Papers by Mehmet Bulent Durmusoglu

İTÜDERGİSİ/d, Sep 5, 2011
Today, product demands have become erratic due to increase in product variaty, and competitivenes... more Today, product demands have become erratic due to increase in product variaty, and competitiveness among companies, recently. Manuacturing systems must be redesigned in order to adapt to these chanceg, and respond quickly to erratic demand. Lead time of the manufacturing system should be decrased in order to achieve these goals. Therefore, onepiece flow was tried to be implemented during design, at this study. Moreover, as the companies produce wide range of products, these products should be in different stages of their life cycle. For instance, products that are at their beginning or birth phase, must be produced in functional layout. Sample parts or prototypes are examples to these part types. However, parts with relatively stable design and high demand must be produced in cells. This results in coexistance of both cells and functional layout at the same factory. These systems are called hybrid cellular manufacturing systems(HMS). These systems are met frequently in real world. However, solution approaches that focus on erratic demand conditions and providing oppurtunities to manufacture in varying cycle times are very limited. For these reasons, a road map for the design of HMS in erratic demand conditions using Axiomatic Design(AD) was proposed at this study. Exceptional operations causing intercell traffic should be eliminated, so as to implement one-piece flow. For this purpose, alternative machines will be utilized. As technology improved, machines have become able to carry out operations of other machines, and this caused them become alternative for each other. At our one-piece flow algorithm, alternative machines are evaluated, and exceptional operations are tried to be eliminated by reassigning them to these alternatives systematically. This algorithm is one of the unique components of our study, because it utilizes alternative machines both in cells and in functional layout in order to eliminate exceptional operations. After the elimination of exceptions, uni-directional flow must be established in each cell. This enhances one-piece flow in cells, and decrases lead time of the parts. Simulation technique is used so as to check sufficiency of system capacity, and bottlenecks are identified on the basis of simulation results. Bottleneck identification is also a tule-based approach using AD principles. While identification of the bottlenecks, workcenters causing delays and the resources causing these bottleneck work centers are searched and identified based on rules. Afterwards, bottlenecks must be eliminated. For this purpose, a systematic procedure was developed and pursued. In order to eliminate bottleneceks, some sequenial solutions were proposed using AD. Solutions must be implemented starting from the simplest to the hardest. The hardest and the last solution is purchasing resources, especially machines. This approach was implemented on a small hypothetical example, to reflect all possible situations. First, part-machines matrix of the problem was clustered using Averga Linkage
Endüstri Mühendisliği, 2000
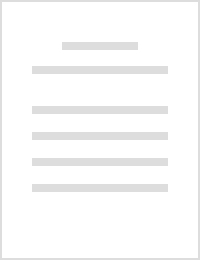
International Journal of Production Research, Aug 13, 2009
ABSTRACT One-piece flow is a design rule that entails production in manufacturing cells on a ‘mak... more ABSTRACT One-piece flow is a design rule that entails production in manufacturing cells on a ‘make one, check one, and move-on one’ basis (Black, J.T., 2007. Design rules for implementing Toyota Production System. International Journal of Production Research, 45 (16), 3639–3664), which reduces manufacturing lead time significantly. This paper proposes a sequential methodology comprised of a mathematical model and a heuristic approach (HA) for the design of a hybrid cellular manufacturing system (HMS), to facilitate one-piece flow practice. The mathematical model is employed in the cases of small- and medium-sized problems, and it attempts to minimise the total number of exceptional operations, while considering machine capacities and alternative machines. The machine-part matrix achieved by the mathematical model is input into the flow line design stage of the HA, where backflow within the cells is eliminated. However, for industrial problems, the proposed HA is utilised. After the formation of the cells by clustering, the HA attempts to eliminate exceptional operations of a given cellular configuration together with a functional structure by employing alternative machines, based on the decision rules developed. Later, unidirectional flow within the cells is achieved and the capacity and budget constraints are satisfied. A medium-sized problem is solved by using both of the approaches, namely, the model integrated with the flow-line design stage of the HA and the complete HA. The results are discussed and the limitations are explained.
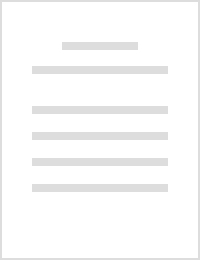
Omega, Aug 1, 2008
Office operations play a significant role in organizational performance; however, their contribut... more Office operations play a significant role in organizational performance; however, their contribution to competitive advantage has not adequately been addressed in the literature. In this study, we develop a methodology for designing an efficient office operation using axiomatic design principles. Axiomatic design allows the use of well-understood patterns of all necessary information when formalizing design objectives. We use these principles to design office cells, and claim that this methodology will improve office operations and contribute to business competitiveness through a reduction in customer lead time. We provide a detailed description of the methodology applied to office cell design, which consists of cell formation and operation, as well as the results of a real-world implementation. Our findings indicate that the methodology works well in improving office operations because it eliminates many non-value-added activities.
Journal of Materials Processing Technology, Dec 1, 2005
... 2, the area of the common range (A cr ) is equal to the probability of success p i [16]. ... ... more ... 2, the area of the common range (A cr ) is equal to the probability of success p i [16]. ... So, the common area is the intersection area of triangular or trapezoidal fuzzy numbers. The commonarea between design range and system range is shown in Fig. 5. ...
This paper provides a framework and a road map for people who are ready to transform their tradit... more This paper provides a framework and a road map for people who are ready to transform their traditional production system from process orientation to cellular orientation, based on Axiomatic Design (AD) principles. A feedback mechanism for continuous improvement is also suggested for evaluating and improving the cellular design against preselected performance criteria. A complete implementation of the proposed methodology at a local manufacturing company and resulting performance improvements are also provided.
In the last years, organizations must pay attention on customer demands for surviving and also fo... more In the last years, organizations must pay attention on customer demands for surviving and also for increasing their market shares. But customers have not stable demand and stable view. Demand is fluctuated through the time period and seasonal variation is mostly common. Organizations' main problem is how to cut costs while producing small numbers of many types of products with

