Papers by Alexander Brosius
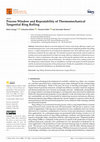
Journal of Manufacturing and Materials Processing
International objectives towards improved resource and energy efficiency require new manufacturin... more International objectives towards improved resource and energy efficiency require new manufacturing processes, such as the proposed thermomechanical tangential profiled ring rolling process. A rapid cooling-down for microstructural adjustment and a final calibration step via cold forming are combined into one single step. The reduction of process steps and the reduced number of heating cycles present opportunities for improved energy efficiency compared to traditional processes. Based on a series of experiments, this paper aims at showing the potential of this new process in terms of obtainable hardness and microstructure. The influence of the active cooling system and the rolling feed is demonstrated. They are identified as essential with regard to both the geometry and the microstructural properties of the produced part. Finally, the repeatability of the process is analyzed, and potential disturbances are identified and ranked.
The 28th Saxon Conference on Forming Technology SFU and the 7th International Conference on Accuracy in Forming Technology ICAFT
This article is an open access article distributed under the terms and conditions of the Creative... more This article is an open access article distributed under the terms and conditions of the Creative Commons Attribution (CC BY
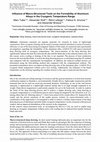
Key Engineering Materials
Aluminum materials are popular materials for research in terms of lightweight construction. How c... more Aluminum materials are popular materials for research in terms of lightweight construction. How cryogenic forming can be used to increase material utilization in terms of resource efficiency is one of the areas being investigated. Subject of this study are numerical and experimental investigations regarding the formability of the aluminum alloy AA6014-T4 with macro-structured deep drawing tools at cryogenic temperatures. The macro-structure of the deep drawing dies significantly reduces the heat flux between the dies and the blank due to the reduced contact area. For this reason, active cooling or heating of the dies is not required. The process of heat conduction between the tool and the blank, as well as the deep drawing process, is calculated using the FE-method and compared with the experimental investigations. In addition, the induced residual stresses are determined using the hole-drilling method and compared with the computational solution. The presented examination shows an ...

Key Engineering Materials
Clinching is a cost efficient method for joining components in series production. To assure the c... more Clinching is a cost efficient method for joining components in series production. To assure the clinch point’s quality, the force displacement curve during clinching or the bottom thickness are monitored. The most significant geometrical characteristics of the clinch point, neck thickness and undercut, are usually tested destructively by microsectioning. However, micrograph preparation goes ahead with a resetting of elastic deformations and crack-closing after unloading. To generate a comprehensive knowledge of the clinch point’s inner geometry under load, in-situ computed tomography (CT) and acoustic testing (TDA) can be combined. While the TDA is highly sensitive to the inner state of the clinch point, it could detect critical events like crack development during loading. If such events are indicated, the loading process is stopped and a stepped in-situ CT of the following crack and deformation development is performed. In this paper, the concept is applied to the process of clinc...
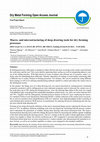
In forming processes, lubrication is needed to reduce friction and wear occurring at the contact ... more In forming processes, lubrication is needed to reduce friction and wear occurring at the contact areas between the work-piece and the tool. This is provided by separating these surfaces as well as transporting abrasive wear out of the sliding interface. With high interest in waste avoidance and efficient use of resources, today's industry aims for substituting these lubricants. Thereby, deposition of coatings or local surface structuring offer a different way to reduce friction in forming processes. For instance, this can be reached by using different hard coatings as well as by utilizing manufacturing methods capable to control and reduce the contact area in the tribological system. In this project, the flange area of a deep drawing tool was macro-structured by turning-process (rotational symmetric geometry) and by milling-process (non rotational-symmetric part) to decrease the contact area of the work-piece up to 94% during the forming process. Also, the drawing edge radius of...
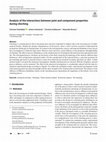
Production Engineering, 2022
Clinching is a joining process that is becoming more and more important in industry due to the in... more Clinching is a joining process that is becoming more and more important in industry due to the increasing use of multi-material designs. Despite the already widespread use of the process, there is still a need for research to understand the mechanisms and design of clinched joints. In contrast to the tool parameters, process and material disturbances have not yet been investigated to a relatively large extent. However, these also have a great influence on the properties and applicability of clinching. The effect of process disturbances on the clinched joint are investigated with numerical and experimental methods. The investigated process variations are the history of the sheets using the pre-hardening of the material, different sheet thicknesses, sheet arrangements and punch strokes. For the consideration of the material history, a specimen geometry for pre-stretching specimens in uniaxial tension is used, from which the pre-stretched secondary specimens are taken. A finite element...
