Shock mount: Difference between revisions
m Add additional use under Mounting machinery |
m →Microphone mounts: removed duplicate "but" |
||
(48 intermediate revisions by 25 users not shown) | |||
Line 1: | Line 1: | ||
{{Short description|Device used for vibration isolation}} |
|||
[[Image:AKG Perception 120 USB condenser microphone with SH 100 shock mount.jpg|250px|right|thumb|Condenser microphone with shock mount]] |
|||
[[Image:Chassis-Plans-Transit-Case.jpg|thumb|right|250px|[[Transit case]] showing internal shock mounting]] |
|||
A '''shock mount''' or '''isolation mount''' is a mechanical [[fastener]] that connects two parts elastically to provide [[shock (mechanics)|shock]] and [[vibration isolation]]. |
|||
Isolation mounts allow equipment to be securely mounted to a foundation and/or frame and, at the same time, allow it to float independently from it. |
|||
==Design== |
|||
[[Rubber bushing]]s compress [[synthetic rubber]] rings on bolts to provide some isolation. Other shock mounts have mechanical [[spring (mechanics)|spring]]s or an [[elastomer]] (in tension or compression) engineered to isolate an item from specified [[mechanical shock]] and [[vibration]]. Some form of [[dashpot]] is usually used with a spring to provide viscous damping. [[Viscoelastic]] materials are common. Maxwell and Kelvin–Voigt models of viscoelasticity use springs and dashpots in series and parallel circuits respectively. Hydraulic and pneumatic components can be included, depending on the use.<ref> {{Citation |
|||
| inventor-last =De |
|||
| inventor-first =GRP |
|||
| inventorlink = |
|||
| inventor2-last = |
|||
| inventor2-first = |
|||
| inventorlink2 = |
|||
| publication-date =10 August 1971 |
|||
| issue-date = |
|||
| title =Air-damped shock mount |
|||
| country-code =US |
|||
| description = |
|||
| patent-number = 3598353 |
|||
| url =https://www.google.com/patents/US3598353 |
|||
| accessdate =11 Feb 2015}}</ref> |
|||
== |
== Uses == |
||
[[File:USS Arkansas (CGN-41) shock trials.jpg|thumb|Explosive shock test of naval ship; equipment on board is isolated from shocks by shock mounts]] |
|||
Shock mounts are found in a wide variety of applications. |
|||
They can be used to isolate the foundation or substrate from the dynamics of the mounted equipment. This is vital on submarines where silence is critical to mission success. Yachts also use shock mounts to dampen mechanical noise (mainly transmitted throughout the structure) and increase comfort. This is usually done through elastic supports and transmission couplings.<ref>{{Cite web|date=2018-01-13|title=Vulkan: il segreto per creare il silenzio a bordo degli yacht|url=https://www.barchemagazine.com/en/gian-piero-repetti-vulkan-italia/|access-date=2021-04-16|website=Barche Magazine ISP}}</ref> |
|||
Shock mounts for microphones can provide basic protection from damage, but their prime use is to isolate microphones from mechanically transmitted noise. This can originate as floor vibrations transmitted through a floor stand, or as "finger" and other handling noise on boom poles. All microphones behave to some extent as accelerometers, with the most sensitive axis being perpendicular to the diaphragm. Additionally, some microphones contain internal elements such as vacuum tubes and transformers which can be inherently microphonic. These are often cushioned by resilient internal methods, in addition to the employment of external isolation mounts. |
|||
Other common examples are the motor and transmission mounts used in virtually every automobile manufactured today. Without isolation mounts, interior noise and comfort levels would be significantly different. Such shock and vibration-isolation mounts are often chosen by the nature of the dynamics produced by the equipment and the weight of the equipment. |
|||
Traditionally the large side-address studio microphone has been strung in a "cat's cradle" mount, using fabric-wound rubber elastic elements to provide isolation. These designs still find some favour, although the elements tend to deteriorate, and sag with time. Newer designs, such as Rycote's "USM" lyre [4], use plastic elastomers, and patented spring shapes to reduce this problem. |
