Papers by Alessandro Daga
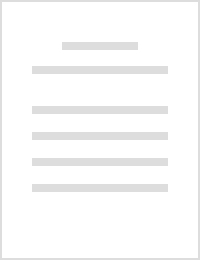
Accelerometric measurements from the rolling bearing test rig of the Dynamic and Identification R... more Accelerometric measurements from the rolling bearing test rig of the Dynamic and Identification Research Group (DIRG), Department of Mechanical and Aerospace Engineering, Politecnico di Torino. Goals: • Vibration Monitoring, Bearing Diagnostics, Damage detection, Damage localization, Damage classification, Damage assessment. Features: • high-speed spindle driving a hollow shaft supported by a couple of identical roller bearings B1 and B3. B1 is the bearing under analysis and features various damages. • two damage types (indentations on a roller and on the inner ring) and severities (0, 150, 250, 450 µm). • a central, larger roller bearing (B2) is loaded through a sledge generating a controlled radial force measured by a load cell. • lubrication is obtained by oil injection into the hollow shaft. • a K-type thermocouple is used to monitor the temperature (manually recorded). • two triaxial accelerometers are mounted on the supports of bearings B1 and B2. Dataset: • stationary acquisitions at different speed & load combinations (speed: 0, 100, 200, 300, 400, 500 Hz; load: 0, 1000, 1400, 1800 N). • endurance acquisitions of the bearing featuring the 450µm roller indentation. Monitoring of the damage evolution for about 230 hours under the same speed and load condition. The extended description of the dataset can be found in the attached pdf "Description and analysis of open access data" or in: A.P. Daga, A. Fasana, S. Marchesiello, L. Garibaldi, The Politecnico di Torino rolling bearing test rig: Description and analysis of open access data, Mechanical Systems and Signal Processing 120 (2019) 252–273. doi:10.1016/j.ymssp.2018.10.010.
Mechanical Systems and Signal Processing, May 1, 2023
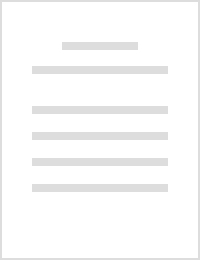
Mechanical Systems and Signal Processing, Apr 1, 2019
Abstract Nowadays, machines-diagnostics via vibration monitoring is rising an always growing inte... more Abstract Nowadays, machines-diagnostics via vibration monitoring is rising an always growing interest thanks to the huge and accurate amount of health information which could be extracted by the raw data coming from accelerometers. Damage severity, type and location of a fault are the kind of information which are buried in the time records. The scope of this paper is double: first, to present the huge amount of data which have been acquired on the rolling bearing test rig of the Dynamic and Identification Research Group (DIRG), in the Department of Mechanical and Aerospace Engineering at Politecnico di Torino and to share them with the scientific community; secondly, to present a statistical approach analysis and its performances as example of a simple technique to be fruitfully adopted for comparison. To this goal, a detailed presentation of the test rig is given, which comprehends different working conditions up to 30,000 rpm, damage types and levels, various sensors positions and directions as well as an endurance test. The related time records can be downloaded from ftp://ftp.polito.it/people/DIRG_BearingData/ . Afterword, tried-and-tested statistical tools are exploited to learn the information about bearing damages from this massive amounts of data. This “data mining” will be performed using inferential statistical techniques as analysis of variance (ANOVA), applied on usual statistical features, which characterize of the signal. A linear discriminant analysis (LDA) in the configuration proposed by Fisher will be also used to see if the data were classifiable in a multidimensional space with this basic algorithm. Finally, an Outlier Analysis based on Mahalanobis distance will be formulated, so as to distinguish a damage condition from the healthy state (training data), compensating when possible for environmental (temperature) and operational (speed and load) variations.