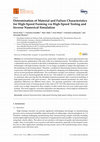
Journal of Manufacturing and Materials Processing, 2020
In conventional forming processes, quasi-static conditions are a good approximation and numerical... more In conventional forming processes, quasi-static conditions are a good approximation and numerical process optimization is the state of the art in industrial practice. Nevertheless, there is still a substantial need for research in the field of identification of material parameters. In production technologies with high forming velocities, it is no longer acceptable to neglect the dependency of the hardening on the forming speed. Therefore, a method for determining material characteristics in processes with high forming speeds was developed by designing and implementing a test setup and an inverse parameter identification. Two acceleration concepts were realized: a pneumatically driven one and an electromagnetically driven one. The method was verified for a mild steel and an aluminum alloy proving that the identified material parameters allow numerical modeling of high-speed processes with good accuracy. The determined material parameters for steel show significant differences for dif...
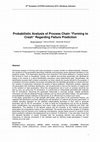
Numerical analysis of forming and crash processes is usually carried out deterministically. Howev... more Numerical analysis of forming and crash processes is usually carried out deterministically. However, the variations of the parameters describing materials and processes cause significant deviations in the prediction quality. This observation becomes more important if the failure prediction in process chains like forming to crash is considered. Usually, the material and process parameters are identified by means of an inverse or a direct identification procedure using experimental data. Nevertheless, the identification process itself contains uncertainty, as mean values are usually utilized for this purpose. It is therefore not known whether the process simulated with the identified parameters is robust and how the variation of parameters influences the quality of failure prediction. Stochastic analysis, replacing the parameters with stochastic distributions, can be performed to find out the variation of outputs due to the variation of input parameters. Since the computational cost o...
To avoid typical problems when connecting different metallic materials as aluminum and titanium a... more To avoid typical problems when connecting different metallic materials as aluminum and titanium as e.g. the formation of intermetallic phases, electromagnetic welding represents an alternative technology to conventional (i.e. usually thermal) joining processes. Although feasibility and potential of this technique are already proved, the fundamental correlations of partand process-parameters have not yet been investigated systematically. As an approach to examine these, the performance of model experiments and supplementary technological tests is suggested. The resulting connection quality is evaluated using metallographic methods.
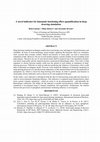
Deep drawing simulation techniques reduce tool design costs and improve tool performance and reli... more Deep drawing simulation techniques reduce tool design costs and improve tool performance and reliability. In terms of strain hardening, mixed models capturing the kinematic effect are sometimes more accurate than isotropic models. Indeed, nonlinearity in strain paths can lead to inconsistent simulation results. However, the use of such models requires a greater number of tests including strain path changes. Therefore, the use of such mixed models shall be required only if the simulation includes non-linear strain paths and the material exhibits a pronounced Bauschinger effect. New tools to help engineers choose between models could ease the spread of more advanced models in simulation of deep drawing processes when needed. With this in mind, an indicator predicting the influence of kinematic effects could help to select an adequate model. In this study, a new indicator is introduced with the idea of characterising strain path non-linearity in order to assess kinematic hardening influence...
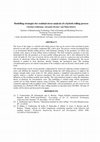
The focus of this paper is a hybrid cold rolling process that can be used to form mechanical join... more The focus of this paper is a hybrid cold rolling process that can be used to form mechanical joints between an axle and a secondary component like a drive gear. The process variant investigated here is an incremental flexible rolling process with kinematic forming of the geometry [1] which also includes some aspects of deep rolling surface treatments. The final workpiece geometry is not only determined by the roll geometry as in most profile rolling processes, but is also influenced by the work roll path [2]. Two sets of actively driven work rolls are used in a transverse and axial rolling process to selectively reduce the diameter of a cylindrical workpiece. Simultaneously, the excess material is pushed in axial direction, thereby forming the mechanical joint. The resulting circumferential groves are natural weak points of the workpiece and can become critical under cyclic loads. This disadvantage can be at least partially compensated by selectively inducing residual compressive st...
Die Erfindung betrifft ein Verfahren zur Herstellung von Verbundwerkstucken (1), insbesondere von... more Die Erfindung betrifft ein Verfahren zur Herstellung von Verbundwerkstucken (1), insbesondere von Blechverbundwerkstucken, bei dem das Verbundwerkstuck (1) aus einer geschichteten Anordnung von mindestens zwei Materialschichten (2, 3) besteht, zwischen denen Verstarkungselemente (4) angeordnet sind. Hierbei werden zur Verstarkung des Verbundwerkstuckes (1) aus strangformigen Verstarkungselementen gebildete Verstarkungsstrukturen (4) zwischen mindestens zwei aneinander grenzende Materialschichten (2, 3) eingebracht und anschliesend wird zumindest eine der Materialschichten (2, 3) umgeformt. Ebenfalls wird ein entsprechendes Verbundwerkstuck (1) beschrieben.
