Papers by Shimaa El-Hadad
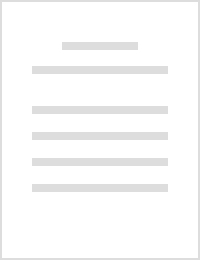
International Journal of Cast Metals Research, 2010
Abstract The influence of alloying elements and cooling conditions on compacted graphite iron is ... more Abstract The influence of alloying elements and cooling conditions on compacted graphite iron is investigated. To investigate the influence of different alloying elements, a sampling cup designed for thermal analysis and tensile test bars were cast. A total of 19 casting trials were performed, for each of the trials; three different cooling conditions were obtained for both the sampling cup and the tensile test bars. Mg has a major influence on the graphite morphology and causes a substantial increase in nodularity. Cu, Si and Sn only cause minor changes in the nodularity, but on the other hand, affect the mechanical properties primarily by altering the pearlite content of the material. Cr and Mo are investigated mainly with respect to their carbide promoting properties. However, no columnar white structure was found in the microstructure. The effect of the microstructure on the thermal history caused by differences in alloying content is also covered.
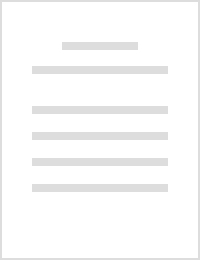
Chemical Papers, Jan 3, 2022
The effects of isothermal oxidation parameters on the oxidation kinetics and morphology of the ox... more The effects of isothermal oxidation parameters on the oxidation kinetics and morphology of the oxides layers obtained on Ti–6Al–4V alloy (Ti64) at 650, 750 and 850 °C for 50 h in dry air were studied. Morphology of the oxide scales was examined by scanning electron microscopy (SEM) and the energy-dispersive X-ray analysis (EDX). The phases in the scales were characterized by X-ray diffraction. The rate of oxidation at the different temperatures was described by a parabolic equation, and the oxidation activation energy value was 191.7 kJ/mol. The parabolic rate constants were 8.80 × 10 –9 , 7.48 × 10 –8 and 7.68 × 10 –7 g 2 /(cm 4 .h) at 650 °C, 750 °C and 850 °C, respectively. The morphologies through the cross section of the oxide layers were analyzed by SEM, spot and line EDX. The analysis of the oxide scale revealed mainly TiO 2 and small amount of Al 2 O 3 . The oxide layers were discontinuous and non-protective layers at 750 °C and 850 °C.

International Journal of Materials Technology and Innovation (Online), Apr 1, 2022
High Entropy Alloys (HEAs) have recently attracted the researchers' attention as a new track in m... more High Entropy Alloys (HEAs) have recently attracted the researchers' attention as a new track in materials design. Research on HEAs has stimulated new ideas and inspired the exploration of the enormous composition space offered by multi-principal element alloys. HEAs can be simply described as alloying systems that are composed of multi-elements in equimolar or near equimolar ratio. Therefore, HEAs have unique properties which significantly differ from the traditional alloy systems. The current review article is concerned with the definition of HEAs, their development history, and their four core effects which make them different from the traditional alloys. Fabrication routes of HEAs with special emphasis on processing via casting technique are surveyed. The innovative microstructure of HEAs that lead to extraordinary mechanical properties is also discussed. Finally, the promising industrial applications and the future insights of these multi principal alloys are covered.
Materials, Oct 5, 2022
This article is an open access article distributed under the terms and conditions of the Creative... more This article is an open access article distributed under the terms and conditions of the Creative Commons Attribution (CC BY

International Journal of Metalcasting, 2020
This work investigates the optimum pouring temperature during semisolid casting (rheo-casting) of... more This work investigates the optimum pouring temperature during semisolid casting (rheo-casting) of Al-17%Si alloy (A390) to obtain the best combination of microstructure modification and wear resistance. Pouring semisolid slurry was done in both metallic and sand molds to observe the effect of cooling rate on the optimum pouring temperature. The molten metal/slurry was poured into the specified mold type through a cooling slope plate which was continuously water cooled. Different pouring temperatures: 670, 690, 710 and 730°C, were applied, and their influence on the microstructure and alloy properties was analyzed. Based on the obtained results, the optimum pouring temperature for semisolid casting was decided for the two mold types. Conventional casting was conducted at the optimum temperature in both metallic and sand molds for comparison. It was observed that rheo-casting using the cooling plate is an effective process in microstructure modification of A390 alloy in terms of refining and redistributing the primary Si and fragmenting the coarse AlFeMnSi phase. The optimum temperatures to obtain small particle size of primary Si, uniform distribution and regular shape using the cooling plate technique were 690°C and 710°C for the metallic and sand molds, respectively. This refinement and homogenization of the microstructure enhanced the hardness and wear resistance of alloy A390.

