Papers by Nadeem Ali Bhatti
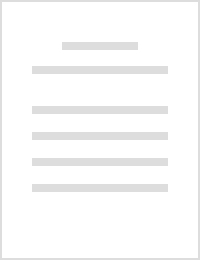
Lecture Notes in Mechanical Engineering, 2019
In this study, a detailed predictive numerical modeling technique is developed for three differen... more In this study, a detailed predictive numerical modeling technique is developed for three different kinds of hybrid and non-hybrid architectures of 3D woven orthogonal composites. A unit cell, full finite element meso model, is developed to simulate the elastic and damage progression behavior under uni-axial compression. Material systems for 3D woven Composites used in this study are Carbon/epoxy, Kevlar epoxy, and Hybrid formulation. The geometry of the constituents of the unit cell, fiber tows, and matrix, was determined through the microscopic analysis of the woven structures. The unit cell model used an idealized geometry without incorporating the fiber undulation which is a pervasive effect during the weaving process of 3D woven composites. Abaqus standard solver and a UMAT code incorporating the damage model within Abaqus was used to compute the deformation of the unit cell under in-plane compression loading. Moreover, determining the effect of void contents on the mechanical properties of the material, Balshin’s empirical equation was used to calibrate the input material parameters. The results from the numerical analysis are then compared with the experimental results and it is found that the predicted elastic modulus and compressive strength for all three types of architecture are in good agreement with the experimental results. Overall, the unit cell meso model furnished fairly accurate estimation of the compressive properties of 3D woven composites for different material systems with consideration of void contents.

This paper aims to provide an overview of experimental and numerical work related to fretting fat... more This paper aims to provide an overview of experimental and numerical work related to fretting fatigue crack initiation criteria. The complexity of modelling fretting fatigue arises due to the presence of multi axial stress state and wear, hence, it is imperative to define the crack initiation criteria. Among many available criteria, some of the most widely used have been summarized here, to provide an insight of the topic and to demonstrate the applicability of these criteria. For convenience, different criteria have been grouped together based on the approaches used to define failure parameters. The generalize classification includes, critical plane approach, stress-invariant approach and continuum damage mechanics approach. Besides experimental work, quantum of work has been done to implement these models using finite element methods (FEM). The strength of finite element methods is demonstrated as it provides minute information about crack initiation phase, contact stresses and es...
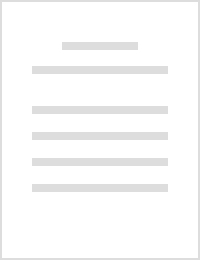
Proceedings of the 7th International Conference on Fracture Fatigue and Wear, 2018
The phenomenon of fretting fatigue can cause crack nucleation at the contact interface due to mul... more The phenomenon of fretting fatigue can cause crack nucleation at the contact interface due to multiaxial loading conditions. The nucleation phase may take a significant proportion of life under fretting fatigue, which leads to micro crack initiation. There are several approaches in vogue to estimate crack initiation life. The current study, however, aims to compare two approaches, namely, Critical Plane (CP) approach and Stress Invariant (SI) approach. Smith Watson Topper (SWT), McDiarmid (MD) parameters, which represent critical plane approach, whereas, Crossland parameter (CL), which represents SI approach, are adopted for this purpose. These parameters are applied to cylinder on a flat configuration and predicted numerical results are also compared with experimental results from literature. It is observed that, under fretting fatigue conditions, life prediction capability of critical plane approach is better than stress invariant approach especially at large number of cycles to f...
Lastly, special thanks to my wife Rabia Naz, son Haziq Ali Bhatti and daughter Zenia Nadeem, for ... more Lastly, special thanks to my wife Rabia Naz, son Haziq Ali Bhatti and daughter Zenia Nadeem, for their love, faithful support, encouragement and comfort that allowed me to focus completely on my work.