Production Engineering, 2021
Thermomechanical ring rolling is an evolution of the process where deformation and heat treatment... more Thermomechanical ring rolling is an evolution of the process where deformation and heat treatment are combined to obtain a product with both the desired geometry and hardness or microstructure in a single step. However, the high sensitivity of the process to the initial condition and to various disturbances limits its repeatability and accuracy. In this paper, the authors implement a concept for hardness control of ring rolling in virtual experiments. A concept based on soft sensors and model predictive control is implemented on a digital twin. The operation of the different models needed for this control loop are detailed and the controller itself is illustrated.
Journal of Machine Engineering, 2020
The efficient use of resources are becoming more important due to economic and environmental requ... more The efficient use of resources are becoming more important due to economic and environmental requirements. In widely used forming processes like deep drawing an avoidance of lubricantsnamely dry deep drawingis a key factor for saving resources. In this paper, a combined approach consisting of a macro-structured tool design and a special modified protective coating is presented. The combination ensures a stable process with a sufficiently wide process window under dry conditions. The absence of lubricants in critical areas has to be compensated by tetrahedral amorphous carbon ta-C films which is additionally structured by Direct Laser Interference Patterning (DLIP) for further improvement of the tribological performance.
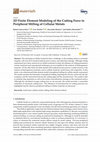
Materials, 2020
The machining of cellular metals has been a challenge, as the resulting surface is extremely irre... more The machining of cellular metals has been a challenge, as the resulting surface is extremely irregular, with torn off or smeared material, poor accuracy, and subsurface damage. Although cutting experiments have been carried out on cellular materials to study the influence of cutting parameters, current analytical and experimental techniques are not suitable for the analysis of heterogeneous materials. On the other hand, the finite element (FE) method has been proven a useful resource in the analysis of heterogeneous materials, such as cellular materials, metal foams, and composites. In this study, a two-dimensional finite element model of peripheral milling for cellular metals is presented. The model considers the kinematics of peripheral milling, depicting the advance of the tool into the workpiece and the interaction between the cutting edge and the mesostructure. The model is able to simulate chip separation as well as the surface and subsurface damage on the machined surface. Al...
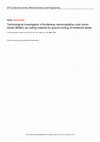
IOP Conference Series: Materials Science and Engineering, 2019
By using a high-pressure/high-temperature process (HP/HT), it is possible to synthesise new ultra... more By using a high-pressure/high-temperature process (HP/HT), it is possible to synthesise new ultra-hard cutting materials called binderless nanocrystalline cubic boron nitride (BNNC). The starting material is a pyrolytically deposited hexagonal boron nitride (pBN), which is converted at temperatures of 1400 °C – 2200 °C and pressures of 10 - 20 GPa in a direct synthesis without any binding material. The average crystallite size of this material is 50 - 100 nm and is thus significantly smaller than conventional polycrystalline cubic boron nitride (PCBN) cutting materials. Compared to conventional PCBN cutting materials, this material has an increased hardness, hot hardness and better temperature resistance. This provides an excellent alternative to extend the process limits for the machining of hardened steels and superalloys. In this conference paper, the first technological results for groove turning in hardened steels with this new promising cutting material will be presented.
AIP Conference Proceedings, 2007
Within the scope of this article a decoupling algorithm to reduce computing time in Finite Elemen... more Within the scope of this article a decoupling algorithm to reduce computing time in Finite Element Analyses of incremental forming processes will be investigated. Based on the given position of the small forming zone, the presented algorithm aims at separating a Finite ...
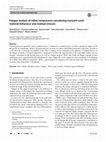
Production Engineering, 2018
Forming processes generally lead to residual stresses. Compressive residual stresses can have a b... more Forming processes generally lead to residual stresses. Compressive residual stresses can have a beneficial impact on the fatigue life of components, which is demonstrated here in terms of a skew-rolled hybrid shaft-hub connection. In order to set the basis for a systematic investigation of this effect, a strategy for the evaluation of the influence of residual stresses on the fatigue resistance of formed components is proposed. It involves the determination of the expectable residual stresses through a simulation of the forming process as well as a fatigue analysis. While state-of-the-art fatigue concepts assume unchanging cyclic material behaviour throughout the entire fatigue life of the component, this assumption is not adequate for residual stress-afflicted components. Hence, a generalization to transient cyclic material behaviour with an asymmetry in tension and compression is introduced.
MATEC Web of Conferences, 2016
This paper presents a new parameter identification scheme for complex yield criteria of sheet met... more This paper presents a new parameter identification scheme for complex yield criteria of sheet metals using experimentally determined load and strain distributions and combining analytical stress analysis on sectional strain data with common inverse analysis. The approach is suitable for specimen with a non-homogenous strain distribution in the specimen and reduces computing time compared to common methods like iteratively updated FEM considerably. It serves to identify a set of material parameters in a fast and precise manner, describing the material behaviour.
Uploads
Papers by Alexander Brosius