Papers by Pavel Podrabinnik
Materials Science Forum, 2015
In this paper the principal feasibility of using cold gas dynamic spraying with laser post treatm... more In this paper the principal feasibility of using cold gas dynamic spraying with laser post treatment technique to create Al-Ni composite coatings is demonstrated. The prepared mixture of two powders was coated on an aluminum substrate and laser annealed. As a result the AlxNy intermetallic phases were observed in the coating. Obtained laser-annealed coatings were studied be means of optical and electron microscopy (SEM), energy dispersive spectroscopy (EDS), X-ray diffractometry and compared with as-sprayed coatings. Effects of laser processing parameters, such as scanning speed, power and beam shape on microstructural evolution of the composite coatings were discussed and optimal regimes for laser assisted CS were determined.
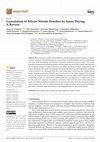
Materials
Spray drying is a widely used method of converting liquid material (aqueous or organic solutions,... more Spray drying is a widely used method of converting liquid material (aqueous or organic solutions, emulsions and suspensions) into a dry powder. Good flowability, narrow size distribution, and controllable morphology are inherent in powders produced by spray drying. This review considers the granulation factors that influence the final properties of the silicon nitride dried powders. The first group includes the types of atomizers, manifolds, and drying chamber configurations. The process parameters fall into the second group and include the following: inlet temperature, atomizing air flow, feed flow rate, drying gas flow rate, outlet temperature, and drying time. Finally, the last group, feedstock parameters, includes many factors such as feed surface tension, feed viscosity, solvent type, solid particle concentration, and additives. Given the large number of factors affecting morphology, particle size and moisture, optimizing the spray drying process is usually achieved by the “tri...
Materials
Potential relations of tribological characteristics of aluminum antifriction alloys with their co... more Potential relations of tribological characteristics of aluminum antifriction alloys with their compositions and mechanical properties were investigated. In this regard, the properties of eight aluminum alloys containing tin from 5.4% to 11% doped with lead, copper, silicon, zinc, magnesium, and titanium were studied. Mechanical properties such as hardness, strength, relative extension, and impact strength were analyzed. Within the tribological tests seizure load and wear of material were evaluated and secondary structures were studied afterwards. The absence of a definitive correlation between tribological behavior and mechanical properties was shown. It was determined that doping tin over 6% is excessive. The seizure load of the alloys increases with the magnesium content. Secondary structures of the alloys with higher wear rates contain one order less magnesium and tin.
PROCEEDINGS OF THE II INTERNATIONAL CONFERENCE ON ADVANCES IN MATERIALS, SYSTEMS AND TECHNOLOGIES: (CAMSTech-II 2021)
Coatings, 2021
The microstructure of the coating obtained by cold gas-dynamic spraying was investigated. A Cu-Al... more The microstructure of the coating obtained by cold gas-dynamic spraying was investigated. A Cu-Al2O3-Zn powder blend was sprayed onto a copper substrate to restore a worn copper contact wire. The coating thickness was 1–2.5 mm. Mechanisms of coating formation are discussed on the basis of microstructure studies. The relationship between the microstructure and the properties of the coating such as adhesion strength and electrical conductivity is shown. Improved adhesion strength was achieved through substrate surface preprocessing with coarse Al2O3 particles.
Materials, 2022
SiC-TiB2-TiC composites with matrices consisting of semiconductor material (SiC), conductive mate... more SiC-TiB2-TiC composites with matrices consisting of semiconductor material (SiC), conductive materials (TiB2-TiC), or their combination were fabricated by spark plasma sintering (SPS) at 2000 °C in a vacuum under a pressure of 80 MPa for 3 min. The composition and microstructure of the obtained composites were studied by X-ray diffraction and a scanning electron microscope equipped with an energy-dispersive detector. The flexural strength, Vickers hardness, and fracture toughness of SPSed samples were determined. Based on the observations in this work, three variations of the sintering process were proposed with different matrix compositions. The dense (99.7%) 60SiC-25TiB2-15TiC vol.% sintered ceramic composites exhibited the highest strength and hardness values of the studied composites, as well as a fracture toughness of 6.2 MPa·m1/2.
