Papers by bertrand Le-Gratiet
Proceedings of SPIE, Mar 8, 2016
Proceedings of SPIE, Mar 19, 2015
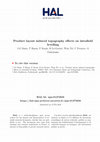
Proceedings of SPIE, Sep 4, 2015
With continuing dimension shrinkage using the TWINSCAN NXT:1950i scanner on the 28nm node and bey... more With continuing dimension shrinkage using the TWINSCAN NXT:1950i scanner on the 28nm node and beyond, the imaging depth of focus (DOF) becomes more critical. Focus budget breakdown studies [Ref 2, 5] show that even though the intrafield component stays the same, it becomes a larger relative percentage of the overall DOF. Process induced topography along with reduced Process Window can lead to yield limitations and defectivity issues on the wafer. In a previous paper, the feasibility of anticipating the scanner levelling measurements (Level Sensor, Agile and Topography) has been shown [1]. This model, built using a multiple variable analysis (PLS: Partial Least Square regression) and GDS densities at different layers showed prediction capabilities of the scanner topography readings up to 0.78 Q² (the equivalent of R² for expected prediction). Using this model, care areas can be defined as parts of the field that cannot be seen nor corrected by the scanner, which can lead to local DOF shrinkage and printing issues. This paper will investigate the link between the care areas and the intrafield focus that can be seen at the wafer level, using offline topography measurements as a reference. Some improvements made on the model are also presented.
Metrology, Inspection, and Process Control XXXVI, May 26, 2022
Metrology, Inspection, and Process Control XXXVI, May 26, 2022
Journal of micro/nanopatterning, materials, and metrology, Dec 6, 2022
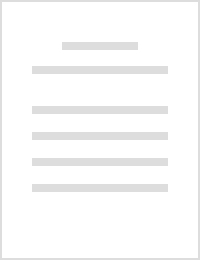
Metrology, Inspection, and Process Control for Microlithography XXXI, 2017
At 28nm technology node and below, hot spot prediction and process window control across producti... more At 28nm technology node and below, hot spot prediction and process window control across production wafers have become increasingly critical to prevent hotspots from becoming yield-limiting defects. We previously established proof of concept for a systematic approach to identify the most critical pattern locations, i.e. hotspots, in a reticle layout by computational lithography and combining process window characteristics of these patterns with across-wafer process variation data to predict where hotspots may become yield impacting defects [1,2]. The current paper establishes the impact of micro-topography on a 28nm metal layer, and its correlation with hotspot best focus variations across a production chip layout. Detailed topography measurements are obtained from an offline tool, and pattern-dependent best focus (BF) shifts are determined from litho simulations that include mask-3D effects. We also establish hotspot metrology and defect verification by SEM image contour extraction and contour analysis. This enables detection of catastrophic defects as well as quantitative characterization of pattern variability, i.e. local and global CD uniformity, across a wafer to establish hotspot defect and variability maps. Finally, we combine defect prediction and verification capabilities for process monitoring by on-product, guided hotspot metrology, i.e. with sampling locations being determined from the defect prediction model and achieved prediction accuracy (capture rate) around 75%
Design-Process-Technology Co-optimization for Manufacturability X, 2016
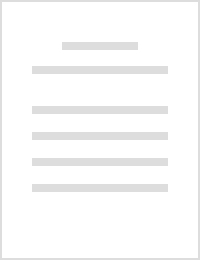
At 28nm technology node and below, hot spot prediction and process window control across producti... more At 28nm technology node and below, hot spot prediction and process window control across production wafers have become increasingly critical to prevent hotspots from becoming yield-limiting defects. We previously established proof of concept for a systematic approach to identify the most critical pattern locations, i.e. hotspots, in a reticle layout by computational lithography and combining process window characteristics of these patterns with across-wafer process variation data to predict where hotspots may become yield impacting defects [1,2]. The current paper establishes the impact of micro-topography on a 28nm metal layer, and its correlation with hotspot best focus variations across a production chip layout. Detailed topography measurements are obtained from an offline tool, and pattern-dependent best focus (BF) shifts are determined from litho simulations that include mask-3D effects. We also establish hotspot metrology and defect verification by SEM image contour extraction and contour analysis. This enables detection of catastrophic defects as well as quantitative characterization of pattern variability, i.e. local and global CD uniformity, across a wafer to establish hotspot defect and variability maps. Finally, we combine defect prediction and verification capabilities for process monitoring by on-product, guided hotspot metrology, i.e. with sampling locations being determined from the defect prediction model and achieved prediction accuracy (capture rate) around 75%
Metrology, Inspection, and Process Control XXXVII
37th European Mask and Lithography Conference
Journal of Micro/Nanopatterning, Materials, and Metrology
2022 33rd Annual SEMI Advanced Semiconductor Manufacturing Conference (ASMC)
Metrology, Inspection, and Process Control XXXVI
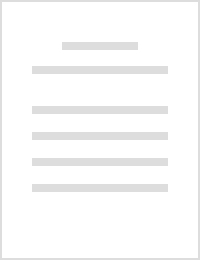
Since the beginning of the Crolles 300mm fab, more and more complex logic technologies, down to 2... more Since the beginning of the Crolles 300mm fab, more and more complex logic technologies, down to 28nm node, have been developed. At the same time, the products mix increased at a very high level : Specifically for the lithography area, this complexity leads to an intricate management of thousands of masks, hundreds of track process recipes, used on various lithography clusters types (193nm including immersion, 248nm and 365nm). In order to apply the best process parameters, APC software is used since many years, and was continuously improved. It now takes into account multi-variate parameters coming from various process contexts. A new sampling tool was developed to adjust the measurements control plan. All kind of in-line measures are addressed (thickness, critical dimensions, overlay…). Since the beginning of this software development, the approach was to keep in mind the APC model. The objective was to use the APC data’s (alarms and warnings) to secure the sampling decisions witho...
