Papers by Cristhian Jaimes
REVISTA AMBIENTAL AGUA, AIRE Y SUELO, Feb 4, 2016
En este artículo se propone el uso de sistemas robotizados remotos para la plantación y mantenimi... more En este artículo se propone el uso de sistemas robotizados remotos para la plantación y mantenimiento de cultivos urbanos implementados en techos, azoteas, fachadas y paredes de edificaciones. El sistema robótico busca evitar el riesgo que puede conllevar el mantenimiento por parte de los operarios de estos cultivos al encontrarse a alturas considerables. De igual forma busca mejorar las condiciones de mantenimiento de los cultivos basándose en un control mixto que integra las tareas planeadas por el usuario y la información de humedad, luminosidad y temperatura captura por los sensores. El sistema robotizado cumple funciones de siembra, riego, fumigación, desyerbado y recolección de frutos. También se presenta un resumen del impacto ambiental que se genera al implementar este tipo de sistemas.
2018 5th International Conference on Control, Decision and Information Technologies (CoDIT), 2018
This article deals with the conceptual design and dimensional synthesis of the parallel linear De... more This article deals with the conceptual design and dimensional synthesis of the parallel linear Delta robot for additive manufacturing. In the conceptual development, the QFD matrix is used to in order to translate user requirements into design parameters. A set of technical specifications is defined, analyzed and evaluated to generate and select engineering solutions concepts. These concepts enable to describe the form, functions and features of the linear delta robot. Secondly, a dimensional synthesis method applied on design of the linear delta robot is presented.
En el presente articulose exponen el estudio, diseno y desarrollo de un robot paralelo tipo Keops... more En el presente articulose exponen el estudio, diseno y desarrollo de un robot paralelo tipo Keops con estructura modificable construido especificamentepara operar en un espacio de trabajo con forma cilindrica. Se presenta en este articulo las etapas del estudio, diseno y desarrollo de robot, la aplicacion de tecnicas de algoritmos geneticos para el calculo optimo de las dimensiones y laarquitectura de control implementada para regular corriente, velocidad y posicionen motores BrushlessDC. Se finaliza exponiendo los resultados obtenidos del desarrollo del robot paralelo tipo Keops con estructura modificable
This paper presents the progress made in the teleoperation of a robot that performs agricultural ... more This paper presents the progress made in the teleoperation of a robot that performs agricultural taskes as: planting, irrigation, spraying and cutting in a small scalable indoor urban farming are presented. A kinematic analysis of the robot built is presented, and the use of a low cost haptic device, which controls more intuitive slave robot, is proposed. Finally some experimental results that demonstrate the operation of the system is presented.
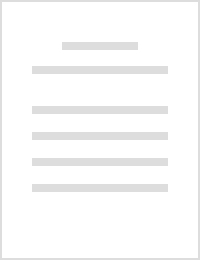
La mora es una de las frutas mas representativas en cuanto a cobertura geografica sembrada en Col... more La mora es una de las frutas mas representativas en cuanto a cobertura geografica sembrada en Colombia y contienen compuestos fenolicos entre ellos las antocianinas. El objetivo de esta investigacion fue evaluar el uso de pretratamientos (microondas, ultrasonido y liofilizacion) para mejorar la extraccion de antocianinas en dos variedades de mora Castilla (R. glaucus) y Silvestre (R. adenotrichos), para su posterior aplicacion como indicador visual de pH. Para ello se realizo un diseno experimental factorial de dos niveles y 4 factores (24 ). El contenido de antocianinas se cuantifico por el metodo de pH diferencial, posteriormente se determino la actividad antioxidante de los extractos mediante los ensayos de DPPH y FRAP. Ademas, se midio el color del extracto a diferentes pH para valorar su uso como indicador visual de pH en diferentes sustancias. Se logro conceptualizar que la variedad de mora y los pretratamientos de liofilizacion y ultrasonido presentaron diferencias significat...