|||
Shock mounts can isolate sensitive equipment from undesirable dynamics of the foundation or substrate. Sensitive laboratory equipment most be isolated from shock from handling and ambient vibration. Military equipment and ships must be able to withstand nearby explosions. |
|||
For end-fire microphones, most often employed for location work, similar elastic stringing was once used. More recently designs moved to o-ring elements, before the Rycote Lyre [5] and Cinela Osix [6] suspensions were introduced. These use spring element designs that give far greater displacement along the microphone's prime axis, while limiting it on the other two. This enables excellent isolation while retaining good control of the microphone. |
|||
Shock mounts are found in some disc drives and [[compact disc player]]s, where the disc and rainy agreement are held by soft [[Bushing (isolator)|bushings]] that isolate them from outside vibration and other outside forces, such as torsion.<ref>{{cite patent |
|||
[4]http://www.reddingaudio.com/rycote-invision-studio.php |
|||
[5]http://www.ips.org.uk/files/11_Rycote_Lyre_Suspensions.pdf |
|||
[6]http://www.cinela.fr/catalog.php?pid=6 |
|||
==Mounting machinery== |
|||
Machinery may have flexible mounts to help control vibration and reduce noise. Automobile engines usually have flexible mounts to reduce operating noise. |
|||
Air Compressors are normally mounted on isolation mounts to protect the tank (receiver) from damage due to vibration created by the reciprocating pump. |
|||
Naval ships have special shock mounts to minimize machinery noise being transmitted to the water. The shock mounts help protect the shipboard operating equipment from the shock of explosions. |
|||
== Disc drives== |
|||
Shock mounts are found in some disc drives and [[compact disc player]]s, in which soft [[Bushing_(isolator)|bushings]] are all that mechanically hold the disk and reading assembly, thereby isolating it from outside vibrations and from other outside loads such as torsion.<ref> {{Citation |
|||
| inventor-last =Ajmani |
| inventor-last =Ajmani |
||
| inventor-first =R S |
| inventor-first =R S |
||
Line 47: | Line 23: | ||
| title =Conductive shock mount for reducing electromagnetic interference in a disk drive system |
| title =Conductive shock mount for reducing electromagnetic interference in a disk drive system |
||
| country-code =US |
| country-code =US |
||
| description = |
|||
| patent-number =5,761,031 |
| patent-number =5,761,031 |
||
| url =https://www.google.com/patents/US5761031 |
| url =https://www.google.com/patents/US5761031 |
||
}}</ref> In this case, isolation mounts are often chosen by the sensitivity of the equipment to shock (fragility) and vibration (natural frequency) and the weight of the equipment. |
|||
| accessdate = 11 Feb 2015}}</ref> |
|||
For shock mounting to be effective, the input shock and vibration must be matched. A shock pulse is characterised by its peak acceleration, duration, and shape (half sine, triangular, trapezoidal, etc.). The [[shock response spectrum]] is a method for further evaluating mechanical shock.<ref>{{Citation | title=The Shock Response Spectrum – A Primer | publisher=Society for Experimental Mechanics | volume=IMAC-XXVII | year=2009 | first1=Alexander | last1=J E | url=http://sem-proceedings.com/27i/sem.org-IMAC-XXVII-Conf-s30p002-The-Shock-Response-Spectrum-A-Primer.pdf | accessdate=9 Feb 2015 | url-status=dead | archiveurl=https://web.archive.org/web/20160304093602/http://sem-proceedings.com/27i/sem.org-IMAC-XXVII-Conf-s30p002-The-Shock-Response-Spectrum-A-Primer.pdf | archivedate=2016-03-04 }}</ref> |
|||
==Other== |
|||
[[Image:Eames LCW shock mount.jpg|250px|thumb|One of two shock mounts holding the back of the [[Eames Lounge Chair Wood]] (LCW). The black rubber is glued to the wood and the bolt only connects the metal to the rubber. There are three similar shock mounts supporting the seat.]] |
|||
Shock mounts can be found in a wide variety of applications. |
|||
