Papers by Catalin Fetecau
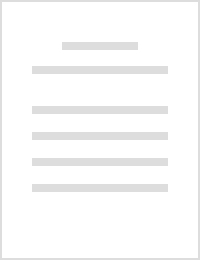
Volume 2: Manufacturing Processes; Manufacturing Systems; Nano/Micro/Meso Manufacturing; Quality and Reliability, Sep 3, 2020
This paper reports on the 3D printing of flexible and stretchable parts based on multiwall carbon... more This paper reports on the 3D printing of flexible and stretchable parts based on multiwall carbon nanotubes (MWCNTs)/polyester-based thermoplastic polyurethane (TPU) nanocomposites. The rheological properties of the MWCNT/TPU nanocomposites with different wt.% of MWCNTs (0.1–3) were determined and used as guidance for the extrusion and 3D printing processes. MWCNT/TPU filaments were extruded and used for 3D printing of different flexible and stretchable parts. The mechanical, electrical, and piezoresistive response of the MWCNT/TPU nanocomposite filaments and 3D printed parts under static and monotonic loading was studied. The experimental results show that with increasing temperature and shear rate, respectively, the shear viscosity of the MWCNT/TPU nanocomposite decreases, whereas the viscosity increases with increasing wt.% of MWCNTs. With the addition of MWCNTs, the elastic modulus and tensile strength of the feedstock filament all increase, enhancing the printability of TPU by increasing the buckling resistance and the stability of the 3D printed layer. The electrical conductivity of the 3D printed MWCNT/TPU nanocomposites increases with increasing wt.% of MWCNTs and exceeds the conductivity of the filaments. The 3D printed MWCNT/TPU nanocomposites with 3 wt.% show an electrical conductivity about 10 S/m, irrespective of the printing direction. Moreover, the 3D printed MWCNT/TPU nanocomposites exhibit good mechanical properties and high piezoresistive sensitivity with gauge factor (50–600) dependent on both strain and printing direction.
MATEC web of conferences, 2019
In this paper, the feasibility of 3D printing polypropylene/ multi-walled carbon nanotube (PP/MWC... more In this paper, the feasibility of 3D printing polypropylene/ multi-walled carbon nanotube (PP/MWCNT) composites by fused deposition modeling. First, the rheological behavior of PP with 0.3, 0.5 and 1 wt.% of MWCNT was investigated in order to determine the printability in terms of melt shear viscosity and flow activation energy. Second, the filament extrusion process was optimized by the trial-and-error method in order to obtain round and constant filaments. Finally, tensile specimens were printed and tested in order to determine the mechanical properties at various printing direction. Experimental results show that the PP/MWCNT composite filaments with MWCNT loading up to 1 wt.% have good printability characteristics and can be successfully 3D printed with good mechanical performance.
In this paper, the impact of recycling and remanufacturing on the behavior of low-density polyeth... more In this paper, the impact of recycling and remanufacturing on the behavior of low-density polyethylene/multi-walled carbon nanotube (LDPE/MWCNT) composites is investigated. LDPE/MWCNT composites with 0.1–5 wt%, previously manufactured by injection molding, were mechanically recycled and remanufactured by injection molding and 3D filament extrusion, and the rheological, electrical, and mechanical properties were analyzed and compared with those of virgin composites under the same conditions. Experimental results demonstrate that the recycled LDPE/MWCNT composites have similar rheological, electrical, and mechanical properties as that of virgin composites, if not better. Therefore, the recycled LDPE/MWCNT composites have a great potential for being used in engineering applications, while reducing the environmental impact.
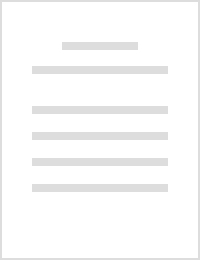
In this paper, millimeter-scale straight parallel micro-channels were fabricated in PMMA (Polymet... more In this paper, millimeter-scale straight parallel micro-channels were fabricated in PMMA (Polymethyl-methacrylate) using the tip-based micro-fabrication method. The dimensional characteristics (channel width, channel depth and pile-up height) of micro-channels were evaluated and the effects of normal load and speed on the micro-channel geometry and friction were examined. A logarithmic relationship between the normal load and micro-channel depth was identified. The experimental results indicate that the selection of the normal load is critical to achieve a desired micro-channel geometry using a single pass scratching. To machine a micro-channel with a finite depth in PMMA, the normal load must be higher than 4.5 N. Within the range of the tested normal loads, about 70% of the channel height was elastically recovered after a single pass, and pile-ups as high as 50–60% of the depth were observed along the micro-channel sides.
