Papers by Diego Cabrera Z.
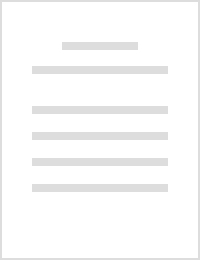
Journal of Computing and Information Science in Engineering
Most of the approaches of feature extraction for data-driven rotating machinery fault diagnosis a... more Most of the approaches of feature extraction for data-driven rotating machinery fault diagnosis assume characteristics of periodicity and seasonality typically inherent to linear signals obtained from different sensors. Nevertheless, the behavior of rotating machinery is not necessarily linear when a failure occurs. Thus, new techniques based on the theory of chaos and nonlinear systems are needed to extract proper features of signals. This article introduces the use of features extracted from the Poincaré plot (PP), which are computed over vibration and current signals measured on a gearbox powered by an induction motor. A comparison between the performance of classic statistical features and PP features is developed by applying feature analysis based on analysis of varaince (ANOVA) and cluster validity assessment to rank and select the subset of best features. K-nearest-neighbor (KNN) algorithm is used to test the performance of the selected feature set for fault severity classifi...
Expert Systems with Applications
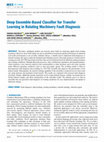
IEEE Access, 2022
Nowadays, intelligent models can correctly detect faults by analysing signals from rotating machi... more Nowadays, intelligent models can correctly detect faults by analysing signals from rotating machinery. However, most of the studies are run in controlled environments and the performance in industrial real-world environments is not yet fully validated. Hence, a suitable tool to implement fault diagnosers is transfer learning, this topic is under development and challenges persist. This paper proposes a framework for creating accurate 1D-CNN based fault classifiers that can be transferred between different rotating machines and working conditions. Multiple Bayesian processes select architecture parameters and hyperparameters, which minimize a loss function related to their transferability to other machines and to the same machine under different operating conditions (such as load and engine speed). The resulting model is fitted to heterogeneous fault diagnosis data resulting in a 1D-CNN ensemble that improves the performance of the unitary model. Subsequently, the transfer learning capability of the ensemble is analyzed on two source data sets using function and parameter based transfer. The results are compared with classical fault diagnosis classifiers. Finally, additional transfer operations on five target domain datasets validate our framework on limited labeled samples and allow interpretation of the ensemble results. The ultimate goal is to find an ensemble that can generalize fault diagnosis on rotating machinery for easy implementation and update in industrial settings.
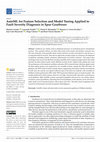
Mathematical and Computational Applications, 2022
Gearboxes are widely used in industrial processes as mechanical power transmission systems. Then,... more Gearboxes are widely used in industrial processes as mechanical power transmission systems. Then, gearbox failures can affect other parts of the system and produce economic loss. The early detection of the possible failure modes and their severity assessment in such devices is an important field of research. Data-driven approaches usually require an exhaustive development of pipelines including models’ parameter optimization and feature selection. This paper takes advantage of the recent Auto Machine Learning (AutoML) tools to propose proper feature and model selection for three failure modes under different severity levels: broken tooth, pitting and crack. The performance of 64 statistical condition indicators (SCI) extracted from vibration signals under the three failure modes were analyzed by two AutoML systems, namely the H2O Driverless AI platform and TPOT, both of which include feature engineering and feature selection mechanisms. In both cases, the systems converged to differ...