Metals, 2018
The analysis of fretting fatigue plays an important role in many engineering fields. The presence... more The analysis of fretting fatigue plays an important role in many engineering fields. The presence of heterogeneity may affect the performance of a machine or a structure, including its lifetime and stability. In this paper, the effect of randomly distributed micro inclusions on the fretting fatigue behaviour of heterogeneous materials is analysed using the finite element method (FEM) for different sizes, shape and properties of inclusions. The effect of micro inclusions on macroscopic material properties is also considered by representative volume element (RVE). It is shown that the influence of micro inclusions on macroscopic material properties cannot be ignored, and the shape and size of the inclusions have less effect on the macroscopic material properties as compared to the material properties of inclusion and volume ratio. In addition, various parameters of inclusions have little effect on the peak tensile stress, which remains almost the same as homogeneous material. Peak she...
Tribology International, 2019
This is a PDF file of an article that has undergone enhancements after acceptance, such as the ad... more This is a PDF file of an article that has undergone enhancements after acceptance, such as the addition of a cover page and metadata, and formatting for readability, but it is not yet the definitive version of record. This version will undergo additional copyediting, typesetting and review before it is published in its final form, but we are providing this version to give early visibility of the article. Please note that, during the production process, errors may be discovered which could affect the content, and all legal disclaimers that apply to the journal pertain.

Tribology International, 2018
Damage nucleation involves creation of micro cracks, which are discontinuities in a material cons... more Damage nucleation involves creation of micro cracks, which are discontinuities in a material considered as continuous at a larger scale. Continuum Damage Mechanics (CDM) approach provides a tool to study damage nucleation under plane and fretting fatigue conditions. Under fretting fatigue conditions, the loading sequence may produce non-proportional stresses. This paper aims to investigate the effect of non-proportional loading on damage nucleation. For this purpose, a CDM based damage model for non-proportional loading is developed and applied to cylindrical pad and flat specimen configuration. The numerical results are also compared with experimental results from literature. It is found that, taking into account the triaxiality function variation in damage law, improves crack initiation lifetime estimation. In addition, a sensitivity analysis is performed by varying stress range and triaxiality function. It is found that for in phase loading only the stress range affects the initiation life, whereas, for out of phase loading both stress range and triaxiality function affect initiation life, especially at higher ranges.

Tribology International, 2018
This study aims to provide an overview of numerical and experimental work, related to crack nucle... more This study aims to provide an overview of numerical and experimental work, related to crack nucleation under fretting fatigue conditions. In fretting fatigue, multiaxial loads and severe stress gradients are present at the contact interface, which can lead to failure. The damage process, in general, is considered as a two-phase phenomenon, namely, nucleation and propagation. Various damage models and approaches are available in literature to model each phase. In the present work, different criteria, related to nucleation phase, are classified based on the approach used to define failure. These approaches include, critical plane approach, stress invariant approach, fretting specific parameters and continuum damage mechanics. Apart from theoretical background, the work related to the applications of these approaches to fretting fatigue problems is also presented. It is observed that, to analyse various aspects, intricate details near the contact interface and mechanisms involved in fretting fatigue, the strength of finite element method can be employed. In the light of numerical and experimental observations, comparison between different approaches, common sources of errors in prediction and generalized conclusions are presented.
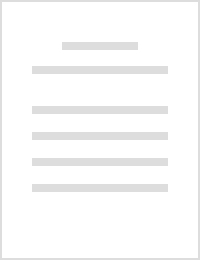
Tribology International, 2019
Abstract Fretting fatigue involves multiaxial stress field due to presence of contact between two... more Abstract Fretting fatigue involves multiaxial stress field due to presence of contact between two bodies. Near the contact edge, high stress gradient may be present depending on load and geometrical conditions. To account for high stress gradient or singular results, a regularization method may be required for better prediction of crack initiation angle and life. In the present work, conventional point and volume averaging methods are compared with a proposed quadrant averaging method to predict crack initiation angle and life. It is found that quadrant method produce more realistic results for initial crack orientation than other methods. Two multiaxial critical plane damage parameters, McDiarmid (MD) and Fatemi Socie (FS) are employed for this purpose. In addition, the influence of stress averaging on crack initiation life is analysed for two different geometries. It is observed that critical radius for stress averaging depends on stress gradient or rate of decay of damage parameter under the surface of the contact.