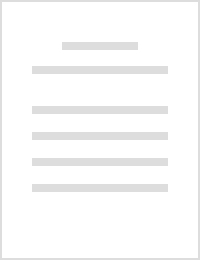
Volume 9: Mechanics of Solids, Structures, and Fluids; Micro- and Nano-Systems Engineering and Packaging; Safety Engineering, Risk, and Reliability Analysis; Research Posters, Oct 30, 2022
In recent years, Artificial Intelligence (AI) is ever more exploited in all the scientific and in... more In recent years, Artificial Intelligence (AI) is ever more exploited in all the scientific and industrial fields and is allowing significant developments in mechanical engineering too. An emblematic contribution was given in terms of safety and reliability since Machine Learning (ML) techniques permitted the monitoring and the prediction of the state of health of machinery, allowing the adoption of predictive maintenance strategies. In fact, data-driven models — based on acquisitions — attract considerable interest both thanks to its theoretical and application development. The evolution of diagnostic techniques is oriented towards Condition-Based Maintenance (CBM) strategies, thus allowing improvements in terms of safety enhancement, cost reduction and increased performances. This paper proposes the development and implementation of a diagnostic/prognostic tool applied to an automated books trimmer industrial machine, implementing condition monitoring by means of accelerometers which can be integrated into a Supervisory Control And Data Acquisition (SCADA) system. Given its use, the core components of this production line are three knives, subjected to significant impulsive forces. Therefore, the target of the work is to infer the wear of these three knives, as they are critical elements of the machinery and have a high impact on the quality of the final product. The project was carried out in collaboration with Tecnau — an industry-leading company — which made it possible to conduct experimentation and data acquisition on their machinery. An appropriate Design Of Experiments (DOE) and the use of inferential statistical techniques — such as the ANalysis Of VAriance (ANOVA) and the identification of significant effects — applied to the multivariate dataset allowed recognizing the most relevant features for Novelty Detection (ND). Both the Linear Discriminant Analysis (LDA) and the k-Nearest Neighbors (kNN) method permitted to correctly distinguish the patterns representing the health conditions of the machinery, classifying the data in the reduced multidimensional space according to the final product quality. The results obtained in terms of accuracy are very positive and promising. This means that the developed method is able to successfully identify the state of health of the blade in spite of varying functioning parameters (book thickness and size, paper type and characteristics) and operating conditions. The algorithm speed and its integration into the industrial line make a real-time condition-based maintenance strategy possible. This diagnostic method is suitable for applications oriented to the paradigm of Industry 4.0 and the digitalization of the industrial sector, which can be integrated with the Internet of Things (IoT) and cloud systems.
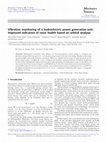
Mechanics & Industry, 2022
Hydropower generation units (HGUs) are electromechanical systems meant to transform the potential... more Hydropower generation units (HGUs) are electromechanical systems meant to transform the potential energy of flowing water (i.e., a renewable energy source) into electrical energy. Thanks to their high manoeuvrability and green footprint, nowadays, HGUs are mission-critical assets for grid operators, as the global energy policy is pushing for a more ecological and healthier energy production. Condition monitoring becomes then a fundamental task for fostering safety while optimizing the maintenance regime of such HGUs. In this regard, this work is meant to improve an ISO20816-based vibration monitoring system by proposing further rotor health indicators based on orbital analysis. The proposed improvement is implemented on a real HGU of the Signayes hydroelectric power plant from C.V.A. S.p.A. À Compagnia Valdostana delle Acque À Compagnie Valdôtaine des Eaux.