Shock mounts used to isolate entire buildings from earthquakes are called [[Seismic base isolation|base isolators]]. |
|||
A similar idea, also known as a shock mount, is found in furniture design, introduced by [[Charles and Ray Eames]]. This provides some shock absorption and serves as a [[living hinge]], allowing the seat back to pivot. |
|||
[[Image:Base isolators under the Utah State Capitol.jpg|thumb|left|Base isolators under the [[Utah State Capitol]] building]] |
|||
Shock mounts are also used in bicycle seats.<ref>{{Citation |
|||
[[Image:Eames LCW shock mount.jpg|thumb|right|One of two shock mounts holding the back of the [[Eames Lounge Chair Wood]] (LCW).<br>The black rubber is glued to the wood and the bolt only connects the metal to the rubber. Three similar shock mounts support the seat.]] |
|||
| inventor-last =Taormino |
|||
A similar idea, also known as a shock mount, is found in furniture design, introduced by [[Charles and Ray Eames]]. It provides some shock absorption and operates as a [[living hinge]], allowing the seat back to pivot. |
|||
| inventor-first =J S |
|||
| inventor2-last =Caselli |
|||
Shock mounts are also sometimes used in bicycle saddles,<ref>{{cite patent |
|||
| inventor2-first = |
|||
| inventor-last =Taormino | inventor-first =J S |
|||
| inventor2-last =Caselli | inventor2-first = |
|||
| publication-date =1 Feb 2000 |
| publication-date =1 Feb 2000 |
||
| issue-date = |
| issue-date = |
||
| title =Laterally pivoting bicycle saddle mount with shock absorber |
| title =Laterally pivoting bicycle saddle mount with shock absorber |
||
| country |
| country =US |
||
| |
| number =6019422 |
||
| patent-number =6019422 |
|||
| url =https://www.google.com/patents/US6019422 |
| url =https://www.google.com/patents/US6019422 |
||
}}</ref> handlebars and chassis. |
|||
| accessdate =11 Feb 2015}}</ref> |
|||
{{Clear}} |
|||
== Design == |
|||
[[File:Isolation_Mount_-_Moulded_Rubber.jpg|thumb|Molded Rubber Shock Isolation Mount]] |
|||
Maxwell and Kelvin–Voigt models of viscoelasticity use springs and dashpots in series and parallel circuits respectively. Hydraulic and pneumatic components can be included, depending on the use.<ref>{{cite patent |
|||
| number = US3598353A |
|||
| title = Air-damped shock mount |
|||
| pubdate =1971 |
|||
| inventor =DeGrey |
|||
| url =https://patents.google.com/patent/US3598353A/en |
|||
}}</ref> |
|||
=== Laminated pads === |
|||
One common type of isolation mounts is laminated pads. Generally, these pads consist of a cork or polymeric foam core which has been laminated between two pieces of ribbed neoprene sheet. |
|||
=== Molded rubber isolation mounts === |
|||
Molded rubber isolation mounts are typically manufactured for specific applications. The best example of this is automotive engine and transmission mounts. [[Rubber bushing]]s compress [[synthetic rubber]] rings on bolts to provide some isolation – operating temperature is sometimes a factor. Other shock mounts have mechanical [[spring (mechanics)|spring]]s or an [[elastomer]] (in tension or compression) engineered to isolate an item from specified [[mechanical shock]] and [[vibration]]. Some form of [[dashpot]] is usually used with a spring to provide viscous damping. [[Viscoelastic]] materials are common. Temperature is a factor in the dynamic response of rubber. Generally, a molded rubber mount is best suited for heavy loads producing higher frequency vibrations. |
|||
[[File:Isolation_Mount_-_Coiled_Cable.jpg|thumb|Coiled Cable Mount]] |
|||
=== Cable isolation mounts === |
|||
Cable mounts are based around a coil of wire rope fixed to an upper and lower mounting bar.<ref>{{cite patent |
|||
| number = US4397069A |
|||
| title = Device and process for the manufacture of vibration-damping and shockproof mountings incorporating at least one helically arranged metal cable and mounting thereby obtained |
|||
| pubdate =1983 |
|||
| inventor =Camossi |
|||
| url =https://patents.google.com/patent/US4397069A/en |
|||
}}</ref><ref>{{cite patent |
|||
| number = US4783038A |
|||
| title =Isolator Apparatus |
|||
| pubdate =1988 |
|||
| inventor = Gilbert, LeKuch, Ferri |
|||
