Papers by Sankalp Bhatiya
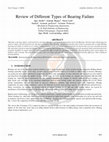
International Journal of Advance Research and Innovative Ideas in Education, 2016
Bearing is moving object, so friction force of comes into play, and must be surpassed to move the... more Bearing is moving object, so friction force of comes into play, and must be surpassed to move the Bearing. Various types of bearings are used to reduce this friction force for moving mechanism. The bearing named from the fact that it bears a turning axle or shaft. Rolling bearings use balls, or rollers so it's called "rolling elements. If the operating loads and speeds are known then you can calculate bearing life expectancy based on material fatigue. These calculations must assume that the bearing is correctly mounted, lubricated and otherwise properly handled. It cannot take into consideration the effect of adverse operating conditions. Bearing failures have great impact on industry and economy. The aim of the present work is to study and spot the major causes that limit bearing efficiency, thus l eading to bearing failure.
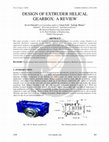
International Journal of Advance Research and Innovative Ideas in Education, 2016
This paper provides a review of the literature on designing and analysis of a gearbox casing. Gea... more This paper provides a review of the literature on designing and analysis of a gearbox casing. Gearbox is an important machinery component in any industry. Helical gears are widely used in numerous engineering applications. Industry is facing the problem of higher disassembly time and difficulty in maintenance. As a solution, split casing needs to be developed. Stress analysis is engineering discipline that determines the stress in materials and structures subjected to static and dynamic forces or loads. Vibrational analysis of casing also plays a vital role in proper working of the gearbox. Gearbox with moving parts gives rise to noise and vibration, which reveals the gearbox condition. FEA method is used for static and vibration analysis. In this paper, we have reviewed the current research state of modal analysis and harmonic frequency response on gearbox casing and also an insight into future research and challenges in this field of study.
Lecture notes in mechanical engineering, 2023
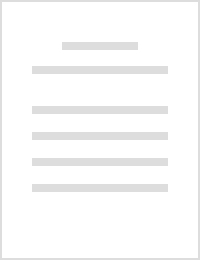
International Journal of Advance Research and Innovative Ideas in Education, 2016
This paper provides a review of the literature on designing and analysis of a gearbox casing. Gea... more This paper provides a review of the literature on designing and analysis of a gearbox casing. Gearbox is an important machinery component in any industry. Helical gears are widely used in numerous engineering applications. Industry is facing the problem of higher disassembly time and difficulty in maintenance. As a solution, split casing needs to be developed. Stress analysis is engineering discipline that determines the stress in materials and structures subjected to static and dynamic forces or loads. Vibrational analysis of casing also plays a vital role in proper working of the gearbox. Gearbox with moving parts gives rise to noise and vibration, which reveals the gearbox condition. FEA method is used for static and vibration analysis. In this paper, we have reviewed the current research state of modal analysis and harmonic frequency response on gearbox casing and also an insight into future research and challenges in this field of study.
Abstract: Bearing is moving object, so friction force of comes into play, and must be surpassed t... more Abstract: Bearing is moving object, so friction force of comes into play, and must be surpassed to move the Bearing. Various types of bearings are used to reduce this friction force for moving mechanism. The bearing named from the fact that it bears a turning axle or shaft. Rolling bearings use balls, or rollers so it’s called "rolling elements. If the operating loads and speeds are known then you can calculate bearing life expectancy based on material fatigue. These calculations must assume that the bearing is correctly mounted, lubricated and otherwise properly handled. It cannot take into consideration the effect of adverse operating conditions. Bearing failures have great impact on industry and economy. The aim of the present work is to study and spot the major causes that limit bearing efficiency, thus leading to bearing failure.