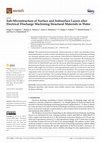
Metals, 2021
The material removal mechanism, submicrostructure of surface and subsurface layers, nanotransform... more The material removal mechanism, submicrostructure of surface and subsurface layers, nanotransformations occurred in surface and subsurface layers during electrical discharge machining two structural materials such as anti-corrosion X10CrNiTi18-10 (12kH18N10T) steel of austenite class and 2024 (D16) duralumin in a deionized water medium were researched. The machining was conducted using a brass tool of 0.25 mm in diameter. The measured discharge gap is 45–60 µm for X10CrNiTi18-10 (12kH18N10T) steel and 105–120 µm for 2024 (D16) duralumin. Surface roughness parameters are arithmetic mean deviation (Ra) of 4.61 µm, 10-point height (Rz) of 28.73 µm, maximum peak-to-valley height (Rtm) of 29.50 µm, mean spacing between peaks (Sm) of 18.0 µm for steel; Ra of 5.41 µm, Rz of 35.29 µm, Rtm of 43.17 µm, Sm of 30.0 µm for duralumin. The recast layer with adsorbed components of the wire tool electrode and carbides was observed up to the depth of 4–6 µm for steel and 2.5–4 µm for duralumin. The ...
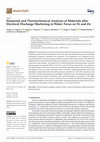
Materials, 2021
The mechanism of the material destruction under discharge pulses and material removal mechanism b... more The mechanism of the material destruction under discharge pulses and material removal mechanism based on the thermochemical nature of the electrical erosion during electrical discharge machining of conductive materials were researched. The experiments were conducted for two structural materials used in the aerospace industry, namely austenite anticorrosion X10CrNiTi18-10 (12kH18N10T) steel and 2024 (D16) duralumin, machined by a brass tool of 0.25 mm in diameter in a deionized water medium. The optimized wire electrical discharge machining factors, measured discharge gaps (recommended offset is 170–175 µm and 195–199 µm, respectively), X-ray photoelectron spectroscopy for both types of materials are reported. Elemental analysis showed the presence of metallic Zn, CuO, iron oxides, chromium oxides, and 58.07% carbides (precipitation and normal atmospheric contamination) for steel and the presence of metallic Zn, CuO, ZnO, aluminum oxide, and 40.37% carbides (contamination) for duralu...
Entropy, 2019
The paper investigates the relationship between the tribological properties/compositions of new a... more The paper investigates the relationship between the tribological properties/compositions of new aluminum antifriction alloys and compositions of the secondary structures formed on their friction surfaces. Eight alloys with various compositions have been analyzed. The elemental compositions of the secondary structures on their friction surfaces have been determined. The relationship between the alloy secondary structure compositions with wear rate has been found. An attempt has been made to determine the secondary structure composition patterns based on the non-equilibrium thermodynamics and self-organization theory.
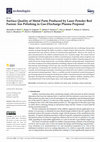
Technologies, 2021
Additive manufacturing has evolved over the past decades into a technology that provides freedom ... more Additive manufacturing has evolved over the past decades into a technology that provides freedom of design through the ability to produce complex-shaped solid structures, reducing the operational time and material volumes in manufacturing significantly. However, the surface of parts manufactured by the additive method remains now extremely rough. The current trend of expanding the industrial application of additive manufacturing is researching surface roughness and finishing. Moreover, the limited choice of materials suitable for additive manufacturing does not satisfy the diverse design requirements, necessitating additional coatings deposition. Requirements for surface treatment and coating deposition technology depend on the intended use of the parts, their material, and technology. In most cases, they cannot be determined based on existing knowledge and experience. It determines the scientific relevance of the analytical research and development of scientific and technological p...