| url = https://patents.google.com/patent/US4783038A/en}}</ref> When properly matched to the load, these mounts provide isolation over a broad frequency range. They are typically applied to high performance applications, such as mounting sensitive instrumentation into off-road vehicles and shipboard. |
|||
{{clear right}} |
|||
=== Coil spring isolation mounts === |
|||
[[File:Isolation_Mount_-_Coil_Spring.jpg|thumb|Typical Coil Spring Isolation Mount]] |
|||
Coil spring isolation mounts generally provide the greatest degree of movement and the best low frequency performance. They are particularly popular for mounting equipment in buildings such as air handlers, filtration units, air conditioning and refrigeration systems and large pipes. Their degree of movement makes them ideal for applications where high flexure and/or expansion and contraction are a consideration. |
|||
{{Clear}} |
|||
== Microphone mounts == |
|||
[[File:AKG Perception 120 USB condenser microphone with SH 100 shock mount.jpg|thumb|left|upright|Large element [[condenser microphone]] in shock mount]] |
|||
Shock mounts for microphones can provide basic protection from damage, but their prime use is to isolate microphones from mechanically transmitted noise. This can originate as floor vibrations transmitted through a floor stand, or as "finger" and other handling noise on boom poles. All microphones behave to some extent as accelerometers, with the most sensitive axis being perpendicular to the diaphragm. Additionally, some microphones contain internal elements such as vacuum tubes and transformers which can be inherently microphonic. These are often cushioned by resilient internal methods, in addition to the employment of external isolation mounts. |
|||
[[File:Astatic crystal mic.jpg|thumb|[[Astatic Corporation|Astatic]] [[crystal microphone]] in a 'ring and spring' mount]] |
|||
Early microphones used a 'ring and spring' mount, where a single rigid ring was mounted and carried the microphone between a number of coil springs, usually four or eight. When early microphones were heavy and omnidirectional, this was adequate. However the single plane of suspension allowed the microphone to twist very easily; once microphones started to become directional, this twisting caused fading of the signal. A more three-dimensional and less planar suspension would be required. |
|||
Large side-address studio microphone are generally strung in "cat's cradle" mounts, using fabric-wound rubber elastic elements to provide isolation. While the elastic elements can deteriorate and sag over time, the low price of the mount and ease of replacing the elastic elements mean they remain a mainstay despite introduction of elastomer-based designs less sensible to degradation over time. |
|||
The same occurs for end-fire microphones, most often employed for location work, however positioning consistency issues in mobile contexts means elastomer-based alternatives have made more inroads: they offer more displacement (positional flexibility) along the prime axis, but better restrict movement along other axis, and have less tendency to keep oscillating after movements, which provide for better control of the microphone's precise position. |
|||
{{Clear}} |
|||
== See also == |
== See also == |
||
*[[ |
*[[Bushing (isolator)|Bushing]] |
||
*[[Vibration isolation]] |
*[[Vibration isolation]] |
||
*[[Shock absorber]] |
*[[Shock absorber]] |
||
*[[MIL-S-901]] |
*[[MIL-S-901]] |
||
*[[ |
*[[Microphonics]] |
||
*[[Cushioning]] |
*[[Cushioning]] |
||
==References== |
==References== |
||
{{ |
{{Reflist}} |
||
* DeSilva, C. W., "Vibration and Shock Handbook", CRC, 2005, {{ISBN|0-8493-1580-8}} |
* DeSilva, C. W., "Vibration and Shock Handbook", CRC, 2005, {{ISBN|0-8493-1580-8}} |
||
* Harris, C. M., and Peirsol, A. G. "Shock and Vibration Handbook", 2001, McGraw Hill, {{ISBN|0-07-137081-1}} |
* Harris, C. M., and Peirsol, A. G. "Shock and Vibration Handbook", 2001, McGraw Hill, {{ISBN|0-07-137081-1}} |
||
==External links== |
==External links== |
||
{{Commons category|Shock mounts}} |
|||
*Shock and vibration testing of shock mounts [https://www.youtube.com/watch?v=xmpsP3ejCXc] |