Ingeniería y Ciencia, 2021
Although there are different alternatives to provide energy, there are still remote regions with ... more Although there are different alternatives to provide energy, there are still remote regions with no nearby possibilities of having an electricity supply that meets their basic needs. Colombia, like many countries, does not have uniform environmental conditions; therefore, applying models for the dimensioning of energy systems based on renewable energy can be inefficient and expensive, making it difficult to access electricity in isolated places. The research aims to develop a sizing strategy for a hybrid system based on locally acquired environmental information to size a system that takes advantage of the natural resources available in the local in the best possible way. Information is collected through a data acquisition system on local environmental conditions, system requirements are established based on energy demand, and a mathematical model is sought that represents the electrical behavior. The model makes it possible to analyze the system’s behavior under variable environmen...

IEEE Access, 2020
In the manufacturing sector, industrial robots are being increasingly improved to execute machini... more In the manufacturing sector, industrial robots are being increasingly improved to execute machining tasks as they exhibit significant advantages in terms of flexibility, cost-effectiveness, affordability, and larger work-space when compared to traditional computer numeric control (CNC) machines. However, programming this kind of equipment for robotic machining is complex, due to closed architecture controller and proprietary programming languages limitations. For that reason, this work aims at contributing to the adoption of the STEP-NC standard (STandard for the Exchange of Product model data-Numerical Control (ISO 10303-238 and ISO 14649)), generating programs for robotic machining operations. The STEP-NC data model enables the integration of information from design, process planning, simulation, manufacturing, and even inspection in a single platform, which could create new alternatives for industrial robotic machining programming. In this context, several previous studies are described in this manuscript aiming to highlight the contribution of this work, in addition to the analysis, implementation, and validation of six different STEP-NC architectures describing the advantages that each architecture provides for achieving robotic machining capabilities. Each introduced architecture can successfully generate a STEP-NC robotic machining program, either as ISO 10303-238 or ISO 14649, which are validated in a simulation environment with both a virtual robot model and a real industrial robot equipped with a LinuxCNC controller. This approach can be implemented in different industrial robots. INDEX TERMS Computer numerical control, data modelling, ISO 10303 AP238, linuxCNC controller, robotic machining, STEP-NC standard.

Procedia Manufacturing, 2019
To meet the demands of information virtualization promoted by the fourth industrial revolution, t... more To meet the demands of information virtualization promoted by the fourth industrial revolution, the processes of manufacturing and quality require an architecture that facilitates the integration of processes. The objective of this article is to present an alternative solution, framed in the concept of interoperability, to link the results obtained in the inspection of a part with the data generated in Compliant-STEP Systems CAD/CAM/CNC. For the implementation of the solution, a closed-loop architecture for manufacturing and inspection it was designed that uses as a mechanism of integration a data model in a neutral format. The measurement results are homogenized both semantically and syntactically to be handled by each of the systems involved in the closed-loop Manufacturing. Dimensional metrology data are used to create a compensation strategy and correct identified manufacturing errors in the inspection process. A framework was designed to manage the exchange of information. The main contribution of the article is the detailed description of the development of the adherent system to the standard ISO 10303 known as STEP (STandard for the Exchange of Product model data). Finally, an analysis is done based on a case study that involves definition and extraction of design specifications, used for both manufacturing and measurement. The solution presented allows the use of measurement data within a closed manufacturing loop, ensuring the integrity of information and access so that each system can use it for different purposes.

IFAC-PapersOnLine, 2019
Among the challenges posed by the new industrial revolution-Industry 4.0 is the integration of sy... more Among the challenges posed by the new industrial revolution-Industry 4.0 is the integration of systems associated with manufacturing. In this sense, the inspection process assumes an important role since it provides the information base to make the decisions that allow reaching the design and quality specifications. From the manufacturing point of view, Additive Manufacturing (AM) contains the potential to meet production demands by making efficient use of resources, reducing manufacturing time, and enabling the manufacture of complex parts. The idea of integrating the inspection process with a robotic system for additive manufacturing seeks both to improve the quality of the parts produced and to find methods to optimize the process and create a sustainable system. However, to make this combination a reality, it is necessary to face the barriers posed by the lack of integration of the information produced by the different computerized systems throughout the life cycle of the product. Thus, there is no integration of feedback information from shop-floor necessary for inspection and validation of the part manufactured with AM, which does not allow a closed-loop digital thread. Concerning this, the present article proposes the development of an integration strategy with a digital data model based on STEP-NC (Standard for the Exchange of Product model data-Numerical Control) for closed-loop AM. The data models in STEP-NC for the AM and inspection tasks it develops, highlighting the scenario of integrated feedback for the closed-loop AM digital thread. Are presented the architecture of integration validated by using an open AM platform and the results of error control over the parts.

