Papers by Mirosław Łomozik
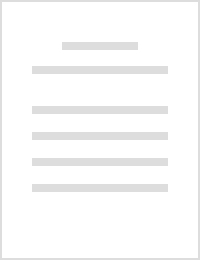
Biuletyn Instytutu Spawalnictwa
The introduction contains information (found in available reference publications) concerning the ... more The introduction contains information (found in available reference publications) concerning the weldability of steel S1300QL. The introduction also presents general information concerning the effect of the microstructure and the chemical composition of filler metals used in the welding of high-strength steels on the mechanical properties of weld deposit. The subject of simulation tests (discussed in the article) was structural steel S1300QL having a yield point of more than 900 MPa S1300QL. Simulations involved both single (Tmax = 1250°C) and double welding thermal cycles (Tmax = 1250°C + 600°C, Tmax = 1250°C + 760°C and Tmax = 1250°C + 900°C) as well as cooling times t8/5 = 3 s, 5 s and 10 s. Specimens with simulated HAZ areas were subjected to impact strength tests performed at a temperature of -40°C and +20°C, Vickers hardness tests (HV10) and microscopic metallographic tests involving the use of light microscopy. The test results are presented in related diagrams and photograph...
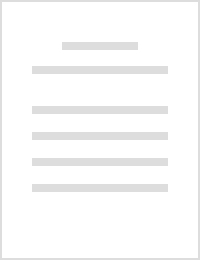
Biuletyn Instytutu Spawalnictwa, 2021
Simulation tests discussed in the article involved structural steel S1100QL having a yield point ... more Simulation tests discussed in the article involved structural steel S1100QL having a yield point of more than 900 MPa. The simulations included single (Tmax = 1250°C) and double welding thermal cycle (Tmax = 1250°C + 600°C, Tmax = 1250°C + 760°C and Tmax = 1250°C + 900°C) as well as cooling times t8/5 = 3, 5 and 10 s. Specimens with the simulated heat affected zone (HAZ) were subjected to impact strength tests performed at a temperature of -40°C and +20°C, Vickers hardness tests (HV10) and microscopic metallographic tests (involving light microscopy). Test results were presented in diagrams and photographs. Related comparisons included results of the structural, hardness and toughness tests of simulated HAZs with analogous results obtained during the actual repair welding of a MAG-welded joint made of steel S1100QL. The final part of the article contains discussion concerning the test results and the statement concerning the obtainment of the significant conformity of the phase comp...
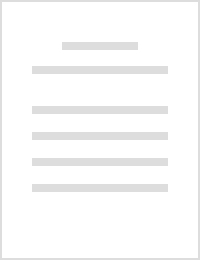
Rynek Energii, 2010
W artykule przedstawiono aktualne problemy dotyczące głównie energetyki konwencjonalnej a także e... more W artykule przedstawiono aktualne problemy dotyczące głównie energetyki konwencjonalnej a także energetyki jądrowej. Ponadto zasygnalizowano możliwości energetyki niekonwencjonalnej w formie alternatywnych źródeł energii takich jak biomasa lub elektrownie wiatrowe. W oparciu o dane literaturowe przedstawiono perspektywy zastosowania różnych grup stali konstrukcyjnych na elementy kotłów w elektrowniach konwencjonalnych takich jak: ściany szczelne, przegrzewacze, komory oraz rurociągi. Przedstawiono przykłady wyników badań wytrzymałości na pełzanie materiałów dla energetyki konwencjonalnej w oparciu o próby długotrwałe stali typu P91, P92, NF12, SAVE12, stali austenitycznych typu Super 304H a także stopów na bazie niklu np. Inconel 740, Haynes 230 itp. Zaprezentowano również przykłady wyników badań wybranych stopów niklu typu IN 792 i CM 247, które są typowane jako materiały konstrukcyjne pracujące w temperaturze do 1000 oC w instalacjach turbin w elektrowniach jądrowych.