Polymers, Jan 23, 2023
This article is an open access article distributed under the terms and conditions of the Creative... more This article is an open access article distributed under the terms and conditions of the Creative Commons Attribution (CC BY
Journal of Materials Processing Technology, Apr 1, 2009
In this paper, a new grinding procedure for the curved cutting edge twist drills is presented, i.... more In this paper, a new grinding procedure for the curved cutting edge twist drills is presented, i.e., the toroidal grinding procedure. Within this procedure, the clearance surface of the twist drill is a cylindrical helicoid surface with a constant pitch. Based on the principle of distance minimization and envelope theory, a numerical method of calculating the grinding wheel profile is developed. This grinding method allows the profile of the main cutting edge to be continuous and obtained directly during the grinding procedure. The feasibility of the toroidal grinding method is verified by drill grinding experiment and drilling measurements.
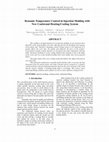
The cooling is an important process in injection molding. It can represent more than 60% of the t... more The cooling is an important process in injection molding. It can represent more than 60% of the total molding cycle time, affecting directly the shrinkage and warpage of the plastic part. Therefore, designing a good cooling system is very important as it greatly affects the cycle time, the quality and indirectly the price of the product. Conventional straight cooling channels are machined into mold components with gun drills. Alternative methods to create cooling channels that conforms or fits to the shape of the cavity and core of the mould providing better heat transfer have been proposed before. This paper deals with a new cooling system that follows the shape of the part in core and cavity. This alternative method uses a metallic mold with thin walls, to increase the heat absorption from the molten plastic and reduce thermal inertia, mounted in a chamber constructed from a thermo-insulating material. Between the active elements of the mold and the exterior chamber a heating/cooling fluid is circulating. This ensures quasi isothermal filling conditions and a uniform as well as a more efficient cooling process.

Although modern surgical techniques in orthopedics are now available, the treatment of the diseas... more Although modern surgical techniques in orthopedics are now available, the treatment of the diseased hip joint does not end with surgical replacement, the postoperative rehabilitation being of the utmost importance. Present hip implants use an acetabular cup, which is constructed entirely of polyethylene or of metal with polyethylene lining. The debris from implant wear, particularly polyethylene is one of the contributory factors of the hip implants failure. Although the technology of hip implants has been intensively developed with high success rates, the mechanism of polyethylene wear and bone degradation are not fully understood. For this reason, our research efforts focus on the dynamic modeling of the hip joint, following regular human activity simulation in which can be determined the forces values from within the prothesed joint and then used in the designing of reliable components.
Multicomponent injection molding is gaining popularity due to its potential to produce multifunct... more Multicomponent injection molding is gaining popularity due to its potential to produce multifunctional parts at low costs. Autodesk Moldflow Insight injection molding simulation software is providing in-depth analysis and optimization of plastic parts and their associated molds which further reduces the production cost of parts. In this paper is presented a study of injection molding optimization process of bi-component tensile test specimens using different materials. The main concern of this optimization is to establish the optimal condition and material combinations for the tensile specimens' injection molding. Also it is very important to study the effects of the interface geometry between the two materials on the strength adhesion.
Journal of Engineering Sciences and Innovation
Filament material is an important factor to be considered in the product development by 3D printi... more Filament material is an important factor to be considered in the product development by 3D printing, since it can affect not only the quality but also the functionality of the printed parts. Thus, the objective of this paper is to investigate how feasible would be to use low- and high-density polyethylene to fabricate 3D printing filaments. Since the extrusion process depends on the rheological behavior of the polymers, first, the melt viscosity of LDPE and HDPE was analyzed by capillary rheology. Then, LDPE and HDPE filaments of 1.75 mm diameter were extruded under different processing conditions and subjected to tensile tests to determine the mechanical properties. Results showed that the LDPE and HDPE are suitable for manufacturing 3D printing filaments if the extrusion processing conditions are optimized.
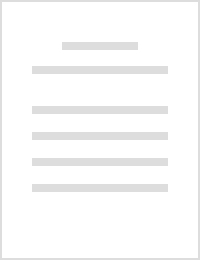
Volume 2: Processes; Materials
This study focuses on 3D printing of multi-walled carbon nanotube/high density polyethylene (MWCN... more This study focuses on 3D printing of multi-walled carbon nanotube/high density polyethylene (MWCNT/HDPE) composites. First, rheological properties of 0.1, 1, and 5 wt.% MWCNT/HDPE composites were investigated to estimate the 3D printability window. Second, filaments with 1.75 mm diameter were fabricated and subsequently extruded by a commercial 3D printer. Finally, the filaments and 3D printed parts were tested to correlate the rheological, mechanical, and electrical properties with processing parameters. Experimental results show that flow behavior of MWCNT/HDPE composites is a critical factor affecting the 3D printability. The shear viscosity exhibits good shear thinning behavior at high shear rates and significantly increases with increasing nanotube loading from 0.1 to 5 wt.%, at low shear rates. Reliable MWCNT/HDPE filaments were obtained with smooth surface finish and good mechanical and electrical properties. The 0.1 and 1 wt.% MWCNT/HDPE filaments exhibit very good printing ...
