Papers by Peter Berkelman

Proceedings of SPIE, Dec 12, 1997
A new haptic interface device has been developed which uses Lorentz force magnetic levitation for... more A new haptic interface device has been developed which uses Lorentz force magnetic levitation for actuation. With this device, the user grasps a oating rigid body to interact with the system. The levitated moving part grasped by the user contains curved oval wound coils and LEDs embedded in a hemispherical shell with a handle xed at its center. The stationary base contains magnet assemblies facing the otor coils and optical position sensors facing the otor LEDs. The device is mounted in the top cover of a desk-side cabinet enclosure containing all the ampli ers, control hardware, microprocessing, and power supplies needed for operation. A network connection provides communication with a workstation to allow i n teraction with simulated 3D environments in real time. Ideally, the haptic interface device should reproduce the dynamics of the modelled or remote environment with such high delity that the user cannot distinguish interaction with the device from interaction with a real object in a real environment. In practice, this ideal can only be approached with a delity that depends on its dynamic properties such as position and force bandwidths, maximum forces and accelerations, position resolution, and realizable impedance range. The motion range of the moving part is approximately 25 mm and 15-20 degrees in all directions. A current o f 0.75 A is required in three of the six coils to generate the vertical force to lift the 850 g levitated mass, dissipating only 13.5 W. Peak forces of over 50 N and torques of over 6 Nm are achievable with the present ampli ers without overheating the actuator coils. Other measured performance results include sti ness ranges from 0.005 N mm to 25.0 N mm and a position control bandwidth of approximately 75 Hz.
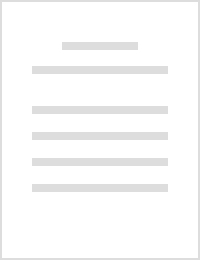
IEEE Magnetics Letters, 2020
This letter describes an electromagnetic feedback control system for rigid-body motion control of... more This letter describes an electromagnetic feedback control system for rigid-body motion control of a magnet. Its novel features are that sensing and actuation using magnetometer sensors and actuator coils operate simultaneously, and magnetic field models from the controlled magnet and each of the actuator coil currents are used together to calculate the 3D position and orientation of the magnet to control motion simultaneously and independently in multiple degrees of freedom including planar translation and two in rotation, leaving rotation about the cylindrical axis of magnetization uncontrolled. The system configuration and the localization and actuation methods are presented with experimental results of magnet localization with constant and varying coil currents, and during feedback control of trajectory following motion of the magnet in multiple directions on a planar surface and with controlled changes in orientation. The intended application of the system is for motion control of magnetic endoscope capsules and other miniature medical devices inside the human body.
The International Journal of Robotics Research, Jul 1, 2000
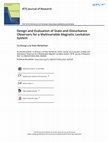
Iete Journal of Research, Oct 15, 2020
For inherently unstable magnetic levitation (maglev) systems, state observation is required for f... more For inherently unstable magnetic levitation (maglev) systems, state observation is required for feedback control, and disturbance estimation is needed to compensate for unknown disturbances. Previous designs for simultaneously observing state and disturbance can lead to aggressive disturbance compensation and an unstable levitation. Aiming at these problems, this paper presents a state and disturbance observer that has a cascade structure for a maglev system. The proposed design allows the dynamics of disturbance observation to be separately tuned from those of state observation, avoiding aggressive disturbance compensation and enabling a stable levitation of a maglev system. In this paper, the proposed and previous state and disturbance observers are designed and realized for a maglev system that features wide ranges of translation and rotation motions in five directions. Comparative studies are reported in this paper, and experimental results show feasibility and efficiency of the proposed scheme.

International journal on advances in intelligent systems, Dec 31, 2013
We have developed a system which can combine realtime dynamic simulations, 3D display, and magnet... more We have developed a system which can combine realtime dynamic simulations, 3D display, and magnetic levitation to provide high-fidelity co-located haptic and graphic interaction. Haptic interaction is generated by a planar horizontal array of cylindrical coils which act in combination to produce arbitrary forces and torques in any direction on magnets fixed to an instrument handle held by the user, according to the position and orientation sensed by a motion tracking sensor and the dynamics of a realtime physical simulation. Co-located graphics are provided by a thin flat screen placed directly above the coil array so that the 3D display of virtual objects shares the same volume as the motion range of the handheld instrument. Shuttered glasses and a head tracking system are used to preserve the alignment of the displayed environment and the interaction handle according to the user's head position. Basic interactive environments have been developed to demonstrate the system feasibility and operation, including rigid bodies with solid contacts, suspended mass-spring-damper assemblies, and deformable surfaces. Interactive physical simulation of these environments requires real-time collision detection between geometric models; numerical, discrete-time numerical integration to calculate the physics of networks of mass, spring, and damper elements; and calculation and actuation of interactive forces to the user in haptic rendering. Incorporating these functions into a single executable requires multiple program threads with various update rates, ideally performed using a multicore processor PC. Details and discussion of various simulations are given with experimental results.
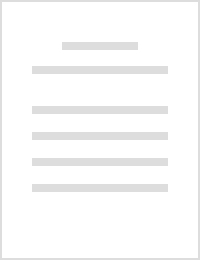
PubMed, 2013
We describe a system which provides high-fidelity haptic feedback in the same physical location a... more We describe a system which provides high-fidelity haptic feedback in the same physical location as a 3D graphical display, in order to enable realistic physical interaction with virtual anatomical tissue during modelled procedures such as needle driving, palpation, and other interventions performed using handheld instruments. The haptic feedback is produced by the interaction between an array of coils located behind a thin flat LCD screen, and permanent magnets embedded in the instrument held by the user. The coil and magnet configuration permits arbitrary forces and torques to be generated on the instrument in real time according to the dynamics of the simulated tissue by activating the coils in combination. A rigid-body motion tracker provides position and orientation feedback of the handheld instrument to the computer simulation, and the 3D display is produced using LCD shutter glasses and a head-tracking system for the user.