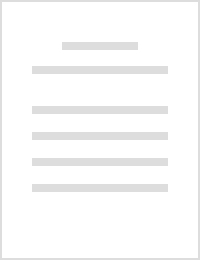
SPIE Proceedings, 2013
ABSTRACT Current process tool performances are getting significantly enhanced by the adoption of ... more ABSTRACT Current process tool performances are getting significantly enhanced by the adoption of advanced process correction application such as DoseMapper for CD or high order overlay correction for overlay. These process control capabilities need appropriate sampling to be efficient. Usually for in field metrology sampling we used to operate with metrology targets placed inside the scribe lines, however in this case the larger the chip the less scribe lines we have and the less relevant is the intrafield sampling. As ST is an IDM we have the opportunity to share with our design division this process control problematic. Since 45/40nm node we have started to put in place the so-called EMET (Embedded Metrology Target) strategy which consists in in-design metrology targets placement. Initially these targets were placed using tiling tools but it soon appeared to be not efficient and even impossible when we talk about targets involving complex metal stack. This papers talks about our current embedded metrology target strategy which has been adapted to enable appropriate target placement for CD and overlay for all critical layers from active to via/metal’s. Solutions needed to be put in place to (i) keep the circuit safe by using Design Rule clean metrology targets, (ii) be highly visible by the designers by placing targets at chip floor planning definition (iii) be upgradable by enabling target re-designs without impact on chip design version.
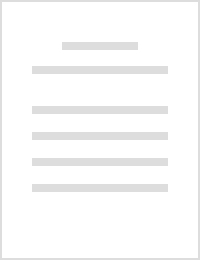
Metrology, Inspection, and Process Control for Microlithography XXVII, 2013
ABSTRACT Gate patterning control for 28nm Fully Depleted Silicon On Insulator (FD-SOI) technology... more ABSTRACT Gate patterning control for 28nm Fully Depleted Silicon On Insulator (FD-SOI) technology faces several challenges. For lithography and etch , usage of DoseMapper requires extensive and accurate metrology to compute adequate dose recipes. From etch side we will have to control both polysilicon and metal gate CD’s. For device integration it will be extremely important to monitor N and PMOS devices and get appropriate gate profiles since transistor morphology is a key contributor to device performances. In parallel of CD control, thin silicon film on top of buried oxide layer will also require a strict control of its thickness. Scatterometry is the only way to get all these informations from a patterned environment [1]. We will show in this paper how scatterometry has been proven to be accurate enough to support the realization of DOE’s for metal gate profile optimisation at gate patterning without doing hundred’s of TEM. Scatterometry results are correlated to parametric tests and TEM for ultimate validation.
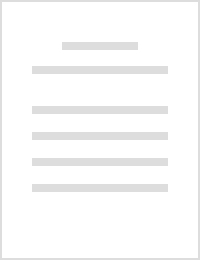
SPIE Proceedings, 2010
ABSTRACT As mask dimensions continue to shrink to meet the ITRS roadmap and with the extension of... more ABSTRACT As mask dimensions continue to shrink to meet the ITRS roadmap and with the extension of 193 nm immersion lithography, the masks are affected by electromagnetic field at high NA. Absorber degradation is regularly reported under long term 193 nm exposures in the subwavelength diffraction regime. The damage mechanism known as Electric Field induced Migration of chrome (EFM) partly contributes to the lifetime reduction of advanced masks. The EFM results in a progressive alteration of the Critical Dimension (CD), CD uniformity (CDU) degradation and assist features. This study evaluates the impact and the rate of absorber degradation due to an intensive ArF irradiation on assist features and its influence on the through pitch process window for sub-45 nm technology nodes. Lithographic performance is characterized after cumulative reticle aging stages. The aging test exposures are carried out directly on 193 nm scanner to duplicate the production environment. The analysis of printed wafers is correlated to advanced mask inspection (AIMSTM). This paper reports results on irradiation damage sensitivity on two types of reticles: conventional 6% attenuated PSM and new binary material OMOG (Opaque MoSi On Glass) reticle. Test patterns have been generated with and without a set of Optical Proximity Corrections (OPC) model calibration structures based on 45nm down to 28nm half-pitch design. The combination of metrology measurements used in this work between printed wafers and reticles enables to define accurately the impact of mask damage caused by EFM effects on various test patterns and CD evolution and highlight some trends about advances masks aging phenomenon.
Uploads
Papers by bertrand Le-Gratiet