Archives of Metallurgy and Materials, 2017
Welded installations failures of power plants, which are often result from a high degree of wear,... more Welded installations failures of power plants, which are often result from a high degree of wear, requires suitable repairs. In the case of cracks formed in the weld bead of waterwall, weld bead is removed and new welded joint is prepared. However, it is associated with consecutive thermal cycles, which affect properties of heat affected zone of welded joint. This study presents the influence of multiple manual metal arc welding associated with repair activities of long operated waterwall of boiler steel on properties of repair welded joints. The work contains the results of macro and microscopic metallographic examination as well as the results of hardness measurements.
Welding International, 2013
Differences in the nature of the thermal cycle run under welding conditions in comparison to that... more Differences in the nature of the thermal cycle run under welding conditions in comparison to that during conventional heat treatment are shown. The methods of investigations into microstructural changes of austenite under welding thermal cycles conditions developed and used at the Welding Institute in Gliwice are discussed. The investigation results, in the form of CTPC-S diagrams for construction steels of grades X12CrCoWVNbl 2-2-2 (VM12-SHC), 7CrMoVTiB10-10 (P24) and 10CrMo9-10 (P22), are presented and compared with those in the form of CTPC diagrams plotted for metallurgical conditions.
Biuletyn Instytutu Spawalnictwa, 2016
The article presents the results concerning the repair welding of a long-operated waterwall using... more The article presents the results concerning the repair welding of a long-operated waterwall using the mechanized TIG method. The tests were focused on determining the effect of a repair performed in order to remove cracks in welded joints located along flat bars opening on the tube wall side on the structure and hardness of the heat affected zone (HAZ) of a repair welded joint in the waterwall. In addition, the tests investigated the influence of multiple repair welding on the formation of structural notches in the HAZ.
Welding International, 2001
a liquid penetration inspection of the fillet-welded joints to detect the presence of cracks; ana... more a liquid penetration inspection of the fillet-welded joints to detect the presence of cracks; analyses of the chemical composition of the steels used in the welded joints, and of the plate fragments; macroscopic and microscopic metallographic examinations; hardness measurements on welded joints; analysis of the content of hydrogen diffusing into the weld metal deposited by the EB 1.46 grade electrodes; an assessment using the Tekken test of the tendency of the steel to cold cracking.
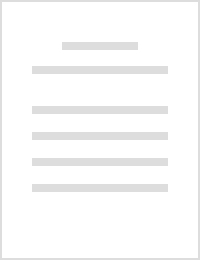
Welding International, 2002
Alloys with anticorrosive properties and especially stainless steels, are now widely used in a va... more Alloys with anticorrosive properties and especially stainless steels, are now widely used in a variety of installations in the chemical and petrochemical industries, in food processing, in cellulose and paper industry, in motor manufacture, atomic power engineering, as well as in the exploitation of natural gas and oil. By virtue of providing the required resistance to corrosion in different environments they contribute to the lengthening of the working life and the reduction in the cost of a range of constructional elements. Many production systems and installations call for the use of elements welded in stainless steels, including also those of the duplex variety. More recently, the Biuletyn Instytutu Spawalnictwa (The Institute of Welding Bulletin) published a series of papers by foreign authors on the subject of the welding of duplex steels. This reflects the interest in the Polish market of corrosion-resistant steel constructions shown by the manufacturers of filler materials. In view of the potentially increased use of duplex-stainless steels in Poland's industry, The Institute of Welding, fulfilling its statutory obligation, initiated an investigation financed by the Committee for Scientific Research into the conditions of welding and the properties of joints made in duplex steels. Fundamental characteristics of such steels, and the results of the investigation are discussed in this paper.