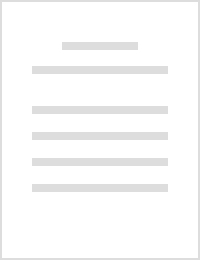
Indian Journal of Applied Research, Apr 1, 2014
Drilling of glass fiber reinforced plastic (GFRP) composite is substantially different from metal... more Drilling of glass fiber reinforced plastic (GFRP) composite is substantially different from metallic materials due to its mechanical properties. Drilling of this material may generate delamination of drilled holes on work piece. The purpose of this review article is to investigate the influence of the cutting parameters, such as cutting speed, feed rate, point angle and volume fraction on delamination produced in case of drilling a GFRP composite. It is essential to measure Delamination, Surface roughness, Torque and Thrust Forces to optimize cutting parameters. Taguchi method and analysis of variance method (ANOVA) is used for minimization of delamination. INTRODUCTION Drilling is one of the most fundamental and most applied metal removal operations in a real manufacturing environment because of its ability to remove material faster and reasonably good surface quality. It is used where quality is an important factor in the production of holes. Greater attention is given to dimensional accuracy and surface roughness of products by the industries in these days. Glass fibre reinforced plastic (GFRP) composites provides high specific strength/stiffness, superior corrosion resistance, light weight construction, low thermal conductivity, and high fatigue strength, ability to char and resistance to chemical and microbiological attacks. Design of experiment (DOE) is useful method in identifying the significant parameters and in studying the possible effect of the variables during the machining trials. This method also can developed experiment between a ranges from un-controllable factors, which will be introduced randomly to carefully controlled parameters. The factors must be either quantitative or qualitative. Experimental Design can be used at the point of greatest leverage to reduce design costs by speeding up the design process reducing late engineering design changes and reducing product material and labor complexity. LITERATURE REVIEW E.Kilickap [1] investigates the influence of the cutting parameters, such as cutting speed and feed rate, and point angle on delamination produced when drilling a GFRP composite. The damage generated associated with drilling GFRP composites were observed, both at the entrance and the exit during the drilling. Hence it is essential to obtain optimum cutting parameters minimizing delamination at drilling of GFRP composites. Moreover, this paper presents the application of Taguchi method and analysis of variance (ANOVA) for minimization of delamination influenced by drilling parameters and drill point angle. The optimum drilling parameter combination was obtained by using the analysis of signal-to-noise ratio. The conclusion revealed that feed rate and cutting speed were the most influential factor on the delamination, respectively. The best results of the delamination were obtained at lower cutting speeds and feed rates. INPUT PARAMETERS : Cutting Speed, Feed Rate, Point Angle OUTPUT PARAMETER : Delamination T.V.Rajamurugan [2] et al attempt has been made to develop empirical relationships between the drilling parameters such as fiber orientation angle, tool feed rate, rotational speed and tool diameter with respect to delamination in drilling of GFR–polyester composites. The empirical relationship has been developed by using response surface methodology. The developed model can be effectively used to predict the delamination in drilling of GFRP composites within the factors and their limits are studied. The result indicated that the increase in feed rate and drill diameter increases the delamination size whereas there is no clear effect is observed for fiber orientation angle. The spindle speed shows only little effect on delamination in drilling of GFR–Polyester composites. INPUT PARAMETERS : Cutting Speed, Feed Rate, Drill Diameter, Fibre Orientation Angle OUTPUT PARAMETER : Delamination K.Panikumar [3] presents an effective approach for the optimisation of drilling parameters with multiple performance characteristics based on the Taguchi’s method with grey relational analysis. Taguchi’s L16, 4-level orthogonal array has been used for the experimentation. The drilling parameters such as spindle speed and feed rate are optimised with consideration of multiple performance characteristics, such as thrust force, work piece surface roughness and delamination factor. Response table and response graph are used for the analysis. The analysis of grey relational grade indicates that feed rate is the more influential parameter than spindle speed. The results indicate that the performance of drilling process can be improved effectively through this approach. INPUT PARAMETERS : Cutting Speed, Feed Rate OUTPUT PARAMETERS : Thrust force, Delamination, Surface Roughness. I.El-Sonbaty [4] et al to investigate the influence of some parameters on the thrust force, torque and surface roughness in drilling processes of fiber-reinforced composite materials. These parameters include cutting speed,…
International Journal of Advance Research and Innovative Ideas in Education, 2016
This paper provides a review of the literature on designing of Cabin tilting mechanism for Earth-... more This paper provides a review of the literature on designing of Cabin tilting mechanism for Earth-moving machinery. In this review we are taking an Earth-moving machinery as a Skid steer loader(SSL). Skid steer loader is an important machinery in any industry. Skid loader is designed in such a way that it can use multiple equipment’s in numerous engineering applications. As this is a compact machinery, therefore there are constraints for maintenance of various subsystem like hydraulics, mounting, engine systems etc., placed at bottom of the cabin. The cabin has got sufficient weight due to ROPS & FOPS considerations. As a solution, there is various methods are available. In this paper several methods of cabin tilting mechanism are reviewed.
Uploads
Papers by Sankalp Bhatiya