Papers by Reginaldo Coelho
Lecture notes in mechanical engineering, Sep 23, 2023
CIRP Annals, 2017
This paper presents the proof-of-concept of an innovative finish machining process wherein materi... more This paper presents the proof-of-concept of an innovative finish machining process wherein material is removed by abrasives suspended in a dense aqueous mixture of cornstarch, which serves as a smart finishing medium. Depending on the mode and rate at which said suspension is subject to strain, it transforms rapidly and reversibly, from being liquid-like, to a state that exhibits jamming-induced solidlike behaviour. This facilitates fine control over the level of mechanical interaction between the workpiece and the abrasives. The research clarifies fundamental process mechanics, and demonstrates the efficacy of exploiting this intriguing phenomenon in surface finishing and edge honing applications.

The transport in the edge region and through the scrape-off-layer (SOL) at the outboard mid-plane... more The transport in the edge region and through the scrape-off-layer (SOL) at the outboard mid-plane of magnetically confined toroidal plasmas is known to be strongly intermittent and dominated by filamentary structures of enhanced plasma pressure – plasma blobs. These structures are generated in the edge region and propagate through the SOL with velocities up to a few percent of the ion acoustic speed. They play a significant role in setting up the plasma profiles in the SOL and for the power deposition profiles. We have investigated the transport dynamics, the ensuing density and pressure profiles in the SOL, and estimated power depositions on plasma facing components by applying the HESEL code. HESEL is an energy conserving four-field Braginskii model governing the dynamical evolution of generalized vorticity, density, electron, and ion pressures [1]. The parallel dynamics in the SOL is parametrized and different divertor conditions attached or detached are mimicked by applying shea...
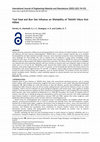
International Journal of Engineering Materials and Manufacture, 2021
Surface texturing, using micro-milling, has promising applications in the industry of medical imp... more Surface texturing, using micro-milling, has promising applications in the industry of medical implants, since it can assist cell adhesion and thus improve osseointegration. Ti6Al4V alloy is used as implant material due to its excellent biocompatibility and high mechanical strength. However, those mechanical properties reduce machinability creating some challenges for micro-milling. The way to initially assess cell adhesion is using surface wettability, usually conducted with water. At the present work, micro-channels were machined in Ti6Al4V by micro end-milling with 500 µm width per 50 µm depth with 1000 µm distant from each other. The effect of feed per tooth (fz) on wettability was analysed and some interesting relations with burrs formed on channel walls were obtained. Values of feed per tooth were 3, 6, 12 and 15 µm. Wettability results showed that slotted surface is more hydrophilic on channel direction, with contact angles around 30° to 43°. In contrast, on the perpendicular ...

Journal of The Brazilian Society of Mechanical Sciences and Engineering, Sep 1, 2011
The needs to comply with an increasingly competitive international market lead industries to some... more The needs to comply with an increasingly competitive international market lead industries to some innovative solutions, such as the use of robotic arms as machine tools. Although these solutions present some well known drawbacks, there are some advantages and niches of application where success is possible. The present work investigates the use of such pieces of equipment to machine aluminum alloys AA2024 applying high speed machining (HSM) technique, assessing surface finishing as a function of different orientation angles between end mill and machined surface. It also tests the best condition to machine foam for prototyping applications. Results indicate that the directions close to the normal are the best compromises because of dynamic stability of the robot arm structure and roughness as low as 4 µm Ra are possible to be achieved in aluminum alloys. A complex shape such as a semi sphere can be easily machined in foam for rapid and accurate prototype machining. Surface finishing can be very smooth and well suitable for industrial applications in such materials.
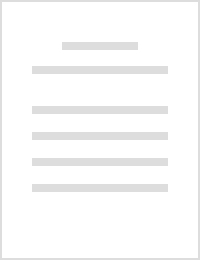
Proceedings of the Institution of Mechanical Engineers, Part B: Journal of Engineering Manufacture, Aug 8, 2016
Cusps and scallops of hardened steel moulds produced by high-speed milling using a ball-nose end ... more Cusps and scallops of hardened steel moulds produced by high-speed milling using a ball-nose end mill were mathematically modelled, characterised by microscopy and experimentally validated. The experimental results show that the part material is crushed or ploughed near the cutter centre, where the cutting speed is very low. This kinematic singularity, associated with tool feed, compresses and bends the ball-nose end mill axially. Because of this double effect, the end mill marks on the part at the end of the milling path cause surface damage and dimensional errors to the hardened mould. A mathematical model may predict the formation of the cusps and scallops and be of use in computer numerical control or computer-aided manufacturing programming to obtain the desired part topography.