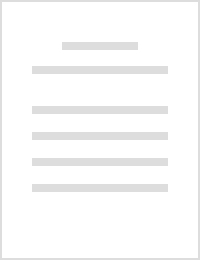
Welding International, 2000
In low-carbon steels, supplied in the as-rolled condition, the mechanical properties (Rc, Rm) are... more In low-carbon steels, supplied in the as-rolled condition, the mechanical properties (Rc, Rm) are functions mainly of carbon content and, therefore, any increase in this quantity results in a reduction in ductility and weldability. The addition to a steel of elements which substantially strengthen solid solutions (Mn, Si) produces an improvement in the mechanical properties, whereas the reduction in grain size the product of post-rolling normalisation improves the ductility and impact strength (e.g. 18G2A steel). However, the number of alloying elements that can be introduced into higher-strength steels is limited by the value of the carbon equivalent. In order that good weldability of such steels may be ensured, this quantity should not exceed a certain magnitude. A simultaneous increase in both the mechanical properties and the ductility can be achieved by the addition of microalloying elements (Nb, V, Ti) to the steels prior to their normalisation. The released dispersive carbides and carbonitrides of the microalloying elements reduce the grain size by either blocking the translation of grain boundaries of the austenite or delaying its recrystallisation. The increase in the mechanical properties is the result of precipitation hardening. In consequence, the carbon content can be reduced in microalloyed steels and thus their weldability improved, unlike the situation that obtains with higher-strength, C-Mn steel grades. Further increases in the yield points of constructional steels can be achieved by using a special method of rolling involving a thermomechanical treatment (Thermomechanical Control Process). This calls for systematic control of both the temperature and the degree of deformation during metal forming. Steels with yield points of about 700 MPa can be made by means of thermomechanical rolling. Higher mechanical properties can be imparted by subjecting the rolled steel to the hardening and tempering processes. The thermomechanical treatment requires the rolling process to be performed in such a way that individual stages of the steel deformation take place at specified temperatures. Two basic effects are utilised here: the influence that the fine-grained structure has on the improvement of mechanical properties and the increase in impact strength; the limitation of, or delay in, recrystallisation imposed by the introduced microalloying elements (Nb, Ti). The rolling process proceeds in two stages (Fig. 1). The first takes place at a temperature lower, by some 100-150 °C, than that of the conventional rolling tempAustenitisation (about 1200°C>
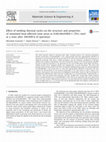
Materials Science and Engineering: A, 2015
The article presents results of structural tests (light, scanning electron and scanning transmiss... more The article presents results of structural tests (light, scanning electron and scanning transmission electron microscopy) of X10CrMoVNb9-1 (T91) creep-resisting steel after approximately 100,000 h of operation. It was ascertained that the parent metal of T91 steel is characterized by the microstructure of tempered martensite with M 23 C 6 carbide precipitates and few dispersive precipitates of MX-type niobium and vanadium carbonitrides. The most inconvenient change in T91 steel precipitate morphology due to long-term operation is the appearance of the Laves Fe 2 Mo phase which along with M 23 C 6 carbide particles forms elongated blocks and conglomerates on grain boundaries. The article also presents results of tests related to the effect of simulated welding thermal cycles on selected properties of X10CrMoVNb9-1 (T91) grade steel at a state after approximately 100,000 h of operation. The tests involved the determination of the chemical composition of the steel tested as well as impact tests, hardness measurements and microscopic metallographic examination (based on light microscopy) of simulated heat-affected zone (HAZ) areas for a cooling time (t 8/5) restricted within a range between 3 s and 120 s, with and without heat treatment. The tests revealed that, among other results, hardness values of simulated HAZ areas in X10CrMoVNb9-1 (T91) steel do not guarantee cold crack safety of the steel at the state without additional heat treatment. It was also observed that simulated welding thermal cycles of cooling times t 8/5 ¼3, 12, 60 and 120 s do not significantly affect the toughness and hardness of simulated HAZ areas of the steel tested.
Welding International, 2004
Schematic diagram of the friction welding process, incorporating stirring of weld material and in... more Schematic diagram of the friction welding process, incorporating stirring of weld material and indicating fundamental pressure-welding parameters.
