Papers by Prof. Dr. Shukry H. Aghdeab
Bio web of conferences/BIO web of conferences, 2024
AIP conference proceedings, 2024
AIP conference proceedings, 2024
Maǧallaẗ al-handasaẗ wa-al-tiknūlūǧiyā, Dec 7, 2023
Al-Qadisiyah Journal for Engineering Sciences, 2014
Maǧallaẗ al-handasaẗ wa-al-tiknūlūǧiyā, Oct 1, 2015
EDM (Electric Discharge Machining) machine was used for machining of conducting cutting materials... more EDM (Electric Discharge Machining) machine was used for machining of conducting cutting materials such as steel 304 in dielectric solution (diesel fuel) by supplied by DC current values (10, 20, 30, 42 and 50A). Voltage of (140V) was used to cut (1) mm thickness. The experimental results reveal that the material removal rate enhanced by increasing the current values also show that the Electrode wear ratio rises with increase in the current values. It is also concluded that the material removal rate reduces with increasing the pulse off time values and the electrode wear ratio.
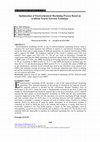
Maǧallaẗ al-handasaẗ wa-al-tiknūlūǧiyā, Dec 1, 2016
Electrochemical machining (ECM) is one of nonconventional machining process used to operation the... more Electrochemical machining (ECM) is one of nonconventional machining process used to operation the most harsh materials that difficult to operate in conventional machining. This search has been used to study impact of different parameters on material removal rate (MRR) and to improve the MRR. The workpiece material in this search is stainless steel 316L, tool material from copper and NaCl (10, 25, 50) g/l was used as electrolyte. Through the experiments noted that the MRR increasing at increased current from (50 to 200) the increasing in MRR reach to 57.60%, also MRR increasing at increasing electrolyte concentration from (10 to 50) g/l increasing in MRR (reach) to 75.17 % and MRR decreasing at increased gap size from (0.5 to 1.5) mm the decreasing in MRR reach to 39.2 %. To predict the values of MRR and to get optimization, artificial neural network was used to get minimum mean squared error (MSE) and minimum average percentage error. In network, separated some values to training set and the remaining for testing set and it was noted that the predicated and experimental values are very close to each other.
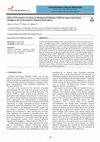
Instrumentation Mesure Métrologie
Chemical Mechanical Polishing (CMP) is the polishing process where the top surface of a wafer is ... more Chemical Mechanical Polishing (CMP) is the polishing process where the top surface of a wafer is smoothed using a slurry containing abrasive grit as well as reactive chemical agents. The polishing process is partly mechanical and partly chemical. The mechanical element's main advantage is that it is achieved without great effort to manufacture and supplies good-quality general mechanical and electrical properties. In the current study, the invention reckons on the chemical and mechanical properties of the composition particles (abrasive slurry) utilized to polish silicon surfaces traveling through chemical-mechanical polishing (CMP). MINITAB 17 software was used to estimate the influence of the (CMP) input variables on the surface roughness (Ra) of the silicon workpiece. Other process input variables were disk speed (rpm), the dose of abrasive, the grain size of the abrasive, and the type of slurry. In order to get the best response surface roughness, the current findings show t...

Advances in Science and Technology Research Journal
Metal matrix composite (MCC) exhibits significantly better properties, like hardness, low density... more Metal matrix composite (MCC) exhibits significantly better properties, like hardness, low density, high tensile strength, and good wear resistance compared to any alloy or other metals. In the present study, the effect of using different proportions (2, 4, 8 and 10 wt.%) of microscopic slide glass nanoparticles (MSGNPs) on the properties of Al-7075 alloy was investigated. The results of the experimental study of the metallurgical characterization and mechanical properties of aluminum MMC that formed by stir casting method were obtained. Stir casting is a process of introducing a reinforcing material into a molten metal by stirring action. Also, the results of the aluminum MMC were compared with those for the base alloy material. Optical microscopy, scanning electron microscope (SEM), energy dispersive spectroscopy (EDS), and X-ray diffraction study (XRD) were carried out to analyze the microstructure and the dispersion of the (MSGNPs) into the composite alloy specimens. Regarding the mechanical properties, the Rockwell hardness gradually increased when the addition of MSGNPs was raised from 0 to 10 wt.%. Additionally, there was a rise in the ultimate tensile strength, peaking at the incorporation rate of 4 wt.% MSGNPs and thereafter, this strength declined. Therefore, the addition of microscopic slide glass nanoparticles to the Al-7075 is virtuous to enhance the properties of this alloy for the engineering application.