*Shock and vibration testing of shock mounts [https://www.youtube.com/watch?v=xmpsP3ejCXc] |
||
{{Authority control}} |
|||
[[Category:Microphones]] |
[[Category:Microphones]] |
||
[[Category:Mechanical vibrations]] |
[[Category:Mechanical vibrations]] |
||
[[Category:Fasteners]] |
|||
[[de:Mikrofon#Mikrofonspinne]] |
Latest revision as of 10:57, 8 March 2024

A shock mount or isolation mount is a mechanical fastener that connects two parts elastically to provide shock and vibration isolation.
Isolation mounts allow equipment to be securely mounted to a foundation and/or frame and, at the same time, allow it to float independently from it.
Uses
[edit]
Shock mounts are found in a wide variety of applications.
They can be used to isolate the foundation or substrate from the dynamics of the mounted equipment. This is vital on submarines where silence is critical to mission success. Yachts also use shock mounts to dampen mechanical noise (mainly transmitted throughout the structure) and increase comfort. This is usually done through elastic supports and transmission couplings.[1]
Other common examples are the motor and transmission mounts used in virtually every automobile manufactured today. Without isolation mounts, interior noise and comfort levels would be significantly different. Such shock and vibration-isolation mounts are often chosen by the nature of the dynamics produced by the equipment and the weight of the equipment.
Shock mounts can isolate sensitive equipment from undesirable dynamics of the foundation or substrate. Sensitive laboratory equipment most be isolated from shock from handling and ambient vibration. Military equipment and ships must be able to withstand nearby explosions.
Shock mounts are found in some disc drives and compact disc players, where the disc and rainy agreement are held by soft bushings that isolate them from outside vibration and other outside forces, such as torsion.[2] In this case, isolation mounts are often chosen by the sensitivity of the equipment to shock (fragility) and vibration (natural frequency) and the weight of the equipment.
For shock mounting to be effective, the input shock and vibration must be matched. A shock pulse is characterised by its peak acceleration, duration, and shape (half sine, triangular, trapezoidal, etc.). The shock response spectrum is a method for further evaluating mechanical shock.[3]
Shock mounts used to isolate entire buildings from earthquakes are called base isolators.


The black rubber is glued to the wood and the bolt only connects the metal to the rubber. Three similar shock mounts support the seat.
A similar idea, also known as a shock mount, is found in furniture design, introduced by Charles and Ray Eames. It provides some shock absorption and operates as a living hinge, allowing the seat back to pivot.
Shock mounts are also sometimes used in bicycle saddles,[4] handlebars and chassis.
Design
[edit]
Maxwell and Kelvin–Voigt models of viscoelasticity use springs and dashpots in series and parallel circuits respectively. Hydraulic and pneumatic components can be included, depending on the use.[5]
Laminated pads
[edit]One common type of isolation mounts is laminated pads. Generally, these pads consist of a cork or polymeric foam core which has been laminated between two pieces of ribbed neoprene sheet.
Molded rubber isolation mounts
[edit]Molded rubber isolation mounts are typically manufactured for specific applications. The best example of this is automotive engine and transmission mounts. Rubber bushings compress synthetic rubber rings on bolts to provide some isolation – operating temperature is sometimes a factor. Other shock mounts have mechanical springs or an elastomer (in tension or compression) engineered to isolate an item from specified mechanical shock and vibration. Some form of dashpot is usually used with a spring to provide viscous damping. Viscoelastic materials are common. Temperature is a factor in the dynamic response of rubber. Generally, a molded rubber mount is best suited for heavy loads producing higher frequency vibrations.