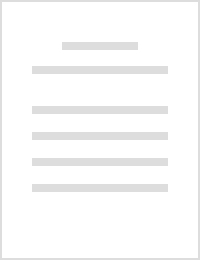
Materials Science Forum, 2010
In the present study, the characteristics of Nd:YAG laser welded joints of 600 MPa DP steel (HDT5... more In the present study, the characteristics of Nd:YAG laser welded joints of 600 MPa DP steel (HDT580X), 2.4 mm in thickness, in respect of hardness, microstructures and mechanical properties were investigated. The test joints have been welded under a shielding gas on the stand for robotic Nd:YAG laser welding at the beam power of 1.5 kW and 2.0 kW. Three combinations of welding parameters were used: 2.0 kW - 2.1 m/min, 2.0 kW - 1.5 m/min and 1.5 kW - 1.2 m/min. Detailed examinations were performed on the joint welded at the highest speed. The microstructure was examined by the optical-, scanning- and transmission electron microscope. The heat affected zone (HAZ) was composed of ferrite, bainite and lath martensite, the weld contained lath martensite. The maximum hardness in the HAZ did not exceed 343 HV. The tensile strength of the welded joint was at the same level as that of the base material. The results of fatigue tests and residual stress measurement of laser welded DP steel joi...
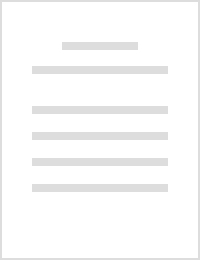
Welding International, 2002
Solid electrode-wires, intended for MAG welding, are made of common and low-alloy constructional ... more Solid electrode-wires, intended for MAG welding, are made of common and low-alloy constructional steels and are usually coated with a thin copper film whose role is to ensure good electrical contact in the contact tube (the current terminal), a low level of resistance to feed in the spiral of the MAG welding clamp, and a temporary anticorrosion protection. The copper film should be thin, uniform, and adhering well to the base. Users' experience indicates that the technology of copper plating does not always ensure that the requirement that the film should be resistant to flaking and peeling off the steel core surface is fulfilled. As a result of this, feed rolls of the semiautomatic welders can damage the wire surface and, in turn, contamination of the welding-clamp spiral with copper can occur. The wire quality is affected not only by the blank (i.e. by the method of melting, the composition of metallic charge of the making of steel, and the content of impurities) but also by the characteristic properties acquired by the wire during its manufacture (i.e. the degree of deformation during the drawing, etc.) including those associated with the deposition of the surface layer. Wires are usually manufactured by the dry drawing process using a variety of drawing lubricants (solid or semi-fluid), and are then subjected to heat treatment. Coating films display various degrees of surface finish. Consequently, the surface of the finished wire as well as the tears in it, may retain a quantity of lubricant left over from the processing which normally consists of salts of the carboxylic acid (soap). The lubricant introduces hydrogen and nitrogen into the zone of the welding arc and thus, undesirably, increases their content in the weld metal. Impurities in the surface film of the electrode wire may also cause the arcing to become destabilised. The manufacturing methods for solid wires, which are used by various producers, are essentially similar. Nevertheless, some differences between them exist in, for instance, the way in which the removal of impurities, scale, and other corrosive substances, and, also, the annealing are carried out (bright annealing is carried out either in vacuum or in inert gases), etc. For instance, the final drawing pass can be preceded by electroplating with copper in the interpass equipment (etching, rinsing, copper plating, rinsing, and boraxing). Properties of the electrolytic copper coatings depend, essentially, on the conditions under which they have been deposited, such as the type and the composition of the bath, the current density, and the process temperature. In addition to the copper plated, other metal-clad wires have now become available on the market, such as, for instance, nickel, chromium or bronze ones, and, also, wires with the so-called 'ecological' coatings (in appearance like coating-less steel wires). According to the manufacturers, this type of coating produces better electric current contact, ensures a greater stability of the welding process and reduces the emission of Cu dust. Literature also provides information about investigations into the wires with film coatings obtained by electrolytic polishing, oxidising, and aluminium impregnation. Within the framework of the No 7 T08C 035 16 Research Project of the Welding Institute, funded by the Science Research Committee, Warsaw, an investigation was initiated into the quality of solid wires for MAG welding produced by a variety of manufacturers. The present paper contains results of the investigations into the properties of film coatings on G3SÍ1-EN 440 solid wires. The assessment of the wire properties was based on the criteria established in the course of the experimentation. This was necessary because the available standards for the .welding wires do not uniquely specify requirements regarding factors such as, for instance, film thickness, its uniformity and surface roughness which influence the quality of the coating."