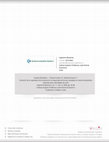
Ingeniería Mecánica, 2008
el corte con altas velocidades en superficies con formas complejas. Fueron maquinados cuerpos de ... more el corte con altas velocidades en superficies con formas complejas. Fueron maquinados cuerpos de prueba con 1 / 4 de circunferencia en acero AISI D2 y H13 con dureza de 53 y 50 HRC, respectivamente. Los experimentos fueron realizados utilizando la estrategia "raster" con herramientas esféricas (Ball Nose) en un centro de maquinado de tres ejes. Los valores de rugosidad y dureza HRC fueron medidos perpendiculares a la dirección de corte en cuatro regiones diferentes. Los resultados demuestran que las regiones de diámetro mínimo, próximas a la línea central de la herramienta y en el punto de contacto del diámetro máximo, presentan los menores valores de rugosidad. No ocurren modificaciones significativas en los valores de HRC y no hubo formación de capa blanca en ninguno de los dos materiales. Considerándose los valores de microdureza medidas radialmente en los cuerpos de prueba no se observa ninguna variación de la microdureza. Palabras claves: Rugosidad Ra; altas velocidades de corte; moldes y matrices; dureza HRC. Variation of roughness and of the hardness in machining of complex forms in hardness steel using high speed cutting.
Industrial Diamond Review, 1999
Machining Science and Technology, Jul 1, 2006
Tapping is one of the most intensively used operations for internal threads with diameters below ... more Tapping is one of the most intensively used operations for internal threads with diameters below about 15 mm. When a tap fails, the workpiece has a significant added value. The present work investigates some aspects of wear and performance when solid carbide coated taps M10 Â1.5 cut hardened AISI H13 and AISI D2. The results indicated that it was possible to make threads on hardened AISI D2, although the number of holes was essentially low and tool breakage was often. Threads on hardened AISI H13 was possible with reasonably low tool wear. Cutting surface presented some indication of small flaws due to the adhered material on the taps.
Journal of materials research and technology, Nov 1, 2021
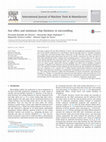
International Journal of Machine Tools & Manufacture, Feb 1, 2015
This paper compares the size effect behaviour in micro-and macromilling by applying Analysis of V... more This paper compares the size effect behaviour in micro-and macromilling by applying Analysis of Variance on the specific cutting force (k c) and relating it with the tool edge radius (r e), workpiece roughness (R a), cutting force and chip formation when cutting slots in AISI 1045 steel. Size effect is observed in micromilling through hyper-proportional increase of the specific cutting force for feeds per tooth (f) lower than endmill edge radius, reaching levels of grinding process (∼70 GPa) when f≅r e /10. This particular milling condition does not produce chips. The minimum uncut chip thickness (h min) varied between 22% and 36% of the endmill edge radius. This range was determined by proposing a curve (k c /R a versus f/r e) where specific cutting force becomes amplified (size effect) due to workpiece roughness association. In addition to the minimum uncut chip thickness, there is a cutting thickness between h min and r e that optimizes workpiece surface integrity and not only forms the chip completely. This thickness may be as important as h min. Besides this, a relation between deformation mechanisms during chip formation and cutting force oscillations is proposed for micromilling and also related to tool tip radius (r ε). This cutting force behaviour enables the determination of certain characteristic chip thicknesses including h min. Finally, it is concluded that minimum uncut chip thickness varies practically from 1/4 to 1/3 of tool cutting edge, regardless of workpiece material, tool geometry, mechanical machining process and technique used for measuring or estimating h min , i.e. numerical, analytical or experimental.
Industrial Diamond Review, 2001
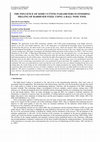
The application of the HSC technology, together with CAM system programming, seem highly attracti... more The application of the HSC technology, together with CAM system programming, seem highly attractive, mainly in the dies and mould industries. Due to the importance of technological knowledge about all parameters involved into this process, the main result is not, in most of the cases, which one desired. Thus, without the domain of this technological knowledge occur a decrease of the productivity and an increase of the costs, mainly the costs related with the cutting tools. This paper investigates the finishing milling operation on flat surfaces of a WNr 1.2367 tool steel, hardened to 50-52 HRc. A High Speed Machining Center was used for the experimental tests. A 6 mm diameter ball nose end milling cutter was used. Three levels of feed per flute (fz) and three radial depth of cut (ae) was evaluated, both input parameters for the CAM systems, which directly affect the productivity and the surface finishing. The milling strategy used was the offset. The tests were carried out in two stages. The first stage, tests were performed in downcut direction. In the second stage experimental tests were performed in upcut direction. The roughness in all regions was evaluated. The tests were performed in a such way that the wear of the tool was very limited. Looking for the best set of cutting data, the results bring out the relationships between the cutting parameters for surface finishing. The increase on feed per flute showed direct increase of surface roughness, but the increase of radial depth of cut showed a larger influence. This shows a possibility to reduce a cut time raising only the feed per flute at same radial depth of cut. In all cases, however, the upcut direction showed better results than downcut for surface roughness.
Uploads
Papers by Reginaldo Coelho