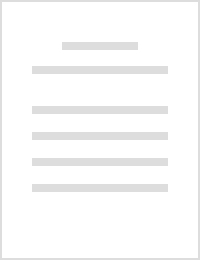
2019 Prognostics and System Health Management Conference (PHM-Paris), 2019
In this paper, a methodology for accelerometer placement comparison for crack detection in railwa... more In this paper, a methodology for accelerometer placement comparison for crack detection in railway axles, using vibration signals and machine learning, was shown. Different vibration signals from six accelerometers were obtained by several conditions of load and speed, with crack depths in axles from 5.7 to 15 mm. This paper describes three stages: acquisition, processing, and analysis. The findings suggest that using the vertical or longitudinal accelerometer located in left allow obtaining higher accuracy than 90% with three features, also called condition indicators. On the other hand, an accuracy such as 96.43% is obtained using a left vertical sensor and 95,98% using a left longitudinal sensor, both with ten features. With this methodology, high accuracy in crack detection was obtained using an accelerometer effective placement. Different vibration signals using six accelerometers were obtained, under several conditions of load and speed, with crack depths in axles from 5.7 to 15 mm.
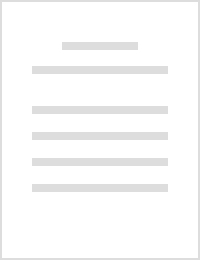
2018 International Conference on Sensing,Diagnostics, Prognostics, and Control (SDPC), 2018
Gearboxes are essential devices for some applications, e.g., industrial rotating mechanical machi... more Gearboxes are essential devices for some applications, e.g., industrial rotating mechanical machines. Besides, the gearboxes malfunctioning can cause economic losses, risks to the human safety and can impair the performance of the systems in which they are included. Thus, it is necessary to find feasible and efficient methods to evaluate their physical condition. This work proposes an approach that uses the Fourier Transform spectrograms and Convolutional Neural Networks (CNN) to classify the gearbox fault severity condition by analyzing the vibration signals provided by an accelerometer. We used a dataset with ten damage levels of one failure mode of a helical gearbox operating under different load and speed values to assess the performance of the proposed solution. Three different CNN configurations were compared concerning accuracy, training time and other parameters. The proposed system achieves average values of accuracy up to 0.9743 regarding AUC, while it presents classification times close to 0.03 seconds, showing itself to be a competitive solution.
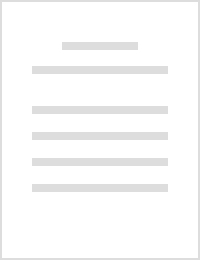
2017 IEEE Symposium on Service-Oriented System Engineering (SOSE), 2017
Fault detection and diagnostic software (FDDS) supports technicians and engineers to deal with op... more Fault detection and diagnostic software (FDDS) supports technicians and engineers to deal with operational matters, in major cases related to complicated systems and advanced technology that require higher performance expectation. Information and communication technologies play an importantrole for implementing efficient maintenance software, therefore, the development of FDDS is posed as an industrial necessity. In case of industrial rotating machinery, data-driven FDDS using available vibration signals, or other related signals monitored from sensors, is currently viewed as an industrial informatics requirement. This paper proposes the application of a Service Oriented Architecture (SOA) to implement an integrated tool for automatically developing and testing machine learning based fault diagnosis models in rotating machinery. As a result, a generic architecture is obtained which is able to build and implement diagnosis models in similar devices or processes. A condition monitoring software application, using the proposed SOA, was implemented in Java and deployed on a computational environment to test its performance in a experimental test bed, under realistic fault mechanical conditions in a gearbox.