Metallic Materials, 2012
The paper presents differences in the character of the course of a thermal cycle in welding condi... more The paper presents differences in the character of the course of a thermal cycle in welding conditions compared with the cycle of a traditional heat treatment. The author elaborates the methodology of testing austenite phase transformations in steels affected by welding thermal cycles; the said methodology has been developed and put in practice at Instytut Spawalnictwa in Gliwice. The results of related tests are presented in the form of CCT diagrams for welding conditions for the following grades of structural steels applied in power engineering sector: X10CrMoVNb9-1
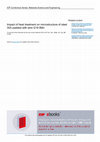
IOP Conference Series: Materials Science and Engineering, 2012
The practical purpose of padding is to increase mechanical properties, hardness and abrasion resi... more The practical purpose of padding is to increase mechanical properties, hardness and abrasion resistance of surface layers of structural elements while maintaining good plastic properties of the core, apply corrosion-resistant layers, regenerate and/or repair the surface etc. The article describes the results of macroscopic and microscopic metallographic examination of components made of 30X steel, which is an equivalent of 32HA steel produced in Poland, and surfaced with G18 8Mn filler wire using MAG method. One of components was not heat treated after surfacing while the other after surfacing was subjected to quenching and tempering. The examination was aimed at determining the effect of heat treatment on changes in the structure of surfaced components. The metallographic examination has been conducted using optical microscopy in the area of parent metal of 30X steel as well as in heat affected zone (HAZ) in steel under and in the surfacing weld. HAZ width under the surfacing weld has also been measured. On the basis of the results showed that heat treatment after padding is responsible for the presence of the structure of tempered martensite in the heat affected zone and is responsible for a greater width of the HAZ, if compared with the condition without heat treatment.
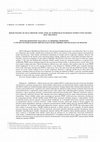
Archives of Metallurgy and Materials, 2011
REPAIR WELDING OF SQV2A PRESSURE VESSEL STEEL BY TEMPER BEAD TECHNIQUES WITHOUT POST WELDING HEAT... more REPAIR WELDING OF SQV2A PRESSURE VESSEL STEEL BY TEMPER BEAD TECHNIQUES WITHOUT POST WELDING HEAT TREATMENT SPAWANIE REMONTOWE STALI SQV2A NA ZBIORNIKI CIŚNIENIOWE Z UŻYCIEM TECHNIKI ŚCIEGÓW ODPUSZCZAJĄCYCH BEZ OBRÓBKI CIEPLNEJ ZŁĄCZA PO SPAWANIU SQV2A Manganese-Molybdenum-Nickel ferritic steel has been developed for pressure vessel fabrication. Due to its chemical composition and carefully controlled heat treatment the SQV2A steel consists of fine-grained tempered martensite/lower bainite microstructure, which exhibits well-balanced combination of strength and low temperature toughness. However, this balance is disturbed by the thermal cycles experienced during welding, producing areas of unaccepted mechanical behaviors. Generally, a decrease in toughness of some regions of BM Heat Affected Zone is the most critical aspect of multi-layer (repair) welding. A full scale Post Welding Heat Treatment (PWHT) usually restores the mechanical behaviors to requested levels. Additionally, PWHT removes hydrogen trapped in the microstructure during welding. A situation becomes critical, when on-site local (repair) welding takes place. Harsh environment, difficult access and a presence other facilities make the in-situ PWHT almost inapplicable. In term of cold cracking prevention, a Gas Tungsten arc Welding (GTAW) gives acceptable hydrogen levels in the weld region; and full scale PWHT is unnecessary. This is the main reason why the GTAW has become a leading process for on-site (repair) welding of heavy section components. Moreover, a automatic GTAW process offers better weld geometry controlling which has become out of importance for welding not followed by PWHT. A precisely controlled multiple weld thermal cycles of predefined peak temperatures in particular weld regions can be employed for restoring the mechanical behavior of critical weld areas instead of full scale PWHT.