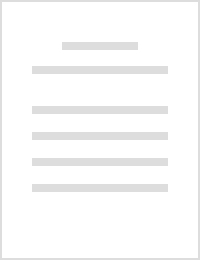
Volume 2: Manufacturing Processes; Manufacturing Systems
Anisogrid cylindrical lattice (ACL) structures have been successfully used in space applications,... more Anisogrid cylindrical lattice (ACL) structures have been successfully used in space applications, demonstrating high mechanical performance and weight efficiency. However, the manufacturing process for the composite ACL structures is very complex and, traditionally, involves different technologies, including winding of filaments or prepregs and curing. Tacking the advantage of the fused deposition modeling (FDM) to manufacture completely integral composite parts with complex shape, in this paper, the FDM-3D printing of ACL structures using carbon fiber (CF) and glass fiber (GF) reinforced polyamide 12 (PA12) composites has been investigated. The mechanical behavior of 3D printed ACL structures has been analyzed in terms of the static stiffness, specific load, and failure mode through axial and transverse compression tests, as a function of the geometrical parameters of the lattice structure. It was observed that, under transverse compression, after the initial linear elastic respons...
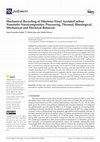
Polymers
Recycling polymer/carbon nanotube (CNT) nanocomposites is not well common, despite a growing inte... more Recycling polymer/carbon nanotube (CNT) nanocomposites is not well common, despite a growing interest in using polymer/carbon nanotube (CNT) nanocomposites in industrial applications. In this study, the influence of mechanical recycling on the thermal, rheological, mechanical and electrical behavior of ethylene-vinyl acetate (EVA)/CNT nanocomposites is investigated. EVA/CNT nanocomposite with different amounts of CNTs (1, 3 and 5 wt.%) was subjected to mechanical grinding and reprocessing by injection molding in a close-loop up to three cycles, and the changes induced by mechanical recycling were monitored by Differential Scanning Calorimetry (DSC), capillary rheology, scanning electron microscopy (SEM), electrical resistance and tensile tests. It was found that the EVA/CNT nanocomposites did not exhibit significant changes in thermal and flow behavior due to mechanical recycling and reprocessing. The recycled EVA/CNT nanocomposites retain close to 75% of the original elastic modulu...
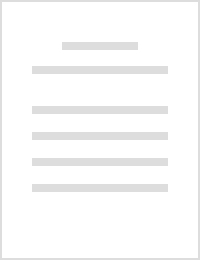
Volume 2: Additive Manufacturing; Materials, 2017
In this paper, millimeter-scale straight parallel micro-channels were fabricated in PMMA (Polymet... more In this paper, millimeter-scale straight parallel micro-channels were fabricated in PMMA (Polymethyl-methacrylate) using the tip-based micro-fabrication method. The dimensional characteristics (channel width, channel depth and pile-up height) of micro-channels were evaluated and the effects of normal load and speed on the micro-channel geometry and friction were examined. A logarithmic relationship between the normal load and micro-channel depth was identified. The experimental results indicate that the selection of the normal load is critical to achieve a desired micro-channel geometry using a single pass scratching. To machine a micro-channel with a finite depth in PMMA, the normal load must be higher than 4.5 N. Within the range of the tested normal loads, about 70% of the channel height was elastically recovered after a single pass, and pile-ups as high as 50–60% of the depth were observed along the micro-channel sides.
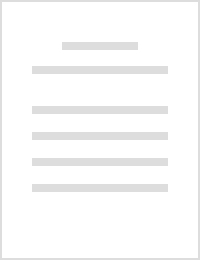
Journal of Manufacturing Science and Engineering, 2020
This paper reports on the 3D printing of flexible and stretchable parts based on multiwall carbon... more This paper reports on the 3D printing of flexible and stretchable parts based on multiwall carbon nanotube (MWCNT)/polyester-based thermoplastic polyurethane (TPU) nanocomposites. The rheological properties of the WCNT/TPU nanocomposites with different wt% of MWCNTs (0.1–3) were determined and used as guidance for the extrusion and 3D printing processes. MWCNT/TPU filaments were extruded and used for 3D printing of different flexible and stretchable parts. The mechanical, electrical, and piezoresistive response of the MWCNT/TPU nanocomposite filaments and 3D printed parts under static and monotonic loading was studied. The experimental results show that with increasing temperature and shear rate, respectively, the shear viscosity of the MWCNT/TPU nanocomposite decreases, whereas the viscosity increases with increasing wt% of MWCNTs. With the addition of MWCNTs, the elastic modulus and tensile strength of the feedstock filament all increase, enhancing the printability of TPU by incre...