Haptic interface devices and teleoperation masters are multiple degree of freedom devices manipul... more Haptic interface devices and teleoperation masters are multiple degree of freedom devices manipulated by an operator to generate realtime motion commands to simulated environments or robot manipulators. In this work we examine the relationship between the simulated friction parameters of a particular spatial positioning master device and the completion times of planar positioning tasks by human operators. It is expected that increasing the Coulomb or viscous friction of the device would tend to increase the completion times of less difficult, quicker positioning tasks and decrease completion times for more difficult fine positioning tasks requiring higher precision from the operator. A common haptic interface device was used to perform continuous sequences of planar positioning tasks. Each trial required 10-12 minutes to complete and consisted of 15 positioning sequences which varied in the size of the target regions and the magnitude and type of simulated friction in the device. With a sample size of 10 test subjects, small effects were generally observed as expected, with the exception of the first 3 to 4 sequences of the trials which are concluded to be an adaptation or learning period for the users during each trial.

Haptic interface devices and teleoperation masters are multiple degree of freedom devices manipul... more Haptic interface devices and teleoperation masters are multiple degree of freedom devices manipulated by an operator to generate realtime motion commands to simulated environments or robot manipulators. In this work we examine the relationship between the simulated friction parameters of a particular spatial positioning master device and the completion times of planar positioning tasks by human operators. It is expected that increasing the Coulomb or viscous friction of the device would tend to increase the completion times of less difficult, quicker positioning tasks and decrease completion times for more difficult fine positioning tasks requiring higher precision from the operator. A common haptic interface device was used to perform continuous sequences of planar positioning tasks. Each trial required 10-12 minutes to complete and consisted of 15 positioning sequences which varied in the size of the target regions and the magnitude and type of simulated friction in the device. With a sample size of 10 test subjects, small effects were generally observed as expected, with the exception of the first 3 to 4 sequences of the trials which are concluded to be an adaptation or learning period for the users during each trial.

International Journal of Medical Robotics and Computer Assisted Surgery, Mar 27, 2017
Background-To date a variety of teleoperated surgical robotic systems have been developed to impr... more Background-To date a variety of teleoperated surgical robotic systems have been developed to improve a surgeons ability to perform demanding single-port procedures. However typical large systems are bulky, expensive, and afford limited angular motion, while smaller designs suffer complications arising from limited motion range, speed, and force generation. This work was to develop and validate a simple, compact, low cost single site teleoperated laparoendoscopic surgical robotic system, with demonstrated capability to carry out basic surgical procedures. Methods-This system builds upon previous work done at the University of Hawaii at Manoa and includes instrument and endoscope manipulators as well as compact articulated instruments designed to overcome single incision geometry complications. A robotic endoscope holder was used for the base, with an added support frame for teleoperated manipulators and instruments fabricated mostly from 3D printed parts. Kinematics and control methods were formulated for the novel manipulator configuration. Results-Trajectory following results from an optical motion tracker and sample task performance results are presented. Conclusions-Results indicate that the system has successfully met the goal of basic surgical functionality while minimizing physical size, complexity, and cost.
Minimally invasive surgery (MIS) has become an important technique in practical surgical procedur... more Minimally invasive surgery (MIS) has become an important technique in practical surgical procedures. Compared with manually operated MIS procedures, surgical robot systems provide more accuracy, enhance dexterity, and make more difficult surgical procedures feasible. In this paper, a prototype teleoperated robotic surgical system which is modular, compact and easy to use is tested with human operators. Two evaluation tasks were performed by participants using manual MIS instruments and this teleoperated robotic surgical system. The task data were analyzed and compared between the manual and robot instrument operation. The results show that compared with typical manual instrument operation, the teleoperated robotic system in this paper has advantages in ease of use, decreased task time, and better accuracy with smooth motions and less tremor.
Springer eBooks, 2001
This paper reports the development of a full-scale instrumented model of the human ear that permi... more This paper reports the development of a full-scale instrumented model of the human ear that permits quantitative evaluation of the utility of a microsurgical assistant robot in the surgical procedure of stapedotomy.