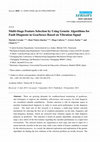
There are growing demands for condition-based monitoring of gearboxes, and techniques to improve ... more There are growing demands for condition-based monitoring of gearboxes, and techniques to improve the reliability, effectiveness and accuracy for fault diagnosis are considered valuable contributions. Feature selection is still an important aspect in machine learning-based diagnosis in order to reach good performance in the diagnosis system. The main aim of this research is to propose a multi-stage feature selection mechanism for selecting the best set of condition parameters on the time, frequency and time-frequency domains, which are extracted from vibration signals for fault diagnosis purposes in gearboxes. The selection is based on genetic algorithms, proposing in each stage a new subset of the best features regarding the classifier performance in a supervised environment. The selected features are augmented at each stage and used as input for a neural network classifier in the next step, while a new subset of feature candidates is treated by the selection process. As a result, the inherent exploration and exploitation of the genetic algorithms for finding the best solutions of the selection problem are locally focused. The
2018 International Conference on Sensing,Diagnostics, Prognostics, and Control (SDPC), 2018
Diagnosing failures during their initial stage is important to avoid unexpected stops and catastr... more Diagnosing failures during their initial stage is important to avoid unexpected stops and catastrophic damages, specially for gear boxes that are crucial components in industrial machines. This work addresses the classification of nine levels of crack failure severity in a gearbox. First of all, features are extracted in time domain from signals coming from an acoustic emission (AE) sensor, and then selected by using four different ranking methods. The classification stage uses the k-Nearest Neighbors (KNN) technique. The results indicate that presented levels of severity can be successfully classified with five features extracted from the AE signal for the four ranking methods.
2019 Prognostics and System Health Management Conference (PHM-Paris), 2019
A method for gearbox pitting faults severity classification using Deep Learning techniques is rep... more A method for gearbox pitting faults severity classification using Deep Learning techniques is reported. The signals are preprocessed for obtaining a 2D time-frequency representation corresponding to the Mel Frequency Cepstral Coefficients. This bi-dimensional representation is the feature space used for classification. A Long Short Term Memory network (LSTM) is used for classifying nine levels of pitting in spur gears. Each signals dataset is used for training and validating a LSTM network. Classification accuracies up to 100 % are obtained during cross-validation with the analyzed signals dataset.
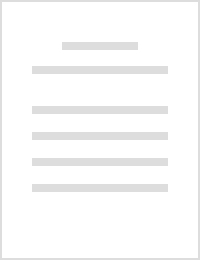
2020 IEEE ANDESCON, 2020
The Prognostics and Health Management (PHM) approach aims to reduce potential failures or machine... more The Prognostics and Health Management (PHM) approach aims to reduce potential failures or machine downtime by determining the system state through the identification of the signals changes produced by the system’s faults. Machine learning (ML) approaches for fault diagnosis usually have high-dimensional feature space that can be obtained from signal processing. Nevertheless, as more features are included in the ML algorithms the processing time increases, there is a tendency for overfitting, and the performance may even decrease. Feature selection has multiple goals including building more simple and comprehensible models, improving the performance on ML algorithms, and preparing clean and understandable data. This paper proposes a methodological framework based on a cluster validity index (CVI) and Sequential Forward Search (SFS) to select the best subset of features applied on the problem of fault severity classification in rolling bearing. The results show that a perfect classification can be obtained with KNN with at least six selected features.
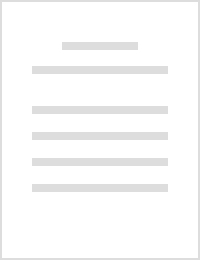
2019 Prognostics and System Health Management Conference (PHM-Qingdao), 2019
With the 3D printing rapidly expanding into various fields, 3D printers, as the equipment, should... more With the 3D printing rapidly expanding into various fields, 3D printers, as the equipment, should adopt a low-cost and small-sample fault diagnosis methods. A fault diagnosis method based on echo state networks (ESN) for 3D printers is proposed in this paper. A low-cost attitude sensor installed on the 3D printer is employed to collect raw fault data. Subsequently, feature extraction is carried out on the raw fault data. Using these features, ESN, as a shallow learning network, is modeled to diagnose faults of 3D printers. Experimental results show that the fault diagnosis method based on ESN still effective for 3D printers in low-cost and small-sample, which can make the fault recognition accuracy of 3D printer reach to 97.26%. Furthermore, contrast results indicated that the fault diagnosis accuracy of ESN is higher and most stable when compare with support vector machine (SVM), locality preserving projection support vector machine (LPPSVM) and principal component analysis support vector machine (PCASVM).