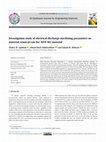
Al-Qadisiyah Journal for Engineering Sciences
EDM (Electrical Discharge Machining) is a common non-traditional machining technique for manufact... more EDM (Electrical Discharge Machining) is a common non-traditional machining technique for manufacture geometry parts made of intricate or extremely rigid metals that are challenging to manufacture using conventional manufacturing techniques. Electrical discharge machining by utilizing electrical discharge erosion, classify the meaning of material removal (MR). This paper's main objective is to discuss the ideal EDM parameters in order to use high-speed steel as workpiece AISI M2 and with using brass & copper as electrodes. Pulse on-time are (100, 150, and 200 µs), Current (10, 24 and 42 A) and Pulse off-time (4, 12 and 25 µs) are the input parameters effect on the material removal rate (MRR) used in the experimental work. The present study's findings shown that the highest MRR with using copper & brass as electrodes with pulse on-time 200 µs, pulse off-time 12 µs and current 42 A, at (0.31284 g/min and 0.18769) respectively, and the lowest average value of the removed materia...
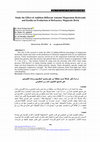
Maǧallaẗ al-handasaẗ wa-al-tiknūlūǧiyā, Dec 1, 2016
This aim of this research is study the effect of adding different percentages of magnesium hydrox... more This aim of this research is study the effect of adding different percentages of magnesium hydroxide, kaolin and water on the production of refractory magnesite brick by use transformer process. Firstly transformative process carried out on the magnesium hydroxide and kaolin to obtain fine particle, after that mixture fine particle Burn in electric furnace at temperature (1000 o C) for (2 hr). The mixture Formed by using semi dry pressing with (10)% water under pressure (500 Kg/cm 2) to obtain forming sample we carried out drying process ,and we can many test from inspection for obtain porosity, density, Water absorption, specific weight and more properties compressive strength. We fined finish refractory brick from light type where the resulted density is equal to (1.33 g\cm3) and suits applications that need to lightness weight with durability.
Design Engineering, Sep 12, 2021
Design Engineering, Sep 12, 2021
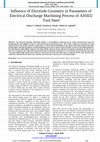
The Electrical Discharge Machining (EDM) is a nontraditional cutting process for metals removing ... more The Electrical Discharge Machining (EDM) is a nontraditional cutting process for metals removing based upon the fundamental fact that negligible tool force is generated during the machining process. Also, EDM is employed in producing very hard materials that are electrically conductive. In this paper, we will study and investigation of the effects of electrode geometry (tip radius and tip angles) with input parameters of EDM machining process such as (pulse current and pulse on time) on the output parameters like Metal Removal Rate (MRR), Electrode Wear Ratio (EWR), thickness of Heat Affected Zone (HAZ) of machining of AISI D2 tool steel were investigated. The results of the experimental study are discussed in this paper. It is revealed that conical electrode with radius 1 mm gives highest MRR and the lowest EWR was with conical electrode with radius 0mm as compared with the other electrodes, the results have indicated that the White Layer Thickness (WLT) increases with increase in ...