Cable isolation mounts
[edit]Cable mounts are based around a coil of wire rope fixed to an upper and lower mounting bar.[6][7] When properly matched to the load, these mounts provide isolation over a broad frequency range. They are typically applied to high performance applications, such as mounting sensitive instrumentation into off-road vehicles and shipboard.
Coil spring isolation mounts
[edit]
Coil spring isolation mounts generally provide the greatest degree of movement and the best low frequency performance. They are particularly popular for mounting equipment in buildings such as air handlers, filtration units, air conditioning and refrigeration systems and large pipes. Their degree of movement makes them ideal for applications where high flexure and/or expansion and contraction are a consideration.
Microphone mounts
[edit]
Shock mounts for microphones can provide basic protection from damage, but their prime use is to isolate microphones from mechanically transmitted noise. This can originate as floor vibrations transmitted through a floor stand, or as "finger" and other handling noise on boom poles. All microphones behave to some extent as accelerometers, with the most sensitive axis being perpendicular to the diaphragm. Additionally, some microphones contain internal elements such as vacuum tubes and transformers which can be inherently microphonic. These are often cushioned by resilient internal methods, in addition to the employment of external isolation mounts.
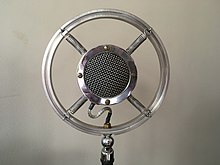
Early microphones used a 'ring and spring' mount, where a single rigid ring was mounted and carried the microphone between a number of coil springs, usually four or eight. When early microphones were heavy and omnidirectional, this was adequate. However the single plane of suspension allowed the microphone to twist very easily; once microphones started to become directional, this twisting caused fading of the signal. A more three-dimensional and less planar suspension would be required.
Large side-address studio microphone are generally strung in "cat's cradle" mounts, using fabric-wound rubber elastic elements to provide isolation. While the elastic elements can deteriorate and sag over time, the low price of the mount and ease of replacing the elastic elements mean they remain a mainstay despite introduction of elastomer-based designs less sensible to degradation over time.
The same occurs for end-fire microphones, most often employed for location work, however positioning consistency issues in mobile contexts means elastomer-based alternatives have made more inroads: they offer more displacement (positional flexibility) along the prime axis, but better restrict movement along other axis, and have less tendency to keep oscillating after movements, which provide for better control of the microphone's precise position.
See also
[edit]References
[edit]- ^ "Vulkan: il segreto per creare il silenzio a bordo degli yacht". Barche Magazine ISP. 2018-01-13. Retrieved 2021-04-16.
- ^ US 5,761,031, Ajmani, R S, "Conductive shock mount for reducing electromagnetic interference in a disk drive system", issued 2 June 1998
- ^ J E, Alexander (2009), The Shock Response Spectrum – A Primer (PDF), vol. IMAC–XXVII, Society for Experimental Mechanics, archived from the original (PDF) on 2016-03-04, retrieved 9 Feb 2015
- ^ US 6019422, Taormino, J S & Caselli, "Laterally pivoting bicycle saddle mount with shock absorber", published 1 Feb 2000
- ^ US3598353A, DeGrey, "Air-damped shock mount", published 1971
- ^ US4397069A, Camossi, "Device and process for the manufacture of vibration-damping and shockproof mountings incorporating at least one helically arranged metal cable and mounting thereby obtained", published 1983
- ^ US4783038A, Gilbert, LeKuch, Ferri, "Isolator Apparatus", published 1988
- DeSilva, C. W., "Vibration and Shock Handbook", CRC, 2005, ISBN 0-8493-1580-8
- Harris, C. M., and Peirsol, A. G. "Shock and Vibration Handbook", 2001, McGraw Hill, ISBN 0-07-137081-1
External links
[edit]
- Shock and vibration testing of shock mounts [1]