Applied sciences, Jul 6, 2021
This article is an open access article distributed under the terms and conditions of the Creative... more This article is an open access article distributed under the terms and conditions of the Creative Commons Attribution (CC BY
International Journal of Impact Engineering, Oct 1, 2023
Springer eBooks, Jun 22, 2022
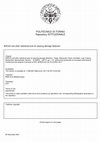
The aim of the paper is to exhaustively exploit and test some statistical tools, such as ANOVA an... more The aim of the paper is to exhaustively exploit and test some statistical tools, such as ANOVA and Linear Discriminant Analysis, to investigate a massive amounts of data collected over a rig available @DIRG Lab, specifically conceived to test high speed aeronautical bearings; the rig permits the control of rotational speed (6000-30000 RPM), radial load (0 to 1800 N) and temperature, and allows monitoring vibrations by means of 4 tri-axial accelerometers. Fifteen different damages have been realised on the bearing but, for simplicity, this papers only treats those cases where simple identification methods have failed or not demonstrated to be fully affordable. The damages have been inferred on rolls or on the internal ring, with different severities, which are reported as a function of their extension, i.e. 150, 250, 450 μm. A total number of 17 combinations of load and speed have been analysed per each damaged bearing. Although ANOVA rigorously applies when some conditions are respected on the probability distribution of the responses, such as Independence of observations, Normality (normal distribution of the residuals) and Homoscedasticity (homogeneity of variances-equal variances), the paper exploits the robustness of the technique even when data do not fully fall into the requisites. Analyses are focused on the best features to be taken into account, trying to seek for the most informative, but also trying to extract a "best choice" for the acceleration direction and the most informative point to be monitored over the simple structure. Wanting to focus on the classification of the single observation, Linear Discriminant Analysis has been tested, demonstrating to be quite effective as the number of misclassification is not very high, (at least considering the widest damages). All these classifications have unfortunately the limit of requiring labelled examples. Acquisitions in undamaged and damaged conditions are in fact essential to guarantee their applicability, which is quite often impossible for real industrial plants. The target can be anyway reached by adopting distances from undamaged conditions which, conversely, must be known as a reference. Advantages of the statistical methods are quickness, simplicity and full independence from human interaction.
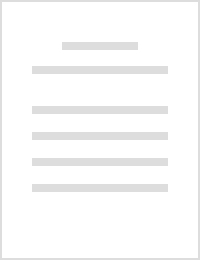
The Dynamics & Identification Research Group at POLITO has been involved in the challenge of ... more The Dynamics & Identification Research Group at POLITO has been involved in the challenge of bearing damage identification for aero-engines for more than ten years. The role of gearboxes in future aircraft scenario is well focused by the Horizon 2020 - Green Engine program, where some important issues are addressed. One is surely the future of fan propeller engines, where the entire engine powers is flowing through the gearbox as for the case of helicopters. This is a real challenge for early diagnostic techniques both for gears and bearings. In this frame, the DIRG has developed and tested a huge number of algorithms seeking for the ―best performances‖ on real application; this statement must be interpreted as a trade-off among many factors such as: the limited number of sensors, the missing direct torque measure, the short time allowed for real time analysis, the decisional path compromise, the number of false and missed alarms, and so on. Some of these methods are quite ancient (RMS, Kurtosis, Skewness, Crest, and similar evolutions such as FM0 - NA4 - NA4* - FM4 -M6A - NB4) but still can be used as a reference to check how more recent techniques can improve the results and the sensibility to early damages, as well as the localisation (in spite of longer elaboration time). Among the new methods, EMD / EEMD [1], SK [3], Stochastic Resonance [2] and Principal Component Analysis (PCA) [4] are compared in the paper in terms of detection capability but also location identification, minimum number of sensors, false alarms and so on. In practice, however, it should be borne in mind that most of these methods are usually employed in sequence or parallel, so that a meaningful comparison cannot be done and, in this case, it would generate a huge number of combination sets. The elaboration time is also considered as one of the parameters toward its adoptability along the paper.
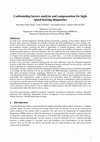
HAL (Le Centre pour la Communication Scientifique Directe), Jul 8, 2019
In recent years, machine diagnostics through vibration monitoring is gaining a rising interest. I... more In recent years, machine diagnostics through vibration monitoring is gaining a rising interest. Indeed, in the literature many advanced techniques are available to disclose the fault establishment as well as damage type, location and severity. Unfortunately, in general, these high-level algorithms are not robust to operational and environmental variables, restricting the field of applicability of machine diagnostics. Most of industrial machines in fact, work with variable loads, at variable speeds and in uncontrolled environments, so that the finally measured signals are often non-stationary. The very common time-series features based on statistical moments (such as root mean square, skewness, kurtosis, peak value and crest factor) undergo variations related to changes in the machine operational parameters (e.g. speed, load, …) or in the environmental parameters (e.g. temperature, humidity, …), which can be seen as non-measured, and then latent, confounding factors with respect to the health information of interest. In order to face such issue, statistical techniques like (in a first exploratory stage) the Principal Component Analysis, or the Factor Analysis, are available. The pursuit of features insensitive to these factors, can be also tackled exploiting the cointegration property of non-stationary signals. In this paper, the most common methods for reducing the influence of latent factors are considered, and applied to investigate the data collected over the rig available at the DIRG laboratory, specifically conceived to test high speed aeronautical bearings monitoring vibrations by means of 2 tri-axial accelerometers while controlling the rotational speed (0-30000 RPM), the radial load (0 to 1800 N) and recording the lubricant oil temperature. The compensation scheme is based on two procedures which are established in univariate analyses, but not so well documented in multivariate cases: the removal of deterministic trends by subtraction of a regression, and the removal of stochastic trends in difference stationary series by subtraction of the onestep ahead prediction from an autoregressive model. The extension of these methods to the multivariate case is here analysed to find an effective way of enhancing damage patterns when the masking effect due to the non-stationarities induced by latent factors is strong.