Gazi Üniversitesi Mühendislik Mimarlık Fakültesi Dergisi
Lojistiğin diğer boyutlarının aksine üretim lojistiği veya iç lojistik ile ilgili literatürde yet... more Lojistiğin diğer boyutlarının aksine üretim lojistiği veya iç lojistik ile ilgili literatürde yeterli sayıda denebilecek çalışma mevcut değildir. Hâlbuki üretim faaliyetleri içerisinde lojistik, önemli bir yer işgal eder, üretimin süresine ve ürün kalitesine doğrudan etki eder. Böylesine önemli olan üretim lojistiği ile ilgili literatürdeki sınırlı sayıdaki çalışmaya bakıldığında çalışmaların depolama stratejilerinin belirlenmesi, depolama araçlarının seçimi, malzeme tasıma hareketlerinin yapılandırılması, malzeme tasıma araç türlerinin seçimi, hücresel yerleşim, hücre içi ve hücreler arası hareketlerin yapılandırılması ile ilgili olduğunu görüyoruz. Bulanık tabanlı bir seçim yaklaşımı olan bulanık ve ağırlıklandırılmış bulanık bilgi aksiyomunun endüstriyel hücrelerdeki taşıma faaliyetleri için kullanılması literatürde yeni sayılabilecek bir çalışma olacaktır. Aksiyomlarla tasarım metodolojisi içerisinde yer alan bilgi aksiyomu, en yalın iç lojistik taşıma yönteminin belirlenmesinde...

Expert Systems with Applications, 2011
Setup times have an important effect on providing quick response to the external besides internal... more Setup times have an important effect on providing quick response to the external besides internal customers. As well as eliminating setup activities, jobs with sequence-dependent setup times should be scheduled efficiently so as to reduce setup times. In this paper, a scheduling methodology which considers parts design characteristics is presented for parallel machines. With respect to the roadmap of the methodology, a parts design characteristics based scheduling algorithm is developed in order to reduce total setup times. When evaluating the performance of sequencing methods, the cable cutting-strippingcrimping (CSC) process of a real life wiring harness production system is focused. In the current scheduling system of CSC division, cable sequences are developed semi-manually by CSC supervisors. Making the proposed methodology compatible with cable sequencing, an expert system is developed so as to reduce the burden of supervisors and improve effectiveness. Performance comparison of scheduling algorithms is based on deviation from the lower bound for the total setup time as well as previously implemented semi-manual cable sequences. With respect to performance comparison, parts design characteristics based scheduling algorithm has resulted in 6.81% reduction of the total setup time compared to implemented semi-manual cable sequences (MCS) for 45-day production data.