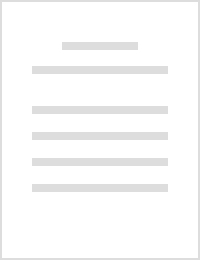
2019 Prognostics and System Health Management Conference (PHM-Paris), 2019
Gears are key elements in mechanical transmission systems. Fault diagnosis in gearboxes is a cutt... more Gears are key elements in mechanical transmission systems. Fault diagnosis in gearboxes is a cutting-edge topic nowadays mainly addressed by machine learning approaches. The success classifying a fault under this approach depends directly on the quality of the information provided to the models, and in gearboxes, quality of captured information depends on the place where a sensor is located. In this work, we propose a deep learning approach for the evaluation of the best of two accelerometers positions for classifying nine severity levels in gearboxes. Based on the performance of LSTM models whose hyperparameters have been found by a Bayesian optimization, we show which one is the best source of information for this layout. Also, we have performed statistical comparisons in order to find any statistical differences between models and accelerometers.
2020 IEEE ANDESCON, 2020
The information technologies are used as tools for predictive maintenance. They allow to anticipa... more The information technologies are used as tools for predictive maintenance. They allow to anticipate any severe damage on industrial machines. This paper proposes a system for fault detection in rotating machines through the acquisition and processing of acoustic signals under the framework of service oriented architecture (SOA). The system takes advantage of resources such as mobile devices for the acquisition of acoustic signals, a computer server for data storage and processing, and web services as a service orchestrator between the mobile device and the processing stage. After the system implementation its functionality is evaluated in the fault detection of gearboxes, resulting in a high detection rate.
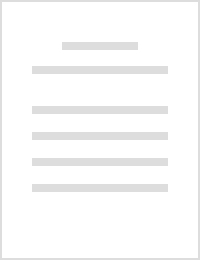
IEEE Transactions on Instrumentation and Measurement, 2021
System health monitoring as the basis of prognostics and health management (PHM) aims to explore ... more System health monitoring as the basis of prognostics and health management (PHM) aims to explore health indices/features for PHM to do condition monitoring, perform abnormal detection, and provide degradation trends for prognostic models. Kurtosis and negative entropy are two classic and popular indices to measure the sparsity of impulsive transients, and they are prone to be affected by impulsive noise. The purpose of this article is twofold. Theoretically, new propositions and their proofs are proposed to illustrate how kurtosis and negative entropy can help to characterize impulsive transients and why they are affected by impulsive noise. Next, a weighted residual regression-based index is proposed to relieve the sensitivity of kurtosis and entropy to impulsive noise and to provide monotonic trends for gear and bearing degradation assessment. Theoretical results show that kurtosis and negative entropy are changed with the length of nonimpulsive regions of impulsive transients. Experimental results demonstrate that the proposed method has better incipient fault detection ability and monotonic trending ability than kurtosis and negative entropy for bearing and gear health monitoring and degradation assessment.
The purpose of this document is to identify the best position of an acoustic emission sensor in a... more The purpose of this document is to identify the best position of an acoustic emission sensor in a gearbox for fault detection. The acoustic emission sensor was located in the four side walls of the gearbox, where three signals were acquired in each position to be analyzed in the time domain by condition indicators and finally the best signals were analyzed in the frequency do-main by means of the gear step frequency. As a result, it was obtained that the sensor must be positioned in the shorter length lateral parts of the gearbox
2021 IEEE Fifth Ecuador Technical Chapters Meeting (ETCM), 2021
In this paper, the constant load torque of a three-phase induction motor is estimated by means of... more In this paper, the constant load torque of a three-phase induction motor is estimated by means of the steady-state electrical torque signal and the motor torque due to the friction loss. In this case study, the load is connected to the motor's output shaft through an electromagnetic brake generating constant load at three magnitudes. Validation of load torque estimation is performed by identifying electrical and mechanical parameters and simulating its mathematical model to compare estimated and simulated constant load signals. Then this methodology can be used to estimate constant load torques on induction motors.