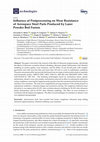
Technologies, 2020
The paper is devoted to the research of the effect of ultrasonic postprocessing—specifically, the... more The paper is devoted to the research of the effect of ultrasonic postprocessing—specifically, the effects of ultrasonic cavitation-abrasive finishing, ultrasonic plastic deformation, and vibration tumbling on surface quality, wear resistance, and the ability of real aircraft parts with complex geometries and with sizes less than and more than 100 mm to work in exploitation conditions. The parts were produced by laser powder bed fusion from two types of anticorrosion steels of austenitic and martensitic grades—20Kh13 (DIN 1.4021, X20Cr13, AISI 420) and 12Kh18N9T (DIN 1.4541, X10CrNiTi18-10, AISI 321). The finishing technologies based on mechanical action—plastic deformation, abrasive wear, and complex mechanolysis showed an effect on reducing the submicron surface roughness, removing the trapped powder granules from the manufactured functional surfaces and their wear resistance. The tests were completed by proving resistance of the produced parts to exploitation conditions—vibration ...
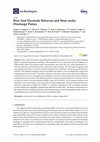
Technologies, 2020
This work is devoted to researching the tool electrode behavior and wear under discharge pulses a... more This work is devoted to researching the tool electrode behavior and wear under discharge pulses at electrical discharge machining. The experiments were conducted on the workpieces of 12Kh18N10T (AISI 321) chrome-nickel anti-corrosion steel and D16 (AA 2024) duralumin by a 0.25-mm-diameter CuZn35 brass tool in a deionized water medium. The developed diagnostic and monitoring mean based on acoustic emission registered the oscillations accompanying machining at 4–8 kHz. The obtained workpiece and non-profiled tool surfaces were investigated by optical and scanning electron microscopy. Calculated volumetric and mass removal rates showed the difference in the character of wear at roughing and finishing. It was shown that interaction between material components in anti-corrosion steel machining had an explosive character between Zn of brass and Ni of steel at a micron level and formed multiple craters of 30–100 µm. The secondary structure and topology of worn tool surfaces were caused by ...
Journal of Manufacturing and Materials Processing, 2020
The work is devoted to the research of the changes that occur in the subsurface layer of the work... more The work is devoted to the research of the changes that occur in the subsurface layer of the workpiece during electrical discharge machining of conductive nanocomposite based on alumina with the use of a brass tool. The nanocomposite of Al2O3 + 30% of TiC was electroerosively machined in a water and hydrocarbon oil. The process of electrical discharge machining is accompanied by oscillations that were registered by diagnostic means. The obtained surface of the samples was researched by the means of scanning electron microscopy and X-ray photoelectron spectroscopy. The observed surface and subsurface changes provide grounding for the conclusions on the nature of processes and reactions that occur between two electrodes and nanomodification of the obtained surfaces that can be an advantage for a series of applications.
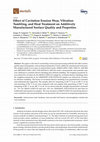
Metals, 2020
The paper is devoted to researching various post-processing methods that affect surface quality, ... more The paper is devoted to researching various post-processing methods that affect surface quality, physical properties, and mechanical properties of laser additively manufactured steel parts. The samples made of two types of anticorrosion steels—20kH13 (DIN 1.4021, X20Cr13, AISI 420) and 12kH18N9T (DIN 1.4541, X10CrNiTi18-10, AISI 321) steels—of martensitic and austenitic class were subjected to cavitation abrasive finishing and vibration tumbling. The roughness parameter Ra was reduced by 4.2 times for the 20kH13 (X20Cr13) sample by cavitation-abrasive finishing when the roughness parameter Ra for 12kH18N9T (X10CrNiTi18-10) sample was reduced by 2.8 times by vibratory tumbling. The factors of cavitation-abrasive finishing were quantitatively evaluated and mathematically supported. The samples after low tempering at 240 °C in air, at 680 °C in oil, and annealing at 760 °C in air were compared with cast samples after quenching at 1030 °C and tempering at 240 °C in air, 680 °C in oil. I...