International Journal of Metalcasting, Sep 16, 2020
Strengthening effect of Y 2 O 3 on AZ92 magnesium alloy using stir casting process has been inves... more Strengthening effect of Y 2 O 3 on AZ92 magnesium alloy using stir casting process has been investigated. Nominal amounts of Y 2 O 3 (0, 1, 1.5, 2, 2.5 and 3 in wt%) were added into the melt vortex in the form of preformed master powder (Mg-30 wt% Y 2 O 3) to improve their wettability with molten AZ92 alloy. The results showed clearly that without Y 2 O 3 addition, the microstructure of the investigated alloy is composed of a-Mg which appeared as coarse dendritic structure, divorced eutectic-containing massive b-Mg 17 Al 12 phase and super-saturated a-Mg solid solution. With Y 2 O 3 addition, the distribution of Y 2 O 3 particles was found within the inter-dendritic regions of the primary a-Mg phase. At 2.5 wt% Y 2 O 3 , a near uniform distribution of Y 2 O 3 particles along the grain boundaries of AZ92 alloy matrix was successfully obtained. However, further addition resulted in agglomeration of Y 2 O 3 particles at 3 wt% addition level. The average tensile strength of the investigated AZ92 alloy was increased from 169 MPa to 198 MPa without a significant reduction in its ductility at optimum addition of 2.5 wt% Y 2 O 3. The fracture mechanism has been also investigated.
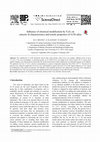
Transactions of Nonferrous Metals Society of China, Jul 1, 2019
The modification of A356 aluminum−silicon alloy using yttrium oxide (Y 2 O 3) was studied. Additi... more The modification of A356 aluminum−silicon alloy using yttrium oxide (Y 2 O 3) was studied. Addition levels of up to 2.5 wt.% Y 2 O 3 were investigated. A premixed powder of Al−30wt.%Y 2 O 3 was added to the melt at about 750 °C using vortex method. Samples were then poured in sand mold. The results showed that evident modification was obtained using the Y 2 O 3 addition. The optimum level was 1.5 wt.%, and was corresponding to a eutectic temperature depression from 568 to 557 °C. The eutectic Si particles were refined in length from 44.8 to 8.3 µm, and modified in aspect ratio from 6.8 to 0.98. Higher additions of Y 2 O 3 caused de-modification of the eutectic Si particles. The ductility of the modified specimens was enhanced by more than 20% compared to the unmodified ones. This was associated with a gradual transfer from cleavage to a more ductile mode of fracture.

Scientific Reports, Jul 12, 2023
The influence of heat treatment processes on microstructure, tensile and tribological properties ... more The influence of heat treatment processes on microstructure, tensile and tribological properties of Ti6Al4V alloy was investigated. The specimens were heated for 30 min at 925 °C and then cooled at various rates by water quenching, air cooling, and furnace cooling. After that, the samples were aged for four hours at 600 °C. Three phases make up the microstructure: primary α-phase (α p), secondary α-phase (α s), and retained β-phase (β r). Cooling in the air and water followed by aging (AC + Aging and WQ + Aging) resulted, α s-phase precipitating inside β r-phase. The highest hardness of 35 HRC was recorded for WQ + Aging specimen due to existence of a high amount of β r-phase and precipitation of α s-phase. On the other hand, the lowest hardness of 26 HRC was obtained for the FC specimen. AC specimen achieved the highest elongation value of 14%. However, WQ + Aging specimen exhibited the highest ultimate tensile strength of 1028 MPa. For WQ + Aging and AC + Aging specimens, the ideal balance of strength and elongation was discovered. The wear resistance of solution-treated specimens was significantly improved by the aging process and 125% improvement could be achieved in WQ compared to WQ + Aging specimens.
Ceramic transactions, Feb 12, 2018

