Papers by Anil Kumar Shrivastava
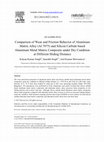
Materials Today: Proceedings, 2017
The wear and friction properties of aluminum matrix alloy and silicon carbide based aluminum meta... more The wear and friction properties of aluminum matrix alloy and silicon carbide based aluminum metal matrix composites under dry condition at different sliding distance (i.e. 1979.20 m and 2262 m) with loads varies between 10 N-30 N have been studied by using pin on disc wear measuring machine (Make: DUCOM, Bangalore). All experiments were performed at room temperature and results revealed that silicon carbide based aluminum metal matrix composites and aluminum matrix alloys possesses better properties at low sliding distance and at lower load also. Although silicon carbide based aluminum metal matrix composites shows better properties compared with aluminum matrix alloy at lower as well as at increased sliding distance under dry condition. Field emission scanning electron microscope (FESEM) of worn surfaces for both silicon carbide aluminum metal matrix composites and aluminum matrix alloys have also been done.
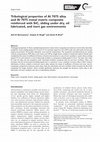
Proceedings of the Institution of Mechanical Engineers, Part J: Journal of Engineering Tribology, 2017
Tribological properties of silicon carbide-based aluminum metal matrix composite and aluminum mat... more Tribological properties of silicon carbide-based aluminum metal matrix composite and aluminum matrix alloy have been studied for various sliding speeds of 3.14 and 3.77 m/s and load range from 10 to 30 N under dry, lubricated, and inert gas (argon) environment. Pin-on-disk tribometer were used for experiments. The composite was fabricated by stir casting route by using aluminum 7075 alloy as the matrix and 10% by weight silicon carbide as reinforced material. Results have revealed that the value of coefficient of friction is found to be maximum in case of inert condition in matrix alloy at sliding speed 3.77 m/s and minimum in case of lubricated condition in composite at sliding speed 3.14 m/s. The wear rate is least for both the alloy and the composite under lubricated condition compared with dry and inert condition. Wear rate increases with the normal load and sliding speed and it is maximum in inert condition of matrix alloy at 30 N. Uniform distribution of silicon carbide in alu...
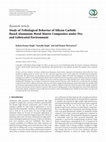
Advances in Materials Science and Engineering, 2016
Friction and wear behavior of silicon carbide based aluminum metal matrix composite and aluminum ... more Friction and wear behavior of silicon carbide based aluminum metal matrix composite and aluminum matrix alloy have been studied for sliding speeds of 3.14 m/s and 3.77 m/s and load range from 10 N to 30 N under dry and lubricated environment, respectively. The experiments were performed on pin on disk tribometer (Make: DUCOM). The composite was fabricated by stir casting process and has several challenges like inferior bonds and interfacial reaction products which will deteriorate the mechanical and tribological properties. Therefore, addition of reactive metal like magnesium (Mg) should be done which will lead to reduced solidification shrinkage, lower tendency towards hot tearing, and faster process cycles. Results have revealed that the developed composites have lower coefficient of friction and wear rates when compared with aluminum matrix alloy under dry and lubricated environment. Experimental results show that under dry condition coefficient of friction of both the matrix all...
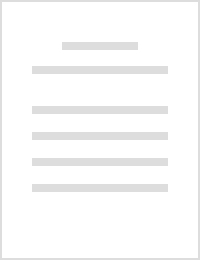
Materials Today: Proceedings, 2021
Now a Days breakthrough technology for eco-friendly materials products is developed (in orthopedi... more Now a Days breakthrough technology for eco-friendly materials products is developed (in orthopedic use as the substrate for implantation of bone), magnesium alloys, because of its suitable strength similar to bone tissue and high compatibility of magnesium and its alloys. Throughout the elevated chloride atmosphere of the physiologic system and the physiological pH(7.4–7.6), pure magnesium will easily corrode. A possible solution to this challenge can be either surface treatment via various methods or alloying of element additions or by the generation of metal matrix composites. The bio-material which is magnesium-based composites can provide resistance against corrosion and adaptable mechanical properties such as elastic modulus, ductility, tensile strength, or combination of these properties and it is the main choice to select magnesium metal matrix composites as opposed to surface treatment methods and alloying of material inclusion. The reinforcing processes are mainly focused o...
