Papers by Ir. Ari Wahjudi, MT
Jurnal Rekayasa Mesin, Dec 14, 2023
Polymer matrix composite (PMC) is widely applied in structural engineering mainly due to its high... more Polymer matrix composite (PMC) is widely applied in structural engineering mainly due to its high strength-to-weight ratio. Of many benefits, the transportation industry uses this type of material mainly due to its high strength-to-weight ratio. In many cases, this strength-to-weight ratio is higher than aluminum or steel base materials. Its manufacturing and fabrication, however, are challenging. For this reason, destructive and non-destructive tests to control product quality during the manufacturing process are worked out. The non-destructive test delivers many benefits since the finished product does not. This paper discusses the benefits of polymer matrix composite application in the structural engineering. In addition, this work also outlined the key parameters and comparison of various non-destructive tests applied for the PMC.
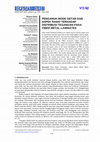
Jurnal Rekayasa Mesin
Fiber metal laminates (FMLs) are widely used in various fields such as automotive and aerospace d... more Fiber metal laminates (FMLs) are widely used in various fields such as automotive and aerospace due to their high stiffness and strength-to-weight ratios. Moreover, they also have high fatigue resistance. In some applications such as aircraft structures, it is crucial to do dynamic analysis of the FMLs structure. FMLs compose of aluminium and fiberglass reinforced polymers (FRPs) are used in this study. The aim of this study is to investigate the effect of shape mode and aspect ratio on the stress distribution of FML by using finite element analysis software. Ten initial mode shapes and the aspect ratio of 1:1.5, 1:2, and 1:2.5 are used as the environmental conditions of the FMLs. The results indicate that the mode shape will change the stress distribution and the maximum stress position. Besides, the results have shown that a wider FMLs plate will increase the maximum stress and deformation. The maximum to minimum stress distribution occurs on the outer aluminium surface, the inner...
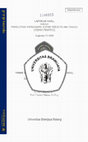
Komposit dengan bahan dasar alami atau dikenal dengan nama bio-komposit akhir-akhir ini mulai ban... more Komposit dengan bahan dasar alami atau dikenal dengan nama bio-komposit akhir-akhir ini mulai banyak dikembangkan selain disebabkan tinjauan ekologis yakni material bio-komposit lebih ramah lingkungan juga disebabkan harganya yang murah dan untuk beberapa bahan alami memiliki kekuatan yang tidak kalah dibandingkan dengan bahan sintetis. Pada penelitian ini komposit menggunakan bahan pengisi serat kenaf dan serbuk kayu dengan matrik poliester 157 BQTN-EX. Kenaf diharapkan yang berupa serat diharapkan memberikan unjuk kerja yang baik beban tarik dan kayu dalam bentuk serbuk diharapkan memberikan unjuk kerja yang baik ketika menerima beban tekan. Komposisi serat kenaf dan serbuk kayu divariasikan dan dicampur bersama matrik polyester dan zat pengaktif kemudian dituang kedalam cetakan dengan cara diinjeksikan. Hasil cetakan berupa spesimen tarik, spesimen impak dan spesimen tekan kemudian diuji untuk mengetahu unjuk kerja dari komposit. Hasil uji sifat mekanik komposit menunjukkan bahwa...
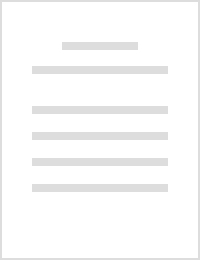
IOP Conference Series: Materials Science and Engineering, 2021
Fiber metal laminates (FMLs) are widely used in various fields such as automotive and aerospace d... more Fiber metal laminates (FMLs) are widely used in various fields such as automotive and aerospace due to their high stiffness and strength to weight ratios. Moreover, they are also high fatigue resistance. In some applications such as aircraft structures, it is crucial to do a dynamic analysis in the FMLs structure. This research aims to investigate the effect of shape mode and crack length on stress distribution in fiber metal laminates. Numerical analysis is performed in this study to evaluate the stress distribution. Ten initial mode shape and crack length of 5 mm, 10 mm, and 15 mm are used as the environmental conditions of the FMLs. The results indicate that the mode shape will change the stress distribution and the maximum stress position. Besides, the crack will propagate when it received tensile stress and in opening mode.
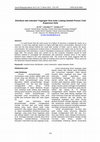
It is well known that the main cause of a failure of structure is initiated by cracks on a member... more It is well known that the main cause of a failure of structure is initiated by cracks on a member. A crack may originate easily in a region with high stress concentration. Because in the rivet and the bolt joining method are usual with number of holes, and to reduce the stress concentration, the compressive residual stress is introduced in the region near by the hole. The cold expansion hole technique is used to developed compressive residual on the vicinity of the edge hole. The present study was carried out by the computer simulation based on finite element method to investigate the distribution and interaction residual stress in the region between holes related to the cold expansion hole. The result of the study suggests that the distance between holes influence the state of residual stress and its magnitude. These cause by the deformed material between holes interact each other. Keywords: residual stress distribution, stress interaction, region between holes
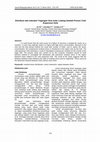
Rekayasa Mesin, Jul 2, 2013
It is well known that the main cause of a failure of structure is initiated by cracks on a member... more It is well known that the main cause of a failure of structure is initiated by cracks on a member. A crack may originate easily in a region with high stress concentration. Because in the rivet and the bolt joining method are usual with number of holes, and to reduce the stress concentration, the compressive residual stress is introduced in the region near by the hole. The cold expansion hole technique is used to developed compressive residual on the vicinity of the edge hole. The present study was carried out by the computer simulation based on finite element method to investigate the distribution and interaction residual stress in the region between holes related to the cold expansion hole. The result of the study suggests that the distance between holes influence the state of residual stress and its magnitude. These cause by the deformed material between holes interact each other.
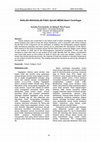
Rekayasa Mesin, May 23, 2012
Failure analysis was conducted on the failure shaft of batch centrifugal. In the analysis the str... more Failure analysis was conducted on the failure shaft of batch centrifugal. In the analysis the stress analysis was used to know the stress distribution, and in conjuction with stress analysis the life time of the component can be estimated. In addition, the fractography anlaysis together with mechanical properties test were carried out to understand the mechanism of the failure. With respect to the result of analysis shows that the failure was caused by fatigue crack initated on the surface of shaft due to the inhomogeneus mechanical properties, in this case, the hardness is lower than that on sub surface of the shaft. Besides that, the stress concentration was found take place on the surface of shaft on which the crack was initated. Further, it was known that during machining process, the material of shaft was heated on elevated temperature on the surface to ease the process. The heating reduced the hardness as well as the strength of the material.
International Journal of Technology, 2018
The crack growth behavior of fiber metal laminates (FMLs) with fiber orientations of 90°/0° and 4... more The crack growth behavior of fiber metal laminates (FMLs) with fiber orientations of 90°/0° and 45°/45° to load direction was investigated with varying stress ratios of the cyclic constant load. The study shows that crack growth behavior depends on the conditions of the cyclic load and the orientation of the fiberglass orientation. A higher stress ratio of the cyclic constant load causes fatigue life to decrease, and is associated with stress concentration just in front of the crack tip. The stress concentration in the FMLs with 45 o /45 o fiberglass orientation is higher than that of 90 o /0 o , which means the fatigue life in the former is shorter. The bridging of the fiberepoxy composite takes place when the stress ratio of the constant cyclic load is lower than 0.4, which also enhances fatigue life.
Uploads
Papers by Ir. Ari Wahjudi, MT