Scientific Reports, Mar 31, 2023
An early corrosion failure of the piping system of a gas heater was reported by a gas complex com... more An early corrosion failure of the piping system of a gas heater was reported by a gas complex company. Local corrosion rates of 0.90 and 0.66 mm/year were observed in the heater piping system. An investigation including visual examination, macrostructure, microstructure (SEM, EDS and XRD), thickness gauging, chemical analysis, and mechanical testing, was performed. The results showed that corrosion damage occurred on the external surface of the pipes. Corrosion occurred at the cold sides of the pipes and elbows. The corrosion pattern is broad and shallow pitting. Some elbows showed an early stage of carbide spheroidization and pearlite decomposition. The EDS microanalysis revealed that the level of sulfur, chlorine, and nitrogen was substantially high in the rust samples. The XRD of the corrosion products showed that the main oxyhydroxide was Akaganeite. The analysis of results showed that the flue gas dew point corrosion was the mechanism of damage, and the root cause was the operation of the heater at low temperatures and the frequent outings of service, combined with evident material drawbacks including low levels of Si, Cu, Ni, Cr, and Mo. These elements should be at their maximum allowable limits of the SA 105 and SA 106 to improve the corrosion resistance of the steel piping components.
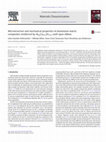
Canadian Metallurgical Quarterly, Jan 19, 2016
Aluminium matrix composites containing 15, 30 and 50 vol.% of pulverized Al 62 Cu 25.5 Fe 12.5 (i... more Aluminium matrix composites containing 15, 30 and 50 vol.% of pulverized Al 62 Cu 25.5 Fe 12.5 (in at.%) melt spun ribbons have been prepared by a vacuum hot pressing (T = 673 K, P = 600 MPa). The microstructure of the initial ribbon and the composites was investigated using X-ray, scanning and transmission electron microscopy. In the as-spun ribbon the quasicrystalline icosahedral phase (i-phase) coexisted with the cubic copper rich β-Al(Cu, Fe) intermetallic compound. The phase composition of Al-Cu-Fe particles changed after consolidation process and the i-phase transformed partially to the ω-Al 70 Cu 20 Fe 10 phase. Additionally, the Θ-Al 2 Cu phase formed at the α(Al)/Al-Cu-Fe particle interfaces. With an increase in volume fraction of the reinforcement the hardness of the composites increased up to HV = 180 for the highest amount of added particles. The ultimate compression strength of the same sample reached the value of 545 MPa.

Journal of Metallurgy, Jan 26, 2015
The main objective of the current work is to investigate the influence of different inoculation c... more The main objective of the current work is to investigate the influence of different inoculation conditions on the microstructure and mechanical properties of heavy section ductile iron (DI) castings. Inoculation treatment was done via one step and double step treatments with different amounts of inoculants. The mechanical properties of the fabricated samples were evaluated. The best inoculation procedure in terms of graphite nodules characteristics and mechanical properties was double inoculation with 0.8% inoculants added at first and 0.2% in the late inoculation step. The presence of Sb in one of the cast alloys controlled the growth of graphite nodules in these heavy section ductile iron castings; however low impact toughness was recorded. The matrix structure of ductile cast iron showed a significant influence not only on the strength and impact properties but also on the fracture mode during testing.
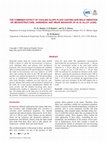
International Journal of Metalcasting, 2020
Semisolid casting using the cooling slope plate method (CSP) is known to refine the microstructur... more Semisolid casting using the cooling slope plate method (CSP) is known to refine the microstructure of hypereutectic aluminum alloys and enhance their mechanical properties. The current research investigates the combined effect of casting using the CSP and mechanical vibration of the mold on microstructure and wear behavior of A390 alloy. After pouring the alloy on the CSP, the mold (sand/ metallic) was vibrated mechanically at 50 Hz during filling and up to solidification. Conventional casting with the same mold vibration conditions was also done for comparison. During CSP casting with mechanical vibration of the mold, the crystal nucleus multiplication inhibits the grain growth, and the dendrite break-up takes place simultaneously, leading to refinement of the microstructure. The double effect of the shear force by melt flow and vibrational turbulence is responsible for fragmentation of the particles. This finding was more pronounced in case of using the sand mold. The quantitative measurements showed that the size of primary Si reduced from * 184 lm for the conventional casting in the sand mold without vibration to * 70 lm when the mold was vibrated and from * 30 lm in case of CSP down to * 20 lm when CSP was followed by mechanical vibration of the mold. However, applying the mechanical vibration after CSP in case of the metallic mold increased the size of primary Si from * 21 to 36 lm. Accordingly, the improvement in the hardness and wear resistance of the CSP samples due to vibration was more significant in case of using the sand mold.