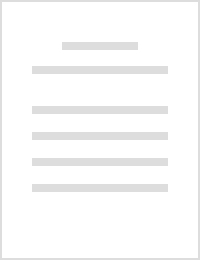
Al-Khwarizmi Engineering Journal, 2018
Electrical Discharge Machining (EDM) is a non-traditional cutting technique for metals removing w... more Electrical Discharge Machining (EDM) is a non-traditional cutting technique for metals removing which is relied upon the basic fact that negligible tool force is produced during the machining process. Also, electrical discharge machining is used in manufacturing very hard materials that are electrically conductive. Regarding the electrical discharge machining procedure, the most significant factor of the cutting parameter is the surface roughness (Ra). Conventional try and error method is time consuming as well as high cost. The purpose of the present research is to develop a mathematical model using response graph modeling (RGM). The impact of various parameters such as (current, pulsation on time and pulsation off time) are studied on the surface roughness in the present research. 27 samples were run by using CNC-EDM machine which used for cutting steel 304 with dielectric solution of gas oil by supplied DC current values (10, 20, and 30A). Voltage of (140V) uses to cut 1.7mm thic...
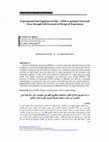
Maǧallaẗ al-handasaẗ wa-al-tiknūlūǧiyā, Feb 1, 2015
Electrical discharge machining (EDM) is a process where the material removal of the workpiece is ... more Electrical discharge machining (EDM) is a process where the material removal of the workpiece is achieved through high frequency sparks between the tool (electrode) and the workpiece immersed into the dielectric solution. It is commonly used to produce moulds and dies, to drill small, burr free holes and to make prototypes for the aerospace and electronics markets. In this work, micro-holeswere fabricated on copper alloys by using EDM. The output responses investigated was electrode wear weight (EWW). Full factorial of Design of Experiment (DOE) module in Minitab was used as a principal methodology to examine the effects of current and machining time over output responses. Experimental results indicate that the EWW was mainly affected by current, and can be reduced by increasing the current parameter. Minimum EWW (0.12gm) obtained at 10A.
Maǧallaẗ al-handasaẗ wa-al-tiknūlūǧiyā, Aug 25, 2020
Al-Qadisiyah Journal for Engineering Sciences, 2014
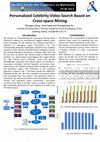
Engineering and Technology Journal, 2020
Electrical Discharge Machining (EDM) is extensively used to manufacture different conductive mate... more Electrical Discharge Machining (EDM) is extensively used to manufacture different conductive materials, including difficult to machine materials with intricate profiles. Powder Mixed Electro-Discharge Machining (PMEDM) is a modern innovation in promoting the capabilities of conventional EDM. In this process, suitable materials in fine powder form are mixed in the dielectric fluid. An equal percentage of graphite and silicon carbide powders have been mixed together with the transformer oil and used as the dielectric media in this work. The aim of this study is to investigate the effect of some process parameters such as peak current, pulse-on time, and powder concentration of machining High-speed steel (HSS)/(M2) on the material removal rate (MRR), tool wear rate (TWR) and the surface roughness (Ra). Experiments have been designed and analyzed using Response Surface Methodology (RSM) approach by adopting a face-centered central composite design (FCCD). It is found that added graphite...
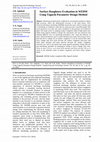
Maǧallaẗ al-handasaẗ wa-al-tiknūlūǧiyā, Jan 25, 2018
Machining of hard metal is difficult by conventional method to obtain high accuracy where the dim... more Machining of hard metal is difficult by conventional method to obtain high accuracy where the dimensional accuracy is the main factor. Wire electrical discharge machining (WEDM) extensively used, which is mostly used in machining of conductive materials by using precisely controlled sparks that occur between a very thin wire and a workpiece in the presence of a dielectric fluid. This study serves in studying surface roughness (SR) of high speed steel (HSS) using taguchi method to design the experiment, this was achieved with utilizing different wire cut machining parameters and study the behavior of these control parameters such as pulse duration (µs), pulse interval (µs), Servo feed and Servo voltage (V) on surface roughness. It can be noticed that when servo voltage and servo feed increase the surface roughness decreases and when pulse duration and pulse interval increase the surface roughness increases too, and It was found with using taguchi parameter design that the best machining variables of combination setting is Servo Voltage (22) volts, Pulse on time (110) μs, servo feed (450) mm/min and Pulse off time (30) μs to reach to the minimum value of surface roughness and hence better surface finish.
Uploads
Papers by Prof. Dr. Shukry H. Aghdeab