İTÜDERGİSİ/d, 2011
Bir üretim sisteminde temel amaç, müşteri taleplerinin zaman ve kalite boyutunda etkin bir şekild... more Bir üretim sisteminde temel amaç, müşteri taleplerinin zaman ve kalite boyutunda etkin bir şekilde karşılanmasıdır. Bu amacı gerçekleştirmek için üretimin büyük partiler halinde ve stok tutarak gerçekleştirilmesi daha mantıklı görünür. Ancak bu yaklaşım, üretim sistemindeki problemleri görünmez hale getirmekle beraber, uzun bekleme sürelerini içermesi nedeniyle üretim temin süresini, dolayısıyla katma değerli olmayan faaliyetlerin oranını arttırmaktadır. Bu durum neticesinde, firmaların hızlı yanıt kabiliyeti ve maliyet performansı olumsuz etkilenir. Paralel makinalarda sıraya bağımlı hazırlık sürelerine sahip işlerin çizelgelenmesini fazla üretim israfına yol açmayacak şekilde sağlayan bu çalışmada, öncelikle, işler arası sıraya bağımlı hazırlık süreleri, ürün tasarım özelliklerinden faydalanan bir matematiksel model ile belirlenmektedir. Böylece, sıraya bağımlı hazırlık süreleri bire-bir ölçüme gerek kalmadan belirlenebilmeleri ve hem güncel hem de güvenilir olmaları sağlanmıştır. Ayrıca, temin sürelerinde önemli bir yer tutan hazırlık sürelerinin düşürülmesi için sıraya bağımlı hazırlık süreleri, odaklanılması önem taşıyan unsurlar arasındadır. Bu bağlamda, sıraya bağımlı hazırlık süreleri toplamını azaltmaya yönelik olarak literatürde yer alan iki sıralama algoritması seçilmiş ve tasarım özelliklerine bağlı bir sıralama algoritması tasarlanmıştır. Sıralama safhasından sonra geliştirilen İş Yükü Bazlı İş Gönderme Sistematiği ile üretim sistem karakteristiğinin çekme sistemine yakınlaştırılması amaçlanmıştır. Geliştirilen metodolojinin performansını değerlendirmek üzere, gerçek bir elektrik donanımı üretim sisteminin kablo kesim-sıyırmaterminalleme sürecine odaklanılmıştır. Belirtilen süreçteki hazırlık işleri analiz edilmiş, ürün tasarım özellikleri belirlenmiştir. Gerçek üretim verileri ile sıralama yöntemlerinin karşılaştırılmasından sonra İş Yükü Bazlı İş Gönderme Sistematiği uygulanmıştır.

DergiPark (Istanbul University), Dec 15, 2021
Yalın düşünme, iç ve dış müşteri gözünde katma değeri olmayan faaliyetleri ortadan kaldırarak az ... more Yalın düşünme, iç ve dış müşteri gözünde katma değeri olmayan faaliyetleri ortadan kaldırarak az ile çoğu yapmaya odaklı bir felsefedir. Ulaşacağı standartlar ile Endüstri 4 çalışmalarının da olmazsa olmaz önemli ilk aşamasıdır. Artan rekabet ve bilinçli müşteri, sadece üretimde değil, artık ofis işlemlerinde de yalın çabaları gerekli kılmaya başlamıştır. Yalın ofis üzerine bu çalışmada, özgün olarak Muhasebe Bölümü yalın bakış açısıyla değerlendirilmiş ve sistematik bir şekilde süreçlerindeki israflar ortaya çıkarılmıştır. Bu israflar, süreç sadeleşme, süreçlerdeki iş yapış biçimlerini değiştirme ve dijital çözümler yardımıyla yok edilmeye başlanmıştır. Hizmet fatura giriş süreleri %44, sürenin değişkenliği %47 oranında düşmüş, ayrıca fatura onaylama sürelerinde de sadeleşme yoluyla %18'lik bir hızlanma sağlanmıştır. Söz konusu performans artışları, Muhasebe Bölümünü yalın kültür dönüşümünde iddialı hale sokmaya başlamıştır.