We have developed two different magnetic levitation devices which provide unprecedented ranges of... more We have developed two different magnetic levitation devices which provide unprecedented ranges of motion in both translation and rotation to a levitated handle to be used for tool-based haptic interaction. The first device levitates a handle attached to a thin spherical shell of flat coils suspended in permanent magnet fields using Lorentz forces. A novel coil type and magnet configuration provides motion ranges of 50 mm and 60 degrees in all directions, double the translation and triple the rotation ranges of the current maximum range Lorentz levitation haptic devices developed at Carnegie Mellon University. The second device uses a planar array of cylindrical coils to levitate a platform of one or more magnets. By using redundant control methods and an experimentally measured high resolution model of the forces and torques generated on the levitated magnets from each coil, the translation range of the magnet in horizontal directions and its rotation in all directions and can be extended potentially indefinitely. The present prototype uses 10 coils to levitate a single magnet over a 80x60 mm planar range, a 30 mm vertical range, and a tilt range of 40 degrees, or to control the yaw rotation of a pair of magnets over 360 degrees. Design and control methods are presented with preliminary motion trajectory results from both devices.

Dynamic Systems and Control, Nov 17, 1996
We are currently fabricating a haptic interface device to enable direct physical interaction with... more We are currently fabricating a haptic interface device to enable direct physical interaction with dynamic simulated three-dimensional environments by exerting and reacting to forces and motions between the user's hand and a magnetically levitated object. Our device uses magnetic levitation rather than a motorized linkage so that the dynamics are simple and actuator nonlinearities such a s h ysteresis, backlash and static friction are eliminated. Magnetic levitation haptic interaction was previously demonstrated using a ne motion robot wrist. A new magnetic levitation device was then designed speci cally to address the requirements of realistic tool-based haptic interaction. A hemispherical device shape was adopted to maximize the ranges of translation and rotation and the ratio of actuator surface area to the levitated mass while enabling the user to grip a tool handle at the hemisphere center, near the center of mass, where translation, rotation, force, and torque ranges are the same in all directions. The new device will have a motion range of at least 12 mm and 7 , position sensing resolution within 3 m, and will be capable of generating peak forces up to 60 N. Preliminary results from testing of position sensors and actuator assemblies support the performance data obtained from model analysis.

IEEE Transactions on Haptics, Oct 1, 2017
Despite the fact that conventional haptic interfaces and rendering algorithms commonly approximat... more Despite the fact that conventional haptic interfaces and rendering algorithms commonly approximate interactions with force only, the dynamic effects of even simple tasks, e.g. writing on a paper, involve both forces and torques. To extend previous algorithms as well as to investigate the effects of torque feedback on human roughness perception, we deployed a novel haptic platform with two probes, fingertip and penhandle. Three torque conditions were examined: 1) Slope Torque, which orients the probe perpendicular to the surface, 2) No Torque, where no active torque is provided by the device, and 3) Stiff Torque, where torque feedback is provided to keep the probe upright. A conventional magnitude estimation experiment was performed. The results indicated that both the torque signals and grasp type mediate human perception of virtual textures. Slope Torque led to greater perceived roughness when the fingertip was used, and the fingertip led to higher roughness ratings than the penhandle with the Slope Torque condition. The Slope Torque algorithm appears to be advantageous for generating rougher surfaces compared to the force-based algorithms which are typically limited by the system stability and actuator saturation.

Lecture Notes in Computer Science, 2000
This paper reports the development of a new miniature force sensor to measure forces at the tip o... more This paper reports the development of a new miniature force sensor to measure forces at the tip of a microsurgical instrument in three dimensions with sub-millinewton resolution. This sensor will enable enhanced force feedback during surgical intervention in which a user directly manipulates surgical instruments cooperatively with a forcereflecting robot arm. This "steady-hand" scaled force interaction enables a surgeon to sense millinewton forces between the instrument and delicate body tissues during microsurgery which would otherwise be far below the threshold of human tactile sensing. The magnified force feedback can increase the dexterity of the surgeon and improve safety by preventing large damaging forces from being exerted by the instrument. The design and analysis of the new force sensor is presented with preliminary testing and force scaling control results.
InTech eBooks, Apr 1, 2010
Abstract The utility of current commercial teleoperated robotic surgery systems is limited by the... more Abstract The utility of current commercial teleoperated robotic surgery systems is limited by their high cost, large size, and time-consuming setup procedures. We have developed a prototype system which aims to overcome these obstacles by being much smaller, simpler, and easier to set up and operate, while providing equivalent functionality and performance for executing surgical procedures. The prototype system is modular and each component manipulator is approximately 2.5 kg or less, so that they system is easily portable and ...
Uploads
Papers by Peter Berkelman