IFAC-PapersOnLine, 2019
The MTConnect standard provides a bridge to bring networked physical manufacturing resources to c... more The MTConnect standard provides a bridge to bring networked physical manufacturing resources to cloud manufacturing environments. However, making legacy manufacturing equipment compliant with this new standard is still a difficult task. Regarding additive manufacturing machines, this issue has been poorly studied. To address the subject, this work introduces an MTConnect-compliant framework for shopfloor data access and monitoring of RepRap additive manufacturing machines based on Arduino open technology controllers. A communication channel based on TCP/IP protocol using an Ethernet module was incorporated into the machine's system to extend the functionalities of RepRap 3D printers to connect to the Internet. Two MTConnect implementation architectures named Type 1 and Type 2 were proposed. A webclient application was also developed to validate the system by performing real-time machine monitoring over the Internet. The proposed MTConnect solution allows retrieving data of axes position, heat-bed temperature, hot-end temperature, material extrusion, current layer number and elapsed time from the web application, demonstrating feasibility to operate in cloud manufacturing environments.

Journal of the Brazilian Society of Mechanical Sciences and Engineering, 2019
Parallel manipulator robots are widely used in a large number of applications because they provid... more Parallel manipulator robots are widely used in a large number of applications because they provide important advantages in terms of superior speeds and accelerations, high stiffness and good dynamic performance. In additive manufacturing (AM), this kind of kinematic structures is being increasingly explored to develop new curved and multi-directional fabrication strategies.Based on this application, this work presents the design and dimensional synthesis of a new structure of the Linear Delta parallel robot for AM (3D printing). The new structure uses an innovative concept of Delta mechanism with single legs and rotational joints, which consists of twelve links (three parallel single legs), three prismatic joints and eleven revolute joints. A particular feature of the proposed mechanism is that it contains a joint common to all the kinematic chains instead of a mobile platform as in the conventional Linear Delta structures. Mobility analysis, inverse and direct kinematics, and a study of dimensional synthesis are described in detail. A method of efficient optimization based on genetic algorithms is used to find the minimum dimensional parameters of the robot, considering the maximization of the useful workspace as the main performance index. In order to validate the proposal, a prototype of the robot was built. Capability and geometric deviations analysis was carried out for three test parts resulting in a 0.3-mm deviation/error within a confidence interval of 99.7%.