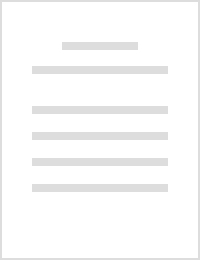
Materials Today: Proceedings, 2020
Abstract For automotive manufacturers, the current scenario is to boost reliability and component... more Abstract For automotive manufacturers, the current scenario is to boost reliability and component performance along with increasing fuel efficiency and the cost of manufacturing. The inquiry is, therefore, being carried out into the use of substitute materials in the development component, increasing the strength-to-weight ratio. The best alternative materials until now were composite materials. This study includes traditional steel helical compression spring and then contrasted with composites used in the development of helical compression spring. The helical compression spring of TATA INDICA VISTA is used for analysis and the helical compression spring load is taken as 4544.3 N. The composite material is EGlass/Epoxy and Carbon/Epoxy. In modeling the helical compression spring, solid works 2013 are used and commercial Ansys 14.5 is used for static and modal analysis. The study shows that the natural frequency produced in the helical compression spring of the composite material is reduced in transverse mode, but increases in both compression and torsional mode.
Materials Today: Proceedings, 2020
Abstract The present research study is oriented with the fabrication of tubular furnace for labor... more Abstract The present research study is oriented with the fabrication of tubular furnace for laboratory uses. The furnace is developed for the sintering/heat treatment of metals/alloys. It is 3 kg capacity with a power rating of 2500 W. The case of the furnace is made by a mild steel sheet and tube by silica in the center of the case horizontally. The tube is pasted with plaster of Paris to make grooves to fix the heating element and the internal volume is filled with glass wool to provide refractoriness between the heating element and mild steel case. It is designed for 1200 °C on an automatic PID control panel and achieved 1121 °C. This project is carried out to enhance the laboratory facility for sintering and heat treatment purposes at very low prices.
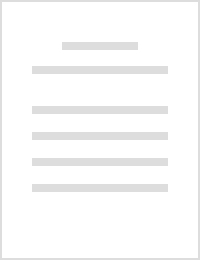
Materials Today: Proceedings, 2020
Abstract The experimental investigation explores the sintering behavior of ferritic (434L) stainl... more Abstract The experimental investigation explores the sintering behavior of ferritic (434L) stainless steel in reducing (H2) atmosphere. Yttria alumina garnet (YAG) and silicon carbide (SiC) were added up to 10 wt.% and 1 wt.% respectively in ferritic (434L) stainless steel. Solid-state and supersolidus liquid-phase sintering (SLPS) has been carried out at 1100 °C and 1300 °C respectively. The effect on the microstructural evolution of sintering and YAG, SiC addition in supersolidus liquid phase sintered samples, is compared with that obtained through solid-state sintering. The density and mechanical properties such as hardness, ultimate tensile strength, yield strength, and elongation have been observed. Through the supersolidus route, the density was higher than that of solid-state-sintered samples. L051 samples showed much higher hardness, ultimate tensile strength, yield strength and elongation compared to the L000, L031 and L101 stainless steel in both supersolidus and solid-state conditions.

Proceedings of International Conference in Mechanical and Energy Technology, 2020
In today's competitive environment (static and dynamic), for achieving the business excellence, c... more In today's competitive environment (static and dynamic), for achieving the business excellence, companies want to implement new and/or modified marketing strategies continuously. Improved features with good-quality products or services result in improving satisfaction in the customer's mind. The guidelines provided in ISO 9000 are ultimate tool to achieve the above-mentioned objective by any organization. Although several multidisciplinary approaches have been proposed to offer quality products as per customer's expectations or demands, total quality management (TQM) is a systematic management instrument that synchronizes the resources and staff in order to accomplish higher product standards, maintaining companies and customer's prospects. This paper reviews and relates the important parameters like ISO 9000, product quality and customers' satisfaction in TQM.
Uploads
Papers by Anil Kumar Shrivastava