Computers & Industrial Engineering, 2016
The use of facilities provided by industrialization and technological developments has led to inc... more The use of facilities provided by industrialization and technological developments has led to increase in occupational diseases and accidents in workplaces. A sheer success in Occupational Health and Safety (OHS) is possible when safety activities for employees, production and business are considered synchronously. OHS systems, where scientific research oriented technological advances applied, are required to be designed with the aim of preventing OHS related problems and their effects in sustainable manner. In this study, a systematic approach is proposed for design of Lean-oriented OHS systems by using Axiomatic Design principles. A holistic roadmap is obtained as the output of the study for the application of OHS system to a production system. The proposed OHS system design is applied to a real life shipyard system from shipbuilding industry and its feasibility is demonstrated.
Assembly Line - Theory and Practice, 2011

Effective use of labor, providing system flexibility, increasing productivity, decreasing lead ti... more Effective use of labor, providing system flexibility, increasing productivity, decreasing lead times and costs are some of the most important factors influencing selection of material handling equipment. In this study, a decision support system (MHAD) considering these factors for material handling equipment selection is developed. MHAD consists of a database, a rulebased system and multi-attribute decision making modules. Database includes the detailed data about equipment types and their properties. The rule-based system module provides rules which are utilized by inference engine for determining the most proper material handling equipment type. Ultimately, a final decision is made for the most proper equipment among the alternatives of the same type using the information axiom of axiomatic design principles. Evaluation of alternatives is made for the cases of both complete and incomplete information. This paper introduces the fuzzy Information axiom approach and uses it in the selection of material handling equipment in a real world problem.

Computers & Industrial Engineering, 2014
This paper presents a new job release (JR) and scheduling methodology for one-stage parallel mach... more This paper presents a new job release (JR) and scheduling methodology for one-stage parallel machines where sequence dependent setup times exist. A decision support system (DSS) based on job release is developed in order to enable the application of the methodology. First, mathematical programming models for both job release and job scheduling are devised. Then, due to the NP-hard nature of the problems, heuristics are proposed. As for the interaction between JR and scheduling, job scheduling is integrated with job release for the proposed heuristic solutions so that the capacity achievement provided by scheduling can be utilized for job release. In brief, product design characteristics oriented scheduling affects JR in the proposed approach. Moreover, value stream mapping (VSM) approach is used with the aim of stating the effect of the proposed methodology. Furthermore, the presented methodology was applied in a real life electric wire-harness production system. The application, based on 120-day production data, revealed that the proposed methodology provided 25% decrease in in-plant manufacturing lead time.
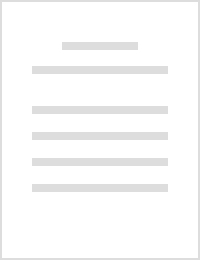
The 40th International Conference on Computers & Indutrial Engineering, 2010
ABSTRACT In the last years, organizations must pay attention on customer demands for surviving an... more ABSTRACT In the last years, organizations must pay attention on customer demands for surviving and also for increasing their market shares. But customers have not stable demand and stable view. Demand is fluctuated through the time period and seasonal variation is mostly common. Organizations' main problem is how to cut costs while producing small numbers of many types of products with seasonal variation. The solution of this problem is built up with lean based production systems. There are many tools of lean production systems as value stream mapping, cellular manufacturing, 5S, SMED, pull production systems and production smoothing. In this study, production smoothing decisions are studied through value stream mappings. Smoothing scenarios for seasonal variation are developed in order to reduce the deterioration of the production systems performance. The scenarios were tested in a real life “white goods” production system. Firstly the work flow was visualized using value stream mapping, then production schedule was created using production smoothing method and lastly developed smoothing scenarios were tested. One of the scenarios with the chosen pull production control system alternative was given the better performance.

Concepts, Methodologies, Tools, and Applications
This chapter focuses on providing a methodology for lean thinking based investment planning from ... more This chapter focuses on providing a methodology for lean thinking based investment planning from the perspective of cellular or hybrid manufacturing systems. The chapter has been divided into three parts. First part provides a general explanation of why lean thinking is so beneficial for managing manufacturing processes and obtaining sustained improvement. This part then moves to the aim of cell formation, and then uses value stream mapping to map current state for visualizing material-information flow and to design a desired future state for examining economic aspects of new machine investment decisions aligned with lean manufacturing principles. The purpose of second part is to explore axiomatic design approach; it provides an overall view of what to do. The third part presents the actual use of the methodology with implementation of hybrid system at a furniture factory; it helps to see application results of this methodology as part of a lean manufacturing program.
Uploads
Papers by Mehmet Bulent Durmusoglu