Proceedings of the Institution of Mechanical Engineers, Part I: Journal of Systems and Control Engineering, 2019
Because of remarkable characteristics such as superior speeds and accelerations, high stiffness a... more Because of remarkable characteristics such as superior speeds and accelerations, high stiffness and good dynamic performance, parallel robots are being increasingly adjusted to different task requirements in the manufacturing field. Their parallel structures made by closed-loop kinematic chains are better suited to develop new curved and multidirectional fabrication strategies in Additive Manufacturing. Based on this application, the conceptual design and dimensional optimization of a new structure of the linear delta parallel robot for Additive Manufacturing (three-dimensional printing) is presented. The new structure uses an innovative concept of delta mechanism with single legs and rotational joints, which consists of 12 links (three single parallel legs), three prismatic joints, and 11 revolute joints. A particular feature of the proposed mechanism is that it contains a joint common to all the kinematic chains instead of a mobile platform. Quality function deployment is used as ...
Procceedings of the 24th ABCM International Congress of Mechanical Engineering, 2017
journal of Engineering Science and Technology Review, 2018
This paper presents the development of a remote robotic platform to monitor and take care of urba... more This paper presents the development of a remote robotic platform to monitor and take care of urban crops. The agricultural robot performs activities such as sowing, irrigation, fumigation, and pruning activities on a small scalable structured crop. The generalities of the design of an anthropomorphic robot with five degrees of freedom, the description of the development of a multipurpose end effector for the development of agricultural tasks, the implemented architecture of the teleoperation system of the robot is presented, including a visual support system and the employment of a low-cost master robot that allows the slave robot to be controlled more intuitively. Finally, some experimental results that show the functioning of the system are presented.
Anais do X Congresso Nacional de Engenharia Mecânica, 2018
Anais do IX Congresso Brasileiro de Engenharia de Fabricação, 2017
Anais do IX Congresso Brasileiro de Engenharia de Fabricação, 2017
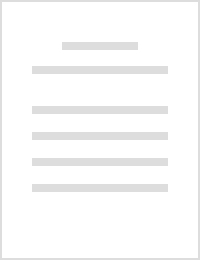
Anais do IX Congresso Brasileiro de Engenharia de Fabricação, 2017
Recentemente, máquinas com arquiteturas baseadas em robôs de cinemática paralela vêm sendo amplam... more Recentemente, máquinas com arquiteturas baseadas em robôs de cinemática paralela vêm sendo amplamente utilizadas em aplicações relacionadas com processos de manufatura aditiva, pelo fato que possuem vantagens como a precisão, baixa inercia, velocidade e aceleração que os tornam atrativos para estas aplicações. Neste contexto, o presente trabalho descreve o desenvolvimento de um robô com arquitetura paralela 5R para aplicações de Manufatura Aditiva. O projeto é abordado sob uma metodologia organizada para o desenvolvimento de produto através de três fases principais: Na primeira fase, de desenvolvimento conceitual, são levantadas as necessidades do cliente usando o método " Quality Function Deployment " para transformar ditas necessidades em um set de especificações metas do produto. Na segunda fase, projeto no nível de sistema, são definidos os princípios de solução para atingir as especificações meta e as melhores alternativas são selecionadas para definir a arquitetura global do sistema. Por último na fase de projeto detalhado, é apresentada a máquina construída com base nos critérios de solução definidos nas duas primeiras fases. Nesta fase também é apresentada uma análise cinemática do mecanismo 5R com intuito de instanciar as equações matemáticas que permitirão o posicionar o efetuador final em um determinado ponto dentro do espaço de trabalho. O resultado deste trabalho é uma máquina baseada em um robô paralelo com capacidade para fabricar peças protótipo ou funcionais utilizando a tecnologia de Modelagem por Deposição Fundida (FDM). Além disso, a plataforma desenvolvida pretende-se utilizar em atividades de treinamento e aperfeiçoamento acadêmico na área de robótica. Palavras-chave: manufatura aditiva, robô paralelo, mecanismo 5R, ferramentas de projeto, analise cinemática.
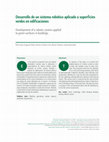
Revista de Tecnología, 2017
Los autores declaran que no tienen conflicto de interés. E T Resumen n este artículo se propone e... more Los autores declaran que no tienen conflicto de interés. E T Resumen n este artículo se propone el uso de sistemas robotizados remotos para la plantación y mantenimiento de cultivos urbanos implementados en techos, azoteas, fachadas y paredes de edificaciones. El sistema robótico busca evitar el riesgo que puede conllevar el mantenimiento por parte de los operarios de estos cultivos al encontrarse a alturas considerables. De igual forma busca mejorar las condiciones de mantenimiento de los cultivos basándose en un control mixto que integra las tareas planeadas por el usuario y la información de humedad, luminosidad y temperatura captura por los sensores. El sistema robotizado cumple funciones de siembra, riego, fumigación, desyerbado y recolección de frutos. También se presenta un resumen del impacto ambiental que se genera al implementar este tipo de sistemas.
Uploads
Papers by Cristhian Jaimes