Applied Sciences, 2019
Gas-phase flows occurring in a plume in a processing zone during selective laser melting (SLM) ca... more Gas-phase flows occurring in a plume in a processing zone during selective laser melting (SLM) can significantly affect the quality of the process. To further enhance SLM performance, the characteristics of the flows should be considered. In this article, the vapor-gas jet emerging from the laser processing zone was studied. It was visualized by interferometry to evaluate flow velocity, geometry and changes in refractory index depending on laser power. The velocity and pressure fields of the vapor jet and the entrained ambient gas were estimated by mathematical modeling. It was shown that the increase of laser power led to higher jet velocity and greater change in its refractory index. The latter also was used to evaluate the content of metal vapor in the plume and its influence on the absorption of laser radiation.
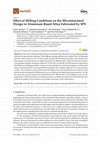
Metals, 2019
In this work, aluminum-based alloys were mechanically alloyed by various doping elements followed... more In this work, aluminum-based alloys were mechanically alloyed by various doping elements followed by spark plasma sintering. Three different mixing methods were studied. First, all elemental powders were mixed for 24 h. In the second and the third method, powders were divided into three groups, and each group was milled separately for different times. Then the obtained mixtures were grouped together and again milled for 12 and 24 h, for the M2 and M3 mixtures, respectively. The influence of milling parameters on the microstructural features of sintered samples was determined using a scanning electron microscope (SEM) equipped with an energy-dispersive X-ray spectroscopy system. The correlation observed between the milling time and microstructural evolution of the powder particles during the milling process was to determine the optimal process parameters. For the first time, the present research has demonstrated the effectiveness of the milling process for the preparation of tailored...
Lubricants, 2019
The influence of the nonequilibrium state of a material on its wear resistance is investigated in... more The influence of the nonequilibrium state of a material on its wear resistance is investigated in this study. Using methods of non-equilibrium thermodynamics and the theory of self-organization, a non-equilibrium material is shown to possess an overall lower wear rate than a material in an equilibrium state. This was experimentally demonstrated to be the case in different materials and tribosystems, such as Babbit operating in complete lubrication conditions, copper in the current collector and a cutting tool with a coating applied on it.
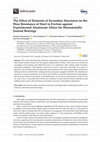
Lubricants, 2019
This article describes the elemental composition of secondary structures formed on the steel cont... more This article describes the elemental composition of secondary structures formed on the steel contact surface during wear test against experimental Al alloys. Wear tests were carried out according to the rotating steel roller-fixed shoe of an antifriction alloy scheme under boundary lubrication conditions. The duration of the test was 40 h, and motor oil M14V2 was used as a lubricant. The microstructure and elemental characterization of the steel surface before and after the tribological test was obtained by scanning electron microscopy equipped with EDX. The simultaneous presence of various constituents of oil, steel, and Al alloys can produce both positive and negative effects on the friction characteristic of the tribosystem. It was shown that presence of Mo, F, S, Si, Ni, and Cr have a favorable effect on the wear resistance of steel and the friction coefficient of the rubbing surfaces due to the formation of secondary structures with optimal composition.
Within the task of replacing bronze journal bearings with aluminum the processes taking part on f... more Within the task of replacing bronze journal bearings with aluminum the processes taking part on friction surface of high-alloyed aluminum alloys working with steel are investigated. The surface and subsurface layer of experimental aluminum bearings were studied before and after tribological tests by scanning electron microscopy including energy-dispersive analysis. Both structural and composition changes in surface layer are shown. It has been revealed that secondary structures are formed on the surface during friction process and include all the chemical elements of the tribosystem which is a consequence of its self-organization. The interaction behavior of some chemical elements of tribological system is discussed.
Mechanics & Industry, 2016
Nowadays the technological perspectives of selective laser melting are limited by available equip... more Nowadays the technological perspectives of selective laser melting are limited by available equipment on the market. Most of the manufactures produce SLM-machine with the maximum power of laser system 200 W, this makes processing very slow and it significantly reduces the field of potential applications for the technology. Meanwhile the limits of laser power are linked to a problem of its effective use. In the current work, the future perspectives of technology are investigated by modeling of 3D technological fields.
Uploads
Papers by Pavel Podrabinnik