The goal of this paper is to study the creep behaviour of multi-walls carbon nanotubes (1, 3, 5 w... more The goal of this paper is to study the creep behaviour of multi-walls carbon nanotubes (1, 3, 5 wt.% MWCNTs) filled polypropylene (PP) through the instrumented indentation technique. Two types of the 3-step indentation test were considered to analyse viscoelastic behaviour through sharp indentation at room temperature. Under the loading conditions, the PP/MWCNTs samples present a time-independent plastic behaviour which must be considered not to under/overestimate the viscoelastic properties. The ratio of residual indentation depth to the maximum indentation depth at peak load calculated from the initial portion of the unloading curve was over 0.7 and demonstrated the plastic character of tested materials. The indentation hardness and modulus calculated from the slope at the unloading curve were changed due to the presence of plastic deformation from the loading phase, to the load intensity and hold time. The local distribution of carbon nanotubes lead to the variation in creep resp...
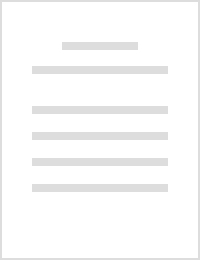
Volume 2: Materials; Joint MSEC-NAMRC-Manufacturing USA, 2018
In this study, the effects of fatigue and cryogenic treatments on the mechanical behavior of low-... more In this study, the effects of fatigue and cryogenic treatments on the mechanical behavior of low-density polyethylene/ multi-walled carbon nanotube (LDPE/MWCNT) composites have been investigated. Injection-molded samples of LDPE/MWCNT composite with different MWCNT weight fractions (0.1–5.0 wt.%) were subjected to cryogenic and fatigue treatments under different testing conditions, and the residual-mechanical properties were investigated. To monitor the fatigue damage, additionally, the electrical conductivity was measured. The results show that the LDPE/MWCNT composites retained good residual-mechanical properties after fatigue (more than 85% of its initial Young modulus) and cryogenic (more than 75% of its initial tensile strength and Young’s modulus) treatment. For the LDPE/MWCNT composites, the electrically conductive nanotube network can be efficiently maintained up to 25 000 fatigue cycles.
GHEORGHE VASILE1, CATALIN FETECAU 2*, ALEXANDRU SERBAN3 1Technical University of Pitesti, Departm... more GHEORGHE VASILE1, CATALIN FETECAU 2*, ALEXANDRU SERBAN3 1Technical University of Pitesti, Department of Technologies and Management, 1 Targul din Vale Str., 110040, Pitesti, Romania 2“Dunarea de Jos” University of Galati, Department of Manufacturing, Robotics and Welding Engineering, 47 Domneasca Str., 800008, Galati, Romania 3“Transilvania” University of Brasov, Department of Installations for Civil Engineering, 29 Eroilor Str., 500036, Brasov, Romania.

The objective of this paper consists in the minimization of warpage problems which depend on the ... more The objective of this paper consists in the minimization of warpage problems which depend on the process parameters during injection molding of thin wall plastic parts using an optimization technique involving Taguchi method, S/N ratio and ANOVA method. For this purpose, a number of experiments are carried out by utilizing the combination of process parameters based on a three-level L 9 Taguchi orthogonal array table. To achieve the minimum warpage, the optimum level of process parameters is determined. A drain with 8 sockets is investigated, where melt temperature, mold temperature, injection speed, and packing pressure are selected to be the process variables. The results show that the optimum parameters that can minimize the warpage problem are: melt temperature (190°C), mold temperature (30°C), injection speed (70 mm/s), and packing pressure (55 MPa). The most effective factor on the warpage is packing pressure with a general influence of 55.71%.
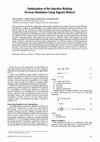
This work aims to present the optimization of the design of a plastic part manufactured at Accura... more This work aims to present the optimization of the design of a plastic part manufactured at Accurate Machine and Tool Ltd. Canada, by using Moldflow [1] combined with the optimization method developed by Dr. Genichi Taguchi. The method uses statistical principles and involves reducing the variation in a process through robust design of experiments. The experimental design proposed by Taguchi uses orthogonal arrays to organize the parameters affecting the process and the levels at which they should be varied; it allows for the collection of the necessary data to determine which factors most affect product quality with a minimum amount of experimentation, thus saving time and resources. Moldflow allows part designers and mold makers to predict the manufacturability and quality of their design during preliminary product development stages. It helps to select the best injection gates configuration, as well as the values of mold temperature (Tw), melt temperature (Tm) and an optimized bod...
Uploads
Papers by Catalin Fetecau