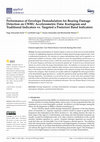
Applied Sciences
Envelope demodulation of vibration signals is surely one of the most successful methods of analys... more Envelope demodulation of vibration signals is surely one of the most successful methods of analysis for highlighting diagnostic information of rolling element bearings incipient faults. From a mathematical perspective, the selection of a proper demodulation band can be regarded as an optimization problem involving a utility function to assess the demodulation performance in a particular band and a scheme to move within the search space of all the possible frequency bands {f, Δf} (center frequency and band size) towards the optimal one. In most of cases, kurtosis-based indices are used to select the proper demodulation band. Nevertheless, to overcome the lack of robustness to non-Gaussian noise, different utility functions can be found in the literature. One of these is the kurtosis of the unbiased autocorrelation of the squared envelope of the filtered signal found in the autogram. These heuristics are usually sufficient to highlight the defect spectral lines in the demodulated sign...
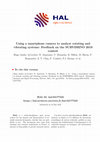
Mechanical Systems and Signal Processing, 2021
A smartphone is a low-cost pocket wireless multichannel multiphysical data acquisition system: th... more A smartphone is a low-cost pocket wireless multichannel multiphysical data acquisition system: the use of such a device for noise and vibration analysis is a challenging task. To what extent is it possible to carry out relevant analysis from it? The Survishno conference, held in Lyon in July 2019, proposed a contest to participants based on this subject. Two challenges were proposed, wherein each a mute video showing an object moving/excited at different frequencies was provided. Due to the frequencies set and the video sampling characteristics, special effects occurred and are visible on both videos. From the first video, participants were asked to estimate the Instantaneous Angular Speed (IAS) of a rotating fan. From the second video, they were asked to perform the modal analysis of a cantilever beam. This paper gathers the interesting ideas proposed by the contestants and proposes a global method to solve these two problems. One major point of the paper might be the advantageous use of the rolling shutter effect, a well-known artefact of smartphone videos, to perform advanced mechanical analyses: the consideration of the unavoidable slight phase shift between the acquisition of each pixel opens up the possibility to perform a dynamic analysis at frequencies that are much higher than the video frame rate.
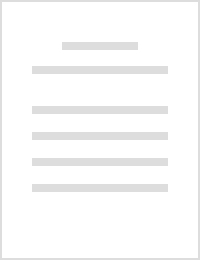
Condition monitoring of gear-based mechanical systems undergoing non-stationary operation conditi... more Condition monitoring of gear-based mechanical systems undergoing non-stationary operation conditions is in general very challenging. In particular, this issue is remarkable as regards wind energy technology because most of the modern wind turbines are geared and gearbox damages account for at least the 20% of their unavailability time. In this work, a new method for the diagnosis of gearbox damages is proposed: the main idea is that vibrations are measured at the tower, instead that at the gearbox. This implies that measurements can be performed without impacting on the wind turbine operation, as desirable by the point of view of wind turbine practitioners. A test case study is discussed: it deals with a wind farm owned by Renvico, featuring 6 wind turbines with 2 MW of rated power each. The vibration measurements at a wind turbine suspected to be damaged and at reference wind turbines are processed through a multivariate Novelty Detection algorithm in the feature space. The applica...
