACS system of real-time
condition monitoring of reciprocating compressors have been considered.
Keywords: reciprocators, reciprocating compressors, monitoring, diagnostics, vibration
time condition monitoring system is presented.
The standard applies to stationary piston compressors, operating on explosive and harmful gases and sets the vibration standards for assessing their technical condition during operation and acceptance tests after mounting and repair.
The vibration parameters rates, specified in STO 03-007-11, are of advisory nature for all the machines which are not enumerated in the vehicles list, supplied in the standard appendix. These rates can be adjusted according to resolutions of the enterprise responsible technical services as bringing the diagnosed equipment to the required reliability activities, guaranteeing safety and fault-free operation of the hazardous facilities equipment. The standard specifies the vibration parameters rates and prescribes their use for the arrangement of vibration monitoring, vibration analysis, technical condition monitoring and operational risks for stationary piston compressor units. This document determines the frequencies ranges of measurement for each vibration parameter and proposes to measure not only the mean square values of acceleration, velocity, displacement, but their amplitudes as well. The vibration rates are given for the five compressors constructive groups with unit capacities from 0,02 to 2 MW. The paper considers the standard STO 03-007-11 main points.
Data collection and processing is the basis of piston compressors monitoring and diagnostics technology, thus providing compressors defects and malfunctions detection with a specified depth of their detailing and reliability and a hazard level.
Realization of monitoring and diagnostics technology is based on application of vibroacoustic signals structure models upon occurrence of various defects and malfunctions in piston compressors components, set of malfunctions and standard values diagnostic features, methods of vibroacoustic signals transformation and a system for their parameters estimation.
The paper considers methodology of the diagnostic signal processing and the monitoring system functional diagram.
The proposed monitoring and diagnostics methodology is based on measurement of vibroacoustic oscillations parameters and characteristics, as well as measurement of direct structural and thermodynamic parameters.
The structure and functioning principles of the expert system for decision making support have been presented.
Functioning algorithm of the automatic expert system includes calculation of the diagnostic features values based on their normative ones, formation of the diagnostic features sets which correspond to individual malfunctions classes and formation of the expert system messages.
The scheme of the system for piston compressors real-time health monitoring has been considered.
The system has a series-parallel structure of a data-measuring complex for data collection and processing, which allows to measure the vibroacoustic signals parameters for piston compressors and their operating modes monitoring. Besides,
the system allows to measure other physical processes parameters, for example, for
monitoring and diagnosis-making purposes it has been provided to measure and apply pressure in decreasing spaces (an indicator diagram), gas temperature, a rod position, leakage through stuffing boxes and others.
on compressors’ vibroactivity. An adequate evaluation of vibroactivity of piston machines is provided by the Russian regulative database on vibration parameters.
Main differences of Russian and global methods of reciprocating compressors health evaluation, particularly, used frequency range, are presented in the article. It is shown that the approach laid in Russian standards on reciprocating compressors vibration regulations, ensures true-to-life assessment of reciprocating compressors assemblies and details condition.
The examples given in the article confirm that the criteria of reciprocating compressors repair correctness assessment should be the machinery health, including its vibroactivity, not just mindless usage of new components purchased from the global brands.
Practical examples of operation and monitoring of reciprocating compressors show that Russian developments and products,
particularly, scientific-methodological and standards base of Vibration-Based Diagnostics monitoring, reciprocating compressors monitoring systems, reciprocating compressors valves are highly competitive with foreign ones, and sometimes even superior to them in parameters and characteristics, which is a positive factor under the conditions of current economic situation and import substitution policy.
Operator is considered as a part of the technological system. Although, personnel’s behavior is usually a combination of the following parameters: input signal - information perceiving, reaction – decision making, response – decision implementing. Based on several researches on behavior of nuclear powers station operators in USA, Italy and other countries, as well as on researches conducted by Russian scientists, required data on operator’s reliability were selected for analysis of operator’s behavior at technological facilities diagnostics and monitoring systems. The calculations revealed that for the monitoring system selected as an example, the failure skipping risk for the set values of static (less than 0.01) and dynamic (less than 0.001) errors considering all related factors of data on reliability of information perception, decision-making, and reaction fulfilled is 0.037, in case when all the facilities and error probability are under control – not more than 0.027. In case when only pump and compressor units are under control, the failure skipping risk is not more than 0.022, when the probability of error in operator’s action is not more than 0.011. The work output shows that on the basis of the researches results an assessment of operators’ reliability can be made in terms of almost any kind of production, but considering only technological capabilities, since operators’ psychological and general training considerable vary in different production industries. Using latest technologies of engineering psychology and design of data support systems, situation assessment systems, decision-making and responding system, as well as achievement in condition monitoring in various production industries one can evaluate hazardous condition skipping risk probability considering static, dynamic errors and human factor.
The purpose of the paper is to present the basic terminology of diagnostics, monitoring and vibroacoustics and its application to the real engineering solutions.
The terminology is suggested by guidelines and regulations, reference, scientific and educational materials, including the researches carried out by the authors.
The analysis of the terminology used in Russia and abroad revealed the differing interpretations in solving engineering problems of the machinery condition monitoring, diagnostics, and health monitoring. In particular, the term “condition monitoring” shall be understood as monitoring of state parameters without diagnostics.
It is shown that the vibroacoustic signal is a random process, and the vibroacoustic diagnostics requires analysis of its stochastic characteristics. For this reason, it is necessary to measure vibration acceleration, velocity and displacement, since the stochastic characteristics of these vibroacoustic oscillation parameters are statistically independent.
The studies performed brought us to the conclusion that the real-time health monitoring systems should provide real-time machinery diagnostics at such time intervals, during which the machinery state of health cannot change from normal to limit. In order to minimize the failure missing risk and ensure reliable diagnostics based-on the vibroacoustic signal parameters, one should measure the vibration acceleration, velocity and displacement with an accuracy of few percent over the frequency range of at least 3000 Hz.
malfunctions of reciprocating machines show that for the diagnostic purposes it is necessary to analyze vibroacoustic signals either in the time domain according to the cyclogram of the reciprocating machine operation or in the envelope spectrum at characteristic frequencies or the noise component. In the event of defects and malfunctions in the centrifugal rotating parts and components, there are excited the vibroacoustic signals, which are advisable to analyze in the direct spectrum or in the spectrum of the noise component envelope. The proposed models enable us to select and form scientifically grounded systems of the machine failure diagnostic signs.