International Journal of Metalcasting
High Entropy Alloys (HEAs) are one of the new families of alloys that gained the attention of res... more High Entropy Alloys (HEAs) are one of the new families of alloys that gained the attention of researchers as a new approach to materials design. The special compositional design of these alloys results in unique microstructures and hence distinguished properties. Corrosion resistance is one of the most important properties of any material used for structural components. Therefore, it is of interest to investigate the electrochemical properties of such recent groups of HEAs alloys to understand their corrosion behavior. In the current study, the electrochemical properties of cast Fe35Mn31Ni18Al13Tix HEAs prepared by induction melting were investigated in 3.5% NaCl and 5% H2SO4 solutions. It was observed that both Ti addition (0.0–3 wt%) and heat treatment (900 °C at 10 and 20 h) altered the alloys microstructure and, hence, affected their corrosion behavior. The base alloy without Ti showed higher resistance to corrosion in both NaCl and H2SO4 solutions compared to Ti-containing allo...
Canadian Metallurgical Quarterly, Dec 14, 2017
The influence of hydrogen on the mechanical properties of Type 304 stainless steel at low tem-Pri... more The influence of hydrogen on the mechanical properties of Type 304 stainless steel at low tem-Principal results obtained are as follows: low-temperature hydrogen embrittlement (LTHE). (2) Non-sensitized specimens hydrogenated and tested under the same conditions showed no such singular embrittlement. (3) Fracture surfaces of specimens that had exhibited singular LTHE behavior revealed an almost wholly intergranular fracture pattern. (4) Hydrogenated specimens exhibited partial recovery of ductility upon dehydrogenation treat-(5) The activation energy governing the recovery process was 51 kJ/mol.
International Journal of Materials Technology and Innovation
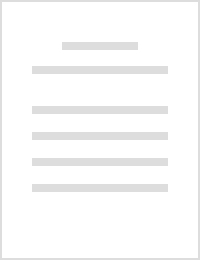
Journal of Materials Engineering and Performance, 2022
Al-Ce alloys are currently receiving attention due to their high-temperature properties. Ultrason... more Al-Ce alloys are currently receiving attention due to their high-temperature properties. Ultrasonic treatment (UST) is a liquid metal processing method, through which the structure of light alloys is modified. In the present study, Al-10 wt.% Ce alloy is prepared by melting and solidification under ultrasonic vibrations. UST temperatures (645-665 °C) are decided using differential scanning calorimetry. This study investigates the morphology of orthorhombic Al11Ce3 compound as influenced by UST, and the corresponding effects on the strength and high-temperature wear properties. It was observed that the shearing behavior of ultrasonic waves fragmented the intermetallic compound. Instead of being coarse and connected lath-like phase, Al11Ce3 was changed to well-fragmented particles. The particle size of Al11Ce3 decreased from ~30 μm to ~3 μm, with UST at 655 °C and up to submicron. The area fraction of the intermetallic particles also increased from ~31 to ~40% after UST at the optimum temperature. The hardness of conventionally solidified alloy increased from ~42 to 50 Hv, and the ultimate compression strength increased from ~290 to 390 MPa, after UST at 655 °C. The fine and well-distributed intermetallic particles observed at the optimum UST temperature increased the wear resistance of the alloy at both RT and higher temperatures.
Uploads
Papers by Shimaa El-Hadad