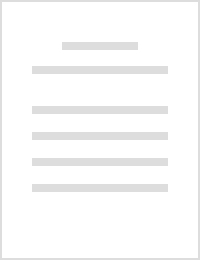
2021 IEEE Fifth Ecuador Technical Chapters Meeting (ETCM), 2021
Condition-based maintenance aims to determine the machine state in real time, by monitoring the s... more Condition-based maintenance aims to determine the machine state in real time, by monitoring the signals it emits. Such signals are potentially unlimited, generated at a high rate, and can evolve over time. These conditions tend to produce changes in the distribution of the data, known as concept drift. This phenomenon is analyzed and used to establish changes in the state of the machine. The present article proposes a methodological framework for the diagnosis of fault severity based on concept drift. A parsimonious unsupervised algorithm based on KNN is proposed to detect concept evolution. The results show that the algorithm is quite effective in declaring a concept evolution that is associated with a change in the failure condition of the machine. Finally, the results show that there is a high correlation between the displacement of the centroids of the emerging concepts and the % of deterioration of the machine.
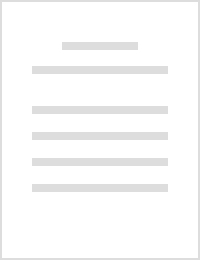
2017 International Conference on Sensing, Diagnostics, Prognostics, and Control (SDPC), 2017
Bearings are one of the most omnipresent and vulnerable components in rotary machinery such as mo... more Bearings are one of the most omnipresent and vulnerable components in rotary machinery such as motors, generators, gearboxes, or wind turbines. The consequences of a bearing fault range from production losses to critical safety issues. To mitigate these consequences condition based maintenance is gaining momentum. This is based on a variety of fault diagnosis techniques where fuzzy clustering plays an important role as it can be used in fault detection, classification, and prognosis. A variety of clustering algorithms have been proposed and applied in this context. However, when the extensive literature on this topic is investigated, it is not clear which clustering algorithm is the most suitable, if any. In an attempt to bridge this gap, this paper reports some preliminary results of a work aiming at comparing four representative fuzzy clustering algorithms: fuzzy c-means (FCM), the Gustafson-Kessel (GK) algorithm, fuzzy c-means with a focal point (FCMFP), and fuzzy neighborhood density-based spatial clustering of applications with noise (FN-DBSCAN). The paper reports only results from the real-world bearing vibration benchmark CWRU data set. The comparison takes into account the quality of the generated partitions measured by the external quality, i.e., Rand index. The conclusions of the study are grounded in statistical tests of hypotheses.
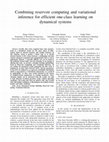
2017 International Conference on Sensing, Diagnostics, Prognostics, and Control (SDPC), 2017
Usually, time series acquired from some measurement in a dynamical system are the main source of ... more Usually, time series acquired from some measurement in a dynamical system are the main source of information about its internal structure and complex behavior. In this situation, trying to predict a future state or to classify internal features in the system becomes a challenging task that requires adequate conceptual and computational tools as well as appropriate datasets. A specially difficult case can be found in the problems framed under one-class learning. In an attempt to sidestep this issue, we present a machine learning methodology based in Reservoir Computing and Variational Inference. In our setting, the dynamical system generating the time series is modeled by an Echo State Network (ESN), and the parameters of the ESN are defined by an expressive probability distribution which is represented as a Variational Autoencoder. As a proof of its applicability, we show some results obtained in the context of condition-based maintenance in rotating machinery, where vibration signals can be measured from the system, our goal is fault detection in helical gearboxes under realistic operating conditions. The results show that our model is able, after trained only with healthy conditions, to discriminate successfully between healthy and faulty conditions.
Uploads
Papers by Diego Cabrera Z.