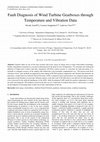
International Journal of Renewable Energy Research, 2017
Gearbox faults are one of the most common and severe causes of energy losses in large wind turbin... more Gearbox faults are one of the most common and severe causes of energy losses in large wind turbine technology. Further, degradation of gearboxes is an elusive phenomenon by the point of view of diagnostics. Yet, nowadays the widespread diffusion of Supervisory Control And Data Acquisition (SCADA) control systems is a keystone for fault prevention. It is desirable to conjugate accuracy of the outputs with intuitiveness and reasonable computational cost. The present work deals with these issues: some methods are proposed for data mining of SCADA gearbox temperature and vibration measurements. In particular, a model based on Artificial Neural Networks (ANN) is proposed and its performances are compared against similar approaches in the literature. It arises that vibration analysis at the time scale of SCADA data isn’t effective for fault diagnosis, even if powered by the artificial intelligence of the ANN, while the proposed ANN model for gearbox temperatures is useful for early faul...
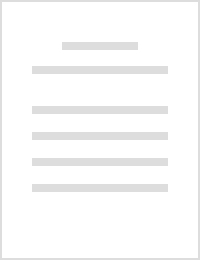
IEEE Transactions on Instrumentation and Measurement, 2021
Large-scale centrifugal compressor is an essential fluid machinery in modern industry. The blades... more Large-scale centrifugal compressor is an essential fluid machinery in modern industry. The blades, a critical part of compressors, always work under severe and harsh conditions and are prone to fatigue failure. Thus, a suitable monitoring technique is necessary to guarantee reliable operation of blades in the long-term. One promising, noncontact, online, technique, is the blade tip-timing (BTT) which is able to recover the vibration characteristics of all the blades simultaneously. However, improvements are still necessary to ensure the accuracy and reliability of the BTT technique for vibration monitoring of large-scale centrifugal compressors. In this article, the resolution error induced by the finite, discrete sampling is studied first. Then, the experimental random errors brought by nonstationary operating conditions are analyzed in detail and the error introduced by the compensation of the geometrical imperfection of the blades is also taken into account. An improved technique is proposed to reduce such random errors by substituting the real key-phase signal with reconstruction by means of the tip-timing signal. Experiment on a centrifugal compressor test-rig with a cracked blade is conducted to verify the effectiveness of the improved technique. Finally, a dynamic model is built to support the experimental result. This work demonstrates the reliability of the improved BTT technique for blade condition monitoring and fault warning of large-scale centrifugal compressors.
Mechanical Systems and Signal Processing, 2017
The contest dealt with the diagnosis of a civil aircraft engine based on vibration data measured ... more The contest dealt with the diagnosis of a civil aircraft engine based on vibration data measured in a transient operating mode and provided by Safran. Based on two independent exercises, the contest offered the possibility to benchmark current diagnostic methods on real data supplemented with several challenges. Outcomes of seven competing teams are reported and discussed. The object of the paper is twofold. It first aims at giving a picture of the current state-of-the-art in vibration-based diagnosis of rolling-element bearings in nonstationary operating conditions. Second, it aims at providing the scientific community with a benchmark and some baseline solutions. In this respect, the data used in the contest are made available as supplementary material.
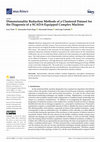
Machines
Machinery diagnostics in the industrial field have assumed a fundamental role for both technical,... more Machinery diagnostics in the industrial field have assumed a fundamental role for both technical, economic and safety reasons. The use of sensors, data collection and analysis has increasingly advanced to investigate the health of machinery, predict the presence of faults and recognize their nature. The amount of data necessary for this purpose means that it is often necessary to implement dimension reduction methods to pre-process the useful features for the classification. Furthermore, the use of a multi-class dataset could involve data clustering in its multi-dimensional space. This study proposes a novel dimensionality reduction method, consisting of the combination of two different techniques. It aims at improving the quality of the features and, consequently, the classification performance with high-dimension clustered datasets. In addition, a case study is analyzed thanks to the data published by the Prognostics and Health Management Europe (PHME) society on the Data Challeng...
Uploads
Papers by Alessandro Daga