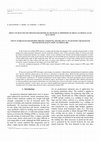
Archives of Metallurgy and Materials, 2011
Impact of Selected FSW Process Parameters on Mechanical Properties of 6082-T6 Aluminium Alloy But... more Impact of Selected FSW Process Parameters on Mechanical Properties of 6082-T6 Aluminium Alloy Butt Joints In the friction stir welding (FSW) process a rotating and travelling tool equipped with a specially designed probe is slowly plunged into joined materials, plasticizes and stirs them thus forming a joint. Various geometric shapes of stirring tools make the motion of plasticized material very complex, which, in turn, translates to the structure and mechanical properties of joints. The article presents the results of tests focused on the impact of selected FSW process parameters on the mechanical properties of butt welded joints made of 6082 aluminium alloy. The tests were performed at various linear welding speeds, using singleand double-sided test joints welded with three types of stirring tools, differing in probe and shoulder geometry. The article reveals the results of mechanical and fatigue tests of the FSW joints.
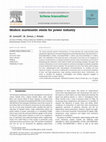
Archives of Civil and Mechanical Engineering, 2012
The article presents general characteristics of heat-resisting and creep-resisting steels intende... more The article presents general characteristics of heat-resisting and creep-resisting steels intended for operation at increased temperature and having martensitic microstructure i.e. X10CrWMoVNb9-2 (T/P92), X11CrMoWVNb9-1-1 (E911) and X12CrCoWVNb12-2-2 (VM12-SHC). The weldability of the aforesaid steels is discussed on the basis of CCT diagrams of austenite transformation in welding conditions and the results of simulation tests aimed at determining the resistance of the steels to brittle and annealing cracking. The paper also contains information on test results related to mechanical (strength and plastic) properties of joints welded with various methods. The description of each of the steels under analysis has been supplemented with technological recommendations on welding and heat treatment of joints. The article is addressed to researchers who are interested in problems of heat-and high-temperature creep resisting constructional steels. Furthermore, the article is intended for designers, technologists and welding engineers engaged in constructional jobs in power industry.
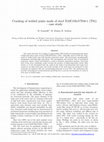
Metallic Materials, 2013
The article describes the cracking of argon-welded TIG-welded circumferential butt joints of ligh... more The article describes the cracking of argon-welded TIG-welded circumferential butt joints of light-wall tubes made of steel X10CrMoVNb9-1 (T91), using filler metal C9 MV-IG. Fragments of welded joints and weld deposits underwent macro-and microscopic metallographic examination involving light microscopy. The investigation also involved tests of mechanical properties, impact energy and hardness, as well as chemical composition analyses. Structural tests of the areas containing cracks revealed the presence of high-temperature ferrite delta (ferrite δ). It was determined that the cracks in the welds of circumferential butt joints were caused by too high yield point and tensile strength of the weld metal not subjected to heat treatment (if compared with the corresponding properties of steel T91). The publication also provides technological recommendations specifying how to prevent the formation of cracks in such types of welded joints.
Uploads
Papers by Mirosław Łomozik