Journal of Physics: Conference Series, 2017
Fretting fatigue phenomena occurs due to interaction between contacting bodies under application ... more Fretting fatigue phenomena occurs due to interaction between contacting bodies under application of cyclic and normal loads. In addition to environmental conditions and material properties, the response at the contact interface highly depends on the combination of applied loads. High stress concentration is present at the contact interface, which can start the damage nucleation process. At the culmination of nucleation process several micro cracks are initiated, ultimately leading to the structural failure. In this study, effect of ratio of tangential to normal load on contact stresses, slip amplitude and damage initiation is studied using finite element analysis. The results are evaluated for Ruiz parameter as it involves the slip amplitude which in an important factor in fretting fatigue conditions. It is observed that tangential to normal load ratio influences the stick zone size and damage initiation life. Furthermore, it is observed that tensile stress is the most important factor that drives the damage initiation to failure for the cases where failure occurs predominantly in mode I manner.

Tribology International, 2018
The phenomenon of fretting fatigue involves multiaxial stress states near the contact interface a... more The phenomenon of fretting fatigue involves multiaxial stress states near the contact interface and is mainly characterized by nucleation and propagation phases. Based on the mechanism of each phase, various approaches have been developed to predict damage initiation location and life. This paper aims to investigate the effectiveness of continuum damage mechanics (CDM) approach under in phase and 90° out of phase loading. Two cases with different material and loading conditions are considered for this analysis. The first case includes constant normal load and phase difference is generated between axial cyclic stress and tangential load. Whereas in the second case, cyclic normal load is applied and phase difference is generated between normal load and other two loads i.e. cyclic axial stress and tangential load. The results obtained using CDM approach are compared to those obtained using critical plane (CP) approach. The numerical results are also compared with experimental results from literature. It is observed that, both approaches provide good estimate of initiation location and life for in phase loading. With phase difference of 90°, the initiation locations also match well with the experimental results, however, for life estimation CDM approach has shown better prediction than CP approach, especially at lower loads. In addition, both approaches have shown that with phase difference of 90°, the fretting fatigue life increases as compared to in phase loading.

Tribology International, 2017
This study focuses on application of critical plane approach to in-phase and out-of-phase loading... more This study focuses on application of critical plane approach to in-phase and out-of-phase loading conditions in fretting fatigue problems. The efficacy of various multiaxial damage criteria is analysed to determine critical plane orientation and initiation life, and is investigated for the first time in case of out-of-phase loading condition. Furthermore, our study focuses on the estimation of initiation angle and initiation lives using multiaxial damage criteria. For analysis purpose, the damage criteria are categorized as stress-based (Findley parameter and McDiarmid criterion), strain-based (Brown-Miller criterion and Fatemi-Socie criterion) and virtual strain energybased (Smith-Watson-Topper criterion and Liu 1 and 2 criteria). It is observed that shear stress and shear strainbased criteria are able to predict both critical plane orientation and fretting fatigue lifetimes, whereas energybased criteria, which employ normal stress and strain, are only suitable to predict initiation life. The deviation in estimation of initiation life for stress-based criteria is observed to be higher than others if the internal stresses are higher than yield stress. It is shown that initiation can occur on either of the preferred shearing plane depending upon material and loading conditions. The phase difference of 90 and 180 increases and decreases the initiation life respectively as compared to in-phase loading. In addition, 90 phase difference introduces more shearing planes for damage nucleation.

Tribology International, 2017
Fretting fatigue is a complex phenomenon involving various factors, such as slip amplitude, coeff... more Fretting fatigue is a complex phenomenon involving various factors, such as slip amplitude, coefficient of friction, shear load and loading phase difference. In this study, three numerical models are used to model the effect of both in phase and out of phase loading on contact stresses and damage initiation locations. Three phase difference angles are considered, i.e. 0°, 90° and 180°, for this purpose. It is observed that phase difference affects the shear traction and tensile stress profiles at the contact interface, whereas no significant effect is observed on convergence efficiency. It is also shown that, due to increase of stick zone width, the convergence is slower during the unloading step than during the loading step. SWT parameter and Ruiz parameter are adopted as two crack initiation criteria in order to investigate their performance in case of out of phase loading. The critical locations predicted by both parameters have shown good agreement with experimental results from literature. In addition, it is observed that phase difference significantly affects the damage initiation location.
Uploads
Papers by Nadeem Ali Bhatti